Контрольная работа 1 Вариант 30
Как влияет модифицирование на строение и свойства литого металла? Объясните причину воздействия.
Модифицирование – использование специально вводимых в жидкий металл примесей (модификаторов) для получения мелкого зерна. Эти примеси, практически не изменяя химического состава сплава, вызывают при кристаллизации измельчение зерна и в итоге улучшение механических свойств. Так, например, при модифицировании магниевых сплавов зерно уменьшается с 0,2-0,3 до 0,01-0,02 мм. При литье слитков в фасонных отливках модифицирование чаще проводят введением в расплав добавок, которые образуют тугоплавкие соединения (карбиды, нитриды, оксиды), кристаллизирующиеся в первую очередь. Выделяясь в виде мельчайших частиц, эти соединения служат зародышами образующихся при затвердевании кристаллов (модификаторы I рода). В качестве модификаторов при модифицировании алюминиевых сплавов применяют Ti, V, Zr; стали – Al, V, Ti. Иногда используют растворимые в жидком металле модификаторы (модификаторы II рода), избирательно адсорбирующиеся на кристаллическом зародыше, которые снижают межфазовое поверхностное натяжение и затрудняют рост кристаллитов. Для алюминиевых сплавов в качестве модификаторов второго рода используют Li, Na, K, для стали – редкоземельные элементы.
Для измельчения структуры эвтектики и устранения избыточных кристаллов кремния силумины модифицируют натрием (0,05-0,08%) путем присадки к расплаву смеси солей 67% NaF и 33% NaCl. В присутствии натрия происходит смещение линий диаграммы состояния и заэвтектический (эвтектический) сплав АЛ2 (11-13% Si) становится доэвтектическим. В этом случае в структуре сплава вместо избыточного кремния появляются кристаллы α-твердого раствора. В процессе затвердевания кристаллы кремния обволакиваются пленкой силицида натрия Na2Si, которая затрудняет их рост. Такие изменения структуры улучшают механические свойства.
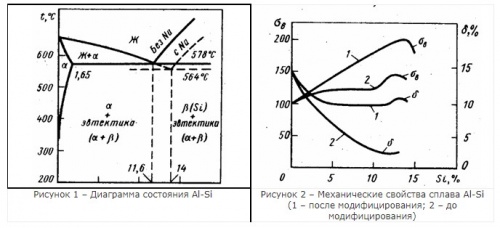
Что такое предел усталости? Опишите методику определения этой характеристики свойств металла.
Предел усталости – механическая характеристика материалов: наибольшее напряжение цикла, которое материал может выдержать повторно N раз без разрушения, где N – заданное техническими условиями большое число (напр., 106, 107, 108).
Испытание на усталость (ГОСТ 25502—79) проводят для определения предела выносливости, под которым понимают наибольшее значение максимального напряжения цикла, при действии которого не происходит усталостного разрушения образца после произвольно большого или заданного числа циклов нагружения. Цикл напряжения — это совокупность переменных значений напряжений за один период их изменения. За максимальное σmax или минимальное σmin напряжение цикла принимают наибольшее или наименьшее по алгебраической величине напряжение. Цикл характеризуется коэффициентом асимметрии: R = σmax/ σmin. Если R = -1, то цикл называют симметричным, если σmin и σmax не равны по величине, то цикл асимметричный.
Предел выносливости обозначается σR (R — коэффициент асимметрии цикла), а при симметричном цикле σ-1. Предел выносливости определяют на вращающемся образце (гладком или с надрезом) с приложением изгибающей нагрузки по симметричному циклу. Для определения используют не менее десяти образцов, чаще диаметром 7,5 мм. Каждый образец испытывают только на одном уровне напряжений до разрушения или до базового числа циклов. По результатам испытания отдельных образцов строят кривые усталости в полулогарифмических или логарифмических координатах σmax – 1/N.
Вычертите диаграмму состояния железо – углерод, укажите структурные составляющие во всех областях диаграммы, опишите превращения и постройте кривую охлаждения (с применением правила фаз) для сплава, содержащего 4,6% С. Какова структура этого сплава при комнатной температуре и как такой сплав называется?
Первичная кристаллизация сплавов системы железо-углерод начинается по достижении температур, соответствующих линии ABCD (линии ликвидус), и заканчивается при температурах, образующих линию AHJECF (линию солидус).
При кристаллизации сплавов по линии АВ из жидкого раствора выделяются кристаллы твердого раствора углерода в α-железе (δ-раствор). Процесс кристаллизации сплавов с содержанием углерода до 0,1 % заканчивается по линии АН с образованием α (δ)-твердого раствора. На линии HJB протекает перитектическое превращение, в результате которого образуется твердый раствор углерода в γ-железе, т. е. аустенит. Процесс первичной кристаллизации сталей заканчивается по линии AHJE.
При температурах, соответствующих линии ВС, из жидкого раствора кристаллизуется аустенит. В сплавах, содержащих от 4,3% до 6,67% углерода, при температурах, соответствующих линии CD, начинают выделяться кристаллы цементита первичного. Цементит, кристаллизующийся из жидкой фазы, называется первичным. B точке С при температуре 1147°С и концентрации углерода в жидком растворе 4,3% образуется эвтектика, которая называется ледебуритом. Эвтектическое превращение с образованием ледебурита можно записать формулой ЖР4,3Л[А2,14+Ц6,67]. Процесс первичной кристаллизации чугунов заканчивается по линии ECF образованием ледебурита.
Таким образом, структура чугунов ниже 1147°С будет: доэвтектических – аустенит + ледебурит, эвтектических – ледебурит и заэвтектических – цементит (первичный) + ледебурит.
Превращения, происходящие в твердом состоянии, называются вторичной кристаллизацией. Они связаны с переходом при охлаждении γ-железа в α-железо и распадом аустенита.
Линия GS соответствует температурам начала превращения аустенита в феррит. Ниже линии GS сплавы состоят из феррита и аустенита.
Линия ЕS показывает температуры начала выделения цементита из аустенита вследствие уменьшения растворимости углерода в аустените с понижением температуры. Цементит, выделяющийся из аустенита, называется вторичным цементитом.
В точке S при температуре 727°С и концентрации углерода в аустените 0,8% образуется эвтектоидная смесь состоящая из феррита и цементита, которая называется перлитом. Перлит получается в результате одновременного выпадения из аустенита частиц феррита и цементита. Процесс превращения аустенита в перлит можно записать формулой А0,8П[Ф0,03+Ц6,67].
Линия PQ показывает на уменьшение растворимости углерода в феррите при охлаждении и выделении цементита, который называется третичным цементитом.
Следовательно, сплавы, содержащие менее 0,008% углерода (точкаQ), являются однофазными и имеют структуру чистого феррита, а сплавы, содержащие углерод от 0,008 до 0,03% – структуру феррит + цементит третичный и называются техническим железом.
Доэвтектоидные стали при температуре ниже 727ºС имеют структуру феррит + перлит и заэвтектоидные – перлит + цементит вторичный в виде сетки по границам зерен.
В доэвтектических чугунах в интервале температур 1147–727ºС при охлаждении из аустенита выделяется цементит вторичный, вследствие уменьшения растворимости углерода (линия ES). По достижении температуры 727ºС (линия PSK) аустенит, обедненный углеродом до 0,8% (точка S), превращаясь в перлит. Таким образом, после окончательного охлаждения структура доэвтектических чугунов состоит из перлита, цементита вторичного и ледебурита превращенного (перлит + цементит).
Структура эвтектических чугунов при температурах ниже 727ºС состоит из ледебурита превращенного. Заэвтектический чугун при температурах ниже 727ºС состоит из ледебурита превращенного и цементита первичного.
Правило фаз устанавливает зависимость между числом степеней свободы, числом компонентов и числом фаз и выражается уравнением:
C = K + 1 – Ф,
где С – число степеней свободы системы;
К – число компонентов, образующих систему;
1 – число внешних факторов (внешним фактором считаем только температуру, так как давление за исключением очень высокого мало влияет на фазовое равновесие сплавов в твердом и жидком состояниях);
Ф – число фаз, находящихся в равновесии.
Сплав железа с углеродом, содержащий 4,6%С, называется заэвтектическим чугуном. Его структура при комнатной температуре – цементит (первичный) + ледебурит.
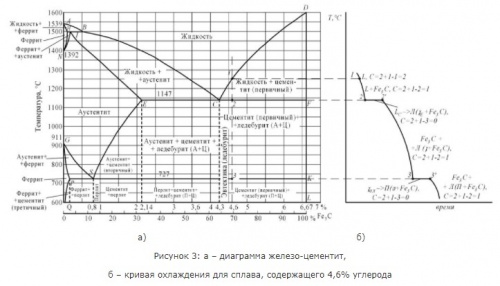
После закалки углеродистой стали была получена структура, состоящая из феррита и мартенсита. Нанесите на диаграмму состояния (примерно), укажите принятую в данном случае температуру нагрева под закалку и опишите все превращения, которые совершились в стали при нагреве и охлаждении. Как называется такой вид закалки?
Температура точки Ас3 для стали 45 составляет 755°С, а Ас1 равна 730°С. Структура доэвтектоидной стали при нагреве её до критической точки Ас1 состоит из зерен перлита и феррита. В точке Ас1 происходит превращение перлита в мелкозернистый аустенит. При дальнейшем нагреве от точки Ас1 до Ас3 избыточный феррит растворяется в аустените и при достижении Ас3 (линия GS) превращения заканчиваются.
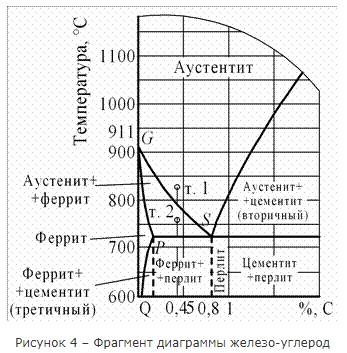
Если доэвтектоидную сталь нагреть выше Ас1, но ниже Ас3 (неполная закалка), то в ее структуре после закалки наряду с мартенситом будут участки феррита. Присутствие феррита как мягкой составляющей снижает твердость стали после закалки. При нагреве до температуры, например, 740°С (т.2 на рисунке 4) структура стали 45 – аустенит + феррит, после охлаждения со скоростью выше критической структура стали – мартенсит + феррит. Температура нагрева стали 45 под неполную закалку составляет 730-755°С.
Для каких сталей применяется отжиг на зернистый перлит? Объясните выбор режима и цель этого вида обработки.
Углеродистые инструментальные стали У8 (У8А), У10 (У10А), У11 (У11А), У12 (У12А) и У13(У13А) вследствие малой устойчивости переохлажденного аустенита имеют небольшую прокаливаемость, и поэтому эти стали применяются для инструментов небольших размеров.
Для заэвтектоидных сталей полный отжиг с нагревом выше Аст (линия ES) вообще не используют, так как при медленном охлаждении после такого нагрева образуется грубая сетка вторичного цементита, ухудшающая механические свойства. К заэвтектоидным углеродистым сталям широко применяют отжиг с нагревом до 740—780 °С и последующим медленным охлаждением. После такого нагрева в аустените остается большое число нерастворившихся включений цементита, которые служат центрами кристаллизации во время распада аустенита при охлаждении.
В результате образуется структура зернистого перлита (сферодита), почему этот отжиг и называют сфероидизирующим. Мелкие частицы цементита при температуре отжига в интервале А1–Аст получаются в результате деления цементитных пластин.
Для режима сфероидизирующего отжига заэвтектоидных сталей характерен узкий температурный «интервал отжигаемости». Нижняя его граница должна находиться выше точки А1, а верхняя граница не должна быть слишком высокой, так как иначе из-за растворения в аустените центров карбидного выделения при охлаждении образуется пластинчатый перлит. Так как точки Аст и А1 сходятся при эвтектоидной концентрации, то у сталей, близких к эвтектоидному составу, «интервал отжигаемости» особенно узок. Например, для сталей У9А и У10А границы этого интервала 740-750 °С, в то время как для сталей У11А, У12А и У13А они находятся в пределах 750-780 °С.
Конечная структура зависит от скорости охлаждения и температуры сфероидизирующего отжига. Чем меньше скорость охлаждения, тем до больших размеров вырастают глобули карбида при распаде аустенита. Регулируя скорость охлаждения, можно получать структуры глобулярного перлита от точечного до крупнозернистого. Более мелкозернистый перлит обладает повышенной твердостью.
С повышением температуры отжига до 800-820 °С твердость снижается из-за развития сфероидизации, а при дальнейшем увеличении температуры отжига твердость растет из-за появления все в большем количестве пластинчатого перлита.
Сфероидизирующему отжигу подвергают углеродистые и легированные инструментальные и шарикоподшипниковые стали.
Сталь со структурой зернистого перлита обладает наименьшей твердостью, легче обрабатывается резанием. Кроме того, зернистый перлит является оптимальной исходной структурой перед закалкой. При исходной структуре зернистого перлита меньше склонность к росту аустенитного зерна, шире допустимый интервал закалочных температур, меньше склонность к растрескиванию при закалке, выше прочность и вязкость закаленной стали (мелкие глобули равномерно распределены в мартенсите закаленной заэвтектоидной стали.
Поэтому металлургические заводы поставляют отожженную инструментальную сталь со структурой зернистого перлита.
Модифицирование – использование специально вводимых в жидкий металл примесей (модификаторов) для получения мелкого зерна. Эти примеси, практически не изменяя химического состава сплава, вызывают при кристаллизации измельчение зерна и в итоге улучшение механических свойств. Так, например, при модифицировании магниевых сплавов зерно уменьшается с 0,2-0,3 до 0,01-0,02 мм. При литье слитков в фасонных отливках модифицирование чаще проводят введением в расплав добавок, которые образуют тугоплавкие соединения (карбиды, нитриды, оксиды), кристаллизирующиеся в первую очередь. Выделяясь в виде мельчайших частиц, эти соединения служат зародышами образующихся при затвердевании кристаллов (модификаторы I рода). В качестве модификаторов при модифицировании алюминиевых сплавов применяют Ti, V, Zr; стали – Al, V, Ti. Иногда используют растворимые в жидком металле модификаторы (модификаторы II рода), избирательно адсорбирующиеся на кристаллическом зародыше, которые снижают межфазовое поверхностное натяжение и затрудняют рост кристаллитов. Для алюминиевых сплавов в качестве модификаторов второго рода используют Li, Na, K, для стали – редкоземельные элементы.
Для измельчения структуры эвтектики и устранения избыточных кристаллов кремния силумины модифицируют натрием (0,05-0,08%) путем присадки к расплаву смеси солей 67% NaF и 33% NaCl. В присутствии натрия происходит смещение линий диаграммы состояния и заэвтектический (эвтектический) сплав АЛ2 (11-13% Si) становится доэвтектическим. В этом случае в структуре сплава вместо избыточного кремния появляются кристаллы α-твердого раствора. В процессе затвердевания кристаллы кремния обволакиваются пленкой силицида натрия Na2Si, которая затрудняет их рост. Такие изменения структуры улучшают механические свойства.
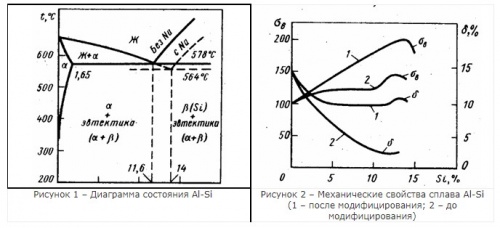
Что такое предел усталости? Опишите методику определения этой характеристики свойств металла.
Предел усталости – механическая характеристика материалов: наибольшее напряжение цикла, которое материал может выдержать повторно N раз без разрушения, где N – заданное техническими условиями большое число (напр., 106, 107, 108).
Испытание на усталость (ГОСТ 25502—79) проводят для определения предела выносливости, под которым понимают наибольшее значение максимального напряжения цикла, при действии которого не происходит усталостного разрушения образца после произвольно большого или заданного числа циклов нагружения. Цикл напряжения — это совокупность переменных значений напряжений за один период их изменения. За максимальное σmax или минимальное σmin напряжение цикла принимают наибольшее или наименьшее по алгебраической величине напряжение. Цикл характеризуется коэффициентом асимметрии: R = σmax/ σmin. Если R = -1, то цикл называют симметричным, если σmin и σmax не равны по величине, то цикл асимметричный.
Предел выносливости обозначается σR (R — коэффициент асимметрии цикла), а при симметричном цикле σ-1. Предел выносливости определяют на вращающемся образце (гладком или с надрезом) с приложением изгибающей нагрузки по симметричному циклу. Для определения используют не менее десяти образцов, чаще диаметром 7,5 мм. Каждый образец испытывают только на одном уровне напряжений до разрушения или до базового числа циклов. По результатам испытания отдельных образцов строят кривые усталости в полулогарифмических или логарифмических координатах σmax – 1/N.
Вычертите диаграмму состояния железо – углерод, укажите структурные составляющие во всех областях диаграммы, опишите превращения и постройте кривую охлаждения (с применением правила фаз) для сплава, содержащего 4,6% С. Какова структура этого сплава при комнатной температуре и как такой сплав называется?
Первичная кристаллизация сплавов системы железо-углерод начинается по достижении температур, соответствующих линии ABCD (линии ликвидус), и заканчивается при температурах, образующих линию AHJECF (линию солидус).
При кристаллизации сплавов по линии АВ из жидкого раствора выделяются кристаллы твердого раствора углерода в α-железе (δ-раствор). Процесс кристаллизации сплавов с содержанием углерода до 0,1 % заканчивается по линии АН с образованием α (δ)-твердого раствора. На линии HJB протекает перитектическое превращение, в результате которого образуется твердый раствор углерода в γ-железе, т. е. аустенит. Процесс первичной кристаллизации сталей заканчивается по линии AHJE.
При температурах, соответствующих линии ВС, из жидкого раствора кристаллизуется аустенит. В сплавах, содержащих от 4,3% до 6,67% углерода, при температурах, соответствующих линии CD, начинают выделяться кристаллы цементита первичного. Цементит, кристаллизующийся из жидкой фазы, называется первичным. B точке С при температуре 1147°С и концентрации углерода в жидком растворе 4,3% образуется эвтектика, которая называется ледебуритом. Эвтектическое превращение с образованием ледебурита можно записать формулой ЖР4,3Л[А2,14+Ц6,67]. Процесс первичной кристаллизации чугунов заканчивается по линии ECF образованием ледебурита.
Таким образом, структура чугунов ниже 1147°С будет: доэвтектических – аустенит + ледебурит, эвтектических – ледебурит и заэвтектических – цементит (первичный) + ледебурит.
Превращения, происходящие в твердом состоянии, называются вторичной кристаллизацией. Они связаны с переходом при охлаждении γ-железа в α-железо и распадом аустенита.
Линия GS соответствует температурам начала превращения аустенита в феррит. Ниже линии GS сплавы состоят из феррита и аустенита.
Линия ЕS показывает температуры начала выделения цементита из аустенита вследствие уменьшения растворимости углерода в аустените с понижением температуры. Цементит, выделяющийся из аустенита, называется вторичным цементитом.
В точке S при температуре 727°С и концентрации углерода в аустените 0,8% образуется эвтектоидная смесь состоящая из феррита и цементита, которая называется перлитом. Перлит получается в результате одновременного выпадения из аустенита частиц феррита и цементита. Процесс превращения аустенита в перлит можно записать формулой А0,8П[Ф0,03+Ц6,67].
Линия PQ показывает на уменьшение растворимости углерода в феррите при охлаждении и выделении цементита, который называется третичным цементитом.
Следовательно, сплавы, содержащие менее 0,008% углерода (точкаQ), являются однофазными и имеют структуру чистого феррита, а сплавы, содержащие углерод от 0,008 до 0,03% – структуру феррит + цементит третичный и называются техническим железом.
Доэвтектоидные стали при температуре ниже 727ºС имеют структуру феррит + перлит и заэвтектоидные – перлит + цементит вторичный в виде сетки по границам зерен.
В доэвтектических чугунах в интервале температур 1147–727ºС при охлаждении из аустенита выделяется цементит вторичный, вследствие уменьшения растворимости углерода (линия ES). По достижении температуры 727ºС (линия PSK) аустенит, обедненный углеродом до 0,8% (точка S), превращаясь в перлит. Таким образом, после окончательного охлаждения структура доэвтектических чугунов состоит из перлита, цементита вторичного и ледебурита превращенного (перлит + цементит).
Структура эвтектических чугунов при температурах ниже 727ºС состоит из ледебурита превращенного. Заэвтектический чугун при температурах ниже 727ºС состоит из ледебурита превращенного и цементита первичного.
Правило фаз устанавливает зависимость между числом степеней свободы, числом компонентов и числом фаз и выражается уравнением:
C = K + 1 – Ф,
где С – число степеней свободы системы;
К – число компонентов, образующих систему;
1 – число внешних факторов (внешним фактором считаем только температуру, так как давление за исключением очень высокого мало влияет на фазовое равновесие сплавов в твердом и жидком состояниях);
Ф – число фаз, находящихся в равновесии.
Сплав железа с углеродом, содержащий 4,6%С, называется заэвтектическим чугуном. Его структура при комнатной температуре – цементит (первичный) + ледебурит.
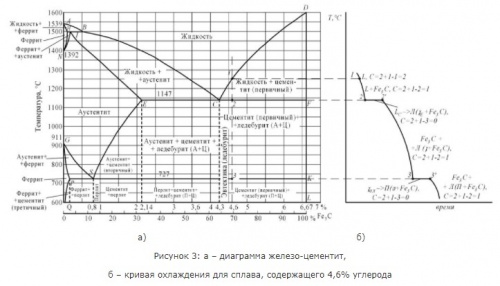
После закалки углеродистой стали была получена структура, состоящая из феррита и мартенсита. Нанесите на диаграмму состояния (примерно), укажите принятую в данном случае температуру нагрева под закалку и опишите все превращения, которые совершились в стали при нагреве и охлаждении. Как называется такой вид закалки?
Температура точки Ас3 для стали 45 составляет 755°С, а Ас1 равна 730°С. Структура доэвтектоидной стали при нагреве её до критической точки Ас1 состоит из зерен перлита и феррита. В точке Ас1 происходит превращение перлита в мелкозернистый аустенит. При дальнейшем нагреве от точки Ас1 до Ас3 избыточный феррит растворяется в аустените и при достижении Ас3 (линия GS) превращения заканчиваются.
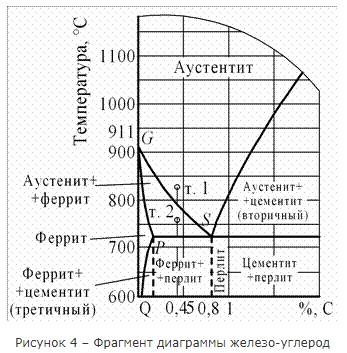
Если доэвтектоидную сталь нагреть выше Ас1, но ниже Ас3 (неполная закалка), то в ее структуре после закалки наряду с мартенситом будут участки феррита. Присутствие феррита как мягкой составляющей снижает твердость стали после закалки. При нагреве до температуры, например, 740°С (т.2 на рисунке 4) структура стали 45 – аустенит + феррит, после охлаждения со скоростью выше критической структура стали – мартенсит + феррит. Температура нагрева стали 45 под неполную закалку составляет 730-755°С.
Для каких сталей применяется отжиг на зернистый перлит? Объясните выбор режима и цель этого вида обработки.
Углеродистые инструментальные стали У8 (У8А), У10 (У10А), У11 (У11А), У12 (У12А) и У13(У13А) вследствие малой устойчивости переохлажденного аустенита имеют небольшую прокаливаемость, и поэтому эти стали применяются для инструментов небольших размеров.
Для заэвтектоидных сталей полный отжиг с нагревом выше Аст (линия ES) вообще не используют, так как при медленном охлаждении после такого нагрева образуется грубая сетка вторичного цементита, ухудшающая механические свойства. К заэвтектоидным углеродистым сталям широко применяют отжиг с нагревом до 740—780 °С и последующим медленным охлаждением. После такого нагрева в аустените остается большое число нерастворившихся включений цементита, которые служат центрами кристаллизации во время распада аустенита при охлаждении.
В результате образуется структура зернистого перлита (сферодита), почему этот отжиг и называют сфероидизирующим. Мелкие частицы цементита при температуре отжига в интервале А1–Аст получаются в результате деления цементитных пластин.
Для режима сфероидизирующего отжига заэвтектоидных сталей характерен узкий температурный «интервал отжигаемости». Нижняя его граница должна находиться выше точки А1, а верхняя граница не должна быть слишком высокой, так как иначе из-за растворения в аустените центров карбидного выделения при охлаждении образуется пластинчатый перлит. Так как точки Аст и А1 сходятся при эвтектоидной концентрации, то у сталей, близких к эвтектоидному составу, «интервал отжигаемости» особенно узок. Например, для сталей У9А и У10А границы этого интервала 740-750 °С, в то время как для сталей У11А, У12А и У13А они находятся в пределах 750-780 °С.
Конечная структура зависит от скорости охлаждения и температуры сфероидизирующего отжига. Чем меньше скорость охлаждения, тем до больших размеров вырастают глобули карбида при распаде аустенита. Регулируя скорость охлаждения, можно получать структуры глобулярного перлита от точечного до крупнозернистого. Более мелкозернистый перлит обладает повышенной твердостью.
С повышением температуры отжига до 800-820 °С твердость снижается из-за развития сфероидизации, а при дальнейшем увеличении температуры отжига твердость растет из-за появления все в большем количестве пластинчатого перлита.
Сфероидизирующему отжигу подвергают углеродистые и легированные инструментальные и шарикоподшипниковые стали.
Сталь со структурой зернистого перлита обладает наименьшей твердостью, легче обрабатывается резанием. Кроме того, зернистый перлит является оптимальной исходной структурой перед закалкой. При исходной структуре зернистого перлита меньше склонность к росту аустенитного зерна, шире допустимый интервал закалочных температур, меньше склонность к растрескиванию при закалке, выше прочность и вязкость закаленной стали (мелкие глобули равномерно распределены в мартенсите закаленной заэвтектоидной стали.
Поэтому металлургические заводы поставляют отожженную инструментальную сталь со структурой зернистого перлита.
0 комментариев