Контрольная работа 1 Вариант 33
Как влияют модификаторы на процесс кристаллизации? Приведите примеры практического использования процесса модифицирования.
Модифицирование – использование специально вводимых в жидкий металл примесей (модификаторов) для получения мелкого зерна. Эти примеси, практически не изменяя химического состава сплава, вызывают при кристаллизации измельчение зерна и в итоге улучшение механических свойств. Так, например, при модифицировании магниевых сплавов зерно уменьшается с 0,2-0,3 до 0,01-0,02 мм. При литье слитков в фасонных отливках
модифицирование чаще проводят введением в расплав добавок, которые образуют тугоплавкие соединения (карбиды, нитриды, оксиды), кристаллизирующиеся в первую очередь. Выделяясь в виде мельчайших частиц, эти соединения служат зародышами образующихся при затвердевании кристаллов (модификаторы I рода). В качестве модификаторов при модифицировании алюминиевых сплавов применяют Ti, V, Zr; стали – Al, V, Ti. Иногда используют растворимые в жидком металле модификаторы (модификаторы II рода), избирательно адсорбирующиеся на кристаллическом зародыше, которые снижают межфазовое поверхностное натяжение и затрудняют рост кристаллитов. Для алюминиевых сплавов в качестве модификаторов второго рода используют Li, Na, K, для стали – редкоземельные элементы.
Для измельчения структуры эвтектики и устранения избыточных кристаллов кремния силумины модифицируют натрием (0,05-0,08%) путем присадки к расплаву смеси солей 67% NaF и 33% NaCl. В присутствии натрия происходит смещение линий диаграммы состояния и заэвтектический (эвтектический) сплав АЛ2 (11-13% Si) становится доэвтектическим. В этом случае в структуре сплава вместо избыточного кремния появляются кристаллы α-твердого раствора. В процессе затвердевания кристаллы кремния обволакиваются пленкой силицида натрия Na2Si, которая затрудняет их рост. Такие изменения структуры улучшают механические свойства.
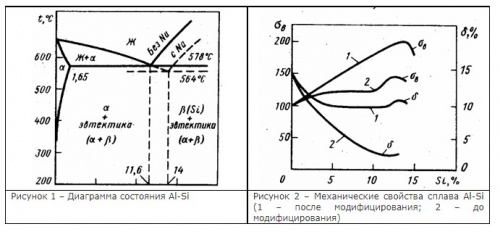
Как определяется температура порога рекристаллизации? Как влияют состав сплава и степень пластической деформации на эту температуру?
Рекристаллизация – процесс зарождения и роста новых недеформированных зерен при нагреве наклепанного металла до определенной температуры.
Наименьшую температуру начала рекристаллизации, при которой протекает рекристаллизация и происходит разупрочнение металла, называют температурным порогом рекристаллизации. Эта температура не является постоянной физической величиной. Для данного металла (сплава) она зависит от длительности нагрева, степени предварительной деформации, величины зерна до деформации и т. д.
Температура начала рекристаллизации металлов, подвергнутых значительной деформации, для технически чистых металлов составляет примерно 0,4 Тпл (правило А. А. Бочвара), для чистых металлов снижается до (0,1...0,2)Тпл, а для сплавов твердых растворов возрастает до (0,5...0,6)Тпл.
Т. е. с повышением чистоты металла температурный порог рекристаллизации снижается:

Сильно влияет на температуру начала рекристаллизации степень деформации при обработке давлением. С увеличением степени деформации температура начала рекристаллизации снижается. Объясняется это тем, что с увеличением степени деформации растут плотность дислокаций и энергия, накопленная при деформации, т. е. возрастает термодинамический стимул рекристаллизации.
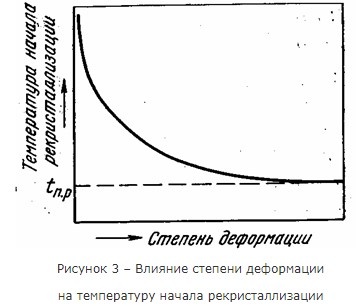
Т. к. плотность дислокаций и соответственно накопленная при деформации энергия с увеличением степени деформации растут с затуханием, то и температура начала рекристаллизации снижается при увеличении степени деформации с затуханием, достигая определенного предела при данном времени отжига.
Вычертите диаграмму состояния железо – карбид железа, укажите структурные составляющие во всех областях диаграммы, опишите превращения и постройте кривую охлаждения (с применением правила фаз) для сплава, содержащего 2,8% С. Какова структура этого сплава при комнатной температуре и как такой сплав называется?
Первичная кристаллизация сплавов системы железо-углерод начинается по достижении температур, соответствующих линии ABCD (линии ликвидус), и заканчивается при температурах, образующих линию AHJECF (линию солидус).
При кристаллизации сплавов по линии АВ из жидкого раствора выделяются кристаллы твердого раствора углерода в α-железе (δ-раствор). Процесс кристаллизации сплавов с содержанием углерода до 0,1 % заканчивается по линии АН с образованием α (δ)-твердого раствора. На линии HJB протекает перитектическое превращение, в результате которого образуется твердый раствор углерода в γ-железе, т. е. аустенит. Процесс первичной кристаллизации сталей заканчивается по линии AHJE.
При температурах, соответствующих линии ВС, из жидкого раствора кристаллизуется аустенит. В сплавах, содержащих от 4,3 % до 6,67 % углерода, при температурах, соответствующих линии CD, начинают выделяться кристаллы цементита первичного. Цементит, кристаллизующийся из жидкой фазы, называется первичным. B точке С при температуре 1147°С и концентрации углерода в жидком растворе 4,3 % образуется эвтектика, которая называется ледебуритом. Эвтектическое превращение с образованием ледебурита можно записать формулой ЖР4,3Л[А2,14+Ц6,67]. Процесс первичной кристаллизации чугунов заканчивается по линии ECF образованием ледебурита.
Таким образом, структура чугунов ниже 1147°С будет: доэвтектических – аустенит+ледебурит, эвтектических – ледебурит и заэвтектических – цементит (первичный)+ледебурит.
Превращения, происходящие в твердом состоянии, называются вторичной кристаллизацией. Они связаны с переходом при охлаждении γ-железа в α-железо и распадом аустенита.
Линия GS соответствует температурам начала превращения аустенита в феррит. Ниже линии GS сплавы состоят из феррита и аустенита.
Линия ЕS показывает температуры начала выделения цементита из аустенита вследствие уменьшения растворимости углерода в аустените с понижением температуры. Цементит, выделяющийся из аустенита, называется вторичным цементитом.
В точке S при температуре 727°С и концентрации углерода в аустените 0,8 % образуется эвтектоидная смесь состоящая из феррита и цементита, которая называется перлитом. Перлит получается в результате одновременного выпадения из аустенита частиц феррита и цементита. Процесс превращения аустенита в перлит можно записать формулой А0,8П[Ф0,03+Ц6,67].
Линия PQ показывает на уменьшение растворимости углерода в феррите при охлаждении и выделении цементита, который называется третичным цементитом.
Следовательно, сплавы, содержащие менее 0,008% углерода (точкаQ), являются однофазными и имеют структуру чистого феррита, а сплавы, содержащие углерод от 0,008 до 0,03% – структуру феррит+цементит третичный и называются техническим железом.
Доэвтектоидные стали при температуре ниже 727ºС имеют структуру феррит + перлит и заэвтектоидные – перлит + цементит вторичный в виде сетки по границам зерен.
В доэвтектических чугунах в интервале температур 1147–727ºС при охлаждении из аустенита выделяется цементит вторичный, вследствие уменьшения растворимости углерода(линия ES). По достижении температуры 727ºС (линия PSK) аустенит, обедненный углеродом до 0,8% (точка S), превращаясь в перлит. Таким образом, после окончательного охлаждения структура доэвтектических чугунов состоит из перлита, цементита вторичного и ледебурита превращенного (перлит+цементит).
Структура эвтектических чугунов при температурах ниже 727ºС состоит из ледебурита превращенного. Заэвтектический чугун при температурах ниже 727ºС состоит из ледебурита превращенного и цементита первичного.
Правило фаз устанавливает зависимость между числом степеней свободы, числом компонентов и числом фаз и выражается уравнением:
C = K + 1 – Ф,
где С – число степеней свободы системы;
К – число компонентов, образующих систему;
1 – число внешних факторов (внешним фактором считаем только температуру, так как давление за исключением очень высокого мало влияет на фазовое равновесие сплавов в твердом и жидком состояниях);
Ф – число фаз, находящихся в равновесии.
Сплав железа с углеродом, содержащий 2,8 %С, называется доэвтектический чугун. Его структура при комнатной температуре – перлит + цементит (вторичный) + ледебурит (перлит + цементит).
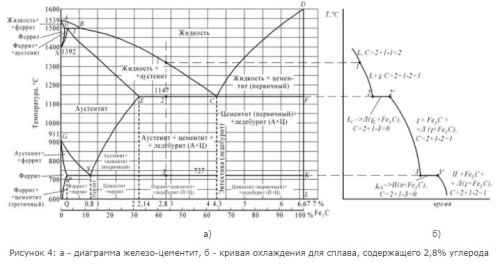
Что такое закалка? Используя диаграмму состояния железо-цементит укажите температуру нагрева под закалку стали 40 и У10. Опишите превращения, происходящие в сталях при выбранном режиме термической обработки, получаемую структуру и свойства.
Закалкой называется нагрев стали до температуры выше фазовых превращений, выдержка при этой температуре и быстрое охлаждение со скоростью больше критической.
Диаграмма состояния железо-цементит представлена на рисунке 2. При комнатной температуре сталь У10 имеет структуру цементита и перлита. До температуры Аc1 сохраняется исходная структура. При температуре Аc1 происходит превращение перлита в аустенит с содержанием углерода 0,8%. При нагреве выше точки Ас1 происходит растворение цементита в аустените (в соответствии с линией SE). Увеличение температуры выше точки Асm вызывает рост зерна аустенита.
Критические точки для стали У10: Аc1 = 730°С; Аcm = 800°С.
Для закалки заэвтектоидные стали нагревают на 50-70°С выше точки Ас1. Таким образом, температура нагрева под закалку составляет 780-800°С. При этих температурах в стали наряду с аустенитом имеется цементит. Поэтому после закалки в структуре заэвтектоидных сталей будет мартенсит с цементитом и небольшое количество остаточного аустенита. Охлаждающая среда при закалке – индустриальное масло. Твердость поверхности после закалки 62-64 HRC. Для снятия напряжений и стабилизации структуры после закалки изделия подвергают низкому отпуску.
Критические точки для стали 40: Аc1 = 730°С; Аc3 = 790°С. Для закалки доэвтектоидные стали нагревают на 30-50 °С выше точки Ас3. Температура нагрева под закалку составляет 820-850 °С.
Почему для изготовления инструмента применятся сталь с исходной структурой зернистого перлита? В результате какой термической обработки можно получить эту структуру? Приведите конкретный режим для любой инструментальной стали.
Сталь со структурой зернистого перлита обладает наименьшей твердостью, легче обрабатывается резанием. Кроме того, зернистый перлит является оптимальной исходной структурой перед закалкой. При исходной структуре зернистого перлита меньше склонность к росту аустенитного зерна, шире допустимый интервал закалочных температур, меньше склонность к растрескиванию при закалке, выше прочность и вязкость закаленной стали (мелкие глобули равномерно распределены в мартенсите закаленной заэвтектоидной стали.
Углеродистые инструментальные стали У8 (У8А), У10 (У10А), У11 (У11А), У12 (У12А) и У13 (У13А) вследствие малой устойчивости переохлажденного аустенита имеют небольшую прокаливаемость, и поэтому эти стали применяются для инструментов небольших размеров.
Для заэвтектоидных сталей полный отжиг с нагревом выше Аст (линия ES) вообще не используют, так как при медленном охлаждении после такого нагрева образуется грубая сетка вторичного цементита, ухудшающая механические свойства. К заэвтектоидным углеродистым сталям широко применяют отжиг с нагревом до 740—780 °С и последующим медленным охлаждением. После такого нагрева в аустените остается большое число нерастворившихся включений цементита, которые служат центрами кристаллизации во время распада аустенита при охлаждении.
В результате образуется структура зернистого перлита (сферодита), почему этот отжиг и называют сфероидизирующим. Мелкие частицы цементита при температуре отжига в интервале А1–Аст получаются в результате деления цементитных пластин.
Для режима сфероидизирующего отжига заэвтектоидных сталей характерен узкий температурный «интервал отжигаемости». Нижняя его граница должна находиться выше точки А1, а верхняя граница не должна быть слишком высокой, так как иначе из-за растворения в аустените центров карбидного выделения при охлаждении образуется пластинчатый перлит. Так как точки Аст и А1 сходятся при эвтектоидной концентрации, то у сталей, близких к эвтектоидному составу, «интервал отжигаемости» особенно узок. Например, для сталей У9А и У10А границы этого интервала 740-750 °С, в то время как для сталей У11А, У12А и У13А они находятся в пределах 750-780 °С.
Конечная структура зависит от скорости охлаждения и температуры сфероидизирующего отжига. Чем меньше скорость охлаждения, тем до больших размеров вырастают глобули карбида при распаде аустенита. Регулируя скорость охлаждения, можно получать структуры глобулярного перлита от точечного до крупнозернистого. Более мелкозернистый перлит обладает повышенной твердостью.
С повышением температуры отжига до 800-820 °С твердость снижается из-за развития сфероидизации, а при дальнейшем увеличении температуры отжига твердость растет из-за появления все в большем количестве пластинчатого перлита.
Сфероидизирующему отжигу подвергают углеродистые и легированные инструментальные и шарикоподшипниковые стали.
Модифицирование – использование специально вводимых в жидкий металл примесей (модификаторов) для получения мелкого зерна. Эти примеси, практически не изменяя химического состава сплава, вызывают при кристаллизации измельчение зерна и в итоге улучшение механических свойств. Так, например, при модифицировании магниевых сплавов зерно уменьшается с 0,2-0,3 до 0,01-0,02 мм. При литье слитков в фасонных отливках
модифицирование чаще проводят введением в расплав добавок, которые образуют тугоплавкие соединения (карбиды, нитриды, оксиды), кристаллизирующиеся в первую очередь. Выделяясь в виде мельчайших частиц, эти соединения служат зародышами образующихся при затвердевании кристаллов (модификаторы I рода). В качестве модификаторов при модифицировании алюминиевых сплавов применяют Ti, V, Zr; стали – Al, V, Ti. Иногда используют растворимые в жидком металле модификаторы (модификаторы II рода), избирательно адсорбирующиеся на кристаллическом зародыше, которые снижают межфазовое поверхностное натяжение и затрудняют рост кристаллитов. Для алюминиевых сплавов в качестве модификаторов второго рода используют Li, Na, K, для стали – редкоземельные элементы.
Для измельчения структуры эвтектики и устранения избыточных кристаллов кремния силумины модифицируют натрием (0,05-0,08%) путем присадки к расплаву смеси солей 67% NaF и 33% NaCl. В присутствии натрия происходит смещение линий диаграммы состояния и заэвтектический (эвтектический) сплав АЛ2 (11-13% Si) становится доэвтектическим. В этом случае в структуре сплава вместо избыточного кремния появляются кристаллы α-твердого раствора. В процессе затвердевания кристаллы кремния обволакиваются пленкой силицида натрия Na2Si, которая затрудняет их рост. Такие изменения структуры улучшают механические свойства.
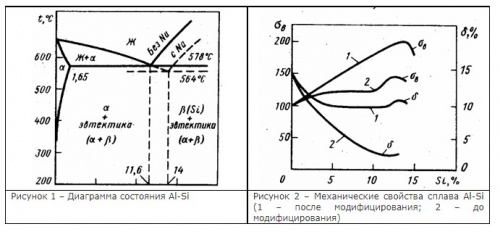
Как определяется температура порога рекристаллизации? Как влияют состав сплава и степень пластической деформации на эту температуру?
Рекристаллизация – процесс зарождения и роста новых недеформированных зерен при нагреве наклепанного металла до определенной температуры.
Наименьшую температуру начала рекристаллизации, при которой протекает рекристаллизация и происходит разупрочнение металла, называют температурным порогом рекристаллизации. Эта температура не является постоянной физической величиной. Для данного металла (сплава) она зависит от длительности нагрева, степени предварительной деформации, величины зерна до деформации и т. д.
Температура начала рекристаллизации металлов, подвергнутых значительной деформации, для технически чистых металлов составляет примерно 0,4 Тпл (правило А. А. Бочвара), для чистых металлов снижается до (0,1...0,2)Тпл, а для сплавов твердых растворов возрастает до (0,5...0,6)Тпл.
Т. е. с повышением чистоты металла температурный порог рекристаллизации снижается:

Сильно влияет на температуру начала рекристаллизации степень деформации при обработке давлением. С увеличением степени деформации температура начала рекристаллизации снижается. Объясняется это тем, что с увеличением степени деформации растут плотность дислокаций и энергия, накопленная при деформации, т. е. возрастает термодинамический стимул рекристаллизации.
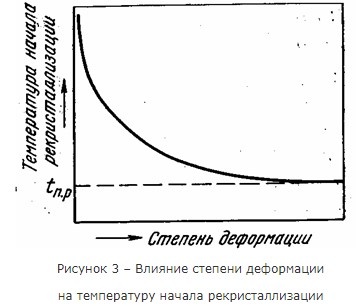
Т. к. плотность дислокаций и соответственно накопленная при деформации энергия с увеличением степени деформации растут с затуханием, то и температура начала рекристаллизации снижается при увеличении степени деформации с затуханием, достигая определенного предела при данном времени отжига.
Вычертите диаграмму состояния железо – карбид железа, укажите структурные составляющие во всех областях диаграммы, опишите превращения и постройте кривую охлаждения (с применением правила фаз) для сплава, содержащего 2,8% С. Какова структура этого сплава при комнатной температуре и как такой сплав называется?
Первичная кристаллизация сплавов системы железо-углерод начинается по достижении температур, соответствующих линии ABCD (линии ликвидус), и заканчивается при температурах, образующих линию AHJECF (линию солидус).
При кристаллизации сплавов по линии АВ из жидкого раствора выделяются кристаллы твердого раствора углерода в α-железе (δ-раствор). Процесс кристаллизации сплавов с содержанием углерода до 0,1 % заканчивается по линии АН с образованием α (δ)-твердого раствора. На линии HJB протекает перитектическое превращение, в результате которого образуется твердый раствор углерода в γ-железе, т. е. аустенит. Процесс первичной кристаллизации сталей заканчивается по линии AHJE.
При температурах, соответствующих линии ВС, из жидкого раствора кристаллизуется аустенит. В сплавах, содержащих от 4,3 % до 6,67 % углерода, при температурах, соответствующих линии CD, начинают выделяться кристаллы цементита первичного. Цементит, кристаллизующийся из жидкой фазы, называется первичным. B точке С при температуре 1147°С и концентрации углерода в жидком растворе 4,3 % образуется эвтектика, которая называется ледебуритом. Эвтектическое превращение с образованием ледебурита можно записать формулой ЖР4,3Л[А2,14+Ц6,67]. Процесс первичной кристаллизации чугунов заканчивается по линии ECF образованием ледебурита.
Таким образом, структура чугунов ниже 1147°С будет: доэвтектических – аустенит+ледебурит, эвтектических – ледебурит и заэвтектических – цементит (первичный)+ледебурит.
Превращения, происходящие в твердом состоянии, называются вторичной кристаллизацией. Они связаны с переходом при охлаждении γ-железа в α-железо и распадом аустенита.
Линия GS соответствует температурам начала превращения аустенита в феррит. Ниже линии GS сплавы состоят из феррита и аустенита.
Линия ЕS показывает температуры начала выделения цементита из аустенита вследствие уменьшения растворимости углерода в аустените с понижением температуры. Цементит, выделяющийся из аустенита, называется вторичным цементитом.
В точке S при температуре 727°С и концентрации углерода в аустените 0,8 % образуется эвтектоидная смесь состоящая из феррита и цементита, которая называется перлитом. Перлит получается в результате одновременного выпадения из аустенита частиц феррита и цементита. Процесс превращения аустенита в перлит можно записать формулой А0,8П[Ф0,03+Ц6,67].
Линия PQ показывает на уменьшение растворимости углерода в феррите при охлаждении и выделении цементита, который называется третичным цементитом.
Следовательно, сплавы, содержащие менее 0,008% углерода (точкаQ), являются однофазными и имеют структуру чистого феррита, а сплавы, содержащие углерод от 0,008 до 0,03% – структуру феррит+цементит третичный и называются техническим железом.
Доэвтектоидные стали при температуре ниже 727ºС имеют структуру феррит + перлит и заэвтектоидные – перлит + цементит вторичный в виде сетки по границам зерен.
В доэвтектических чугунах в интервале температур 1147–727ºС при охлаждении из аустенита выделяется цементит вторичный, вследствие уменьшения растворимости углерода(линия ES). По достижении температуры 727ºС (линия PSK) аустенит, обедненный углеродом до 0,8% (точка S), превращаясь в перлит. Таким образом, после окончательного охлаждения структура доэвтектических чугунов состоит из перлита, цементита вторичного и ледебурита превращенного (перлит+цементит).
Структура эвтектических чугунов при температурах ниже 727ºС состоит из ледебурита превращенного. Заэвтектический чугун при температурах ниже 727ºС состоит из ледебурита превращенного и цементита первичного.
Правило фаз устанавливает зависимость между числом степеней свободы, числом компонентов и числом фаз и выражается уравнением:
C = K + 1 – Ф,
где С – число степеней свободы системы;
К – число компонентов, образующих систему;
1 – число внешних факторов (внешним фактором считаем только температуру, так как давление за исключением очень высокого мало влияет на фазовое равновесие сплавов в твердом и жидком состояниях);
Ф – число фаз, находящихся в равновесии.
Сплав железа с углеродом, содержащий 2,8 %С, называется доэвтектический чугун. Его структура при комнатной температуре – перлит + цементит (вторичный) + ледебурит (перлит + цементит).
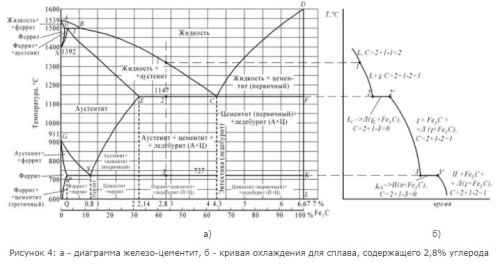
Что такое закалка? Используя диаграмму состояния железо-цементит укажите температуру нагрева под закалку стали 40 и У10. Опишите превращения, происходящие в сталях при выбранном режиме термической обработки, получаемую структуру и свойства.
Закалкой называется нагрев стали до температуры выше фазовых превращений, выдержка при этой температуре и быстрое охлаждение со скоростью больше критической.
Диаграмма состояния железо-цементит представлена на рисунке 2. При комнатной температуре сталь У10 имеет структуру цементита и перлита. До температуры Аc1 сохраняется исходная структура. При температуре Аc1 происходит превращение перлита в аустенит с содержанием углерода 0,8%. При нагреве выше точки Ас1 происходит растворение цементита в аустените (в соответствии с линией SE). Увеличение температуры выше точки Асm вызывает рост зерна аустенита.
Критические точки для стали У10: Аc1 = 730°С; Аcm = 800°С.
Для закалки заэвтектоидные стали нагревают на 50-70°С выше точки Ас1. Таким образом, температура нагрева под закалку составляет 780-800°С. При этих температурах в стали наряду с аустенитом имеется цементит. Поэтому после закалки в структуре заэвтектоидных сталей будет мартенсит с цементитом и небольшое количество остаточного аустенита. Охлаждающая среда при закалке – индустриальное масло. Твердость поверхности после закалки 62-64 HRC. Для снятия напряжений и стабилизации структуры после закалки изделия подвергают низкому отпуску.
Критические точки для стали 40: Аc1 = 730°С; Аc3 = 790°С. Для закалки доэвтектоидные стали нагревают на 30-50 °С выше точки Ас3. Температура нагрева под закалку составляет 820-850 °С.
Почему для изготовления инструмента применятся сталь с исходной структурой зернистого перлита? В результате какой термической обработки можно получить эту структуру? Приведите конкретный режим для любой инструментальной стали.
Сталь со структурой зернистого перлита обладает наименьшей твердостью, легче обрабатывается резанием. Кроме того, зернистый перлит является оптимальной исходной структурой перед закалкой. При исходной структуре зернистого перлита меньше склонность к росту аустенитного зерна, шире допустимый интервал закалочных температур, меньше склонность к растрескиванию при закалке, выше прочность и вязкость закаленной стали (мелкие глобули равномерно распределены в мартенсите закаленной заэвтектоидной стали.
Углеродистые инструментальные стали У8 (У8А), У10 (У10А), У11 (У11А), У12 (У12А) и У13 (У13А) вследствие малой устойчивости переохлажденного аустенита имеют небольшую прокаливаемость, и поэтому эти стали применяются для инструментов небольших размеров.
Для заэвтектоидных сталей полный отжиг с нагревом выше Аст (линия ES) вообще не используют, так как при медленном охлаждении после такого нагрева образуется грубая сетка вторичного цементита, ухудшающая механические свойства. К заэвтектоидным углеродистым сталям широко применяют отжиг с нагревом до 740—780 °С и последующим медленным охлаждением. После такого нагрева в аустените остается большое число нерастворившихся включений цементита, которые служат центрами кристаллизации во время распада аустенита при охлаждении.
В результате образуется структура зернистого перлита (сферодита), почему этот отжиг и называют сфероидизирующим. Мелкие частицы цементита при температуре отжига в интервале А1–Аст получаются в результате деления цементитных пластин.
Для режима сфероидизирующего отжига заэвтектоидных сталей характерен узкий температурный «интервал отжигаемости». Нижняя его граница должна находиться выше точки А1, а верхняя граница не должна быть слишком высокой, так как иначе из-за растворения в аустените центров карбидного выделения при охлаждении образуется пластинчатый перлит. Так как точки Аст и А1 сходятся при эвтектоидной концентрации, то у сталей, близких к эвтектоидному составу, «интервал отжигаемости» особенно узок. Например, для сталей У9А и У10А границы этого интервала 740-750 °С, в то время как для сталей У11А, У12А и У13А они находятся в пределах 750-780 °С.
Конечная структура зависит от скорости охлаждения и температуры сфероидизирующего отжига. Чем меньше скорость охлаждения, тем до больших размеров вырастают глобули карбида при распаде аустенита. Регулируя скорость охлаждения, можно получать структуры глобулярного перлита от точечного до крупнозернистого. Более мелкозернистый перлит обладает повышенной твердостью.
С повышением температуры отжига до 800-820 °С твердость снижается из-за развития сфероидизации, а при дальнейшем увеличении температуры отжига твердость растет из-за появления все в большем количестве пластинчатого перлита.
Сфероидизирующему отжигу подвергают углеродистые и легированные инструментальные и шарикоподшипниковые стали.
0 комментариев