Контрольная работа 1 Вариант 16
Опишите линейные несовершенства кристаллического строения. Как они влияют на свойства металлов и сплавов.
В любом реальном кристалле всегда имеются дефекты строения. Линейные несовершенства имеют малые размеры в двух измерениях и большую протяженность в третьем. Эти несовершенства называются дислокациями.
Краевая дислокация представляет собой линию, вдоль которой обрывается внутри кристалла край “лишней“ полуплоскости (рисунок 1)
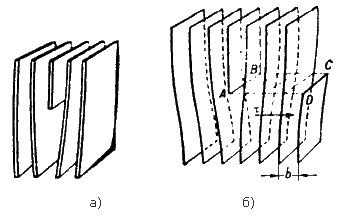
Рисунок 1 – Краевая дислокация (а) и механизм ее образования (б)
Неполная плоскость называется экстраплоскостью.
Большинство дислокаций образуются путем сдвигового механизма. Ее образование можно описать при помощи следующей операции. Надрезать кристалл по плоскости АВСD, сдвинуть нижнюю часть относительно верхней на один период решетки в направлении, перпендикулярном АВ, а затем вновь сблизить атомы на краях разреза внизу.
Наибольшие искажения в расположении атомов в кристалле имеют место вблизи нижнего края экстраплоскости. Вправо и влево от края экстраплоскости эти искажения малы (несколько периодов решетки), а вдоль края экстраплоскости искажения простираются через весь кристалл и могут быть очень велики (тысячи периодов решетки) (рисунок 2).
Если экстраплоскость находится в верхней части кристалла, то краевая дислокация – положительная (┴), если в нижней, то – отрицательная (┬). Дислокации одного знака отталкиваются, а противоположные притягиваются.
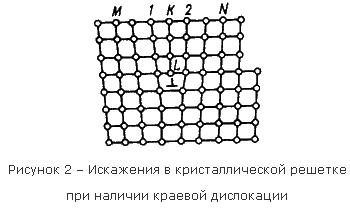
Другой тип дислокаций был описан Бюргерсом, и получил название винтовая дислокация
Винтовая дислокация получена при помощи частичного сдвига по плоскости Q вокруг линии EF (рисунок 3).На поверхности кристалла образуется ступенька, проходящая от точки Е до края кристалла. Такой частичный сдвиг нарушает параллельность атомных слоев, кристалл превращается в одну атомную плоскость, закрученную по винту в виде полого геликоида вокруг линии EF, которая представляет границу, отделяющую часть плоскости скольжения, где сдвиг уже произошел, от части, где сдвиг не начинался. Вдоль линии EF наблюдается макроскопический характер области несовершенства, в других направлениях ее размеры составляют несколько периодов.
Если переход от верхних горизонтов к нижним осуществляется поворотом по часовой стрелке, то дислокация правая, а если поворотом против часовой стрелки – левая.
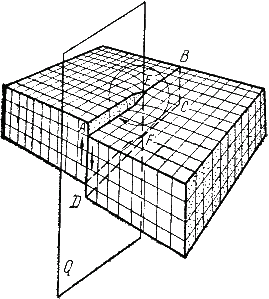
Рисунок 3 – Механизм образования винтовой дислокации
Винтовая дислокация не связана с какой-либо плоскостью скольжения, она может перемещаться по любой плоскости, проходящей через линию дислокации. Вакансии и дислоцированные атомы к винтовой дислокации не стекают.
В процессе кристаллизации атомы вещества, выпадающие из пара или раствора, легко присоединяются к ступеньке, что приводит к спиральному механизму роста кристалла.
Линии дислокаций не могут обрываться внутри кристалла, они должны либо быть замкнутыми, образуя петлю, либо разветвляться на несколько дислокаций, либо выходить на поверхность кристалла.
Дислокационная структура материала характеризуется плотностью дислокаций.
Плотность дислокаций в кристалле определяется как среднее число линий дислокаций, пересекающих внутри тела площадку площадью 1 м2, или как суммарная длина линий дислокаций в объеме 1 м3:
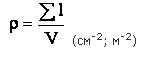
Плотность дислокаций изменяется в широких пределах и зависит от состояния материала. После тщательного отжига плотность дислокаций составляет 105…107 м-2, в кристаллах с сильно деформированной кристаллической решеткой плотность дислокаций достигает 1015…10 16 м –2.
Плотность дислокации в значительной мере определяет пластичность и прочность материала(рисунок 4).
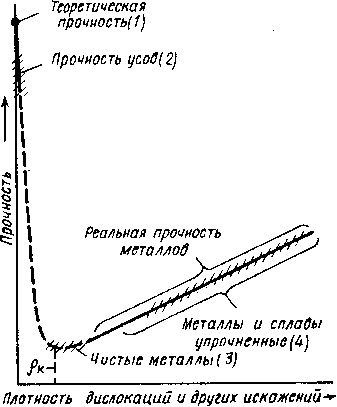
Рисунок 4 – Влияние плотности дислокаций на прочность

Если плотность меньше значения а, то сопротивление деформированию резко возрастает, а прочность приближается к теоретической. Повышение прочности достигается созданием металла с бездефектной структурой, а также повышением плотности дислокаций, затрудняющим их движение. В настоящее время созданы кристаллы без дефектов – нитевидные кристаллы длиной до 2 мм, толщиной 0,5…20 мкм – «усы» с прочностью, близкой к теоретической: для железа σВ = 13000 МПа, для меди σВ =30000 МПа. При упрочнении металлов увеличением плотности дислокаций, она не должна превышать значений 1015…10 16 м –2. В противном случае образуются трещины.
Дислокации влияют не только на прочность и пластичность, но и на другие свойства кристаллов. С увеличением плотности дислокаций возрастает внутреннее, изменяются оптические свойства, повышается электросопротивление металла. Дислокации увеличивают среднюю скорость диффузии в кристалле, ускоряют старение и другие процессы, уменьшают химическую стойкость, поэтому в результате обработки поверхности кристалла специальными веществами в местах выхода дислокаций образуются ямки.
Дислокации образуются при образовании кристаллов из расплава или газообразной фазы, при срастании блоков с малыми углами разориентировки. При перемещении вакансий внутри кристалла, они концентрируются, образуя полости в виде дисков. Если такие диски велики, то энергетически выгодно «захлопывание» их с образованием по краю диска краевой дислокации. Образуются дислокации при деформации, в процессе кристаллизации, при термической обработке.
Деформацией называется изменение формы и размеров тела под действием напряжений.
Напряжение – сила, действующая на единицу площади сечения детали.
Напряжения и вызываемые ими деформации могут возникать при действии на тело внешних сил растяжения, сжатия и т.д., а также в результате фазовых (структурных) превращений, усадки и других физико-химических процессов, протекающих в металлах, и связанных с изменением объема.
Металл, находящийся в напряженном состоянии, при любом виде нагружения всегда испытывает напряжения нормальные и касательные.
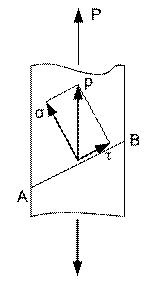
Рисунок 2 – Схема возникновения нормальных и касательных напряжений в металле при его нагружения
Рост нормальных и касательных напряжений приводит к разным последствиям. Рост нормальных напряжений приводит к хрупкому разрушению. Пластическую деформацию вызывают касательные напряжения.
При пластическом деформировании одна часть кристалла перемещается по отношению к другой под действием касательных напряжений. При снятии нагрузок сдвиг остается, т.е. происходит пластическая деформация.
С увеличением степени деформации характеристики пластичности (относительное удлинение, относительное сужение) и вязкости (ударная вязкость) уменьшаются, а прочностные характеристики (предел упругости, предел текучести, предел прочности) и твердость увеличиваются. Также повышается электросопротивление, снижаются сопротивление коррозии, теплопроводность, магнитная проницаемость.
Совокупность явлений, связанных с изменением механических, физических и других свойств металлов в процессе пластической деформации называют деформационным упрочнением или наклепом.
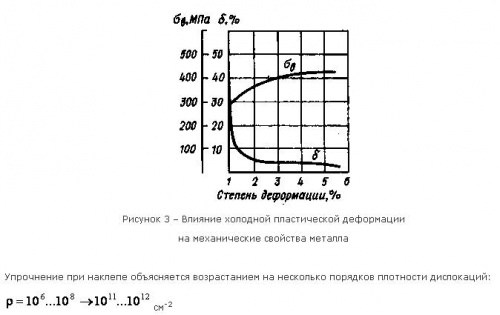
Их свободное перемещение затрудняется взаимным влиянием, также торможением дислокаций в связи с измельчением блоков и зерен, искажениями решетки металлов, возникновением напряжений.
Вычертите диаграмму состояния железо-карбид железа, укажите структурные составляющие во всех областях диаграммы, опишите превращения и постройте кривую охлаждения (с применением правила фаз) для сплава, содержащего 1,3%С. Какова структура этого сплава при комнатной температуре и как такой сплав называется?
Первичная кристаллизация сплавов системы железо-углерод начинается по достижении температур, соответствующих линии ABCD (линии ликвидус), и заканчивается при температурах, образующих линию AHJECF (линию солидус).
При кристаллизации сплавов по линии АВ из жидкого раствора выделяются кристаллы твердого раствора углерода в α-железе (δ-раствор). Процесс кристаллизации сплавов с содержанием углерода до 0,1% заканчивается по линии АН с образованием α (δ)-твердого раствора. На линии HJB протекает перитектическое превращение, в результате которого образуется твердый раствор углерода в γ-железе, т. е. аустенит. Процесс первичной кристаллизации сталей заканчивается по линии AHJE.
При температурах, соответствующих линии ВС, из жидкого раствора кристаллизуется аустенит. В сплавах, содержащих от 4,3% до 6,67% углерода, при температурах, соответствующих линии CD, начинают выделяться кристаллы цементита первичного. Цементит, кристаллизующийся из жидкой фазы, называется первичным. B точке С при температуре 1147°С и концентрации углерода в жидком растворе 4,3% образуется эвтектика, которая называется ледебуритом. Эвтектическое превращение с образованием ледебурита можно записать формулой ЖР4,3 ->Л[А2,14+Ц6,67]. Процесс первичной кристаллизации чугунов заканчивается по линии ECF образованием ледебурита.
Таким образом, структура чугунов ниже 1147°С будет: доэвтектических – аустенит + ледебурит, эвтектических – ледебурит и заэвтектических – цементит (первичный) + ледебурит.
Превращения, происходящие в твердом состоянии, называются вторичной кристаллизацией. Они связаны с переходом при охлаждении γ-железа в α-железо и распадом аустенита.
Линия GS соответствует температурам начала превращения аустенита в феррит. Ниже линии GS сплавы состоят из феррита и аустенита.
Линия ЕS показывает температуры начала выделения цементита из аустенита вследствие уменьшения растворимости углерода в аустените с понижением температуры. Цементит, выделяющийся из аустенита, называется вторичным цементитом.
В точке S при температуре 727°С и концентрации углерода в аустените 0,8% образуется эвтектоидная смесь состоящая из феррита и цементита, которая называется перлитом. Перлит получается в результате одновременного выпадения из аустенита частиц феррита и цементита. Процесс превращения аустенита в перлит можно записать формулой А0,8->П[Ф0,03+Ц6,67].
Линия PQ показывает на уменьшение растворимости углерода в феррите при охлаждении и выделении цементита, который называется третичным цементитом.
Следовательно, сплавы, содержащие менее 0,008% углерода (точкаQ), являются однофазными и имеют структуру чистого феррита, а сплавы, содержащие углерод от 0,008 до 0,03% – структуру феррит + цементит третичный и называются техническим железом.
Доэвтектоидные стали при температуре ниже 727ºС имеют структуру феррит + перлит и заэвтектоидные – перлит + цементит вторичный в виде сетки по границам зерен.
В доэвтектических чугунах в интервале температур 1147-727ºС при охлаждении из аустенита выделяется цементит вторичный, вследствие уменьшения растворимости углерода (линия ES). По достижении температуры 727ºС (линия PSK) аустенит, обедненный углеродом до 0,8% (точка S), превращаясь в перлит. Таким образом, после окончательного охлаждения структура доэвтектических чугунов состоит из перлита, цементита вторичного и ледебурита превращенного (перлит+цементит).
Структура эвтектических чугунов при температурах ниже 727ºС состоит из ледебурита превращенного. Заэвтектический чугун при температурах ниже 727ºС состоит из ледебурита превращенного и цементита первичного.
Правило фаз устанавливает зависимость между числом степеней свободы, числом компонентов и числом фаз и выражается уравнением:
C = K + 1 – Ф,
где С – число степеней свободы системы;
К – число компонентов, образующих систему;
1 – число внешних факторов (внешним фактором считаем только температуру, так как давление за исключением очень высокого мало влияет на фазовое равновесие сплавов в твердом и жидком состояниях);
Ф – число фаз, находящихся в равновесии.
Сплав железа с углеродом, содержащий 1,3%С, называется заэвтектоидной сталью. Его структура при комнатной температуре цементит + перлит.
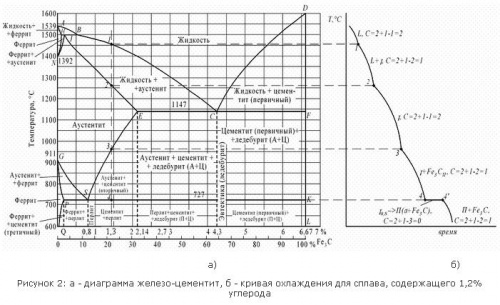
Вычертите диаграмму изотермического превращения аустенита для стали У8, нанесите на нее кривую режима изотермической обработки, обеспечивающей получение твердости 45 НRC. Укажите, как этот режим называется, опишите сущность превращений и какая структура получается в данном случае?
Изотермической обработкой, необходимой для получения твердости 45 НRC, является изотермическая закалка.
Изотермическая закалка выполняется так же, как и ступенчатая, но выдержка в закалочной среде более продолжительна. При такой выдержке происходит изотермический распад аустенита с образованием бейнита. Продолжительность выдержки в закалочной среде зависит от устойчивости переохлажденного аустенита при температурах выше Мн и определяется по диаграмме изотермического превращения аустенита для каждой марки стали. В качестве охлаждающих сред при изотермической закалке применяют расплавленные соли (например, 55% KNO и 45% NaNO2) или расплавленные щелочи (20% NaOH и 80% KOH). Добавка 5–10 % воды в расплав щелочей и солей увеличивает скорость охлаждения.
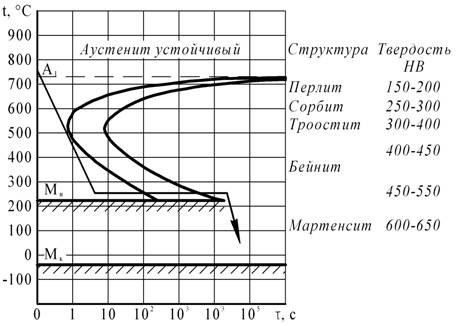
Рисунок 4 – Диаграмма изотермического превращения аустенита стали У8
Нижний бейнит по сравнению с продуктами распада аустенита в перлитной области (перлит, троостит) имеет более высокую твердость и прочность при сохранении высокой пластичности.
С помощью диаграммы состояния железо–цементит определите температуру полного и неполного отжига и нормализации для стали 30. Охарактеризуйте эти режимы термической обработки и опишите структуру и свойства стали.
Полный отжиг заключается в нагреве доэвтектоидной стали на 30-50°С выше температуры, соответствующей точке Ас3 (для стали 30 Ас3 = 800°С), выдержке при этой температуре для полного прогрева и завершения фазовых превращений в объеме металла и последующем медленном охлаждении.
При медленном охлаждении стали приближаются к фазовому и структурному равновесию. Структура после отжига – феррит + перлит. После отжига сталь имеет низкую твердость и прочность.
Основные цели отжига: перекристаллизация стали (измельчение зерна), снятие внутренних напряжений, снижение твердости и улучшение обрабатываемости.
Неполный отжиг отличается от полного тем, что сталь нагревают до более низкой температуры (немного выше точки А1 (для стали 30 А1 = 730°С)). Неполный отжиг доэвтектоидных сталей применяют для улучшения обрабатываемости резанием. При неполном отжиге происходит частичная перекристаллизация стали – вследствие перехода перлита в аустенит. Избыточный феррит лишь частично превращается в аустенит. Структура после отжига – феррит + перлит.
Нормализация заключается в нагреве доэвтектоидной стали до температуры, превышающей точку Ас3 на 40-50 °С, в непродолжительной выдержке для прогрева садки и завершения фазовых превращений и охлаждении на воздухе. Нормализация вызывает полную фазовую перекристаллизацию стали и устраняет крупнозернистую структуру, полученную при литье, прокатке, ковке или штамповке. Нормализацию широко применяют для улучшения свойств стальных отливок вместо закалки и отпуска.
Ускоренное охлаждение на воздухе приводит к распаду аустенита при более низких температурах, что повышает дисперсность феррито-цементитной структуры и увеличивает количество перлита или, точнее, сорбита или троостита. Это повышает прочность и твердость нормализованной средне- и высокоуглеродистой стали по сравнению с отожженной.

В любом реальном кристалле всегда имеются дефекты строения. Линейные несовершенства имеют малые размеры в двух измерениях и большую протяженность в третьем. Эти несовершенства называются дислокациями.
Краевая дислокация представляет собой линию, вдоль которой обрывается внутри кристалла край “лишней“ полуплоскости (рисунок 1)
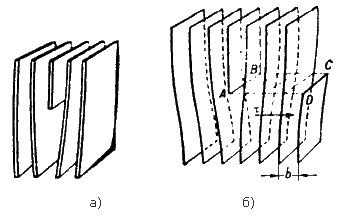
Рисунок 1 – Краевая дислокация (а) и механизм ее образования (б)
Неполная плоскость называется экстраплоскостью.
Большинство дислокаций образуются путем сдвигового механизма. Ее образование можно описать при помощи следующей операции. Надрезать кристалл по плоскости АВСD, сдвинуть нижнюю часть относительно верхней на один период решетки в направлении, перпендикулярном АВ, а затем вновь сблизить атомы на краях разреза внизу.
Наибольшие искажения в расположении атомов в кристалле имеют место вблизи нижнего края экстраплоскости. Вправо и влево от края экстраплоскости эти искажения малы (несколько периодов решетки), а вдоль края экстраплоскости искажения простираются через весь кристалл и могут быть очень велики (тысячи периодов решетки) (рисунок 2).
Если экстраплоскость находится в верхней части кристалла, то краевая дислокация – положительная (┴), если в нижней, то – отрицательная (┬). Дислокации одного знака отталкиваются, а противоположные притягиваются.
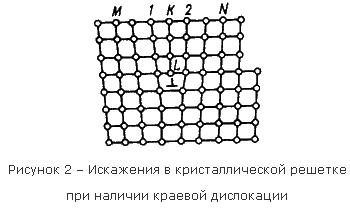
Другой тип дислокаций был описан Бюргерсом, и получил название винтовая дислокация
Винтовая дислокация получена при помощи частичного сдвига по плоскости Q вокруг линии EF (рисунок 3).На поверхности кристалла образуется ступенька, проходящая от точки Е до края кристалла. Такой частичный сдвиг нарушает параллельность атомных слоев, кристалл превращается в одну атомную плоскость, закрученную по винту в виде полого геликоида вокруг линии EF, которая представляет границу, отделяющую часть плоскости скольжения, где сдвиг уже произошел, от части, где сдвиг не начинался. Вдоль линии EF наблюдается макроскопический характер области несовершенства, в других направлениях ее размеры составляют несколько периодов.
Если переход от верхних горизонтов к нижним осуществляется поворотом по часовой стрелке, то дислокация правая, а если поворотом против часовой стрелки – левая.
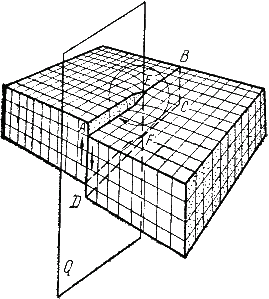
Рисунок 3 – Механизм образования винтовой дислокации
Винтовая дислокация не связана с какой-либо плоскостью скольжения, она может перемещаться по любой плоскости, проходящей через линию дислокации. Вакансии и дислоцированные атомы к винтовой дислокации не стекают.
В процессе кристаллизации атомы вещества, выпадающие из пара или раствора, легко присоединяются к ступеньке, что приводит к спиральному механизму роста кристалла.
Линии дислокаций не могут обрываться внутри кристалла, они должны либо быть замкнутыми, образуя петлю, либо разветвляться на несколько дислокаций, либо выходить на поверхность кристалла.
Дислокационная структура материала характеризуется плотностью дислокаций.
Плотность дислокаций в кристалле определяется как среднее число линий дислокаций, пересекающих внутри тела площадку площадью 1 м2, или как суммарная длина линий дислокаций в объеме 1 м3:
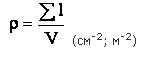
Плотность дислокаций изменяется в широких пределах и зависит от состояния материала. После тщательного отжига плотность дислокаций составляет 105…107 м-2, в кристаллах с сильно деформированной кристаллической решеткой плотность дислокаций достигает 1015…10 16 м –2.
Плотность дислокации в значительной мере определяет пластичность и прочность материала(рисунок 4).
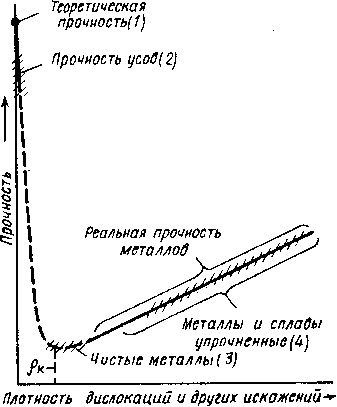
Рисунок 4 – Влияние плотности дислокаций на прочность

Если плотность меньше значения а, то сопротивление деформированию резко возрастает, а прочность приближается к теоретической. Повышение прочности достигается созданием металла с бездефектной структурой, а также повышением плотности дислокаций, затрудняющим их движение. В настоящее время созданы кристаллы без дефектов – нитевидные кристаллы длиной до 2 мм, толщиной 0,5…20 мкм – «усы» с прочностью, близкой к теоретической: для железа σВ = 13000 МПа, для меди σВ =30000 МПа. При упрочнении металлов увеличением плотности дислокаций, она не должна превышать значений 1015…10 16 м –2. В противном случае образуются трещины.
Дислокации влияют не только на прочность и пластичность, но и на другие свойства кристаллов. С увеличением плотности дислокаций возрастает внутреннее, изменяются оптические свойства, повышается электросопротивление металла. Дислокации увеличивают среднюю скорость диффузии в кристалле, ускоряют старение и другие процессы, уменьшают химическую стойкость, поэтому в результате обработки поверхности кристалла специальными веществами в местах выхода дислокаций образуются ямки.
Дислокации образуются при образовании кристаллов из расплава или газообразной фазы, при срастании блоков с малыми углами разориентировки. При перемещении вакансий внутри кристалла, они концентрируются, образуя полости в виде дисков. Если такие диски велики, то энергетически выгодно «захлопывание» их с образованием по краю диска краевой дислокации. Образуются дислокации при деформации, в процессе кристаллизации, при термической обработке.
Деформацией называется изменение формы и размеров тела под действием напряжений.
Напряжение – сила, действующая на единицу площади сечения детали.
Напряжения и вызываемые ими деформации могут возникать при действии на тело внешних сил растяжения, сжатия и т.д., а также в результате фазовых (структурных) превращений, усадки и других физико-химических процессов, протекающих в металлах, и связанных с изменением объема.
Металл, находящийся в напряженном состоянии, при любом виде нагружения всегда испытывает напряжения нормальные и касательные.
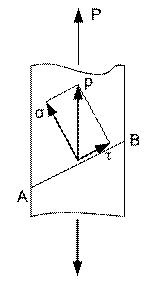
Рисунок 2 – Схема возникновения нормальных и касательных напряжений в металле при его нагружения
Рост нормальных и касательных напряжений приводит к разным последствиям. Рост нормальных напряжений приводит к хрупкому разрушению. Пластическую деформацию вызывают касательные напряжения.
При пластическом деформировании одна часть кристалла перемещается по отношению к другой под действием касательных напряжений. При снятии нагрузок сдвиг остается, т.е. происходит пластическая деформация.
С увеличением степени деформации характеристики пластичности (относительное удлинение, относительное сужение) и вязкости (ударная вязкость) уменьшаются, а прочностные характеристики (предел упругости, предел текучести, предел прочности) и твердость увеличиваются. Также повышается электросопротивление, снижаются сопротивление коррозии, теплопроводность, магнитная проницаемость.
Совокупность явлений, связанных с изменением механических, физических и других свойств металлов в процессе пластической деформации называют деформационным упрочнением или наклепом.
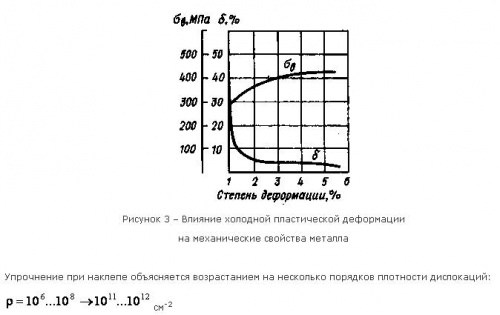
Их свободное перемещение затрудняется взаимным влиянием, также торможением дислокаций в связи с измельчением блоков и зерен, искажениями решетки металлов, возникновением напряжений.
Вычертите диаграмму состояния железо-карбид железа, укажите структурные составляющие во всех областях диаграммы, опишите превращения и постройте кривую охлаждения (с применением правила фаз) для сплава, содержащего 1,3%С. Какова структура этого сплава при комнатной температуре и как такой сплав называется?
Первичная кристаллизация сплавов системы железо-углерод начинается по достижении температур, соответствующих линии ABCD (линии ликвидус), и заканчивается при температурах, образующих линию AHJECF (линию солидус).
При кристаллизации сплавов по линии АВ из жидкого раствора выделяются кристаллы твердого раствора углерода в α-железе (δ-раствор). Процесс кристаллизации сплавов с содержанием углерода до 0,1% заканчивается по линии АН с образованием α (δ)-твердого раствора. На линии HJB протекает перитектическое превращение, в результате которого образуется твердый раствор углерода в γ-железе, т. е. аустенит. Процесс первичной кристаллизации сталей заканчивается по линии AHJE.
При температурах, соответствующих линии ВС, из жидкого раствора кристаллизуется аустенит. В сплавах, содержащих от 4,3% до 6,67% углерода, при температурах, соответствующих линии CD, начинают выделяться кристаллы цементита первичного. Цементит, кристаллизующийся из жидкой фазы, называется первичным. B точке С при температуре 1147°С и концентрации углерода в жидком растворе 4,3% образуется эвтектика, которая называется ледебуритом. Эвтектическое превращение с образованием ледебурита можно записать формулой ЖР4,3 ->Л[А2,14+Ц6,67]. Процесс первичной кристаллизации чугунов заканчивается по линии ECF образованием ледебурита.
Таким образом, структура чугунов ниже 1147°С будет: доэвтектических – аустенит + ледебурит, эвтектических – ледебурит и заэвтектических – цементит (первичный) + ледебурит.
Превращения, происходящие в твердом состоянии, называются вторичной кристаллизацией. Они связаны с переходом при охлаждении γ-железа в α-железо и распадом аустенита.
Линия GS соответствует температурам начала превращения аустенита в феррит. Ниже линии GS сплавы состоят из феррита и аустенита.
Линия ЕS показывает температуры начала выделения цементита из аустенита вследствие уменьшения растворимости углерода в аустените с понижением температуры. Цементит, выделяющийся из аустенита, называется вторичным цементитом.
В точке S при температуре 727°С и концентрации углерода в аустените 0,8% образуется эвтектоидная смесь состоящая из феррита и цементита, которая называется перлитом. Перлит получается в результате одновременного выпадения из аустенита частиц феррита и цементита. Процесс превращения аустенита в перлит можно записать формулой А0,8->П[Ф0,03+Ц6,67].
Линия PQ показывает на уменьшение растворимости углерода в феррите при охлаждении и выделении цементита, который называется третичным цементитом.
Следовательно, сплавы, содержащие менее 0,008% углерода (точкаQ), являются однофазными и имеют структуру чистого феррита, а сплавы, содержащие углерод от 0,008 до 0,03% – структуру феррит + цементит третичный и называются техническим железом.
Доэвтектоидные стали при температуре ниже 727ºС имеют структуру феррит + перлит и заэвтектоидные – перлит + цементит вторичный в виде сетки по границам зерен.
В доэвтектических чугунах в интервале температур 1147-727ºС при охлаждении из аустенита выделяется цементит вторичный, вследствие уменьшения растворимости углерода (линия ES). По достижении температуры 727ºС (линия PSK) аустенит, обедненный углеродом до 0,8% (точка S), превращаясь в перлит. Таким образом, после окончательного охлаждения структура доэвтектических чугунов состоит из перлита, цементита вторичного и ледебурита превращенного (перлит+цементит).
Структура эвтектических чугунов при температурах ниже 727ºС состоит из ледебурита превращенного. Заэвтектический чугун при температурах ниже 727ºС состоит из ледебурита превращенного и цементита первичного.
Правило фаз устанавливает зависимость между числом степеней свободы, числом компонентов и числом фаз и выражается уравнением:
C = K + 1 – Ф,
где С – число степеней свободы системы;
К – число компонентов, образующих систему;
1 – число внешних факторов (внешним фактором считаем только температуру, так как давление за исключением очень высокого мало влияет на фазовое равновесие сплавов в твердом и жидком состояниях);
Ф – число фаз, находящихся в равновесии.
Сплав железа с углеродом, содержащий 1,3%С, называется заэвтектоидной сталью. Его структура при комнатной температуре цементит + перлит.
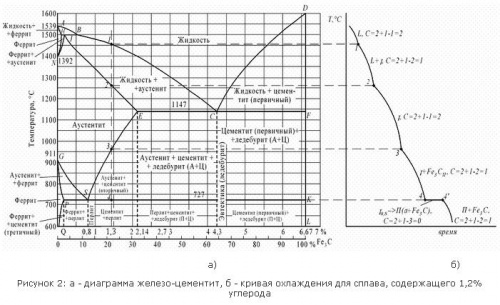
Вычертите диаграмму изотермического превращения аустенита для стали У8, нанесите на нее кривую режима изотермической обработки, обеспечивающей получение твердости 45 НRC. Укажите, как этот режим называется, опишите сущность превращений и какая структура получается в данном случае?
Изотермической обработкой, необходимой для получения твердости 45 НRC, является изотермическая закалка.
Изотермическая закалка выполняется так же, как и ступенчатая, но выдержка в закалочной среде более продолжительна. При такой выдержке происходит изотермический распад аустенита с образованием бейнита. Продолжительность выдержки в закалочной среде зависит от устойчивости переохлажденного аустенита при температурах выше Мн и определяется по диаграмме изотермического превращения аустенита для каждой марки стали. В качестве охлаждающих сред при изотермической закалке применяют расплавленные соли (например, 55% KNO и 45% NaNO2) или расплавленные щелочи (20% NaOH и 80% KOH). Добавка 5–10 % воды в расплав щелочей и солей увеличивает скорость охлаждения.
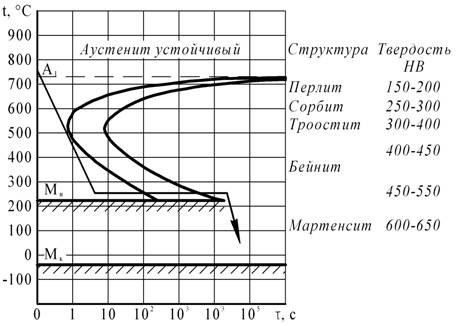
Рисунок 4 – Диаграмма изотермического превращения аустенита стали У8
Нижний бейнит по сравнению с продуктами распада аустенита в перлитной области (перлит, троостит) имеет более высокую твердость и прочность при сохранении высокой пластичности.
С помощью диаграммы состояния железо–цементит определите температуру полного и неполного отжига и нормализации для стали 30. Охарактеризуйте эти режимы термической обработки и опишите структуру и свойства стали.
Полный отжиг заключается в нагреве доэвтектоидной стали на 30-50°С выше температуры, соответствующей точке Ас3 (для стали 30 Ас3 = 800°С), выдержке при этой температуре для полного прогрева и завершения фазовых превращений в объеме металла и последующем медленном охлаждении.
При медленном охлаждении стали приближаются к фазовому и структурному равновесию. Структура после отжига – феррит + перлит. После отжига сталь имеет низкую твердость и прочность.
Основные цели отжига: перекристаллизация стали (измельчение зерна), снятие внутренних напряжений, снижение твердости и улучшение обрабатываемости.
Неполный отжиг отличается от полного тем, что сталь нагревают до более низкой температуры (немного выше точки А1 (для стали 30 А1 = 730°С)). Неполный отжиг доэвтектоидных сталей применяют для улучшения обрабатываемости резанием. При неполном отжиге происходит частичная перекристаллизация стали – вследствие перехода перлита в аустенит. Избыточный феррит лишь частично превращается в аустенит. Структура после отжига – феррит + перлит.
Нормализация заключается в нагреве доэвтектоидной стали до температуры, превышающей точку Ас3 на 40-50 °С, в непродолжительной выдержке для прогрева садки и завершения фазовых превращений и охлаждении на воздухе. Нормализация вызывает полную фазовую перекристаллизацию стали и устраняет крупнозернистую структуру, полученную при литье, прокатке, ковке или штамповке. Нормализацию широко применяют для улучшения свойств стальных отливок вместо закалки и отпуска.
Ускоренное охлаждение на воздухе приводит к распаду аустенита при более низких температурах, что повышает дисперсность феррито-цементитной структуры и увеличивает количество перлита или, точнее, сорбита или троостита. Это повышает прочность и твердость нормализованной средне- и высокоуглеродистой стали по сравнению с отожженной.

0 комментариев