Контрольная работа 1 Вариант 39
Охарактеризуйте параметры процесса кристаллизации. Их влияние на величину зерна кристаллизующегося металла.
Величина зерна зависит от (параметров процесса кристаллизации):
– степени переохлаждения;
– температура нагрева и разливки жидкого металла;
– химический состав и присутствие посторонних примесей.
Охлаждение жидкости ниже равновесной температуры кристаллизации называется переохлаждением, которое характеризуется степенью переохлаждения (ΔТ):
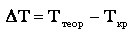
Процесс кристаллизации состоит из образования центров кристаллизации и роста кристаллов из этих центров.
В свою очередь, число центров кристаллизации (ч.ц.) и скорость роста кристаллов (с.р.) зависят от степени переохлаждения.
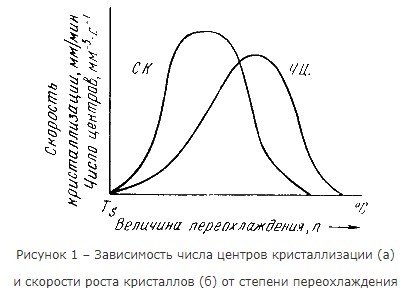
При небольшой степени переохлаждения ΔТ (малой скорости охлаждения) число зародышей мало. В этих условиях будет получено крупное зерно. С увеличением степени переохлаждения скорость образования зародышей возрастает, количество их увеличивается и размер зерна в затвердевшем металле уменьшается.
Часто источником образования зародышей являются всевозможные твердые частицы, которые всегда присутствуют в расплаве. Структурное сходство между поверхностями сопряжения зародыша и частицы посторонней примеси приводит к уменьшению размера критического зародыша, работы его образования, и затвердевание жидкости начинается при меньшем переохлаждении, чем при самопроизвольном зарождении.
Чем больше примесей, тем больше центров кристаллизации, тем мельче зерно.
Размер зерна сильно влияет на его механические свойства. Эти свойства, особенно вязкость и пластичность, выше, если металл имеет мелкое зерно.
В чем сущность явления наклепа? Его влияние на эксплуатационные свойства.
Наклеп – изменение структуры и свойств металлического материала, вызванное пластической деформацией.
Наклеп снижает пластичность и ударную вязкость, но увеличивает предел пропорциональность, предел текучести и твердость. Наклеп снижает сопротивление материала деформации противоположного знака. При поверхностном наклепе изменяется остаточное напряженное состояние в материале и повышается его усталостная прочность. Наклеп возникает при обработке металлов давлением (прокатка, волочение, ковка, штамповка), резанием, при обкатке роликами, при специальной обработке дробью.
Упрочнение металла в процессе пластической деформации (наклеп) объясняется увеличением числа дефектов кристаллического строения (дислокаций, вакансий, межузельных атомов). Повышение плотности дефектов кристаллического строения затрудняет движение отдельных новых дислокаций, а, следовательно, повышает сопротивление деформации и уменьшает пластичность. Наибольшее значение имеет увеличение плотности дислокаций, так как возникающее при этом между ними взаимодействие тормозит дальнейшее их перемещение.
Вычертите диаграмму состояния железо – карбид железа, укажите структурные составляющие во всех областях диаграммы, опишите превращения и постройте кривую охлаждения (с применением правила фаз) для сплава, содержащего 3,3% С. Какова структура этого сплава при комнатной температуре и как такой сплав называется?
Первичная кристаллизация сплавов системы железо-углерод начинается по достижении температур, соответствующих линии ABCD (линии ликвидус), и заканчивается при температурах, образующих линию AHJECF (линию солидус).
При кристаллизации сплавов по линии АВ из жидкого раствора выделяются кристаллы твердого раствора углерода в α-железе (δ-раствор). Процесс кристаллизации сплавов с содержанием углерода до 0,1 % заканчивается по линии АН с образованием α (δ)-твердого раствора. На линии HJB протекает перитектическое превращение, в результате которого образуется твердый раствор углерода в γ-железе, т. е. аустенит. Процесс первичной кристаллизации сталей заканчивается по линии AHJE.
При температурах, соответствующих линии ВС, из жидкого раствора кристаллизуется аустенит. В сплавах, содержащих от 4,3 % до 6,67 % углерода, при температурах, соответствующих линии CD, начинают выделяться кристаллы цементита первичного. Цементит, кристаллизующийся из жидкой фазы, называется первичным. B точке С при температуре 1147°С и концентрации углерода в жидком растворе 4,3 % образуется эвтектика, которая называется ледебуритом. Эвтектическое превращение с образованием ледебурита можно записать формулой ЖР4,3Л[А2,14+Ц6,67]. Процесс первичной кристаллизации чугунов заканчивается по линии ECF образованием ледебурита.
Таким образом, структура чугунов ниже 1147°С будет: доэвтектических — аустенит+ледебурит, эвтектических — ледебурит и заэвтектических — цементит (первичный)+ледебурит.
Превращения, происходящие в твердом состоянии, называются вторичной кристаллизацией. Они связаны с переходом при охлаждении γ-железа в α-железо и распадом аустенита.
Линия GS соответствует температурам начала превращения аустенита в феррит. Ниже линии GS сплавы состоят из феррита и аустенита.
Линия ЕS показывает температуры начала выделения цементита из аустенита вследствие уменьшения растворимости углерода в аустените с понижением температуры. Цементит, выделяющийся из аустенита, называется вторичным цементитом.
В точке S при температуре 727°С и концентрации углерода в аустените 0,8 % образуется эвтектоидная смесь состоящая из феррита и цементита, которая называется перлитом. Перлит получается в результате одновременного выпадения из аустенита частиц феррита и цементита. Процесс превращения аустенита в перлит можно записать формулой А0,8П[Ф0,03+Ц6,67].
Линия PQ показывает на уменьшение растворимости углерода в феррите при охлаждении и выделении цементита, который называется третичным цементитом.
Следовательно, сплавы, содержащие менее 0,008% углерода (точкаQ), являются однофазными и имеют структуру чистого феррита, а сплавы, содержащие углерод от 0,008 до 0,03% – структуру феррит+цементит третичный и называются техническим железом.
Доэвтектоидные стали при температуре ниже 727ºС имеют структуру феррит+перлит и заэвтектоидные – перлит+цементит вторичный в виде сетки по границам зерен.
В доэвтектических чугунах в интервале температур 1147–727ºС при охлаждении из аустенита выделяется цементит вторичный, вследствие уменьшения растворимости углерода(линия ES). По достижении температуры 727ºС (линия PSK) аустенит, обедненный углеродом до 0,8% (точка S), превращаясь в перлит. Таким образом, после окончательного охлаждения структура доэвтектических чугунов состоит из перлита, цементита вторичного и ледебурита превращенного (перлит+цементит).
Структура эвтектических чугунов при температурах ниже 727ºС состоит из ледебурита превращенного. Заэвтектический чугун при температурах ниже 727ºС состоит из ледебурита превращенного и цементита первичного.
Правило фаз устанавливает зависимость между числом степеней свободы, числом компонентов и числом фаз и выражается уравнением:
C = K + 1 – Ф,
где С – число степеней свободы системы;
К – число компонентов, образующих систему;
1 – число внешних факторов (внешним фактором считаем только температуру, так как давление за исключением очень высокого мало влияет на фазовое равновесие сплавов в твердом и жидком состояниях);
Ф – число фаз, находящихся в равновесии.
Сплав железа с углеродом, содержащий 3,3%С, называется доэвтектическим чугуном. Его структура при комнатной температуре цементит + перлит + ледебурит.
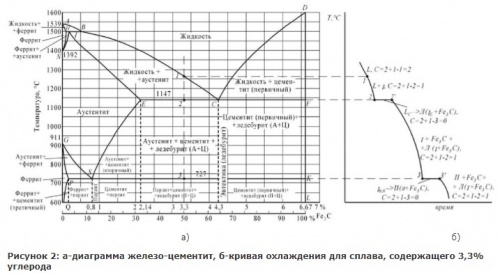
Что такое закалка? Используя диаграмму состояния железо – цементит, укажите температуру нагрева под закалку стали 50 и У12. Опишите превращения, происходящие в сталях при выбранном режиме обработки, получаемую структуру и свойства.
Закалкой называется нагрев стали до температуры выше фазовых превращений, выдержка при этой температуре и быстрое охлаждение со скоростью больше критической.
При комнатной температуре сталь У12 имеет структуру цементита и перлита. До температуры Аc1 сохраняется исходная структура. При температуре Аc1 происходит превращение перлита в аустенит с содержанием углерода 0,8%. При нагреве выше точки Ас1 происходит растворение цементита в аустените (в соответствии с линией SE). Увеличение температуры выше точки Асm вызывает рост зерна аустенита.
Критические точки для стали У12: Аc1 = 730°С; Аcm = 820°С.
Для закалки заэвтектоидные стали нагревают на 50-70°С выше точки Ас1.
Таким образом, температура нагрева под закалку составляет 780-800°С. При этих температурах в стали наряду с аустенитом имеется цементит. Поэтому после закалки в структуре заэвтектоидных сталей будет мартенсит с цементитом и небольшое количество остаточного аустенита. Охлаждающая среда при закалке – индустриальное масло. Твердость поверхности после закалки 62-64 HRC.
Критические точки для стали 50: Аc1 = 725°С; Аc3 = 760°С. Для закалки доэвтектоидные стали нагревают на 30-50 °С выше точки Ас3. Температура нагрева под закалку составляет 820-840°С. Охлаждающая среда при закалке – вода. Структура стали 50 при температуре нагрева под закалку – аустенит, после охлаждения со скоростью выше критической – мартенсит.
Для снятия напряжений и стабилизации структуры после закалки изделия подвергают низкому отпуску.
Изделия после правильно выполненной закалки и последующего отпуска имеют твердость более низкую, чем предусмотрено техническими условиями. Чем вызван этот эффект и как можно его исправить?
Рассмотрим данное задание на примере углеродистых сталей.
Недостаточная твердость закаленной стали может быть вызвана недогревом (низкая температура закалки, слишком короткая выдержка при правильной температуре печи) или при недостаточно интенсивном охлаждении, т.е. со скоростью меньше критической. Однако в задание указано, что закалка выполнена правильно. В результате закалки получен мартенсит (или мартенсит + цементит для заэвтектоидной стали).
Поэтому твердость более низкая, чем предусмотрено техническими условиями, есть результат проведения отпуска при температурах выше необходимых.
Зависимость твердости углеродистых сталей разного состава от температуры отпуска представлена на рисунке 3.
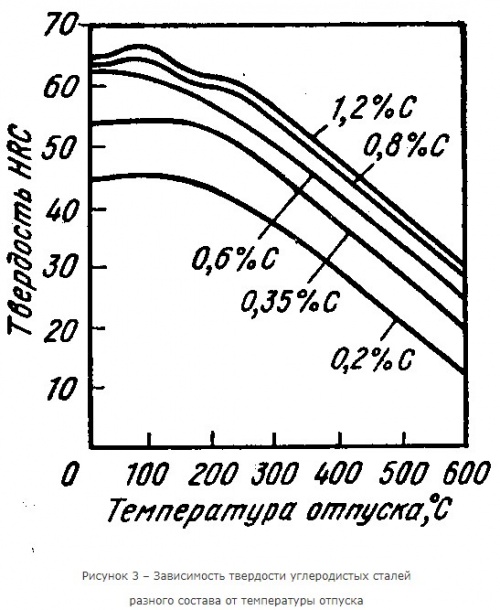
При нагреве при отпуске происходит выделение углерода из мартенсита, приводящее к уменьшению искажений решетки α-железа. Такой мартенсит называют отпущенным. При температурах порядка 300-400°С завершается выделение углерода и образуется высокодисперсная ферритно-цементитная смесь, называемая трооститом отпуска. При дальнейшем нагреве происходит коагуляция кристаллов карбидов и уменьшается дисперсность структуры. Структуру углеродистой стали образующуюся при температурах отпуска 500-650°С, называют сорбитом отпуска. При более высоких температурах нагрева образуется перлит отпуска.
С увеличением температуры отпуска общий уровень напряжений уменьшается, что выражается снижением твердости.
Величина зерна зависит от (параметров процесса кристаллизации):
– степени переохлаждения;
– температура нагрева и разливки жидкого металла;
– химический состав и присутствие посторонних примесей.
Охлаждение жидкости ниже равновесной температуры кристаллизации называется переохлаждением, которое характеризуется степенью переохлаждения (ΔТ):
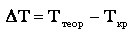
Процесс кристаллизации состоит из образования центров кристаллизации и роста кристаллов из этих центров.
В свою очередь, число центров кристаллизации (ч.ц.) и скорость роста кристаллов (с.р.) зависят от степени переохлаждения.
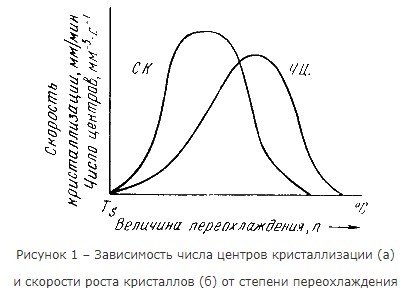
При небольшой степени переохлаждения ΔТ (малой скорости охлаждения) число зародышей мало. В этих условиях будет получено крупное зерно. С увеличением степени переохлаждения скорость образования зародышей возрастает, количество их увеличивается и размер зерна в затвердевшем металле уменьшается.
Часто источником образования зародышей являются всевозможные твердые частицы, которые всегда присутствуют в расплаве. Структурное сходство между поверхностями сопряжения зародыша и частицы посторонней примеси приводит к уменьшению размера критического зародыша, работы его образования, и затвердевание жидкости начинается при меньшем переохлаждении, чем при самопроизвольном зарождении.
Чем больше примесей, тем больше центров кристаллизации, тем мельче зерно.
Размер зерна сильно влияет на его механические свойства. Эти свойства, особенно вязкость и пластичность, выше, если металл имеет мелкое зерно.
В чем сущность явления наклепа? Его влияние на эксплуатационные свойства.
Наклеп – изменение структуры и свойств металлического материала, вызванное пластической деформацией.
Наклеп снижает пластичность и ударную вязкость, но увеличивает предел пропорциональность, предел текучести и твердость. Наклеп снижает сопротивление материала деформации противоположного знака. При поверхностном наклепе изменяется остаточное напряженное состояние в материале и повышается его усталостная прочность. Наклеп возникает при обработке металлов давлением (прокатка, волочение, ковка, штамповка), резанием, при обкатке роликами, при специальной обработке дробью.
Упрочнение металла в процессе пластической деформации (наклеп) объясняется увеличением числа дефектов кристаллического строения (дислокаций, вакансий, межузельных атомов). Повышение плотности дефектов кристаллического строения затрудняет движение отдельных новых дислокаций, а, следовательно, повышает сопротивление деформации и уменьшает пластичность. Наибольшее значение имеет увеличение плотности дислокаций, так как возникающее при этом между ними взаимодействие тормозит дальнейшее их перемещение.
Вычертите диаграмму состояния железо – карбид железа, укажите структурные составляющие во всех областях диаграммы, опишите превращения и постройте кривую охлаждения (с применением правила фаз) для сплава, содержащего 3,3% С. Какова структура этого сплава при комнатной температуре и как такой сплав называется?
Первичная кристаллизация сплавов системы железо-углерод начинается по достижении температур, соответствующих линии ABCD (линии ликвидус), и заканчивается при температурах, образующих линию AHJECF (линию солидус).
При кристаллизации сплавов по линии АВ из жидкого раствора выделяются кристаллы твердого раствора углерода в α-железе (δ-раствор). Процесс кристаллизации сплавов с содержанием углерода до 0,1 % заканчивается по линии АН с образованием α (δ)-твердого раствора. На линии HJB протекает перитектическое превращение, в результате которого образуется твердый раствор углерода в γ-железе, т. е. аустенит. Процесс первичной кристаллизации сталей заканчивается по линии AHJE.
При температурах, соответствующих линии ВС, из жидкого раствора кристаллизуется аустенит. В сплавах, содержащих от 4,3 % до 6,67 % углерода, при температурах, соответствующих линии CD, начинают выделяться кристаллы цементита первичного. Цементит, кристаллизующийся из жидкой фазы, называется первичным. B точке С при температуре 1147°С и концентрации углерода в жидком растворе 4,3 % образуется эвтектика, которая называется ледебуритом. Эвтектическое превращение с образованием ледебурита можно записать формулой ЖР4,3Л[А2,14+Ц6,67]. Процесс первичной кристаллизации чугунов заканчивается по линии ECF образованием ледебурита.
Таким образом, структура чугунов ниже 1147°С будет: доэвтектических — аустенит+ледебурит, эвтектических — ледебурит и заэвтектических — цементит (первичный)+ледебурит.
Превращения, происходящие в твердом состоянии, называются вторичной кристаллизацией. Они связаны с переходом при охлаждении γ-железа в α-железо и распадом аустенита.
Линия GS соответствует температурам начала превращения аустенита в феррит. Ниже линии GS сплавы состоят из феррита и аустенита.
Линия ЕS показывает температуры начала выделения цементита из аустенита вследствие уменьшения растворимости углерода в аустените с понижением температуры. Цементит, выделяющийся из аустенита, называется вторичным цементитом.
В точке S при температуре 727°С и концентрации углерода в аустените 0,8 % образуется эвтектоидная смесь состоящая из феррита и цементита, которая называется перлитом. Перлит получается в результате одновременного выпадения из аустенита частиц феррита и цементита. Процесс превращения аустенита в перлит можно записать формулой А0,8П[Ф0,03+Ц6,67].
Линия PQ показывает на уменьшение растворимости углерода в феррите при охлаждении и выделении цементита, который называется третичным цементитом.
Следовательно, сплавы, содержащие менее 0,008% углерода (точкаQ), являются однофазными и имеют структуру чистого феррита, а сплавы, содержащие углерод от 0,008 до 0,03% – структуру феррит+цементит третичный и называются техническим железом.
Доэвтектоидные стали при температуре ниже 727ºС имеют структуру феррит+перлит и заэвтектоидные – перлит+цементит вторичный в виде сетки по границам зерен.
В доэвтектических чугунах в интервале температур 1147–727ºС при охлаждении из аустенита выделяется цементит вторичный, вследствие уменьшения растворимости углерода(линия ES). По достижении температуры 727ºС (линия PSK) аустенит, обедненный углеродом до 0,8% (точка S), превращаясь в перлит. Таким образом, после окончательного охлаждения структура доэвтектических чугунов состоит из перлита, цементита вторичного и ледебурита превращенного (перлит+цементит).
Структура эвтектических чугунов при температурах ниже 727ºС состоит из ледебурита превращенного. Заэвтектический чугун при температурах ниже 727ºС состоит из ледебурита превращенного и цементита первичного.
Правило фаз устанавливает зависимость между числом степеней свободы, числом компонентов и числом фаз и выражается уравнением:
C = K + 1 – Ф,
где С – число степеней свободы системы;
К – число компонентов, образующих систему;
1 – число внешних факторов (внешним фактором считаем только температуру, так как давление за исключением очень высокого мало влияет на фазовое равновесие сплавов в твердом и жидком состояниях);
Ф – число фаз, находящихся в равновесии.
Сплав железа с углеродом, содержащий 3,3%С, называется доэвтектическим чугуном. Его структура при комнатной температуре цементит + перлит + ледебурит.
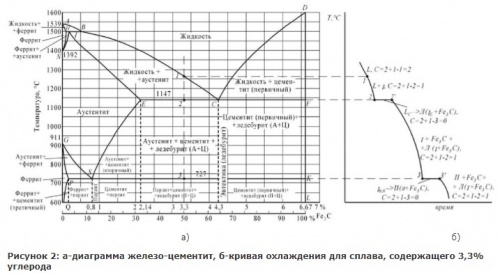
Что такое закалка? Используя диаграмму состояния железо – цементит, укажите температуру нагрева под закалку стали 50 и У12. Опишите превращения, происходящие в сталях при выбранном режиме обработки, получаемую структуру и свойства.
Закалкой называется нагрев стали до температуры выше фазовых превращений, выдержка при этой температуре и быстрое охлаждение со скоростью больше критической.
При комнатной температуре сталь У12 имеет структуру цементита и перлита. До температуры Аc1 сохраняется исходная структура. При температуре Аc1 происходит превращение перлита в аустенит с содержанием углерода 0,8%. При нагреве выше точки Ас1 происходит растворение цементита в аустените (в соответствии с линией SE). Увеличение температуры выше точки Асm вызывает рост зерна аустенита.
Критические точки для стали У12: Аc1 = 730°С; Аcm = 820°С.
Для закалки заэвтектоидные стали нагревают на 50-70°С выше точки Ас1.
Таким образом, температура нагрева под закалку составляет 780-800°С. При этих температурах в стали наряду с аустенитом имеется цементит. Поэтому после закалки в структуре заэвтектоидных сталей будет мартенсит с цементитом и небольшое количество остаточного аустенита. Охлаждающая среда при закалке – индустриальное масло. Твердость поверхности после закалки 62-64 HRC.
Критические точки для стали 50: Аc1 = 725°С; Аc3 = 760°С. Для закалки доэвтектоидные стали нагревают на 30-50 °С выше точки Ас3. Температура нагрева под закалку составляет 820-840°С. Охлаждающая среда при закалке – вода. Структура стали 50 при температуре нагрева под закалку – аустенит, после охлаждения со скоростью выше критической – мартенсит.
Для снятия напряжений и стабилизации структуры после закалки изделия подвергают низкому отпуску.
Изделия после правильно выполненной закалки и последующего отпуска имеют твердость более низкую, чем предусмотрено техническими условиями. Чем вызван этот эффект и как можно его исправить?
Рассмотрим данное задание на примере углеродистых сталей.
Недостаточная твердость закаленной стали может быть вызвана недогревом (низкая температура закалки, слишком короткая выдержка при правильной температуре печи) или при недостаточно интенсивном охлаждении, т.е. со скоростью меньше критической. Однако в задание указано, что закалка выполнена правильно. В результате закалки получен мартенсит (или мартенсит + цементит для заэвтектоидной стали).
Поэтому твердость более низкая, чем предусмотрено техническими условиями, есть результат проведения отпуска при температурах выше необходимых.
Зависимость твердости углеродистых сталей разного состава от температуры отпуска представлена на рисунке 3.
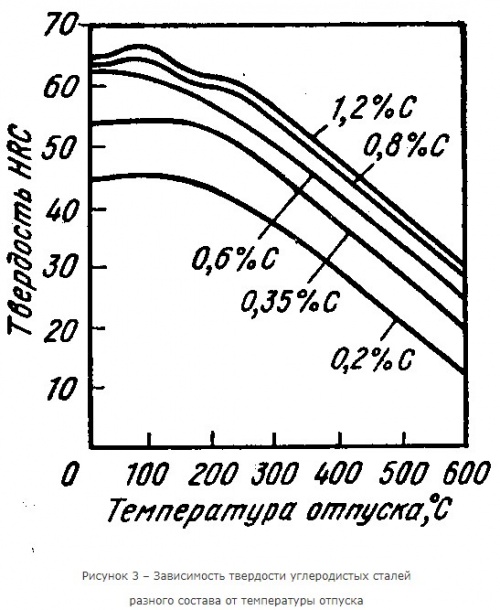
При нагреве при отпуске происходит выделение углерода из мартенсита, приводящее к уменьшению искажений решетки α-железа. Такой мартенсит называют отпущенным. При температурах порядка 300-400°С завершается выделение углерода и образуется высокодисперсная ферритно-цементитная смесь, называемая трооститом отпуска. При дальнейшем нагреве происходит коагуляция кристаллов карбидов и уменьшается дисперсность структуры. Структуру углеродистой стали образующуюся при температурах отпуска 500-650°С, называют сорбитом отпуска. При более высоких температурах нагрева образуется перлит отпуска.
С увеличением температуры отпуска общий уровень напряжений уменьшается, что выражается снижением твердости.
0 комментариев