Контрольная работа 1 Вариант 38
В чем сущность металлического, ионного и ковалентного типов связи?
Металлическая связь – тип связи атомов в кристаллических веществах, обладающих металлическими свойствами (металлах, металлидах). М. с. обусловлена большой концентрацией в таких кристаллах квазисвободных электронов (электронов проводимости). Отрицательно заряженный электронный газ «связывает» положительно заряженные ионы друг с другом.
Ковалентная связь – один из видов химической связи между двумя атомами, которая осуществляется общей для них электронной парой (по одному электрону от каждого атома).
К. с. существует как в молекулах (в любых агрегатных состояниях), так и между атомами, образующими решетку кристалла. К. с. может связывать одинаковые атомы (в молекулах H2, Cl2, в кристаллах алмаза) или разные (в молекулах воды, в кристаллах карборунда SiC). Почти все виды основных связей в молекулах органических соединений являются ковалентными (С — С, С — Н, С — N и др.). К. с. очень прочны. Этим объясняется малая химическая активность парафиновых углеводородов. Многие неорганические соединения, кристаллы которых имеют атомную решётку, то есть образуются с помощью К. с., являются тугоплавкими, обладают высокой твёрдостью и износостойкостью. К ним принадлежат некоторые карбиды, силициды, бориды, нитриды (в частности, известный боразон BN), нашедшие применение в новой технике.
Ионная связь – электровалентная связь, гетеровалентная связь, один из видов химической связи, в основе которого лежит электростатическое взаимодействие между противоположно заряженными ионами. Такие связи в сравнительно чистом виде образуются в галогенидах щелочных металлов, например KF, так как атомы щелочных металлов имеют по одному слабо удерживаемому электрону (энергия связи примерно 3-5 эв), а атомы галогенов обладают наибольшим сродством к электрону. Но даже в кристаллах (и тем более в молекулах) этих соединений полной передачи электрона от атома металла атому галогена большей частью все же не происходит.
Распространенные прежде представления об образовании в других случаях двух-, трех- или четырехзарядных ионов Ca2+, C2-, B3+, Si4+ не подтвердились, так как химическая связь образуется в таких случаях более сложным путём. Для оценки степени ионности связи пользуются понятием эффективного заряда иона.
Каким способом можно восстановить пластичность холоднокатанных медных лент? Назначьте режим термической обработки и опишите сущность происходящих процессов.
С увеличением степени холодной деформации свойства, характеризующие сопротивление деформации повышаются, а способность к пластической деформации уменьшается. Это явление получило название наклепа.
Рекристаллизационный отжиг используют в промышленности как первоначальную операцию перед холодной обработкой давлением (для придания материалу наибольшей пластичности), как промежуточный процесс между операциями холодного деформирования (для снятия наклепа) и как окончательную (выходную) термическую обработку (для придания полуфабрикату или изделию необходимых свойств).
При нагреве наклепанного металла не восстанавливается старое зерно, а появляется совершенно новое зерно, размеры которого могут существенно отличаться от исходного. Происходит образование новых, равноосных зерен вместо ориентированной волокнистой структуры деформированного металла.
Температура отжига для достижения рекристаллизации по всему объему и сокращения времени процесса превышает температуру порога рекристаллизации. Температура нагрева связана с температурой плавления: ТН ≈ 0,4 Тпл (для чистых металлов).
Для меди: Тн = 0,4 (1083 + 273) – 273 ≈ 270 °С.
Вычертите диаграмму состояния железо – карбид железа, укажите структурные составляющие во всех областях диаграммы, опишите превращения и постройте кривую охлаждения (с применением правила фаз) для сплава, содержащего 0,2% С. Какова структура этого сплава при комнатной температуре и как такой сплав называется?
Первичная кристаллизация сплавов системы железо-углерод начинается по достижении температур, соответствующих линии ABCD (линии ликвидус), и заканчивается при температурах, образующих линию AHJECF (линию солидус).
При кристаллизации сплавов по линии АВ из жидкого раствора выделяются кристаллы твердого раствора углерода в α-железе (δ-раствор). Процесс кристаллизации сплавов с содержанием углерода до 0,1 % заканчивается по линии АН с образованием α (δ)-твердого раствора. На линии HJB протекает перитектическое превращение, в результате которого образуется твердый раствор углерода в γ-железе, т. е. аустенит. Процесс первичной кристаллизации сталей заканчивается по линии AHJE.
При температурах, соответствующих линии ВС, из жидкого раствора кристаллизуется аустенит. В сплавах, содержащих от 4,3 % до 6,67 % углерода, при температурах, соответствующих линии CD, начинают выделяться кристаллы цементита первичного. Цементит, кристаллизующийся из жидкой фазы, называется первичным. B точке С при температуре 1147°С и концентрации углерода в жидком растворе 4,3 % образуется эвтектика, которая называется ледебуритом. Эвтектическое превращение с образованием ледебурита можно записать формулой ЖР4,3Л[А2,14+Ц6,67]. Процесс первичной кристаллизации чугунов заканчивается по линии ECF образованием ледебурита.
Таким образом, структура чугунов ниже 1147°С будет: доэвтектических – аустенит+ледебурит, эвтектических – ледебурит и заэвтектических – цементит (первичный)+ледебурит.
Превращения, происходящие в твердом состоянии, называются вторичной кристаллизацией. Они связаны с переходом при охлаждении γ-железа в α-железо и распадом аустенита.
Линия GS соответствует температурам начала превращения аустенита в феррит. Ниже линии GS сплавы состоят из феррита и аустенита.
Линия ЕS показывает температуры начала выделения цементита из аустенита вследствие уменьшения растворимости углерода в аустените с понижением температуры. Цементит, выделяющийся из аустенита, называется вторичным цементитом.
В точке S при температуре 727°С и концентрации углерода в аустените 0,8 % образуется эвтектоидная смесь состоящая из феррита и цементита, которая называется перлитом. Перлит получается в результате одновременного выпадения из аустенита частиц феррита и цементита. Процесс превращения аустенита в перлит можно записать формулой А0,8П[Ф0,03+Ц6,67].
Линия PQ показывает на уменьшение растворимости углерода в феррите при охлаждении и выделении цементита, который называется третичным цементитом.
Следовательно, сплавы, содержащие менее 0,008% углерода (точкаQ), являются однофазными и имеют структуру чистого феррита, а сплавы, содержащие углерод от 0,008 до 0,03% – структуру феррит+цементит третичный и называются техническим железом.
Доэвтектоидные стали при температуре ниже 727ºС имеют структуру феррит+перлит и заэвтектоидные – перлит+цементит вторичный в виде сетки по границам зерен.
В доэвтектических чугунах в интервале температур 1147–727ºС при охлаждении из аустенита выделяется цементит вторичный, вследствие уменьшения растворимости углерода(линия ES). По достижении температуры 727ºС (линия PSK) аустенит, обедненный углеродом до 0,8% (точка S), превращаясь в перлит. Таким образом, после окончательного охлаждения структура доэвтектических чугунов состоит из перлита, цементита вторичного и ледебурита превращенного (перлит+цементит).
Структура эвтектических чугунов при температурах ниже 727ºС состоит из ледебурита превращенного. Заэвтектический чугун при температурах ниже 727ºС состоит из ледебурита превращенного и цементита первичного.
Правило фаз устанавливает зависимость между числом степеней свободы, числом компонентов и числом фаз и выражается уравнением:
C = K + 1 – Ф,
где С – число степеней свободы системы;
К – число компонентов, образующих систему;
1 – число внешних факторов (внешним фактором считаем только температуру, так как давление за исключением очень высокого мало влияет на фазовое равновесие сплавов в твердом и жидком состояниях);
Ф – число фаз, находящихся в равновесии.
Сплав железа с углеродом, содержащий 0,2%С, называется доэвтектоидной сталью. Его структура при комнатной температуре – Феррит + Цементит (первичный).
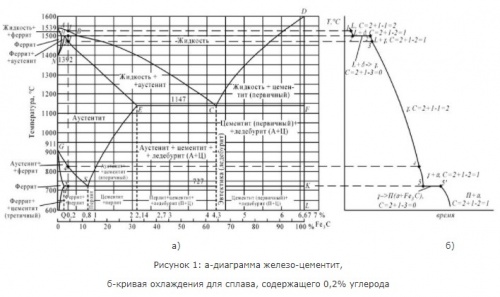
Используя диаграмму состояния железо-цементит, опишите структурные превращения, происходящие при нагреве стали У10. Укажите критические точки и выберите оптимальный режим нагрева этой стали под закалку. Охарактеризуйте процесс закалки, опишите получаемую структуру и свойства стали.
Диаграмма состояния железо-цементит представлена на рисунке 1. При комнатной температуре сталь У10 имеет структуру цементита и перлита. До температуры Аc1 сохраняется исходная структура. При температуре Аc1 происходит превращение перлита в аустенит с содержанием углерода 0,8%. При нагреве выше точки Ас1 происходит растворение цементита в аустените (в соответствии с линией SE). Увеличение температуры выше точки Асm вызывает рост зерна аустенита.
Критические точки для стали У10: Аc1 = 730°С; Аcm = 800°С.
Для закалки заэвтектоидные стали нагревают на 50-70°С выше точки Ас1. Таким образом, температура нагрева под закалку составляет 780-800°С. При этих температурах в стали наряду с аустенитом имеется цементит. Поэтому после закалки в структуре заэвтектоидных сталей будет мартенсит с цементитом и небольшое количество остаточного аустенита. Охлаждающая среда при закалке – индустриальное масло. Твердость поверхности после закалки 62-64 HRC. Для снятия напряжений и стабилизации структуры после закалки изделия подвергают низкому отпуску.
Используя диаграмму состояния железо – карбид железа и кривую изменения твердости в зависимости от температуры отпуска, назначьте для углеродистой стали 40 температуру закалки и температуру отпуска, необходимые для обеспечения твердости 250 НВ. Опишите превращения на всех этапах термической обработки и получаемую структуру.
Закалка доэвтектоидной стали заключается в нагреве стали до температуры выше критической (Ас3), в выдержке и последующем охлаждении со скоростью, превышающей критическую.
Температура точки Ас3 для стали 40 составляет 790°С.
Доэвтектоидные стали для закалки следует нагревать до температуры на 30-50°С выше Ас3. Температура нагрева стали под закалку, таким образом, составляет 820-840°С. Структура стали 40 при температуре нагрева под закалку – аустенит, после охлаждения со скоростью выше критической – мартенсит.
В зависимости от температуры отпуска меняется твердость закаленной стали. Например, при 600°С твердость НВ не более 200 ед., при 400°С – не более 280 ед., а при 200°С – не более 450 ед.
Поэтому для получения твердости 250 НВ закаленную сталь подвергают высокому отпуску при температуре 500-520°С. Структура стали после высокого отпуска – сорбит отпуска. Высокий отпуск создает наилучшее соотношение прочности и вязкости.
Термическая обработка, состоящая из закалки и высокого отпуска, называют улучшением.
Металлическая связь – тип связи атомов в кристаллических веществах, обладающих металлическими свойствами (металлах, металлидах). М. с. обусловлена большой концентрацией в таких кристаллах квазисвободных электронов (электронов проводимости). Отрицательно заряженный электронный газ «связывает» положительно заряженные ионы друг с другом.
Ковалентная связь – один из видов химической связи между двумя атомами, которая осуществляется общей для них электронной парой (по одному электрону от каждого атома).
К. с. существует как в молекулах (в любых агрегатных состояниях), так и между атомами, образующими решетку кристалла. К. с. может связывать одинаковые атомы (в молекулах H2, Cl2, в кристаллах алмаза) или разные (в молекулах воды, в кристаллах карборунда SiC). Почти все виды основных связей в молекулах органических соединений являются ковалентными (С — С, С — Н, С — N и др.). К. с. очень прочны. Этим объясняется малая химическая активность парафиновых углеводородов. Многие неорганические соединения, кристаллы которых имеют атомную решётку, то есть образуются с помощью К. с., являются тугоплавкими, обладают высокой твёрдостью и износостойкостью. К ним принадлежат некоторые карбиды, силициды, бориды, нитриды (в частности, известный боразон BN), нашедшие применение в новой технике.
Ионная связь – электровалентная связь, гетеровалентная связь, один из видов химической связи, в основе которого лежит электростатическое взаимодействие между противоположно заряженными ионами. Такие связи в сравнительно чистом виде образуются в галогенидах щелочных металлов, например KF, так как атомы щелочных металлов имеют по одному слабо удерживаемому электрону (энергия связи примерно 3-5 эв), а атомы галогенов обладают наибольшим сродством к электрону. Но даже в кристаллах (и тем более в молекулах) этих соединений полной передачи электрона от атома металла атому галогена большей частью все же не происходит.
Распространенные прежде представления об образовании в других случаях двух-, трех- или четырехзарядных ионов Ca2+, C2-, B3+, Si4+ не подтвердились, так как химическая связь образуется в таких случаях более сложным путём. Для оценки степени ионности связи пользуются понятием эффективного заряда иона.
Каким способом можно восстановить пластичность холоднокатанных медных лент? Назначьте режим термической обработки и опишите сущность происходящих процессов.
С увеличением степени холодной деформации свойства, характеризующие сопротивление деформации повышаются, а способность к пластической деформации уменьшается. Это явление получило название наклепа.
Рекристаллизационный отжиг используют в промышленности как первоначальную операцию перед холодной обработкой давлением (для придания материалу наибольшей пластичности), как промежуточный процесс между операциями холодного деформирования (для снятия наклепа) и как окончательную (выходную) термическую обработку (для придания полуфабрикату или изделию необходимых свойств).
При нагреве наклепанного металла не восстанавливается старое зерно, а появляется совершенно новое зерно, размеры которого могут существенно отличаться от исходного. Происходит образование новых, равноосных зерен вместо ориентированной волокнистой структуры деформированного металла.
Температура отжига для достижения рекристаллизации по всему объему и сокращения времени процесса превышает температуру порога рекристаллизации. Температура нагрева связана с температурой плавления: ТН ≈ 0,4 Тпл (для чистых металлов).
Для меди: Тн = 0,4 (1083 + 273) – 273 ≈ 270 °С.
Вычертите диаграмму состояния железо – карбид железа, укажите структурные составляющие во всех областях диаграммы, опишите превращения и постройте кривую охлаждения (с применением правила фаз) для сплава, содержащего 0,2% С. Какова структура этого сплава при комнатной температуре и как такой сплав называется?
Первичная кристаллизация сплавов системы железо-углерод начинается по достижении температур, соответствующих линии ABCD (линии ликвидус), и заканчивается при температурах, образующих линию AHJECF (линию солидус).
При кристаллизации сплавов по линии АВ из жидкого раствора выделяются кристаллы твердого раствора углерода в α-железе (δ-раствор). Процесс кристаллизации сплавов с содержанием углерода до 0,1 % заканчивается по линии АН с образованием α (δ)-твердого раствора. На линии HJB протекает перитектическое превращение, в результате которого образуется твердый раствор углерода в γ-железе, т. е. аустенит. Процесс первичной кристаллизации сталей заканчивается по линии AHJE.
При температурах, соответствующих линии ВС, из жидкого раствора кристаллизуется аустенит. В сплавах, содержащих от 4,3 % до 6,67 % углерода, при температурах, соответствующих линии CD, начинают выделяться кристаллы цементита первичного. Цементит, кристаллизующийся из жидкой фазы, называется первичным. B точке С при температуре 1147°С и концентрации углерода в жидком растворе 4,3 % образуется эвтектика, которая называется ледебуритом. Эвтектическое превращение с образованием ледебурита можно записать формулой ЖР4,3Л[А2,14+Ц6,67]. Процесс первичной кристаллизации чугунов заканчивается по линии ECF образованием ледебурита.
Таким образом, структура чугунов ниже 1147°С будет: доэвтектических – аустенит+ледебурит, эвтектических – ледебурит и заэвтектических – цементит (первичный)+ледебурит.
Превращения, происходящие в твердом состоянии, называются вторичной кристаллизацией. Они связаны с переходом при охлаждении γ-железа в α-железо и распадом аустенита.
Линия GS соответствует температурам начала превращения аустенита в феррит. Ниже линии GS сплавы состоят из феррита и аустенита.
Линия ЕS показывает температуры начала выделения цементита из аустенита вследствие уменьшения растворимости углерода в аустените с понижением температуры. Цементит, выделяющийся из аустенита, называется вторичным цементитом.
В точке S при температуре 727°С и концентрации углерода в аустените 0,8 % образуется эвтектоидная смесь состоящая из феррита и цементита, которая называется перлитом. Перлит получается в результате одновременного выпадения из аустенита частиц феррита и цементита. Процесс превращения аустенита в перлит можно записать формулой А0,8П[Ф0,03+Ц6,67].
Линия PQ показывает на уменьшение растворимости углерода в феррите при охлаждении и выделении цементита, который называется третичным цементитом.
Следовательно, сплавы, содержащие менее 0,008% углерода (точкаQ), являются однофазными и имеют структуру чистого феррита, а сплавы, содержащие углерод от 0,008 до 0,03% – структуру феррит+цементит третичный и называются техническим железом.
Доэвтектоидные стали при температуре ниже 727ºС имеют структуру феррит+перлит и заэвтектоидные – перлит+цементит вторичный в виде сетки по границам зерен.
В доэвтектических чугунах в интервале температур 1147–727ºС при охлаждении из аустенита выделяется цементит вторичный, вследствие уменьшения растворимости углерода(линия ES). По достижении температуры 727ºС (линия PSK) аустенит, обедненный углеродом до 0,8% (точка S), превращаясь в перлит. Таким образом, после окончательного охлаждения структура доэвтектических чугунов состоит из перлита, цементита вторичного и ледебурита превращенного (перлит+цементит).
Структура эвтектических чугунов при температурах ниже 727ºС состоит из ледебурита превращенного. Заэвтектический чугун при температурах ниже 727ºС состоит из ледебурита превращенного и цементита первичного.
Правило фаз устанавливает зависимость между числом степеней свободы, числом компонентов и числом фаз и выражается уравнением:
C = K + 1 – Ф,
где С – число степеней свободы системы;
К – число компонентов, образующих систему;
1 – число внешних факторов (внешним фактором считаем только температуру, так как давление за исключением очень высокого мало влияет на фазовое равновесие сплавов в твердом и жидком состояниях);
Ф – число фаз, находящихся в равновесии.
Сплав железа с углеродом, содержащий 0,2%С, называется доэвтектоидной сталью. Его структура при комнатной температуре – Феррит + Цементит (первичный).
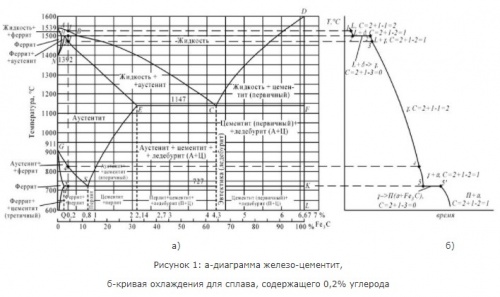
Используя диаграмму состояния железо-цементит, опишите структурные превращения, происходящие при нагреве стали У10. Укажите критические точки и выберите оптимальный режим нагрева этой стали под закалку. Охарактеризуйте процесс закалки, опишите получаемую структуру и свойства стали.
Диаграмма состояния железо-цементит представлена на рисунке 1. При комнатной температуре сталь У10 имеет структуру цементита и перлита. До температуры Аc1 сохраняется исходная структура. При температуре Аc1 происходит превращение перлита в аустенит с содержанием углерода 0,8%. При нагреве выше точки Ас1 происходит растворение цементита в аустените (в соответствии с линией SE). Увеличение температуры выше точки Асm вызывает рост зерна аустенита.
Критические точки для стали У10: Аc1 = 730°С; Аcm = 800°С.
Для закалки заэвтектоидные стали нагревают на 50-70°С выше точки Ас1. Таким образом, температура нагрева под закалку составляет 780-800°С. При этих температурах в стали наряду с аустенитом имеется цементит. Поэтому после закалки в структуре заэвтектоидных сталей будет мартенсит с цементитом и небольшое количество остаточного аустенита. Охлаждающая среда при закалке – индустриальное масло. Твердость поверхности после закалки 62-64 HRC. Для снятия напряжений и стабилизации структуры после закалки изделия подвергают низкому отпуску.
Используя диаграмму состояния железо – карбид железа и кривую изменения твердости в зависимости от температуры отпуска, назначьте для углеродистой стали 40 температуру закалки и температуру отпуска, необходимые для обеспечения твердости 250 НВ. Опишите превращения на всех этапах термической обработки и получаемую структуру.
Закалка доэвтектоидной стали заключается в нагреве стали до температуры выше критической (Ас3), в выдержке и последующем охлаждении со скоростью, превышающей критическую.
Температура точки Ас3 для стали 40 составляет 790°С.
Доэвтектоидные стали для закалки следует нагревать до температуры на 30-50°С выше Ас3. Температура нагрева стали под закалку, таким образом, составляет 820-840°С. Структура стали 40 при температуре нагрева под закалку – аустенит, после охлаждения со скоростью выше критической – мартенсит.
В зависимости от температуры отпуска меняется твердость закаленной стали. Например, при 600°С твердость НВ не более 200 ед., при 400°С – не более 280 ед., а при 200°С – не более 450 ед.
Поэтому для получения твердости 250 НВ закаленную сталь подвергают высокому отпуску при температуре 500-520°С. Структура стали после высокого отпуска – сорбит отпуска. Высокий отпуск создает наилучшее соотношение прочности и вязкости.
Термическая обработка, состоящая из закалки и высокого отпуска, называют улучшением.
0 комментариев