Контрольная работа 1 Вариант 21
Каковы характерные свойства металлов и чем они определяются?
Свойства обусловлены особенностями строения металлов. Согласно теории металлического состояния, металл представляет собой вещество, состоящее из положительных ядер, вокруг которых по орбиталям вращаются электроны. На последнем уровне число электронов невелико и они слабо связаны с ядром. Эти электроны имеют возможность перемещаться по всему объему металла, т.е. принадлежать целой совокупности атомов.
Металлы в твердом и отчасти в жидком состоянии обладают рядом характерных свойств:
– высокими теплопроводностью и электрической проводимостью;
– положительным температурным коэффициентом электрического сопротивления; с повышением температуры электрическое сопротивление чистых металлов возрастает; большое число металлов обладают сверхпроводимостью (у этих металлов при температуре, близкой к абсолютному нулю, электрическое сопротивление падает скачкообразно, практически до нуля);
– термоэлектронной эмиссией, т. е. способностью испускать электроны при нагреве;
– хорошей отражательной способностью: металлы непрозрачны и обладают металлическим блеском;
– повышенной способностью к пластической деформации.
Таким образом, пластичность, теплопроводность и электропроводность обеспечиваются наличием «электронного газа».
Как устанавливается температура порога рекристаллизации металла и сплава? Приведите несколько конкретных примеров.
Рекристаллизация – процесс зарождения и роста новых недеформированных зерен при нагреве наклепанного металла до определенной температуры.
Наименьшую температуру начала рекристаллизации, при которой протекает рекристаллизация и происходит разупрочнение металла, называют температурным порогом рекристаллизации. Эта температура не является постоянной физической величиной. Для данного металла (сплава) она зависит от длительности нагрева, степени предварительной деформации, величины зерна до деформации и т. д.
Температура начала рекристаллизации металлов, подвергнутых значительной деформации, для технически чистых металлов составляет примерно 0,4 Тпл (правило А.А. Бочвара), для чистых металлов снижается до (0,1...0,2)Тпл, а для сплавов твердых растворов возрастает до (0,5...0,6)Тпл.
Т. е. с повышением чистоты металла температурный порог рекристаллизации снижается:

Сильно влияет на температуру начала рекристаллизации степень деформации при обработке давлением. С увеличением степени деформации температура начала рекристаллизации снижается. Объясняется это тем, что с увеличением степени деформации растут плотность дислокаций и энергия, накопленная при деформации, т. е. возрастает термодинамический стимул рекристаллизации.
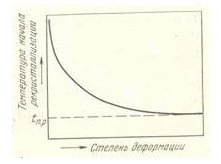
Т. к. плотность дислокаций и соответственно накопленная при деформации энергия с увеличением степени деформации растут с затуханием, то и температура начала рекристаллизации снижается при увеличении степени деформации с затуханием, достигая определенного предела при данном времени отжига.
Рекристаллизационный отжиг используют в промышленности как первоначальную операцию перед холодной обработкой давлением (для придания материалу наибольшей пластичности), как промежуточный процесс между операциями холодного деформирования (для снятия наклепа) и как окончательную (выходную) термическую обработку (для придания полуфабрикату или изделию необходимых свойств).
Вычертите диаграмму состояния железо – карбид железа, укажите структурные составляющие во всех областях диаграммы, опишите превращения и постройте кривую охлаждения (с применением правила фаз) для сплава, содержащего 0,3% С. Какова структура этого сплава при комнатной температуре и как такой сплав называется?
Первичная кристаллизация сплавов системы железо-углерод начинается по достижении температур, соответствующих линии ABCD (линии ликвидус), и заканчивается при температурах, образующих линию AHJECF (линию солидус).
При кристаллизации сплавов по линии АВ из жидкого раствора выделяются кристаллы твердого раствора углерода в α-железе (δ-раствор). Процесс кристаллизации сплавов с содержанием углерода до 0,1 % заканчивается по линии АН с образованием α (δ)-твердого раствора. На линии HJB протекает перитектическое превращение, в результате которого образуется твердый раствор углерода в γ-железе, т. е. аустенит. Процесс первичной кристаллизации сталей заканчивается по линии AHJE.
При температурах, соответствующих линии ВС, из жидкого раствора кристаллизуется аустенит. В сплавах, содержащих от 4,3 % до 6,67 % углерода, при температурах, соответствующих линии CD, начинают выделяться кристаллы цементита первичного. Цементит, кристаллизующийся из жидкой фазы, называется первичным. B точке С при температуре 1147°С и концентрации углерода в жидком растворе 4,3 % образуется эвтектика, которая называется ледебуритом. Эвтектическое превращение с образованием ледебурита можно записать формулой ЖР4,3Л[А2,14+Ц6,67]. Процесс первичной кристаллизации чугунов заканчивается по линии ECF образованием ледебурита.
Таким образом, структура чугунов ниже 1147°С будет: доэвтектических – аустенит+ледебурит, эвтектических – ледебурит и заэвтектических – цементит (первичный)+ледебурит.
Превращения, происходящие в твердом состоянии, называются вторичной кристаллизацией. Они связаны с переходом при охлаждении γ-железа в α-железо и распадом аустенита.
Линия GS соответствует температурам начала превращения аустенита в феррит. Ниже линии GS сплавы состоят из феррита и аустенита.
Линия ЕS показывает температуры начала выделения цементита из аустенита вследствие уменьшения растворимости углерода в аустените с понижением температуры. Цементит, выделяющийся из аустенита, называется вторичным цементитом.
В точке S при температуре 727°С и концентрации углерода в аустените 0,8 % образуется эвтектоидная смесь состоящая из феррита и цементита, которая называется перлитом. Перлит получается в результате одновременного выпадения из аустенита частиц феррита и цементита. Процесс превращения аустенита в перлит можно записать формулой А0,8П[Ф0,03+Ц6,67].
Линия PQ показывает на уменьшение растворимости углерода в феррите при охлаждении и выделении цементита, который называется третичным цементитом.
Следовательно, сплавы, содержащие менее 0,008% углерода (точкаQ), являются однофазными и имеют структуру чистого феррита, а сплавы, содержащие углерод от 0,008 до 0,03% – структуру феррит+цементит третичный и называются техническим железом.
Доэвтектоидные стали при температуре ниже 727ºС имеют структуру феррит+перлит и заэвтектоидные – перлит+цементит вторичный в виде сетки по границам зерен.
В доэвтектических чугунах в интервале температур 1147–727ºС при охлаждении из аустенита выделяется цементит вторичный, вследствие уменьшения растворимости углерода (линия ES). По достижении температуры 727ºС (линия PSK) аустенит, обедненный углеродом до 0,8% (точка S), превращаясь в перлит. Таким образом, после окончательного охлаждения структура доэвтектических чугунов состоит из перлита, цементита вторичного и ледебурита превращенного (перлит+цементит).
Структура эвтектических чугунов при температурах ниже 727ºС состоит из ледебурита превращенного. Заэвтектический чугун при температурах ниже 727ºС состоит из ледебурита превращенного и цементита первичного.
Правило фаз устанавливает зависимость между числом степеней свободы, числом компонентов и числом фаз и выражается уравнением:
C = K + 1 – Ф,
где С – число степеней свободы системы;
К – число компонентов, образующих систему;
1 – число внешних факторов (внешним фактором считаем только температуру, так как давление за исключением очень высокого мало влияет на фазовое равновесие сплавов в твердом и жидком состояниях);
Ф – число фаз, находящихся в равновесии.
Сплав железа с углеродом, содержащий 0,3 %С, называется доэвтектоидной сталью. Его структура при комнатной температуре – перлит + ферррит.
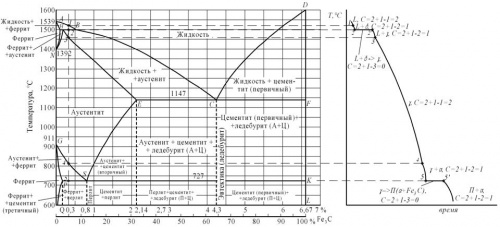
а) б)
Рисунок 1: а-диаграмма железо-цементит, б-кривая охлаждения для сплава, содержащего 0,3% углерода
После закалки углеродистой стали была получена структура мартенсит + цементит. Нанесите на диаграмму состояния железо-цементит ординату (примерно) обрабатываемой стали, укажите температуру ее нагрева под закалку. Опишите превращения, которые произошли при нагреве и охлаждении стали.
Структура мартенсит + цементит соответствует закаленной заэвтектоидной углеродистой стали. Стали, содержащие от 0,8 до 2,14% углерода, называются заэвтектоидными. Выше линии ES в этих сплавах будет только аустенит.
При температурах, соответствующих линии ES, аустенит оказывается насыщенным углеродом, и при понижении температуры из него выделяется вторичный цементит. Поэтому при температуре ниже линии ES сплавы становятся двухфазными (аустенит + вторичный цементит). По мере выделения цементита концентрация углерода в аустените уменьшается согласно линии ES.
При снижении температуры до А1 (727°С) аустенит, содержащий 0,8%С (точка S), превращается в перлит. После охлаждения заэвтектоидные стали состоят из перлита и вторичного цементита, который выделяется в виде сетки по границам бывшего зерна аустенита или в виде игл (пластин), закономерно ориентированных относительно аустенита. Количество избыточного (вторичного) цементита возрастает с увеличением содержания в стали углерода.
Выделение вторичного цементита в виде сетки и игл делает таль хрупкой. Поэтому специальной термической обработкой и деформацией его придают зернистую форму.
Из заэвтектоидных сталей выбираем сталь У10, содержащую 0,95 -1,04 %С. Ее критические точки: Ас1=730°С, Аcm=800°С. Температура нагрева под закалку назначается из условия: Ас1 + (30 ¸ 50) = 760 ¸ 780°С.
Закалкой называется нагрев стали до температур выше фазовых превращений, выдержка при этой температуре и быстрое охлаждение со скоростью больше критической.
В результате закалки из аустенита образуется неустойчивая структура мартенсит.
Закалка стали У10 заключается в нагреве до температуры 760 – 780°С, выдержке и охлаждении в воде. Охлаждение в воде обеспечивает скорость охлаждения выше критической. В результате закалки получаем структуру мартенсит. Мартенсит представляет собой пересыщенный твердый раствор углерода в α-железе.
Изделия из стали 45 требуется подвергнуть улучшению. Назначьте режим термической обработки, опишите сущность происходящих превращений, структуру и свойства стали после обработки.
Улучшение заключается в закалке и высоком отпуске стали.
Закалка доэвтектоидной стали заключается в нагреве стали до температуры выше критической (Ас3), в выдержке и последующем охлаждении со скоростью, превышающей критическую.
Доэвтектоидные стали для закалки следует нагревать до температуры на 30-50°С выше Ас3. Температура точки Ас3 для стали 45 составляет 755°С, а Ас1 равна 730°С. Структура доэвтектоидной стали при нагреве её до критической точки Ас1 состоит из зерен перлита и феррита. В точке Ас1 происходит превращение перлита в мелкозернистый аустенит. При дальнейшем нагреве от точки Ас1 до Ас3 избыточный феррит растворяется в аустените и при достижении Ас3 (линия GS) превращения заканчиваются.
Температура нагрева стали под закалку, таким образом, составляет 800-820°С. Структура стали 45 при температуре нагрева под закалку – аустенит, после охлаждения со скоростью выше критической – мартенсит.
Высокий отпуск проводится при температуре 580-600˚С. В результате получаем структуру – сорбит отпуска. Высокий отпуск создает наилучшее соотношение прочности и вязкости.
Закалка с высоким отпуском (по сравнению с нормализацией или отжигом) повышает временное сопротивление, предел текучести, относительное сужение и особенно ударную вязкость. Высокие отпуск почти полностью снимает остаточные напряжения, возникшие при закалке.
Свойства стали 45 после улучшения: σВ = 870 МПа; σт= 700 МПа; δ= 13%; ψ = 65%; KCU = 1,3 МДж/м2; НВ = 255.
Свойства обусловлены особенностями строения металлов. Согласно теории металлического состояния, металл представляет собой вещество, состоящее из положительных ядер, вокруг которых по орбиталям вращаются электроны. На последнем уровне число электронов невелико и они слабо связаны с ядром. Эти электроны имеют возможность перемещаться по всему объему металла, т.е. принадлежать целой совокупности атомов.
Металлы в твердом и отчасти в жидком состоянии обладают рядом характерных свойств:
– высокими теплопроводностью и электрической проводимостью;
– положительным температурным коэффициентом электрического сопротивления; с повышением температуры электрическое сопротивление чистых металлов возрастает; большое число металлов обладают сверхпроводимостью (у этих металлов при температуре, близкой к абсолютному нулю, электрическое сопротивление падает скачкообразно, практически до нуля);
– термоэлектронной эмиссией, т. е. способностью испускать электроны при нагреве;
– хорошей отражательной способностью: металлы непрозрачны и обладают металлическим блеском;
– повышенной способностью к пластической деформации.
Таким образом, пластичность, теплопроводность и электропроводность обеспечиваются наличием «электронного газа».
Как устанавливается температура порога рекристаллизации металла и сплава? Приведите несколько конкретных примеров.
Рекристаллизация – процесс зарождения и роста новых недеформированных зерен при нагреве наклепанного металла до определенной температуры.
Наименьшую температуру начала рекристаллизации, при которой протекает рекристаллизация и происходит разупрочнение металла, называют температурным порогом рекристаллизации. Эта температура не является постоянной физической величиной. Для данного металла (сплава) она зависит от длительности нагрева, степени предварительной деформации, величины зерна до деформации и т. д.
Температура начала рекристаллизации металлов, подвергнутых значительной деформации, для технически чистых металлов составляет примерно 0,4 Тпл (правило А.А. Бочвара), для чистых металлов снижается до (0,1...0,2)Тпл, а для сплавов твердых растворов возрастает до (0,5...0,6)Тпл.
Т. е. с повышением чистоты металла температурный порог рекристаллизации снижается:

Сильно влияет на температуру начала рекристаллизации степень деформации при обработке давлением. С увеличением степени деформации температура начала рекристаллизации снижается. Объясняется это тем, что с увеличением степени деформации растут плотность дислокаций и энергия, накопленная при деформации, т. е. возрастает термодинамический стимул рекристаллизации.
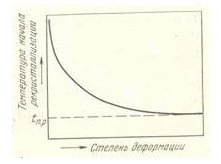
Т. к. плотность дислокаций и соответственно накопленная при деформации энергия с увеличением степени деформации растут с затуханием, то и температура начала рекристаллизации снижается при увеличении степени деформации с затуханием, достигая определенного предела при данном времени отжига.
Рекристаллизационный отжиг используют в промышленности как первоначальную операцию перед холодной обработкой давлением (для придания материалу наибольшей пластичности), как промежуточный процесс между операциями холодного деформирования (для снятия наклепа) и как окончательную (выходную) термическую обработку (для придания полуфабрикату или изделию необходимых свойств).
Вычертите диаграмму состояния железо – карбид железа, укажите структурные составляющие во всех областях диаграммы, опишите превращения и постройте кривую охлаждения (с применением правила фаз) для сплава, содержащего 0,3% С. Какова структура этого сплава при комнатной температуре и как такой сплав называется?
Первичная кристаллизация сплавов системы железо-углерод начинается по достижении температур, соответствующих линии ABCD (линии ликвидус), и заканчивается при температурах, образующих линию AHJECF (линию солидус).
При кристаллизации сплавов по линии АВ из жидкого раствора выделяются кристаллы твердого раствора углерода в α-железе (δ-раствор). Процесс кристаллизации сплавов с содержанием углерода до 0,1 % заканчивается по линии АН с образованием α (δ)-твердого раствора. На линии HJB протекает перитектическое превращение, в результате которого образуется твердый раствор углерода в γ-железе, т. е. аустенит. Процесс первичной кристаллизации сталей заканчивается по линии AHJE.
При температурах, соответствующих линии ВС, из жидкого раствора кристаллизуется аустенит. В сплавах, содержащих от 4,3 % до 6,67 % углерода, при температурах, соответствующих линии CD, начинают выделяться кристаллы цементита первичного. Цементит, кристаллизующийся из жидкой фазы, называется первичным. B точке С при температуре 1147°С и концентрации углерода в жидком растворе 4,3 % образуется эвтектика, которая называется ледебуритом. Эвтектическое превращение с образованием ледебурита можно записать формулой ЖР4,3Л[А2,14+Ц6,67]. Процесс первичной кристаллизации чугунов заканчивается по линии ECF образованием ледебурита.
Таким образом, структура чугунов ниже 1147°С будет: доэвтектических – аустенит+ледебурит, эвтектических – ледебурит и заэвтектических – цементит (первичный)+ледебурит.
Превращения, происходящие в твердом состоянии, называются вторичной кристаллизацией. Они связаны с переходом при охлаждении γ-железа в α-железо и распадом аустенита.
Линия GS соответствует температурам начала превращения аустенита в феррит. Ниже линии GS сплавы состоят из феррита и аустенита.
Линия ЕS показывает температуры начала выделения цементита из аустенита вследствие уменьшения растворимости углерода в аустените с понижением температуры. Цементит, выделяющийся из аустенита, называется вторичным цементитом.
В точке S при температуре 727°С и концентрации углерода в аустените 0,8 % образуется эвтектоидная смесь состоящая из феррита и цементита, которая называется перлитом. Перлит получается в результате одновременного выпадения из аустенита частиц феррита и цементита. Процесс превращения аустенита в перлит можно записать формулой А0,8П[Ф0,03+Ц6,67].
Линия PQ показывает на уменьшение растворимости углерода в феррите при охлаждении и выделении цементита, который называется третичным цементитом.
Следовательно, сплавы, содержащие менее 0,008% углерода (точкаQ), являются однофазными и имеют структуру чистого феррита, а сплавы, содержащие углерод от 0,008 до 0,03% – структуру феррит+цементит третичный и называются техническим железом.
Доэвтектоидные стали при температуре ниже 727ºС имеют структуру феррит+перлит и заэвтектоидные – перлит+цементит вторичный в виде сетки по границам зерен.
В доэвтектических чугунах в интервале температур 1147–727ºС при охлаждении из аустенита выделяется цементит вторичный, вследствие уменьшения растворимости углерода (линия ES). По достижении температуры 727ºС (линия PSK) аустенит, обедненный углеродом до 0,8% (точка S), превращаясь в перлит. Таким образом, после окончательного охлаждения структура доэвтектических чугунов состоит из перлита, цементита вторичного и ледебурита превращенного (перлит+цементит).
Структура эвтектических чугунов при температурах ниже 727ºС состоит из ледебурита превращенного. Заэвтектический чугун при температурах ниже 727ºС состоит из ледебурита превращенного и цементита первичного.
Правило фаз устанавливает зависимость между числом степеней свободы, числом компонентов и числом фаз и выражается уравнением:
C = K + 1 – Ф,
где С – число степеней свободы системы;
К – число компонентов, образующих систему;
1 – число внешних факторов (внешним фактором считаем только температуру, так как давление за исключением очень высокого мало влияет на фазовое равновесие сплавов в твердом и жидком состояниях);
Ф – число фаз, находящихся в равновесии.
Сплав железа с углеродом, содержащий 0,3 %С, называется доэвтектоидной сталью. Его структура при комнатной температуре – перлит + ферррит.
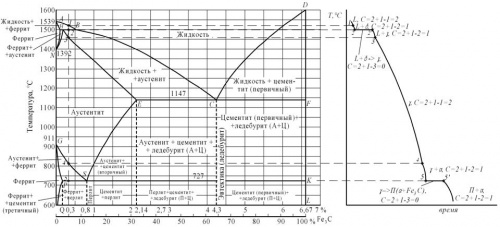
а) б)
Рисунок 1: а-диаграмма железо-цементит, б-кривая охлаждения для сплава, содержащего 0,3% углерода
После закалки углеродистой стали была получена структура мартенсит + цементит. Нанесите на диаграмму состояния железо-цементит ординату (примерно) обрабатываемой стали, укажите температуру ее нагрева под закалку. Опишите превращения, которые произошли при нагреве и охлаждении стали.
Структура мартенсит + цементит соответствует закаленной заэвтектоидной углеродистой стали. Стали, содержащие от 0,8 до 2,14% углерода, называются заэвтектоидными. Выше линии ES в этих сплавах будет только аустенит.
При температурах, соответствующих линии ES, аустенит оказывается насыщенным углеродом, и при понижении температуры из него выделяется вторичный цементит. Поэтому при температуре ниже линии ES сплавы становятся двухфазными (аустенит + вторичный цементит). По мере выделения цементита концентрация углерода в аустените уменьшается согласно линии ES.
При снижении температуры до А1 (727°С) аустенит, содержащий 0,8%С (точка S), превращается в перлит. После охлаждения заэвтектоидные стали состоят из перлита и вторичного цементита, который выделяется в виде сетки по границам бывшего зерна аустенита или в виде игл (пластин), закономерно ориентированных относительно аустенита. Количество избыточного (вторичного) цементита возрастает с увеличением содержания в стали углерода.
Выделение вторичного цементита в виде сетки и игл делает таль хрупкой. Поэтому специальной термической обработкой и деформацией его придают зернистую форму.
Из заэвтектоидных сталей выбираем сталь У10, содержащую 0,95 -1,04 %С. Ее критические точки: Ас1=730°С, Аcm=800°С. Температура нагрева под закалку назначается из условия: Ас1 + (30 ¸ 50) = 760 ¸ 780°С.
Закалкой называется нагрев стали до температур выше фазовых превращений, выдержка при этой температуре и быстрое охлаждение со скоростью больше критической.
В результате закалки из аустенита образуется неустойчивая структура мартенсит.
Закалка стали У10 заключается в нагреве до температуры 760 – 780°С, выдержке и охлаждении в воде. Охлаждение в воде обеспечивает скорость охлаждения выше критической. В результате закалки получаем структуру мартенсит. Мартенсит представляет собой пересыщенный твердый раствор углерода в α-железе.
Изделия из стали 45 требуется подвергнуть улучшению. Назначьте режим термической обработки, опишите сущность происходящих превращений, структуру и свойства стали после обработки.
Улучшение заключается в закалке и высоком отпуске стали.
Закалка доэвтектоидной стали заключается в нагреве стали до температуры выше критической (Ас3), в выдержке и последующем охлаждении со скоростью, превышающей критическую.
Доэвтектоидные стали для закалки следует нагревать до температуры на 30-50°С выше Ас3. Температура точки Ас3 для стали 45 составляет 755°С, а Ас1 равна 730°С. Структура доэвтектоидной стали при нагреве её до критической точки Ас1 состоит из зерен перлита и феррита. В точке Ас1 происходит превращение перлита в мелкозернистый аустенит. При дальнейшем нагреве от точки Ас1 до Ас3 избыточный феррит растворяется в аустените и при достижении Ас3 (линия GS) превращения заканчиваются.
Температура нагрева стали под закалку, таким образом, составляет 800-820°С. Структура стали 45 при температуре нагрева под закалку – аустенит, после охлаждения со скоростью выше критической – мартенсит.
Высокий отпуск проводится при температуре 580-600˚С. В результате получаем структуру – сорбит отпуска. Высокий отпуск создает наилучшее соотношение прочности и вязкости.
Закалка с высоким отпуском (по сравнению с нормализацией или отжигом) повышает временное сопротивление, предел текучести, относительное сужение и особенно ударную вязкость. Высокие отпуск почти полностью снимает остаточные напряжения, возникшие при закалке.
Свойства стали 45 после улучшения: σВ = 870 МПа; σт= 700 МПа; δ= 13%; ψ = 65%; KCU = 1,3 МДж/м2; НВ = 255.
0 комментариев