Контрольная работа 1 Вариант 20
Опишите условия получения мелкозернистой структуры металла при самопроизвольно развивающейся кристаллизации (используя кривые Тамманна).
Переход металла из жидкого состояния в твердое (кристаллическое) называется кристаллизацией. Процесс кристаллизации может протекать только при переохлаждении металла ниже равновесной температуры Тп. Разность между температурами Тп и Тк, при которых может протекать процесс кристаллизации, носит название степени переохлаждения:
ΔT=Tп-Тк.
Термические кривые, характеризующие процесс кристаллизации чистых металлов при охлаждении с разной скоростью v, показаны на рисунке
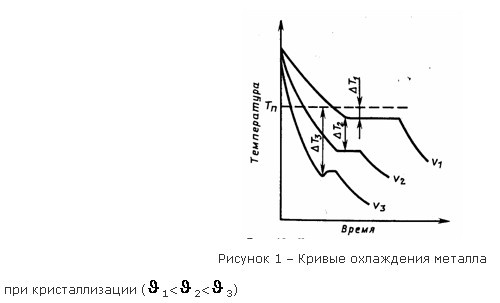
При очень медленном охлаждении степень переохлаждения невелика и процесс кристаллизации протекает при температуре близкой к равновесной Тп. На термической кривой при температуре кристаллизации отмечается горизонтальная площадка (остановка в падении температуры), образование которой объясняется выделением скрытой теплоты кристаллизации, несмотря на отвод теплоты при охлаждении.
С увеличением скорости охлаждения степень переохлаждения возрастает (кривые v2, v3) и процесс кристаллизации протекает при температурах, лежащих значительно ниже равновесной температуры кристаллизации.
Чем больше скорость образования зародышей и меньше скорость роста их, тем меньше размер кристалла (зерна), выросшего из одного зародыша, и, следовательно, более мелкозернистой будет структура металла.
При небольшой скорости переохлаждения ΔT (малой скорости охлаждения) число зародышей мало. В этих условиях будет получено крупное зерно. С увеличением степени переохлаждения скорость образования зародышей возрастает, количество их увеличивается и размер зерна в затвердевшем металле уменьшается.
Размер зерна металла сильно влияет на его механические свойства. Эти свойства, особенно вязкость и пластичность, выше, если металл имеет мелкое зерно.
Что такое холодная деформация? Как при этом изменяются структура и свойства металла?
Холодной деформацией называют такую, которую проводят при температуре ниже температуры рекристаллизации. Поэтому холодная деформация сопровождается упрочнением (наклепом) металла.
Форма заготовки при обработке давлением изменяется под действием внешних сил вследствие пластической деформации каждого кристаллита в соответствии со схемой главных деформаций. Основное изменение формы кристаллитов состоит в том, что они вытягиваются в направлении главной деформации растяжения (например, в направлении прокатки или волочения). С повышением степени холодной деформации зерна все более вытягиваются и структура становится волокнистой.
С увеличением степени холодной деформации показатели сопротивления деформированию (временное сопротивление, предел текучести и твердости) возрастают, а показатели пластичности (относительное удлинение и сужение) падают.
Вычертите диаграмму состояния железо-карбид железа, укажите структурные составляющие во всех областях диаграммы, опишите превращения и постройте кривую охлаждения (с применением правила фаз) для сплава, содержащего 1,6% С. Какова структура этого сплава при комнатной температуре и как такой сплав называется?
Первичная кристаллизация сплавов системы железо-углерод начинается по достижении температур, соответствующих линии ABCD (линии ликвидус), и заканчивается при температурах, образующих линию AHJECF (линию солидус).
При кристаллизации сплавов по линии АВ из жидкого раствора выделяются кристаллы твердого раствора углерода в α-железе (δ-раствор). Процесс кристаллизации сплавов с содержанием углерода до 0,1% заканчивается по линии АН с образованием α (δ)-твердого раствора. На линии HJB протекает перитектическое превращение, в результате которого образуется твердый раствор углерода в γ-железе, т. е. аустенит. Процесс первичной кристаллизации сталей заканчивается по линии AHJE.
При температурах, соответствующих линии ВС, из жидкого раствора кристаллизуется аустенит. В сплавах, содержащих от 4,3% до 6,67% углерода, при температурах, соответствующих линии CD, начинают выделяться кристаллы цементита первичного. Цементит, кристаллизующийся из жидкой фазы, называется первичным. B точке С при температуре 1147°С и концентрации углерода в жидком растворе 4,3 % образуется эвтектика, которая называется ледебуритом. Эвтектическое превращение с образованием ледебурита можно записать формулой ЖР4,3Л[А2,14+Ц6,67]. Процесс первичной кристаллизации чугунов заканчивается по линии ECF образованием ледебурита.
Таким образом, структура чугунов ниже 1147°С будет: доэвтектических — аустенит + ледебурит, эвтектических — ледебурит и заэвтектических — цементит (первичный)+ледебурит.
Превращения, происходящие в твердом состоянии, называются вторичной кристаллизацией. Они связаны с переходом при охлаждении γ-железа в α-железо и распадом аустенита.
Линия GS соответствует температурам начала превращения аустенита в феррит. Ниже линии GS сплавы состоят из феррита и аустенита.
Линия ЕS показывает температуры начала выдел пня цементита из аустенита вследствие уменьшения растворимости углерода в аустените с понижением температуры. Цементит, выделяющийся из аустенита, называется вторичным цементитом.
В точке S при температуре 727°С и концентрации углерода в аустените 0,8 % образуется эвтектоидная смесь состоящая из феррита и цементита, которая называется перлитом. Перлит получается в результате одновременного выпадения из аустенита частиц феррита и цементита. Процесс превращения аустенита в перлит можно записать формулой А0,8П[Ф0,03+Ц6,67].
Линия PQ показывает на уменьшение растворимости углерода в феррите при охлаждении и выделении цементита, который называется третичным цементитом.
Следовательно, сплавы, содержащие менее 0,008% углерода (точкаQ), являются однофазными и имеют структуру чистого феррита, а сплавы, содержащие углерод от 0,008 до 0,03% – структуру феррит + цементит третичный и называются техническим железом.
Доэвтектоидные стали при температуре ниже 727ºС имеют структуру феррит + перлит и заэвтектоидные – перлит + цементит вторичный в виде сетки по границам зерен.
В доэвтектических чугунах в интервале температур 1147–727ºС при охлаждении из аустенита выделяется цементит вторичный, вследствие уменьшения растворимости углерода(линия ES). По достижении температуры 727ºС (линия PSK) аустенит, обедненный углеродом до 0,8% (точка S), превращаясь в перлит. Таким образом, после окончательного охлаждения структура доэвтектических чугунов состоит из перлита, цементита вторичного и ледебурита превращенного (перлит + цементит).
Структура эвтектических чугунов при температурах ниже 727ºС состоит из ледебурита превращенного. Заэвтектический чугун при температурах ниже 727ºС состоит из ледебурита превращенного и цементита первичного.
Правило фаз устанавливает зависимость между числом степеней свободы, числом компонентов и числом фаз и выражается уравнением:
C = K + 1 – Ф,
где С – число степеней свободы системы;
К – число компонентов, образующих систему;
1 – число внешних факторов (внешним фактором считаем только температуру, так как давление за исключением очень высокого мало влияет на фазовое равновесие сплавов в твердом и жидком состояниях);
Ф – число фаз, находящихся в равновесии.
Сплав железа с углеродом, содержащий 1,6%С, называется заэвтектоидной сталью. Его структура при комнатной температуре цементит (вторичный) + перлит.
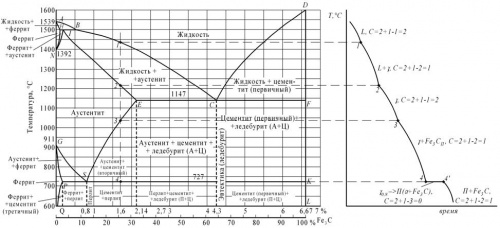
а) б)
Рисунок 2: а-диаграмма железо-цементит, б-кривая охлаждения для сплава, содержащего 1,6% углерода
Используя диаграмму состояния железо – карбид железа и кривую изменения твердости в зависимости от температуры отпуска, назначьте режим термической обработки для углеродистой стали 45, необходимый для обеспечения твердости 550 НВ. Опишите превращения, происходящие на всех этапах термической обработки, и получаемую после обработки структуру.
После закалки с печным нагревом и низкого отпуска (160-180°С) можно получить твердость стали 45 не более 500 НВ. С увеличением температуры отпуска твердость закаленной стали снижается. Так, при высоком отпуске (580-600°С) твердость стали на глубину прокаливания не превышает 250НВ.
Закалка токами высокой частоты (ТВЧ) позволяет получить твердость на 40-60 НВ выше, чем при закалке с печным нагревом. Это объясняется тем, что применение высокоскоростного нагрева и смещение превращений в область температур, превышающих температуру критической точки Ас3 (за счет высокой скорости нагрева), позволяет получить мелкозернистый аустенит, а после охлаждения на глубину прокаливания – мартенсит мелкоигольчатого и безыгольчатого строения. Закалка ТВЧ проводится при температуре 920-940˚С
После закалки ТВЧ изделие подвергают низкому отпуску 160-180˚С. Более высокие температуры применять не следует, так как это приводит к снижению твердости. Низкий отпуск, незначительно снижая твердость закаленного изделия, существенно повышает сопротивление стали хрупкому разрушению. Структура стали после низкого отпуска на глубину прокаливания – мартенсит отпуска.
В результате термической обработки твердость изделия на глубину прокаливания составит 550 НВ.
Каковы причины возникновения внутренних напряжений при закалке? Каким способом можно предохранить изделие от образования закалочных трещин?
Внутренние напряжения при закалке стали возникают вследствие неравномерного охлаждения поверхности и сердцевины изделия (эти напряжения называют тепловыми), увеличения объема и неоднородности протекания мартенситного превращения по объему изделия. Напряжения, вызываемые этим превращением, называют структурными, или фазовыми.
Неодинаковое распределение температур по сечению изделия при быстром охлаждении сопровождается и неравномерным изменением объема. Поверхностные слои сжимаются быстрее, чем внутренние. Однако сжатию поверхностных слоев препятствуют внутренние слои. Это приводит к тому, что в поверхностных слоях образуются временные (т.е. исчезающие после снятия нагрузки) растягивающие, а во внутренних слоях — сжимающие напряжения.
Рассмотрим теперь условия образования структурных напряжений при полной прокаливаемости. При этом тепловые напряжения условно учитываться не будут.
По достижении при закалке температур ниже точки Мн мартенсит в первую очередь образуется на поверхности, где точка Мн будет достигнута раньше, чем в сердцевине. Так как превращение аустенит – мартенсит сопровождается увеличением объема, то это приводит к образованию на поверхности временных сжимающих напряжений, а во внутренних слоях – растягивающих напряжений. По мере развития превращения знак напряжений на поверхности и в сердцевине меняется.
Структурные напряжения относительно тепловых изменяются в обратном порядке. В результате мартенситного превращения на поверхности образуются остаточные напряжения растяжения, а в сердцевине – напряжения сжатия. Эти остаточные напряжения, как и тепловые, возникают в результате появления под действием временных напряжений не только упругой, но и неодинаковой по сечению остаточной деформации.
При закалке стали одновременно возникают как тепловые, так и структурные напряжения, которые суммируют. В данной схеме тепловые напряжения превышали структурные, поэтому на поверхности образовались напряжения сжатия. Однако в зависимости от соотношения между тепловыми и структурными напряжениями могут получиться различные эпюры суммарных напряжений, а в поверхностных слоях напряжения могут иметь разный знак и различную величину. Во многих случаях величина фазовых напряжений больше, чем величина тепловых.
Остаточные напряжения, полученные после закалки, не характеризуют напряжения, возникающие при охлаждении (нагреве) стали. Остаточные напряжения всегда меньше временных напряжений, образующихся в процессе охлаждения.
Если величина напряжений превышает сопротивление отрыву и металл мало пластичен, то напряжения не могут быть уменьшены пластической деформацией. Это вызывает образование трещин. Наиболее опасны при этом растягивающие напряжения на поверхности, которые способствуют образованию трещин и снижают предел выносливости стали.
Растягивающие напряжения возникают в основном вследствие структурных напряжений, которые нужно стремиться уменьшить. Структурные напряжения тем больше, чем выше температура закалки и скорость охлаждения в интервале температур Мн и Мк. Для снижения структурных напряжений нужно замедлять скорость охлаждения ниже точки Мн и избегать перегрева стали.
Переход металла из жидкого состояния в твердое (кристаллическое) называется кристаллизацией. Процесс кристаллизации может протекать только при переохлаждении металла ниже равновесной температуры Тп. Разность между температурами Тп и Тк, при которых может протекать процесс кристаллизации, носит название степени переохлаждения:
ΔT=Tп-Тк.
Термические кривые, характеризующие процесс кристаллизации чистых металлов при охлаждении с разной скоростью v, показаны на рисунке
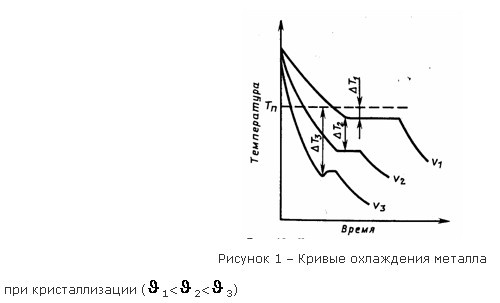
При очень медленном охлаждении степень переохлаждения невелика и процесс кристаллизации протекает при температуре близкой к равновесной Тп. На термической кривой при температуре кристаллизации отмечается горизонтальная площадка (остановка в падении температуры), образование которой объясняется выделением скрытой теплоты кристаллизации, несмотря на отвод теплоты при охлаждении.
С увеличением скорости охлаждения степень переохлаждения возрастает (кривые v2, v3) и процесс кристаллизации протекает при температурах, лежащих значительно ниже равновесной температуры кристаллизации.
Чем больше скорость образования зародышей и меньше скорость роста их, тем меньше размер кристалла (зерна), выросшего из одного зародыша, и, следовательно, более мелкозернистой будет структура металла.
При небольшой скорости переохлаждения ΔT (малой скорости охлаждения) число зародышей мало. В этих условиях будет получено крупное зерно. С увеличением степени переохлаждения скорость образования зародышей возрастает, количество их увеличивается и размер зерна в затвердевшем металле уменьшается.
Размер зерна металла сильно влияет на его механические свойства. Эти свойства, особенно вязкость и пластичность, выше, если металл имеет мелкое зерно.
Что такое холодная деформация? Как при этом изменяются структура и свойства металла?
Холодной деформацией называют такую, которую проводят при температуре ниже температуры рекристаллизации. Поэтому холодная деформация сопровождается упрочнением (наклепом) металла.
Форма заготовки при обработке давлением изменяется под действием внешних сил вследствие пластической деформации каждого кристаллита в соответствии со схемой главных деформаций. Основное изменение формы кристаллитов состоит в том, что они вытягиваются в направлении главной деформации растяжения (например, в направлении прокатки или волочения). С повышением степени холодной деформации зерна все более вытягиваются и структура становится волокнистой.
С увеличением степени холодной деформации показатели сопротивления деформированию (временное сопротивление, предел текучести и твердости) возрастают, а показатели пластичности (относительное удлинение и сужение) падают.
Вычертите диаграмму состояния железо-карбид железа, укажите структурные составляющие во всех областях диаграммы, опишите превращения и постройте кривую охлаждения (с применением правила фаз) для сплава, содержащего 1,6% С. Какова структура этого сплава при комнатной температуре и как такой сплав называется?
Первичная кристаллизация сплавов системы железо-углерод начинается по достижении температур, соответствующих линии ABCD (линии ликвидус), и заканчивается при температурах, образующих линию AHJECF (линию солидус).
При кристаллизации сплавов по линии АВ из жидкого раствора выделяются кристаллы твердого раствора углерода в α-железе (δ-раствор). Процесс кристаллизации сплавов с содержанием углерода до 0,1% заканчивается по линии АН с образованием α (δ)-твердого раствора. На линии HJB протекает перитектическое превращение, в результате которого образуется твердый раствор углерода в γ-железе, т. е. аустенит. Процесс первичной кристаллизации сталей заканчивается по линии AHJE.
При температурах, соответствующих линии ВС, из жидкого раствора кристаллизуется аустенит. В сплавах, содержащих от 4,3% до 6,67% углерода, при температурах, соответствующих линии CD, начинают выделяться кристаллы цементита первичного. Цементит, кристаллизующийся из жидкой фазы, называется первичным. B точке С при температуре 1147°С и концентрации углерода в жидком растворе 4,3 % образуется эвтектика, которая называется ледебуритом. Эвтектическое превращение с образованием ледебурита можно записать формулой ЖР4,3Л[А2,14+Ц6,67]. Процесс первичной кристаллизации чугунов заканчивается по линии ECF образованием ледебурита.
Таким образом, структура чугунов ниже 1147°С будет: доэвтектических — аустенит + ледебурит, эвтектических — ледебурит и заэвтектических — цементит (первичный)+ледебурит.
Превращения, происходящие в твердом состоянии, называются вторичной кристаллизацией. Они связаны с переходом при охлаждении γ-железа в α-железо и распадом аустенита.
Линия GS соответствует температурам начала превращения аустенита в феррит. Ниже линии GS сплавы состоят из феррита и аустенита.
Линия ЕS показывает температуры начала выдел пня цементита из аустенита вследствие уменьшения растворимости углерода в аустените с понижением температуры. Цементит, выделяющийся из аустенита, называется вторичным цементитом.
В точке S при температуре 727°С и концентрации углерода в аустените 0,8 % образуется эвтектоидная смесь состоящая из феррита и цементита, которая называется перлитом. Перлит получается в результате одновременного выпадения из аустенита частиц феррита и цементита. Процесс превращения аустенита в перлит можно записать формулой А0,8П[Ф0,03+Ц6,67].
Линия PQ показывает на уменьшение растворимости углерода в феррите при охлаждении и выделении цементита, который называется третичным цементитом.
Следовательно, сплавы, содержащие менее 0,008% углерода (точкаQ), являются однофазными и имеют структуру чистого феррита, а сплавы, содержащие углерод от 0,008 до 0,03% – структуру феррит + цементит третичный и называются техническим железом.
Доэвтектоидные стали при температуре ниже 727ºС имеют структуру феррит + перлит и заэвтектоидные – перлит + цементит вторичный в виде сетки по границам зерен.
В доэвтектических чугунах в интервале температур 1147–727ºС при охлаждении из аустенита выделяется цементит вторичный, вследствие уменьшения растворимости углерода(линия ES). По достижении температуры 727ºС (линия PSK) аустенит, обедненный углеродом до 0,8% (точка S), превращаясь в перлит. Таким образом, после окончательного охлаждения структура доэвтектических чугунов состоит из перлита, цементита вторичного и ледебурита превращенного (перлит + цементит).
Структура эвтектических чугунов при температурах ниже 727ºС состоит из ледебурита превращенного. Заэвтектический чугун при температурах ниже 727ºС состоит из ледебурита превращенного и цементита первичного.
Правило фаз устанавливает зависимость между числом степеней свободы, числом компонентов и числом фаз и выражается уравнением:
C = K + 1 – Ф,
где С – число степеней свободы системы;
К – число компонентов, образующих систему;
1 – число внешних факторов (внешним фактором считаем только температуру, так как давление за исключением очень высокого мало влияет на фазовое равновесие сплавов в твердом и жидком состояниях);
Ф – число фаз, находящихся в равновесии.
Сплав железа с углеродом, содержащий 1,6%С, называется заэвтектоидной сталью. Его структура при комнатной температуре цементит (вторичный) + перлит.
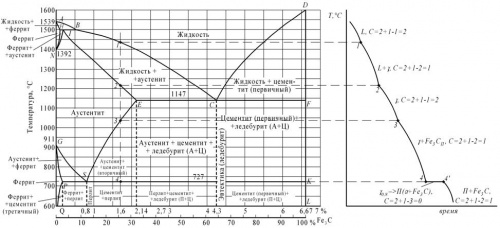
а) б)
Рисунок 2: а-диаграмма железо-цементит, б-кривая охлаждения для сплава, содержащего 1,6% углерода
Используя диаграмму состояния железо – карбид железа и кривую изменения твердости в зависимости от температуры отпуска, назначьте режим термической обработки для углеродистой стали 45, необходимый для обеспечения твердости 550 НВ. Опишите превращения, происходящие на всех этапах термической обработки, и получаемую после обработки структуру.
После закалки с печным нагревом и низкого отпуска (160-180°С) можно получить твердость стали 45 не более 500 НВ. С увеличением температуры отпуска твердость закаленной стали снижается. Так, при высоком отпуске (580-600°С) твердость стали на глубину прокаливания не превышает 250НВ.
Закалка токами высокой частоты (ТВЧ) позволяет получить твердость на 40-60 НВ выше, чем при закалке с печным нагревом. Это объясняется тем, что применение высокоскоростного нагрева и смещение превращений в область температур, превышающих температуру критической точки Ас3 (за счет высокой скорости нагрева), позволяет получить мелкозернистый аустенит, а после охлаждения на глубину прокаливания – мартенсит мелкоигольчатого и безыгольчатого строения. Закалка ТВЧ проводится при температуре 920-940˚С
После закалки ТВЧ изделие подвергают низкому отпуску 160-180˚С. Более высокие температуры применять не следует, так как это приводит к снижению твердости. Низкий отпуск, незначительно снижая твердость закаленного изделия, существенно повышает сопротивление стали хрупкому разрушению. Структура стали после низкого отпуска на глубину прокаливания – мартенсит отпуска.
В результате термической обработки твердость изделия на глубину прокаливания составит 550 НВ.
Каковы причины возникновения внутренних напряжений при закалке? Каким способом можно предохранить изделие от образования закалочных трещин?
Внутренние напряжения при закалке стали возникают вследствие неравномерного охлаждения поверхности и сердцевины изделия (эти напряжения называют тепловыми), увеличения объема и неоднородности протекания мартенситного превращения по объему изделия. Напряжения, вызываемые этим превращением, называют структурными, или фазовыми.
Неодинаковое распределение температур по сечению изделия при быстром охлаждении сопровождается и неравномерным изменением объема. Поверхностные слои сжимаются быстрее, чем внутренние. Однако сжатию поверхностных слоев препятствуют внутренние слои. Это приводит к тому, что в поверхностных слоях образуются временные (т.е. исчезающие после снятия нагрузки) растягивающие, а во внутренних слоях — сжимающие напряжения.
Рассмотрим теперь условия образования структурных напряжений при полной прокаливаемости. При этом тепловые напряжения условно учитываться не будут.
По достижении при закалке температур ниже точки Мн мартенсит в первую очередь образуется на поверхности, где точка Мн будет достигнута раньше, чем в сердцевине. Так как превращение аустенит – мартенсит сопровождается увеличением объема, то это приводит к образованию на поверхности временных сжимающих напряжений, а во внутренних слоях – растягивающих напряжений. По мере развития превращения знак напряжений на поверхности и в сердцевине меняется.
Структурные напряжения относительно тепловых изменяются в обратном порядке. В результате мартенситного превращения на поверхности образуются остаточные напряжения растяжения, а в сердцевине – напряжения сжатия. Эти остаточные напряжения, как и тепловые, возникают в результате появления под действием временных напряжений не только упругой, но и неодинаковой по сечению остаточной деформации.
При закалке стали одновременно возникают как тепловые, так и структурные напряжения, которые суммируют. В данной схеме тепловые напряжения превышали структурные, поэтому на поверхности образовались напряжения сжатия. Однако в зависимости от соотношения между тепловыми и структурными напряжениями могут получиться различные эпюры суммарных напряжений, а в поверхностных слоях напряжения могут иметь разный знак и различную величину. Во многих случаях величина фазовых напряжений больше, чем величина тепловых.
Остаточные напряжения, полученные после закалки, не характеризуют напряжения, возникающие при охлаждении (нагреве) стали. Остаточные напряжения всегда меньше временных напряжений, образующихся в процессе охлаждения.
Если величина напряжений превышает сопротивление отрыву и металл мало пластичен, то напряжения не могут быть уменьшены пластической деформацией. Это вызывает образование трещин. Наиболее опасны при этом растягивающие напряжения на поверхности, которые способствуют образованию трещин и снижают предел выносливости стали.
Растягивающие напряжения возникают в основном вследствие структурных напряжений, которые нужно стремиться уменьшить. Структурные напряжения тем больше, чем выше температура закалки и скорость охлаждения в интервале температур Мн и Мк. Для снижения структурных напряжений нужно замедлять скорость охлаждения ниже точки Мн и избегать перегрева стали.
0 комментариев