Контрольная работа 1 Вариант 28
Что такое твердый раствор? Виды твердых растворов, примеры.
Твердыми растворами называют фазы, в которых один из компонентов сплава сохраняет свою кристаллическую решетку, а атомы других (или другого) компонентов располагаются в решетке первого компонента (растворителя), изменяя ее размеры (периоды).
Таким образом, твердый раствор, состоящий из двух или нескольких компонентов, имеет один тип решетки и представляет собой одну фазу.
Существуют твердые растворы внедрения и твердые растворы замещения.
При образовании твердых растворов внедрения атомы растворенного компонента B размещаются между атомами растворителя A в его кристаллической решетке. При образовании твердых растворов замещения атомы растворенного компонента B замещают часть атомов растворителя (компонент A) в его кристаллической решетке.
Твердые растворы: а – замещения, б – внедрения
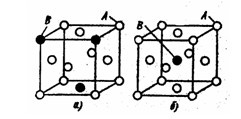
Рисунок 1 – Твердые растворы: а – замещения, б – внедрения
Поскольку размеры растворенных атомов отличаются от размеров атомов растворителя, то образование твердого раствора сопровождается искажением кристаллической решетки растворителя.
Искажения кристаллической решетки в твердых растворах замещения:
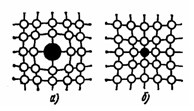
Рисунок 2 – Искажения кристаллической решетки в твердых растворах замещения:
а – атом растворенного компонента больше атома растворителя
б – атом растворенного компонента меньше атома растворителя
Твердые растворы замещения могут быть с ограниченной и неограниченной растворимостью. В твердых растворах с ограниченной растворимостью концентрация растворенного компонента возможна до определенных пределов.
В твердых растворах с неограниченной растворимостью возможна любая концентрация растворенного компонента (от 0 до 100 %). Твердые растворы с неограниченной растворимостью образуются при соблюдении следующих условий: 1) у компонентов должны быть однотипные кристаллические решетки; 2) различие в атомных радиусах компонентов не должно превышать для сплавов на основе железа 9%, а для сплавов на основе меди 15%; 3) компоненты должны обладать близостью физико-химических свойств. Однако соблюдение этих свойств не всегда приводит к образованию твердых растворов замещения с неограниченной растворимостью. На практике, как правило, образуются твердые растворы с ограниченной растворимостью.
Твердые растворы внедрения могут быть только с ограниченной концентрации, поскольку число пор в решетке ограничено, а атомы основного компонента сохраняются в узлах решетки.
Твердые растворы замещения с неограниченной растворимостью на основе компонентов: Ag и Au, Ni и Cu, Mo и W, V и Ti, и т.д.
Твердые растворы замещения с ограниченной растворимостью на основе компонентов: Al и Cu, Cu и Zn, и т.д.
Твердые растворы внедрения: при растворении в металлах неметаллических элементов, как углерод, бор, азот и кислород. Например: Fe и С.
Под действием каких напряжений происходит пластическая деформация, и как при этом изменяются структура и свойства металла?
Деформацией называется изменение формы и размеров тела под действием напряжений.
Напряжение – сила, действующая на единицу площади сечения детали.
Напряжения и вызываемые ими деформации могут возникать при действии на тело внешних сил растяжения, сжатия и т.д., а также в результате фазовых (структурных) превращений, усадки и других физико-химических процессов, протекающих в металлах, и связанных с изменением объема.
Металл, находящийся в напряженном состоянии, при любом виде нагружения всегда испытывает напряжения нормальные и касательные.
Схема возникновения нормальных и касательных напряжений в металле при его нагружения
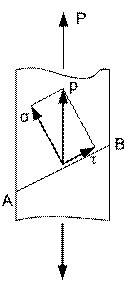
Рисунок 3 – Схема возникновения нормальных и касательных напряжений в металле при его нагружения
Рост нормальных и касательных напряжений приводит к разным последствиям. Рост нормальных напряжений приводит к хрупкому разрушению. Пластическую деформацию вызывают касательные напряжения.
При пластическом деформировании одна часть кристалла перемещается по отношению к другой под действием касательных напряжений. При снятии нагрузок сдвиг остается, т.е. происходит пластическая деформация.
С увеличением степени деформации характеристики пластичности (относительное удлинение, относительное сужение) и вязкости (ударная вязкость) уменьшаются, а прочностные характеристики (предел упругости, предел текучести, предел прочности) и твердость увеличиваются. Также повышается электросопротивление, снижаются сопротивление коррозии, теплопроводность, магнитная проницаемость.
Совокупность явлений, связанных с изменением механических, физических и других свойств металлов в процессе пластической деформации называют деформационным упрочнением или наклепом.
Влияние холодной пластической деформации на механические свойства металла

Рисунок 4 – Влияние холодной пластической деформации на механические свойства металла
Упрочнение при наклепе объясняется возрастанием на несколько порядков плотности дислокаций:

Их свободное перемещение затрудняется взаимным влиянием, также торможением дислокаций в связи с измельчением блоков и зерен, искажениями решетки металлов, возникновением напряжений.
Вычертите диаграмму состояния железо – карбид железа, укажите структурные составляющие во всех областях диаграммы, опишите превращения и постройте кривую охлаждения (с применением правила фаз) для сплава, содержащего 0,8% С. Какова структура этого сплава при комнатной температуре и как такой сплав называется?
Первичная кристаллизация сплавов системы железо-углерод начинается по достижении температур, соответствующих линии ABCD (линии ликвидус), и заканчивается при температурах, образующих линию AHJECF (линию солидус).
При кристаллизации сплавов по линии АВ из жидкого раствора выделяются кристаллы твердого раствора углерода в α-железе (δ-раствор). Процесс кристаллизации сплавов с содержанием углерода до 0,1 % заканчивается по линии АН с образованием α (δ)-твердого раствора. На линии HJB протекает перитектическое превращение, в результате которого образуется твердый раствор углерода в γ-железе, т. е. аустенит. Процесс первичной кристаллизации сталей заканчивается по линии AHJE.
При температурах, соответствующих линии ВС, из жидкого раствора кристаллизуется аустенит. В сплавах, содержащих от 4,3% до 6,67% углерода, при температурах, соответствующих линии CD, начинают выделяться кристаллы цементита первичного. Цементит, кристаллизующийся из жидкой фазы, называется первичным. B точке С при температуре 1147°С и концентрации углерода в жидком растворе 4,3% образуется эвтектика, которая называется ледебуритом. Эвтектическое превращение с образованием ледебурита можно записать формулой ЖР4,3Л[А2,14+Ц6,67]. Процесс первичной кристаллизации чугунов заканчивается по линии ECF образованием ледебурита.
Таким образом, структура чугунов ниже 1147°С будет: доэвтектических – аустенит + ледебурит, эвтектических – ледебурит и заэвтектических – цементит (первичный) + ледебурит.
Превращения, происходящие в твердом состоянии, называются вторичной кристаллизацией. Они связаны с переходом при охлаждении γ-железа в α-железо и распадом аустенита.
Линия GS соответствует температурам начала превращения аустенита в феррит. Ниже линии GS сплавы состоят из феррита и аустенита.
Линия ЕS показывает температуры начала выделения цементита из аустенита вследствие уменьшения растворимости углерода в аустените с понижением температуры. Цементит, выделяющийся из аустенита, называется вторичным цементитом.
В точке S при температуре 727°С и концентрации углерода в аустените 0,8% образуется эвтектоидная смесь состоящая из феррита и цементита, которая называется перлитом. Перлит получается в результате одновременного выпадения из аустенита частиц феррита и цементита. Процесс превращения аустенита в перлит можно записать формулой А0,8П[Ф0,03+Ц6,67].
Линия PQ показывает на уменьшение растворимости углерода в феррите при охлаждении и выделении цементита, который называется третичным цементитом.
Следовательно, сплавы, содержащие менее 0,008% углерода (точка Q), являются однофазными и имеют структуру чистого феррита, а сплавы, содержащие углерод от 0,008 до 0,03% – структуру феррит + цементит третичный и называются техническим железом.
Доэвтектоидные стали при температуре ниже 727ºС имеют структуру феррит + перлит и заэвтектоидные – перлит + цементит вторичный в виде сетки по границам зерен.
В доэвтектических чугунах в интервале температур 1147–727ºС при охлаждении из аустенита выделяется цементит вторичный, вследствие уменьшения растворимости углерода(линия ES). По достижении температуры 727ºС (линия PSK) аустенит, обедненный углеродом до 0,8% (точка S), превращаясь в перлит. Таким образом, после окончательного охлаждения структура доэвтектических чугунов состоит из перлита, цементита вторичного и ледебурита превращенного (перлит + цементит).
Структура эвтектических чугунов при температурах ниже 727ºС состоит из ледебурита превращенного. Заэвтектический чугун при температурах ниже 727ºС состоит из ледебурита превращенного и цементита первичного.
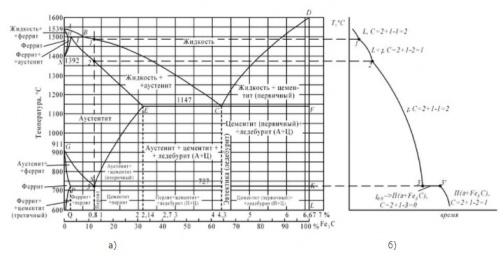
Рисунок 5: а-диаграмма железо-цементит, б-кривая охлаждения для сплава, содержащего 0,8% углерода
Правило фаз устанавливает зависимость между числом степеней свободы, числом компонентов и числом фаз и выражается уравнением:
C = K + 1 – Ф,
где С – число степеней свободы системы;
К – число компонентов, образующих систему;
1 – число внешних факторов (внешним фактором считаем только температуру, так как давление за исключением очень высокого мало влияет на фазовое равновесие сплавов в твердом и жидком состояниях);
Ф – число фаз, находящихся в равновесии.
Сплав железа с углеродом, содержащий 0,8% С, называется эвтектоидной сталью. Его структура при комнатной температуре – Перлит.
Используя диаграмму состояния железо-цементит, определите температуру полного и неполного отжига и нормализации для стали 15. Охарактеризуйте эти режимы термической обработки и опишите микроструктуру и свойства стали.
Критические точки Ас1 и Ас3 для стали 15:
Ас1 = 735°С; Ас3 = 860°С.
Полный отжиг заключается в нагреве доэвтектоидной стали на 30-50°С выше температуры, соответствующей точке Ас3, выдержке при этой температуре для полного прогрева и завершения фазовых превращений в объеме металла и последующем медленном охлаждении. Температура полного отжига стали 15 составляет 890-910°С. После отжига сталь имеет низкую твердость и прочность при высокой пластичности. При фазовой перекристаллизации измельчается зерно и устраняется видманштеттова структура и строчечность, вызванная ликвацией, и другие неблагоприятные структуры стали. Структура после полного отжига: перлит и феррит.
Неполный отжиг отличается от полного тем, что сталь нагревают до более низкой температуры (немного выше точки Ас1). При этом происходит частичная перекристаллизация перлитной составляющей. Неполному отжигу подвергают доэвтектоидные стали с целью снятия внутренних напряжений и улучшения обрабатываемости резанием в том случае, если предварительная горячая обработка не привела к образованию крупного зерна. Температура неполного отжига стали 15 составляет 740-760°С. После отжига сталь имеет низкую твердость и прочность при высокой пластичности. Структура после полного отжига: перлит и феррит.
Нормализацией называется доэвтектоидной стали нагрев до температуры выше Аc3 на 40-50°С с последующим охлаждением на воздухе. При нормализации происходит перекристаллизация стали, устраняющая крупнозернистую структуру, полученную при литье или ковке. В результате охлаждения на воздухе распад аустенита на ферритно-цементитную смесь происходит при более низких температурах, а, следовательно, повышается дисперсность смеси. Доэвтектоидные стали подвергают нормализации вместо отжига. В результате твердость немного возрастает, но улучшается качество поверхности при резании. Температура нормализации для стали 15 составляет 900-910°С. Структура после полного отжига: перлит и феррит.
В чем отличие обычной закалки от ступенчатой и изотермической? Каковы преимущества и недостатки каждого из этих видов закалки?
Оптимальный способ закалки выбирают в зависимости от состава стали, формы и размеров детали. Чем больше углерода в стали, тем больше объемные изменения, тем при более низкой температуре происходит превращение аустенита в мартенсит, тем больше вероятность образования трещин, тем тщательнее нужно выбирать способ охлаждения.
Чем сложнее деталь, тем больше различие в сечениях детали, больше величина внутренних напряжений, возникающих при охлаждении. Существуют следующие способы закалки:
Схема различных способов закалки
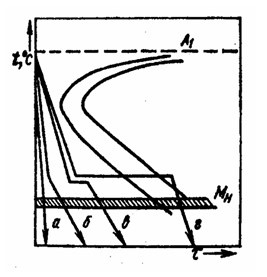
Рисунок 6 – Схема различных способов закалки
а – в одном охладителе, б – в двух средах, в – ступенчатая, г – изотермическая
Закалка в одном охладителе (а) получила наиболее широкое применение. Нагретую до определенной температуры деталь погружают в закалочную среду, где она остается до полного охлаждения. Этот способ применяют для деталей простой формы из углеродистых и легированных сталей. Детали из углеродистых сталей диаметром более 5 мм охлаждают в воде, а менее – в масле. Легированные стали охлаждают в масле. Такой способ наиболее распространен вследствие его простоты и дешевизны. Для обычной закалки характерно большое различие в скоростях охлаждения поверхности и сердцевины детали, которое является основной причиной образования термических напряжений и закалочных трещин.
При ступенчатой закалке (в) нагретая деталь охлаждается в закалочной среде, имеющей температуру несколько выше точки Мн (обычно 230-250 °С), и выдерживается в ней до выравнивания температуры по всему сечению. Выдержка не должна быть очень длительной, чтобы не вызвать превращения аустенита в бейнит. Затем следует окончательное охлаждение на воздухе, во время которого происходит превращение аустенита в мартенсит. При ступенчатой закалке уменьшаются объемные изменения, коробление и опасность возникновения трещин. Правку изделий, склонных к короблению, осуществляют в период охлаждения на воздухе. Основной недостаток ступенчатой закалки – малая скорость охлаждения в горячей среде. Поэтому применение ступенчатой закалки к углеродистым сталям ограничено изделиями небольшого сечения (до 8-10 мм толщиной). Изделие большого сечения охлаждается в горячей среде медленно, и аустенит успевает претерпеть эвтектоидный распад. Изделия из легированных сталей, у которых меньше критическая скорость охлаждения, проще подвергать ступенчатой закалке. Так, например, ступенчатой закалкой широко пользуются при обработке инструментов и деталей машин из хромистой стали.
Изотермическая закалка (г) выполняется так же, как и ступенчатая, но выдержка в закалочной среде более продолжительна. При такой выдержке происходит изотермический распад аустенита с образованием бейнита. Продолжительность выдержки в закалочной среде зависит от устойчивости переохлажденного аустенита при температурах выше Мн и определяется по диаграмме изотермического превращения аустенита для каждой марки стали. В основном изотермической закалке подвергают легированные стали. В качестве охлаждающих сред при ступенчатой и изотермической закалке применяют расплавленные соли или расплавленные щелочи. Добавка 5-10% воды в расплав щелочей и солей увеличивает скорость охлаждения. Резкое уменьшение закалочных напряжений и коробления – важное преимущество изотермической закалки. Кроме того, у изотермической закалки есть и другое преимущество. При бейнитном превращении в некоторых легированных сталях сохраняется большое количество остаточного аустенита, который не превращается в мартенсит при охлаждении после изотермической выдержки. Изотермическая закалка таких сталей обеспечивает высокую ударную вязкость, резко уменьшает чувствительность к надрезу по сравнению с закаленной на мартенсит и отпущенной сталью. Следовательно, изотермическая закалка позволяет повысить конструктивную прочность стали.
Твердыми растворами называют фазы, в которых один из компонентов сплава сохраняет свою кристаллическую решетку, а атомы других (или другого) компонентов располагаются в решетке первого компонента (растворителя), изменяя ее размеры (периоды).
Таким образом, твердый раствор, состоящий из двух или нескольких компонентов, имеет один тип решетки и представляет собой одну фазу.
Существуют твердые растворы внедрения и твердые растворы замещения.
При образовании твердых растворов внедрения атомы растворенного компонента B размещаются между атомами растворителя A в его кристаллической решетке. При образовании твердых растворов замещения атомы растворенного компонента B замещают часть атомов растворителя (компонент A) в его кристаллической решетке.
Твердые растворы: а – замещения, б – внедрения
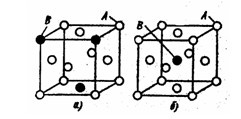
Рисунок 1 – Твердые растворы: а – замещения, б – внедрения
Поскольку размеры растворенных атомов отличаются от размеров атомов растворителя, то образование твердого раствора сопровождается искажением кристаллической решетки растворителя.
Искажения кристаллической решетки в твердых растворах замещения:
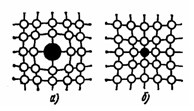
Рисунок 2 – Искажения кристаллической решетки в твердых растворах замещения:
а – атом растворенного компонента больше атома растворителя
б – атом растворенного компонента меньше атома растворителя
Твердые растворы замещения могут быть с ограниченной и неограниченной растворимостью. В твердых растворах с ограниченной растворимостью концентрация растворенного компонента возможна до определенных пределов.
В твердых растворах с неограниченной растворимостью возможна любая концентрация растворенного компонента (от 0 до 100 %). Твердые растворы с неограниченной растворимостью образуются при соблюдении следующих условий: 1) у компонентов должны быть однотипные кристаллические решетки; 2) различие в атомных радиусах компонентов не должно превышать для сплавов на основе железа 9%, а для сплавов на основе меди 15%; 3) компоненты должны обладать близостью физико-химических свойств. Однако соблюдение этих свойств не всегда приводит к образованию твердых растворов замещения с неограниченной растворимостью. На практике, как правило, образуются твердые растворы с ограниченной растворимостью.
Твердые растворы внедрения могут быть только с ограниченной концентрации, поскольку число пор в решетке ограничено, а атомы основного компонента сохраняются в узлах решетки.
Твердые растворы замещения с неограниченной растворимостью на основе компонентов: Ag и Au, Ni и Cu, Mo и W, V и Ti, и т.д.
Твердые растворы замещения с ограниченной растворимостью на основе компонентов: Al и Cu, Cu и Zn, и т.д.
Твердые растворы внедрения: при растворении в металлах неметаллических элементов, как углерод, бор, азот и кислород. Например: Fe и С.
Под действием каких напряжений происходит пластическая деформация, и как при этом изменяются структура и свойства металла?
Деформацией называется изменение формы и размеров тела под действием напряжений.
Напряжение – сила, действующая на единицу площади сечения детали.
Напряжения и вызываемые ими деформации могут возникать при действии на тело внешних сил растяжения, сжатия и т.д., а также в результате фазовых (структурных) превращений, усадки и других физико-химических процессов, протекающих в металлах, и связанных с изменением объема.
Металл, находящийся в напряженном состоянии, при любом виде нагружения всегда испытывает напряжения нормальные и касательные.
Схема возникновения нормальных и касательных напряжений в металле при его нагружения
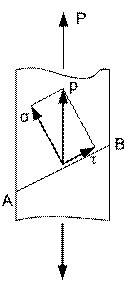
Рисунок 3 – Схема возникновения нормальных и касательных напряжений в металле при его нагружения
Рост нормальных и касательных напряжений приводит к разным последствиям. Рост нормальных напряжений приводит к хрупкому разрушению. Пластическую деформацию вызывают касательные напряжения.
При пластическом деформировании одна часть кристалла перемещается по отношению к другой под действием касательных напряжений. При снятии нагрузок сдвиг остается, т.е. происходит пластическая деформация.
С увеличением степени деформации характеристики пластичности (относительное удлинение, относительное сужение) и вязкости (ударная вязкость) уменьшаются, а прочностные характеристики (предел упругости, предел текучести, предел прочности) и твердость увеличиваются. Также повышается электросопротивление, снижаются сопротивление коррозии, теплопроводность, магнитная проницаемость.
Совокупность явлений, связанных с изменением механических, физических и других свойств металлов в процессе пластической деформации называют деформационным упрочнением или наклепом.
Влияние холодной пластической деформации на механические свойства металла

Рисунок 4 – Влияние холодной пластической деформации на механические свойства металла
Упрочнение при наклепе объясняется возрастанием на несколько порядков плотности дислокаций:

Их свободное перемещение затрудняется взаимным влиянием, также торможением дислокаций в связи с измельчением блоков и зерен, искажениями решетки металлов, возникновением напряжений.
Вычертите диаграмму состояния железо – карбид железа, укажите структурные составляющие во всех областях диаграммы, опишите превращения и постройте кривую охлаждения (с применением правила фаз) для сплава, содержащего 0,8% С. Какова структура этого сплава при комнатной температуре и как такой сплав называется?
Первичная кристаллизация сплавов системы железо-углерод начинается по достижении температур, соответствующих линии ABCD (линии ликвидус), и заканчивается при температурах, образующих линию AHJECF (линию солидус).
При кристаллизации сплавов по линии АВ из жидкого раствора выделяются кристаллы твердого раствора углерода в α-железе (δ-раствор). Процесс кристаллизации сплавов с содержанием углерода до 0,1 % заканчивается по линии АН с образованием α (δ)-твердого раствора. На линии HJB протекает перитектическое превращение, в результате которого образуется твердый раствор углерода в γ-железе, т. е. аустенит. Процесс первичной кристаллизации сталей заканчивается по линии AHJE.
При температурах, соответствующих линии ВС, из жидкого раствора кристаллизуется аустенит. В сплавах, содержащих от 4,3% до 6,67% углерода, при температурах, соответствующих линии CD, начинают выделяться кристаллы цементита первичного. Цементит, кристаллизующийся из жидкой фазы, называется первичным. B точке С при температуре 1147°С и концентрации углерода в жидком растворе 4,3% образуется эвтектика, которая называется ледебуритом. Эвтектическое превращение с образованием ледебурита можно записать формулой ЖР4,3Л[А2,14+Ц6,67]. Процесс первичной кристаллизации чугунов заканчивается по линии ECF образованием ледебурита.
Таким образом, структура чугунов ниже 1147°С будет: доэвтектических – аустенит + ледебурит, эвтектических – ледебурит и заэвтектических – цементит (первичный) + ледебурит.
Превращения, происходящие в твердом состоянии, называются вторичной кристаллизацией. Они связаны с переходом при охлаждении γ-железа в α-железо и распадом аустенита.
Линия GS соответствует температурам начала превращения аустенита в феррит. Ниже линии GS сплавы состоят из феррита и аустенита.
Линия ЕS показывает температуры начала выделения цементита из аустенита вследствие уменьшения растворимости углерода в аустените с понижением температуры. Цементит, выделяющийся из аустенита, называется вторичным цементитом.
В точке S при температуре 727°С и концентрации углерода в аустените 0,8% образуется эвтектоидная смесь состоящая из феррита и цементита, которая называется перлитом. Перлит получается в результате одновременного выпадения из аустенита частиц феррита и цементита. Процесс превращения аустенита в перлит можно записать формулой А0,8П[Ф0,03+Ц6,67].
Линия PQ показывает на уменьшение растворимости углерода в феррите при охлаждении и выделении цементита, который называется третичным цементитом.
Следовательно, сплавы, содержащие менее 0,008% углерода (точка Q), являются однофазными и имеют структуру чистого феррита, а сплавы, содержащие углерод от 0,008 до 0,03% – структуру феррит + цементит третичный и называются техническим железом.
Доэвтектоидные стали при температуре ниже 727ºС имеют структуру феррит + перлит и заэвтектоидные – перлит + цементит вторичный в виде сетки по границам зерен.
В доэвтектических чугунах в интервале температур 1147–727ºС при охлаждении из аустенита выделяется цементит вторичный, вследствие уменьшения растворимости углерода(линия ES). По достижении температуры 727ºС (линия PSK) аустенит, обедненный углеродом до 0,8% (точка S), превращаясь в перлит. Таким образом, после окончательного охлаждения структура доэвтектических чугунов состоит из перлита, цементита вторичного и ледебурита превращенного (перлит + цементит).
Структура эвтектических чугунов при температурах ниже 727ºС состоит из ледебурита превращенного. Заэвтектический чугун при температурах ниже 727ºС состоит из ледебурита превращенного и цементита первичного.
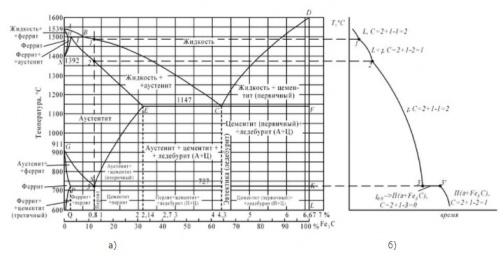
Рисунок 5: а-диаграмма железо-цементит, б-кривая охлаждения для сплава, содержащего 0,8% углерода
Правило фаз устанавливает зависимость между числом степеней свободы, числом компонентов и числом фаз и выражается уравнением:
C = K + 1 – Ф,
где С – число степеней свободы системы;
К – число компонентов, образующих систему;
1 – число внешних факторов (внешним фактором считаем только температуру, так как давление за исключением очень высокого мало влияет на фазовое равновесие сплавов в твердом и жидком состояниях);
Ф – число фаз, находящихся в равновесии.
Сплав железа с углеродом, содержащий 0,8% С, называется эвтектоидной сталью. Его структура при комнатной температуре – Перлит.
Используя диаграмму состояния железо-цементит, определите температуру полного и неполного отжига и нормализации для стали 15. Охарактеризуйте эти режимы термической обработки и опишите микроструктуру и свойства стали.
Критические точки Ас1 и Ас3 для стали 15:
Ас1 = 735°С; Ас3 = 860°С.
Полный отжиг заключается в нагреве доэвтектоидной стали на 30-50°С выше температуры, соответствующей точке Ас3, выдержке при этой температуре для полного прогрева и завершения фазовых превращений в объеме металла и последующем медленном охлаждении. Температура полного отжига стали 15 составляет 890-910°С. После отжига сталь имеет низкую твердость и прочность при высокой пластичности. При фазовой перекристаллизации измельчается зерно и устраняется видманштеттова структура и строчечность, вызванная ликвацией, и другие неблагоприятные структуры стали. Структура после полного отжига: перлит и феррит.
Неполный отжиг отличается от полного тем, что сталь нагревают до более низкой температуры (немного выше точки Ас1). При этом происходит частичная перекристаллизация перлитной составляющей. Неполному отжигу подвергают доэвтектоидные стали с целью снятия внутренних напряжений и улучшения обрабатываемости резанием в том случае, если предварительная горячая обработка не привела к образованию крупного зерна. Температура неполного отжига стали 15 составляет 740-760°С. После отжига сталь имеет низкую твердость и прочность при высокой пластичности. Структура после полного отжига: перлит и феррит.
Нормализацией называется доэвтектоидной стали нагрев до температуры выше Аc3 на 40-50°С с последующим охлаждением на воздухе. При нормализации происходит перекристаллизация стали, устраняющая крупнозернистую структуру, полученную при литье или ковке. В результате охлаждения на воздухе распад аустенита на ферритно-цементитную смесь происходит при более низких температурах, а, следовательно, повышается дисперсность смеси. Доэвтектоидные стали подвергают нормализации вместо отжига. В результате твердость немного возрастает, но улучшается качество поверхности при резании. Температура нормализации для стали 15 составляет 900-910°С. Структура после полного отжига: перлит и феррит.
В чем отличие обычной закалки от ступенчатой и изотермической? Каковы преимущества и недостатки каждого из этих видов закалки?
Оптимальный способ закалки выбирают в зависимости от состава стали, формы и размеров детали. Чем больше углерода в стали, тем больше объемные изменения, тем при более низкой температуре происходит превращение аустенита в мартенсит, тем больше вероятность образования трещин, тем тщательнее нужно выбирать способ охлаждения.
Чем сложнее деталь, тем больше различие в сечениях детали, больше величина внутренних напряжений, возникающих при охлаждении. Существуют следующие способы закалки:
Схема различных способов закалки
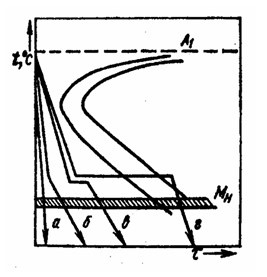
Рисунок 6 – Схема различных способов закалки
а – в одном охладителе, б – в двух средах, в – ступенчатая, г – изотермическая
Закалка в одном охладителе (а) получила наиболее широкое применение. Нагретую до определенной температуры деталь погружают в закалочную среду, где она остается до полного охлаждения. Этот способ применяют для деталей простой формы из углеродистых и легированных сталей. Детали из углеродистых сталей диаметром более 5 мм охлаждают в воде, а менее – в масле. Легированные стали охлаждают в масле. Такой способ наиболее распространен вследствие его простоты и дешевизны. Для обычной закалки характерно большое различие в скоростях охлаждения поверхности и сердцевины детали, которое является основной причиной образования термических напряжений и закалочных трещин.
При ступенчатой закалке (в) нагретая деталь охлаждается в закалочной среде, имеющей температуру несколько выше точки Мн (обычно 230-250 °С), и выдерживается в ней до выравнивания температуры по всему сечению. Выдержка не должна быть очень длительной, чтобы не вызвать превращения аустенита в бейнит. Затем следует окончательное охлаждение на воздухе, во время которого происходит превращение аустенита в мартенсит. При ступенчатой закалке уменьшаются объемные изменения, коробление и опасность возникновения трещин. Правку изделий, склонных к короблению, осуществляют в период охлаждения на воздухе. Основной недостаток ступенчатой закалки – малая скорость охлаждения в горячей среде. Поэтому применение ступенчатой закалки к углеродистым сталям ограничено изделиями небольшого сечения (до 8-10 мм толщиной). Изделие большого сечения охлаждается в горячей среде медленно, и аустенит успевает претерпеть эвтектоидный распад. Изделия из легированных сталей, у которых меньше критическая скорость охлаждения, проще подвергать ступенчатой закалке. Так, например, ступенчатой закалкой широко пользуются при обработке инструментов и деталей машин из хромистой стали.
Изотермическая закалка (г) выполняется так же, как и ступенчатая, но выдержка в закалочной среде более продолжительна. При такой выдержке происходит изотермический распад аустенита с образованием бейнита. Продолжительность выдержки в закалочной среде зависит от устойчивости переохлажденного аустенита при температурах выше Мн и определяется по диаграмме изотермического превращения аустенита для каждой марки стали. В основном изотермической закалке подвергают легированные стали. В качестве охлаждающих сред при ступенчатой и изотермической закалке применяют расплавленные соли или расплавленные щелочи. Добавка 5-10% воды в расплав щелочей и солей увеличивает скорость охлаждения. Резкое уменьшение закалочных напряжений и коробления – важное преимущество изотермической закалки. Кроме того, у изотермической закалки есть и другое преимущество. При бейнитном превращении в некоторых легированных сталях сохраняется большое количество остаточного аустенита, который не превращается в мартенсит при охлаждении после изотермической выдержки. Изотермическая закалка таких сталей обеспечивает высокую ударную вязкость, резко уменьшает чувствительность к надрезу по сравнению с закаленной на мартенсит и отпущенной сталью. Следовательно, изотермическая закалка позволяет повысить конструктивную прочность стали.
0 комментариев