Контрольная работа 1 Вариант 26
Объясните сущность явления дендритной ликвации и методы ее устранения.
Ликвация – неоднородность химического состава сплавов, возникающая при кристаллизации.
Ликвация обусловлена тем, что сплавы, в отличие от чистых металлов, кристаллизуются не при одной температуре, а в интервале температур.При этом состав кристаллов, образующихся в начале затвердевания, может существенно отличаться от состава последних капель
кристаллизующегося маточного раствора. Чем шире температурный интервал кристаллизации сплава, тем сильнее развивается ликвация, причем наибольшую склонность к ней проявляют те компоненты сплава, которые наиболее сильно влияют на ширину интервала кристаллизации (для стали – сера, кислород, фосфор, углерод). Ликвация оказывает, как правило, вредное влияние на качество металла.
Дендритная ликвация проявляется в микрообъемах сплава, близких к размеру зерен.
Дендритная ликвация может быть ослаблена продолжительным нагревом затвердевшего сплава при температурах, обеспечивающих достаточную скорость диффузии (несколько ниже солидуса). После такого нагрева, называемого диффузионным отжигом или гомогенизацией, дендритная структура литого сплава уже не выявляется и сплав состоит из однородных кристаллов твердого раствора.
Диффузионный отжиг – это термическая обработка, при которой главным процессом является устранение последствий дендритной ликвации.
Слитки из углеродистых сталей обычно не подвергают диффузионному отжигу, так как в них при нагреве под горячую обработку давлением из-за быстрой диффузии углерода в аустените дендритная ликвация успевает исчезнуть. Диффузионному отжигу подвергают слитки легированной стали с целью уменьшения дендритной или внутрикристаллитной ликвации, которая повышает склонность стали, обрабатываемой давлением, к хрупкому излому, к анизотропии свойств и возникновению таких дефектов, как шиферность (слоистый излом) и флокены (тонкие; внутренние трещины, наблюдаемые в изломе в виде белых овальных пятен).
Дендритная ликвация понижает пластичность и вязкость легированной стали. Поэтому слитки и крупные отливки нередко подвергают гомогенизирующему или диффузионному отжигу. Нагрев при диффузионном отжиге должен быть до высоких температур 1100-1200°С, так как только в этом случае более полно протекают диффузионные процессы, необходимые для выравнивания в отдельных объемах состава стали. Диффузия наиболее интенсивно протекает в начале выдержки, заметно снижаясь с течением времени. Поэтому во избежание образования большого количества окалины, уменьшения расхода топлива и увеличения производительности печей выдержка должна быть минимальной, обычно 15-20 ч. После выдержки садку охлаждают до 800-820°С в печи, а далее на воздухе.
Во многих случаях для уменьшения дендритной ликвации не проводят специального диффузионного отжига, а выполняют более высокий и длительный нагрев для горячей деформации. В результате диффузионного отжига получается крупное зерно. Этот недостаток устраняется при последующей обработке слитка давлением или в процессе последующей термической обработке.
Какими стандартными характеристиками механических свойств описывается пластичность металлов и сплавов? Как они определяются?
Пластичность – свойство твердых тел необратимо деформироваться под действием механических нагрузок.
Отсутствие или небольшое значение пластичности называется хрупкостью.
Характеристики пластичности определяют при статических испытаниях. Статическими называют испытания, при которых прилагаемая нагрузка возрастает медленно и плавно. Чаще применяют испытания на растяжение, позволяющие по результатам одного опыта установить нескольких важных механических характеристик металла или сплава. Для испытания на растяжение используют стандартные образцы (ГОСТ 1497-84). Машины для испытания снабжены прибором, записывающим диаграмму растяжения (рисунок 1).
Относительное удлинение характеризует пластичность материала.
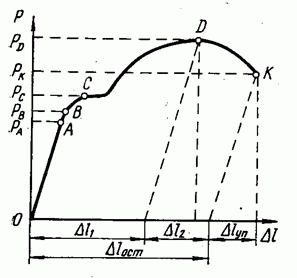
Рисунок 1 – Диаграмма растяжения образца из низкоуглеродистой стали
Относительное удлинение δ представляет собой отношение приращения длины образца после его разрыва к первоначальной расчетной длине l0 и выражается в процентах:
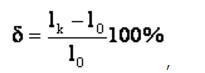
где lк – длина образца после разрыва
Под относительным сужением понимают отношение уменьшения поперечного сечения разорванного образца к первоначальной площади поперечного сечения, выраженное в процентах:
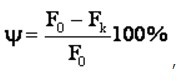
где Fк – площадь поперечного сечения в месте разрыва.
Вычертите диаграмму состояния железо-карбид железа, укажите структурные составляющие во всех областях диаграммы, опишите превращения и постройте кривую охлаждения (с применением правила фаз) для сплава, содержащего 1,2%С. Какова структура этого сплава при комнатной температуре и как такой сплав называется?
Первичная кристаллизация сплавов системы железо-углерод начинается по достижении температур, соответствующих линии ABCD (линии ликвидус), и заканчивается при температурах, образующих линию AHJECF (линию солидус).
При кристаллизации сплавов по линии АВ из жидкого раствора выделяются кристаллы твердого раствора углерода в α-железе (δ-раствор). Процесс кристаллизации сплавов с содержанием углерода до 0,1% заканчивается по линии АН с образованием α (δ)-твердого раствора. На линии HJB протекает перитектическое превращение, в результате которого образуется твердый раствор углерода в γ-железе, т. е. аустенит. Процесс первичной кристаллизации сталей заканчивается по линии AHJE.
При температурах, соответствующих линии ВС, из жидкого раствора кристаллизуется аустенит. В сплавах, содержащих от 4,3% до 6,67% углерода, при температурах, соответствующих линии CD, начинают выделяться кристаллы цементита первичного. Цементит, кристаллизующийся из жидкой фазы, называется первичным. B точке С при температуре 1147°С и концентрации углерода в жидком растворе 4,3% образуется эвтектика, которая называется ледебуритом. Эвтектическое превращение с образованием ледебурита можно записать формулой ЖР4,3Л[А2,14+Ц6,67]. Процесс первичной кристаллизации чугунов заканчивается по линии ECF образованием ледебурита.
Таким образом, структура чугунов ниже 1147°С будет: доэвтектических – аустенит + ледебурит, эвтектических – ледебурит и заэвтектических – цементит (первичный) + ледебурит.
Превращения, происходящие в твердом состоянии, называются вторичной кристаллизацией. Они связаны с переходом при охлаждении γ-железа в α-железо и распадом аустенита.
Линия GS соответствует температурам начала превращения аустенита в феррит. Ниже линии GS сплавы состоят из феррита и аустенита.
Линия ЕS показывает температуры начала выделения цементита из аустенита вследствие уменьшения растворимости углерода в аустените с понижением температуры. Цементит, выделяющийся из аустенита, называется вторичным цементитом.
В точке S при температуре 727°С и концентрации углерода в аустените 0,8% образуется эвтектоидная смесь состоящая из феррита и цементита, которая называется перлитом. Перлит получается в результате одновременного выпадения из аустенита частиц феррита и цементита. Процесс превращения аустенита в перлит можно записать формулой А0,8П[Ф0,03+Ц6,67].
Линия PQ показывает на уменьшение растворимости углерода в феррите при охлаждении и выделении цементита, который называется третичным цементитом.
Следовательно, сплавы, содержащие менее 0,008% углерода (точкаQ), являются однофазными и имеют структуру чистого феррита, а сплавы, содержащие углерод от 0,008 до 0,03% – структуру феррит + цементит третичный и называются техническим железом.
Доэвтектоидные стали при температуре ниже 727ºС имеют структуру феррит + перлит и заэвтектоидные – перлит + цементит вторичный в виде сетки по границам зерен.
В доэвтектических чугунах в интервале температур 1147-727ºС при охлаждении из аустенита выделяется цементит вторичный, вследствие уменьшения растворимости углерода (линия ES). По достижении температуры 727ºС (линия PSK) аустенит, обедненный углеродом до 0,8% (точка S), превращаясь в перлит. Таким образом, после окончательного охлаждения структура доэвтектических чугунов состоит из перлита, цементита вторичного и ледебурита превращенного (перлит + цементит).
Структура эвтектических чугунов при температурах ниже 727ºС состоит из ледебурита превращенного. Заэвтектический чугун при температурах ниже 727ºС состоит из ледебурита превращенного и цементита первичного.
Правило фаз устанавливает зависимость между числом степеней свободы, числом компонентов и числом фаз и выражается уравнением:
C = K + 1 – Ф,
где С – число степеней свободы системы;
К – число компонентов, образующих систему;
1 – число внешних факторов (внешним фактором считаем только температуру, так как давление за исключением очень высокого мало влияет на фазовое равновесие сплавов в твердом и жидком состояниях);
Ф – число фаз, находящихся в равновесии.
Сплав железа с углеродом, содержащий 1,2%С, называется заэвтектоидной сталью. Его структура при комнатной температуре цементит + перлит.
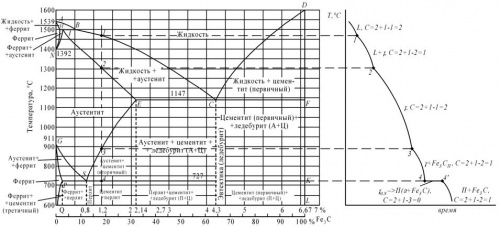
а) б)
Рисунок 2: а — диаграмма железо-цементит, б — кривая охлаждения для сплава, содержащего 1,2% углерода
Как можно устранить крупнозернистую структуру в кованой стали 30? Используя диаграмму состояния железо-цементит, обоснуйте выбор режима термической обработки для исправления структуры. Опишите структурные превращения и характер изменения свойств.
Крупнозернистую структуру в кованой стали 30 можно устранить отжигом при температуре 850-870°С (рисунок 3).
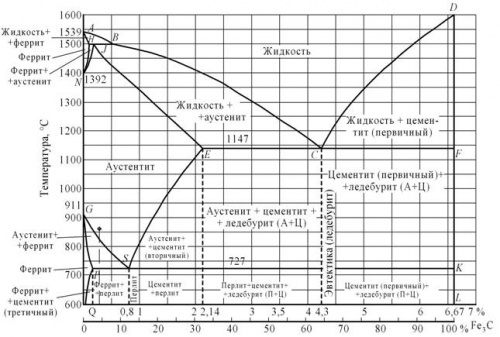
Рисунок 3 – Диаграмма состояния железо-углерод
После отжига в стали 30 получается структура феррит + перлит. Сталь имеет низкую твердость (НВ не более 1870 МПа) и прочность при высокой пластичности. При фазовой перекристаллизации измельчается зерно. Понижая прочность и твердость, отжиг облегчает обработку, резание среднеуглеродистой стали. Измельчая зерно, снимая внутренние напряжения и уменьшая структурную неоднородность, отжиг способствует повышению пластичности и вязкости по сравнению со свойствами, полученными после ковки. При нагреве до температуры выше точки Ас3 (820°С) на 30-50°С образуется аустенит, характеризующийся мелким зерном, поэтому при охлаждении возникает мелкозернистая структура, обеспечивающая высокую вязкость и пластичность и возможность достижения высоких свойств после окончательной термической обработки. Чрезмерное повышение температуры нагрева выше точки Ас3 вызывает рост зерна аустенита, что ухудшает свойства стали.
Укажите температуры, при которых производится процесс прочностного азотирования. Объясните, почему азотирование не производится при температурах ниже 500 и выше 700°С (используя диаграмму состояния железо-азот). Назовите марки сталей, применяемых для азотирования, и опишите полный цикл их термической и химико-термической обработки.
Азотированием называется химико-термическая обработка, заключающаяся в диффузионном насыщении поверхностного слоя стали азотом.
Упрочнение при азотировании достигается за счет фаз, образующихся из твердых растворов на базе нитридов. Азотирования при температурах ниже 500°С не производится, т.к. этих температур не достаточно для образования упрочняющих фаз (ε, γ΄, γ, α) (рисунок 4).
Азотирование является окончательной термической обработкой. Ему обычно предшествует термическая обработка, заключающаяся в закалке и высоком отпуске стали, для получения повышенной прочности и вязкости в сердцевине изделия. Отпуск проводят при высокой температуре 600-675°С, превышающей максимальную температуру последующего азотирования и обеспечивающей получение твердости, при которой сталь можно обрабатывать резанием. Структура стали после этого отпуска – сорбит отпуска. Поэтому для сохранения полученных в результате улучшения свойств не следует назначать температуру азотирования выше температуры высокого отпуска.
Обычно азотированию подвергают конструкционные стали, содержащие алюминий: 38Х2МЮА, 38Х2Ю и т.д. и не содержащие алюминия: 40Х, 40ХФ, 18ХГТ, 30ХГТ, 40ХНМА, 20Х3ВА, 30Х3МФ, 18Х2Н4ВА и т.д. Стали без алюминия технологичнее, многие из них имеют более высокие механические свойства, чем сталь 38Х2МЮА, но пониженную твердость азотированного слоя.
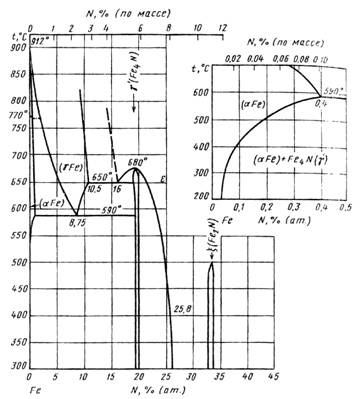
Рисунок 4 – Диаграмма состояния железо-азот
Технологический процесс азотирования предусматривает несколько операций:
1. предварительная термическая обработка заготовки (как правило, улучшение);
2. механическая обработка деталей, а также шлифование, которое придает окончательные размеры детали;
3. защита участков, не подлежащих азотированию, нанесением тонкого слоя олова электролитическим методом или жидкого стекла;
4. азотирование;
5. окончательное шлифование или доводка изделия.
Ликвация – неоднородность химического состава сплавов, возникающая при кристаллизации.
Ликвация обусловлена тем, что сплавы, в отличие от чистых металлов, кристаллизуются не при одной температуре, а в интервале температур.При этом состав кристаллов, образующихся в начале затвердевания, может существенно отличаться от состава последних капель
кристаллизующегося маточного раствора. Чем шире температурный интервал кристаллизации сплава, тем сильнее развивается ликвация, причем наибольшую склонность к ней проявляют те компоненты сплава, которые наиболее сильно влияют на ширину интервала кристаллизации (для стали – сера, кислород, фосфор, углерод). Ликвация оказывает, как правило, вредное влияние на качество металла.
Дендритная ликвация проявляется в микрообъемах сплава, близких к размеру зерен.
Дендритная ликвация может быть ослаблена продолжительным нагревом затвердевшего сплава при температурах, обеспечивающих достаточную скорость диффузии (несколько ниже солидуса). После такого нагрева, называемого диффузионным отжигом или гомогенизацией, дендритная структура литого сплава уже не выявляется и сплав состоит из однородных кристаллов твердого раствора.
Диффузионный отжиг – это термическая обработка, при которой главным процессом является устранение последствий дендритной ликвации.
Слитки из углеродистых сталей обычно не подвергают диффузионному отжигу, так как в них при нагреве под горячую обработку давлением из-за быстрой диффузии углерода в аустените дендритная ликвация успевает исчезнуть. Диффузионному отжигу подвергают слитки легированной стали с целью уменьшения дендритной или внутрикристаллитной ликвации, которая повышает склонность стали, обрабатываемой давлением, к хрупкому излому, к анизотропии свойств и возникновению таких дефектов, как шиферность (слоистый излом) и флокены (тонкие; внутренние трещины, наблюдаемые в изломе в виде белых овальных пятен).
Дендритная ликвация понижает пластичность и вязкость легированной стали. Поэтому слитки и крупные отливки нередко подвергают гомогенизирующему или диффузионному отжигу. Нагрев при диффузионном отжиге должен быть до высоких температур 1100-1200°С, так как только в этом случае более полно протекают диффузионные процессы, необходимые для выравнивания в отдельных объемах состава стали. Диффузия наиболее интенсивно протекает в начале выдержки, заметно снижаясь с течением времени. Поэтому во избежание образования большого количества окалины, уменьшения расхода топлива и увеличения производительности печей выдержка должна быть минимальной, обычно 15-20 ч. После выдержки садку охлаждают до 800-820°С в печи, а далее на воздухе.
Во многих случаях для уменьшения дендритной ликвации не проводят специального диффузионного отжига, а выполняют более высокий и длительный нагрев для горячей деформации. В результате диффузионного отжига получается крупное зерно. Этот недостаток устраняется при последующей обработке слитка давлением или в процессе последующей термической обработке.
Какими стандартными характеристиками механических свойств описывается пластичность металлов и сплавов? Как они определяются?
Пластичность – свойство твердых тел необратимо деформироваться под действием механических нагрузок.
Отсутствие или небольшое значение пластичности называется хрупкостью.
Характеристики пластичности определяют при статических испытаниях. Статическими называют испытания, при которых прилагаемая нагрузка возрастает медленно и плавно. Чаще применяют испытания на растяжение, позволяющие по результатам одного опыта установить нескольких важных механических характеристик металла или сплава. Для испытания на растяжение используют стандартные образцы (ГОСТ 1497-84). Машины для испытания снабжены прибором, записывающим диаграмму растяжения (рисунок 1).
Относительное удлинение характеризует пластичность материала.
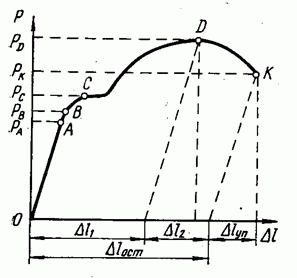
Рисунок 1 – Диаграмма растяжения образца из низкоуглеродистой стали
Относительное удлинение δ представляет собой отношение приращения длины образца после его разрыва к первоначальной расчетной длине l0 и выражается в процентах:
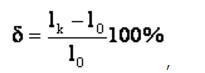
где lк – длина образца после разрыва
Под относительным сужением понимают отношение уменьшения поперечного сечения разорванного образца к первоначальной площади поперечного сечения, выраженное в процентах:
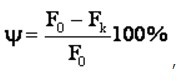
где Fк – площадь поперечного сечения в месте разрыва.
Вычертите диаграмму состояния железо-карбид железа, укажите структурные составляющие во всех областях диаграммы, опишите превращения и постройте кривую охлаждения (с применением правила фаз) для сплава, содержащего 1,2%С. Какова структура этого сплава при комнатной температуре и как такой сплав называется?
Первичная кристаллизация сплавов системы железо-углерод начинается по достижении температур, соответствующих линии ABCD (линии ликвидус), и заканчивается при температурах, образующих линию AHJECF (линию солидус).
При кристаллизации сплавов по линии АВ из жидкого раствора выделяются кристаллы твердого раствора углерода в α-железе (δ-раствор). Процесс кристаллизации сплавов с содержанием углерода до 0,1% заканчивается по линии АН с образованием α (δ)-твердого раствора. На линии HJB протекает перитектическое превращение, в результате которого образуется твердый раствор углерода в γ-железе, т. е. аустенит. Процесс первичной кристаллизации сталей заканчивается по линии AHJE.
При температурах, соответствующих линии ВС, из жидкого раствора кристаллизуется аустенит. В сплавах, содержащих от 4,3% до 6,67% углерода, при температурах, соответствующих линии CD, начинают выделяться кристаллы цементита первичного. Цементит, кристаллизующийся из жидкой фазы, называется первичным. B точке С при температуре 1147°С и концентрации углерода в жидком растворе 4,3% образуется эвтектика, которая называется ледебуритом. Эвтектическое превращение с образованием ледебурита можно записать формулой ЖР4,3Л[А2,14+Ц6,67]. Процесс первичной кристаллизации чугунов заканчивается по линии ECF образованием ледебурита.
Таким образом, структура чугунов ниже 1147°С будет: доэвтектических – аустенит + ледебурит, эвтектических – ледебурит и заэвтектических – цементит (первичный) + ледебурит.
Превращения, происходящие в твердом состоянии, называются вторичной кристаллизацией. Они связаны с переходом при охлаждении γ-железа в α-железо и распадом аустенита.
Линия GS соответствует температурам начала превращения аустенита в феррит. Ниже линии GS сплавы состоят из феррита и аустенита.
Линия ЕS показывает температуры начала выделения цементита из аустенита вследствие уменьшения растворимости углерода в аустените с понижением температуры. Цементит, выделяющийся из аустенита, называется вторичным цементитом.
В точке S при температуре 727°С и концентрации углерода в аустените 0,8% образуется эвтектоидная смесь состоящая из феррита и цементита, которая называется перлитом. Перлит получается в результате одновременного выпадения из аустенита частиц феррита и цементита. Процесс превращения аустенита в перлит можно записать формулой А0,8П[Ф0,03+Ц6,67].
Линия PQ показывает на уменьшение растворимости углерода в феррите при охлаждении и выделении цементита, который называется третичным цементитом.
Следовательно, сплавы, содержащие менее 0,008% углерода (точкаQ), являются однофазными и имеют структуру чистого феррита, а сплавы, содержащие углерод от 0,008 до 0,03% – структуру феррит + цементит третичный и называются техническим железом.
Доэвтектоидные стали при температуре ниже 727ºС имеют структуру феррит + перлит и заэвтектоидные – перлит + цементит вторичный в виде сетки по границам зерен.
В доэвтектических чугунах в интервале температур 1147-727ºС при охлаждении из аустенита выделяется цементит вторичный, вследствие уменьшения растворимости углерода (линия ES). По достижении температуры 727ºС (линия PSK) аустенит, обедненный углеродом до 0,8% (точка S), превращаясь в перлит. Таким образом, после окончательного охлаждения структура доэвтектических чугунов состоит из перлита, цементита вторичного и ледебурита превращенного (перлит + цементит).
Структура эвтектических чугунов при температурах ниже 727ºС состоит из ледебурита превращенного. Заэвтектический чугун при температурах ниже 727ºС состоит из ледебурита превращенного и цементита первичного.
Правило фаз устанавливает зависимость между числом степеней свободы, числом компонентов и числом фаз и выражается уравнением:
C = K + 1 – Ф,
где С – число степеней свободы системы;
К – число компонентов, образующих систему;
1 – число внешних факторов (внешним фактором считаем только температуру, так как давление за исключением очень высокого мало влияет на фазовое равновесие сплавов в твердом и жидком состояниях);
Ф – число фаз, находящихся в равновесии.
Сплав железа с углеродом, содержащий 1,2%С, называется заэвтектоидной сталью. Его структура при комнатной температуре цементит + перлит.
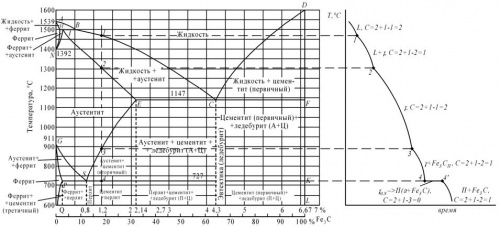
а) б)
Рисунок 2: а — диаграмма железо-цементит, б — кривая охлаждения для сплава, содержащего 1,2% углерода
Как можно устранить крупнозернистую структуру в кованой стали 30? Используя диаграмму состояния железо-цементит, обоснуйте выбор режима термической обработки для исправления структуры. Опишите структурные превращения и характер изменения свойств.
Крупнозернистую структуру в кованой стали 30 можно устранить отжигом при температуре 850-870°С (рисунок 3).
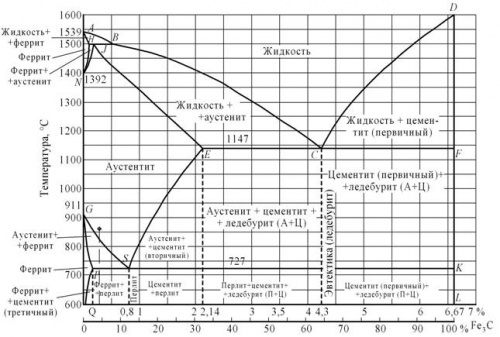
Рисунок 3 – Диаграмма состояния железо-углерод
После отжига в стали 30 получается структура феррит + перлит. Сталь имеет низкую твердость (НВ не более 1870 МПа) и прочность при высокой пластичности. При фазовой перекристаллизации измельчается зерно. Понижая прочность и твердость, отжиг облегчает обработку, резание среднеуглеродистой стали. Измельчая зерно, снимая внутренние напряжения и уменьшая структурную неоднородность, отжиг способствует повышению пластичности и вязкости по сравнению со свойствами, полученными после ковки. При нагреве до температуры выше точки Ас3 (820°С) на 30-50°С образуется аустенит, характеризующийся мелким зерном, поэтому при охлаждении возникает мелкозернистая структура, обеспечивающая высокую вязкость и пластичность и возможность достижения высоких свойств после окончательной термической обработки. Чрезмерное повышение температуры нагрева выше точки Ас3 вызывает рост зерна аустенита, что ухудшает свойства стали.
Укажите температуры, при которых производится процесс прочностного азотирования. Объясните, почему азотирование не производится при температурах ниже 500 и выше 700°С (используя диаграмму состояния железо-азот). Назовите марки сталей, применяемых для азотирования, и опишите полный цикл их термической и химико-термической обработки.
Азотированием называется химико-термическая обработка, заключающаяся в диффузионном насыщении поверхностного слоя стали азотом.
Упрочнение при азотировании достигается за счет фаз, образующихся из твердых растворов на базе нитридов. Азотирования при температурах ниже 500°С не производится, т.к. этих температур не достаточно для образования упрочняющих фаз (ε, γ΄, γ, α) (рисунок 4).
Азотирование является окончательной термической обработкой. Ему обычно предшествует термическая обработка, заключающаяся в закалке и высоком отпуске стали, для получения повышенной прочности и вязкости в сердцевине изделия. Отпуск проводят при высокой температуре 600-675°С, превышающей максимальную температуру последующего азотирования и обеспечивающей получение твердости, при которой сталь можно обрабатывать резанием. Структура стали после этого отпуска – сорбит отпуска. Поэтому для сохранения полученных в результате улучшения свойств не следует назначать температуру азотирования выше температуры высокого отпуска.
Обычно азотированию подвергают конструкционные стали, содержащие алюминий: 38Х2МЮА, 38Х2Ю и т.д. и не содержащие алюминия: 40Х, 40ХФ, 18ХГТ, 30ХГТ, 40ХНМА, 20Х3ВА, 30Х3МФ, 18Х2Н4ВА и т.д. Стали без алюминия технологичнее, многие из них имеют более высокие механические свойства, чем сталь 38Х2МЮА, но пониженную твердость азотированного слоя.
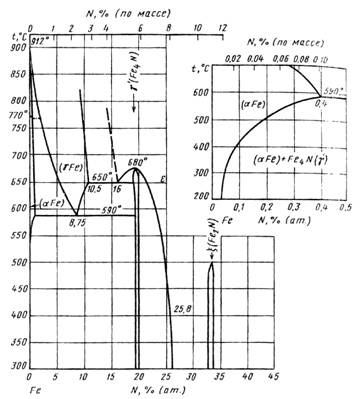
Рисунок 4 – Диаграмма состояния железо-азот
Технологический процесс азотирования предусматривает несколько операций:
1. предварительная термическая обработка заготовки (как правило, улучшение);
2. механическая обработка деталей, а также шлифование, которое придает окончательные размеры детали;
3. защита участков, не подлежащих азотированию, нанесением тонкого слоя олова электролитическим методом или жидкого стекла;
4. азотирование;
5. окончательное шлифование или доводка изделия.
0 комментариев