Контрольная работа 1 Вариант 40
Начертите диаграмму состояния для случая неограниченной растворимости компонентов в твердом виде. Охарактеризуйте структуру сплавов.
Диаграмма состояний сплавов с неограниченной растворимостью компонентов представлена на рисунке 1.
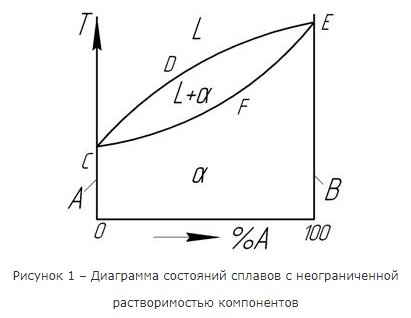
В этих сплавах компоненты в твердом состоянии неограниченно растворяются друг в друге; при этом образуется взаимный твердый раствор α. В данном случае чистые компоненты А и В не являются самостоятельными фазами системы, – они представляют собой предельные частные случаи твердого раствора α.
Однофазные области на диаграмме:
1) жидкость L – выше линии ликвидус CDE;
2) твердый раствор α – ниже линии солидус CFE.
Кристаллизация сплавов этого типа начинается на линии СDE и заканчивается на линии CFE постепенным переходом жидкого раствора L в твердые кристаллы α. Структуры всех сплавов этого типа при комнатной температура подобны: однородные кристаллы твердого раствора α, являющиеся единственной структурной составляющей в сплавах этого типа.
Что такое горячая пластическая деформация? Какие процессы происходят при этом? Опишите характер изменения структуры и свойств.
В зависимости от соотношения температуры деформации и температуры рекристаллизации различают холодную и горячую деформации.
Деформацию называют горячей, если ее проводят при температуре выше температуры рекристаллизации для получения полностью рекристаллизованной структуры.
При этих температурах деформация также вызывает упрочнение «горячий наклеп», которое полностью или частично снимается рекристаллизацией, протекающей при температурах обработки и при последующем охлаждении.
При горячей обработке давлением (прокатке, прессовании, ковке, штамповке и т. д.) упрочнение в результате наклепа (повышение плотности дислокаций) непосредственно в процессе деформации непрерывно чередуется с процессом разупрочнения (уменьшением плотности дислокаций) при динамической полигонизации и рекристаллизации во время деформации и охлаждения. В этом основное отличие динамической полигонизации и рекристаллизации от статической.
Горячую деформацию в зависимости от состава сплава и скорости деформации обычно проводят при температурах (0,7-0,75) Тпл.
Вычертите диаграмму состояния железо-карбид железа, укажите структурные составляющие во всех областях диаграммы, опишите превращения и постройте кривую охлаждения (с применением правила фаз) для сплава, содержащего 0,35% С. Какова структура этого сплава при комнатной температуре и как такой сплав называется?
Первичная кристаллизация сплавов системы железо-углерод начинается по достижении температур, соответствующих линии ABCD (линии ликвидус), и заканчивается при температурах, образующих линию AHJECF (линию солидус).
При кристаллизации сплавов по линии АВ из жидкого раствора выделяются кристаллы твердого раствора углерода в α-железе (δ-раствор). Процесс кристаллизации сплавов с содержанием углерода до 0,1 % заканчивается по линии АН с образованием α (δ)-твердого раствора. На линии HJB протекает перитектическое превращение, в результате которого образуется твердый раствор углерода в γ-железе, т. е. аустенит. Процесс первичной кристаллизации сталей заканчивается по линии AHJE.
При температурах, соответствующих линии ВС, из жидкого раствора кристаллизуется аустенит. В сплавах, содержащих от 4,3% до 6,67% углерода, при температурах, соответствующих линии CD, начинают выделяться кристаллы цементита первичного. Цементит, кристаллизующийся из жидкой фазы, называется первичным. B точке С при температуре 1147°С и концентрации углерода в жидком растворе 4,3% образуется эвтектика, которая называется ледебуритом. Эвтектическое превращение с образованием ледебурита можно записать формулой ЖР4,3Л[А2,14+Ц6,67]. Процесс первичной кристаллизации чугунов заканчивается по линии ECF образованием ледебурита.
Таким образом, структура чугунов ниже 1147°С будет: доэвтектических — аустенит + ледебурит, эвтектических — ледебурит и заэвтектических — цементит (первичный)+ледебурит.
Превращения, происходящие в твердом состоянии, называются вторичной кристаллизацией. Они связаны с переходом при охлаждении γ-железа в α-железо и распадом аустенита.
Линия GS соответствует температурам начала превращения аустенита в феррит. Ниже линии GS сплавы состоят из феррита и аустенита.
Линия ЕS показывает температуры начала выделения цементита из аустенита вследствие уменьшения растворимости углерода в аустените с понижением температуры. Цементит, выделяющийся из аустенита, называется вторичным цементитом.
В точке S при температуре 727°С и концентрации углерода в аустените 0,8 % образуется эвтектоидная смесь состоящая из феррита и цементита, которая называется перлитом. Перлит получается в результате одновременного выпадения из аустенита частиц феррита и цементита. Процесс превращения аустенита в перлит можно записать формулой А0,8П[Ф0,03+Ц6,67].
Линия PQ показывает на уменьшение растворимости углерода в феррите при охлаждении и выделении цементита, который называется третичным цементитом.
Следовательно, сплавы, содержащие менее 0,008% углерода (точка Q), являются однофазными и имеют структуру чистого феррита, а сплавы, содержащие углерод от 0,008 до 0,03% – структуру феррит+цементит третичный и называются техническим железом.
Доэвтектоидные стали при температуре ниже 727 ºС имеют структуру феррит + перлит и заэвтектоидные – перлит + цементит вторичный в виде сетки по границам зерен.
В доэвтектических чугунах в интервале температур 1147–727 ºС при охлаждении из аустенита выделяется цементит вторичный, вследствие уменьшения растворимости углерода (линия ES). По достижении температуры 727 ºС (линия PSK) аустенит, обедненный углеродом до 0,8 % (точка S), превращаясь в перлит. Таким образом, после окончательного охлаждения структура доэвтектических чугунов состоит из перлита, цементита вторичного и ледебурита превращенного (перлит + цементит).
Структура эвтектических чугунов при температурах ниже 727ºС состоит из ледебурита превращенного. Заэвтектический чугун при температурах ниже 727ºС состоит из ледебурита превращенного и цементита первичного.
Правило фаз устанавливает зависимость между числом степеней свободы, числом компонентов и числом фаз и выражается уравнением:
C = K + 1 – Ф,
где С – число степеней свободы системы;
К – число компонентов, образующих систему;
1 – число внешних факторов (внешним фактором считаем только температуру, так как давление за исключением очень высокого мало влияет на фазовое равновесие сплавов в твердом и жидком состояниях);
Ф – число фаз, находящихся в равновесии.
Сплав железа с углеродом, содержащий 0,35 % С, называется доэвтектоидной сталью. Его структура при комнатной температуре феррит + перлит.
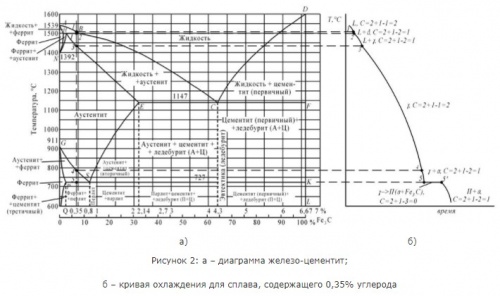
Покажите графически режим отжига для получения перлитного ковкого чугуна. Опишите структурные превращения, происходящие в процессе отжига. Каковы механические свойства чугуна после термической обработки, его структура?
Ковкие чугуны получают из белых чугунов путем графитизирующего отжига (томление).
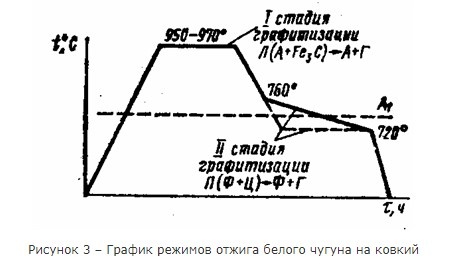
Отжиг проводится в две стадии. Сначала отливки белого чугуна нагревают в течение 20-25 ч до температуры 950-970 °С. Во время выдержки (15 ч) при этой температуре протекает первая стадия графитизации, г. е. распад цементита, входящего в состав ледебурита (A + Fe3C), и установление стабильного равновесия аустенит + графит. В результате распада цементита образуется хлопьевидный графит. Затем отливки медленно охлаждают (в течение 6-12 ч) до температуры 720 °С. При охлаждении происходит выделение из аустенита вторичного графита и рост графитовых включений. По достижении температуры 720 °С дают вторую длительную выдержку, при которой происходит распад цементита, входящего в перлит, на феррит и графит. Вторая стадия графитизации длится около 30 ч, и после ее завершения структура чугуна состоит из графита и феррита. Излом ферритного чугуна бархатисто-черный ввиду большого количества графита.
Если вторую стадию графитизации не проводят, то получают ковкий чугун со структурой графит + перлит. Излом такого чугуна светлый.
Для ускорения отжига белого чугуна на ковкий принимают различные меры: чугун модифицируют алюминием (реже бором или висмутом), повышают температуру нагрева перед разливкой, проводят перед отжигом закалку, повышают температуру первой стадии графитизации (до 1080 °С) и т. д.
Маркируют ковкие чугуны буквами КЧ — ковкий чугун и цифрами. Первые цифры обозначают предел прочности при растяжении, вторые — относительное удлинение (%). Например: КЧ45-6; στ=450 МПа, =6 %.
Из ковкого чугуна изготовляют картер заднего моста, чашки дифференциала, тормозные колодки, ступицы колес для автомобилей и др.
Чугуны со специальными свойствами используются в тех случаях, когда отливка кроме прочности должна обладать специфическими свойствами (износостойкостью, коррозионной стойкостью, жаростойкостью и т. д.).
После термической обработки углеродистой стали получена структура: цементит + мартенсит отпуска. Нанесите на диаграмму состояния железо-цементит ординату заданной стали (примерно) и укажите температуру нагрева этой стали под закалку. Назначьте температуру отпуска, обеспечивающую получение указанной структуры и опишите все превращения, которые совершились в стали в процессе закалки и отпуска.
Структура цементит + мартенсит отпуска получается после закалки и низкого отпуска заэвтектоидной углеродистой стали. Рассмотрим на примере стали У12.
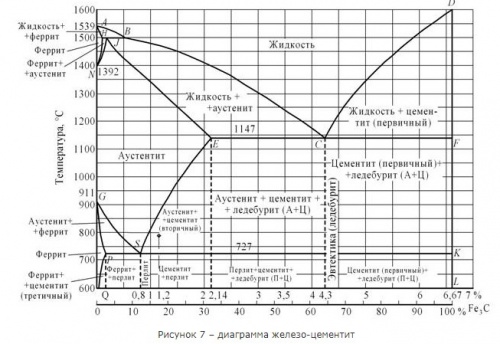
Диаграмма состояния железо-цементит представлена выше. При комнатной температуре сталь У12 имеет структуру цементита и перлита. До температуры Аc1 сохраняется исходная структура. При температуре Аc1 происходит превращение перлита в аустенит с содержанием углерода 0,8%. При нагреве выше точки Ас1 происходит растворение цементита в аустените (в соответствии с линией SE). Увеличение температуры выше точки Асm вызывает рост зерна аустенита.
Критические точки для стали У12: Аc1 = 730°С; Аcm = 820°С.
Для закалки заэвтектоидные стали нагревают на 50-70°С выше точки Ас1. Таким образом, температура нагрева под закалку составляет 780-800°С. При этих температурах в стали наряду с аустенитом имеется цементит. Поэтому после закалки в структуре заэвтектоидных сталей будет мартенсит с цементитом и небольшое количество остаточного аустенита.
Для снятия напряжений и стабилизации структуры после закалки изделия подвергают низкому отпуску при температуре 160–180 °С. Структура стали после низкого отпуска – отпущенный мартенсит + карбиды.
Диаграмма состояний сплавов с неограниченной растворимостью компонентов представлена на рисунке 1.
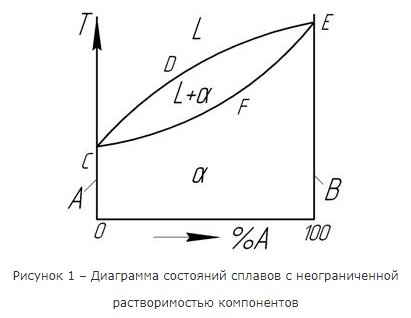
В этих сплавах компоненты в твердом состоянии неограниченно растворяются друг в друге; при этом образуется взаимный твердый раствор α. В данном случае чистые компоненты А и В не являются самостоятельными фазами системы, – они представляют собой предельные частные случаи твердого раствора α.
Однофазные области на диаграмме:
1) жидкость L – выше линии ликвидус CDE;
2) твердый раствор α – ниже линии солидус CFE.
Кристаллизация сплавов этого типа начинается на линии СDE и заканчивается на линии CFE постепенным переходом жидкого раствора L в твердые кристаллы α. Структуры всех сплавов этого типа при комнатной температура подобны: однородные кристаллы твердого раствора α, являющиеся единственной структурной составляющей в сплавах этого типа.
Что такое горячая пластическая деформация? Какие процессы происходят при этом? Опишите характер изменения структуры и свойств.
В зависимости от соотношения температуры деформации и температуры рекристаллизации различают холодную и горячую деформации.
Деформацию называют горячей, если ее проводят при температуре выше температуры рекристаллизации для получения полностью рекристаллизованной структуры.
При этих температурах деформация также вызывает упрочнение «горячий наклеп», которое полностью или частично снимается рекристаллизацией, протекающей при температурах обработки и при последующем охлаждении.
При горячей обработке давлением (прокатке, прессовании, ковке, штамповке и т. д.) упрочнение в результате наклепа (повышение плотности дислокаций) непосредственно в процессе деформации непрерывно чередуется с процессом разупрочнения (уменьшением плотности дислокаций) при динамической полигонизации и рекристаллизации во время деформации и охлаждения. В этом основное отличие динамической полигонизации и рекристаллизации от статической.
Горячую деформацию в зависимости от состава сплава и скорости деформации обычно проводят при температурах (0,7-0,75) Тпл.
Вычертите диаграмму состояния железо-карбид железа, укажите структурные составляющие во всех областях диаграммы, опишите превращения и постройте кривую охлаждения (с применением правила фаз) для сплава, содержащего 0,35% С. Какова структура этого сплава при комнатной температуре и как такой сплав называется?
Первичная кристаллизация сплавов системы железо-углерод начинается по достижении температур, соответствующих линии ABCD (линии ликвидус), и заканчивается при температурах, образующих линию AHJECF (линию солидус).
При кристаллизации сплавов по линии АВ из жидкого раствора выделяются кристаллы твердого раствора углерода в α-железе (δ-раствор). Процесс кристаллизации сплавов с содержанием углерода до 0,1 % заканчивается по линии АН с образованием α (δ)-твердого раствора. На линии HJB протекает перитектическое превращение, в результате которого образуется твердый раствор углерода в γ-железе, т. е. аустенит. Процесс первичной кристаллизации сталей заканчивается по линии AHJE.
При температурах, соответствующих линии ВС, из жидкого раствора кристаллизуется аустенит. В сплавах, содержащих от 4,3% до 6,67% углерода, при температурах, соответствующих линии CD, начинают выделяться кристаллы цементита первичного. Цементит, кристаллизующийся из жидкой фазы, называется первичным. B точке С при температуре 1147°С и концентрации углерода в жидком растворе 4,3% образуется эвтектика, которая называется ледебуритом. Эвтектическое превращение с образованием ледебурита можно записать формулой ЖР4,3Л[А2,14+Ц6,67]. Процесс первичной кристаллизации чугунов заканчивается по линии ECF образованием ледебурита.
Таким образом, структура чугунов ниже 1147°С будет: доэвтектических — аустенит + ледебурит, эвтектических — ледебурит и заэвтектических — цементит (первичный)+ледебурит.
Превращения, происходящие в твердом состоянии, называются вторичной кристаллизацией. Они связаны с переходом при охлаждении γ-железа в α-железо и распадом аустенита.
Линия GS соответствует температурам начала превращения аустенита в феррит. Ниже линии GS сплавы состоят из феррита и аустенита.
Линия ЕS показывает температуры начала выделения цементита из аустенита вследствие уменьшения растворимости углерода в аустените с понижением температуры. Цементит, выделяющийся из аустенита, называется вторичным цементитом.
В точке S при температуре 727°С и концентрации углерода в аустените 0,8 % образуется эвтектоидная смесь состоящая из феррита и цементита, которая называется перлитом. Перлит получается в результате одновременного выпадения из аустенита частиц феррита и цементита. Процесс превращения аустенита в перлит можно записать формулой А0,8П[Ф0,03+Ц6,67].
Линия PQ показывает на уменьшение растворимости углерода в феррите при охлаждении и выделении цементита, который называется третичным цементитом.
Следовательно, сплавы, содержащие менее 0,008% углерода (точка Q), являются однофазными и имеют структуру чистого феррита, а сплавы, содержащие углерод от 0,008 до 0,03% – структуру феррит+цементит третичный и называются техническим железом.
Доэвтектоидные стали при температуре ниже 727 ºС имеют структуру феррит + перлит и заэвтектоидные – перлит + цементит вторичный в виде сетки по границам зерен.
В доэвтектических чугунах в интервале температур 1147–727 ºС при охлаждении из аустенита выделяется цементит вторичный, вследствие уменьшения растворимости углерода (линия ES). По достижении температуры 727 ºС (линия PSK) аустенит, обедненный углеродом до 0,8 % (точка S), превращаясь в перлит. Таким образом, после окончательного охлаждения структура доэвтектических чугунов состоит из перлита, цементита вторичного и ледебурита превращенного (перлит + цементит).
Структура эвтектических чугунов при температурах ниже 727ºС состоит из ледебурита превращенного. Заэвтектический чугун при температурах ниже 727ºС состоит из ледебурита превращенного и цементита первичного.
Правило фаз устанавливает зависимость между числом степеней свободы, числом компонентов и числом фаз и выражается уравнением:
C = K + 1 – Ф,
где С – число степеней свободы системы;
К – число компонентов, образующих систему;
1 – число внешних факторов (внешним фактором считаем только температуру, так как давление за исключением очень высокого мало влияет на фазовое равновесие сплавов в твердом и жидком состояниях);
Ф – число фаз, находящихся в равновесии.
Сплав железа с углеродом, содержащий 0,35 % С, называется доэвтектоидной сталью. Его структура при комнатной температуре феррит + перлит.
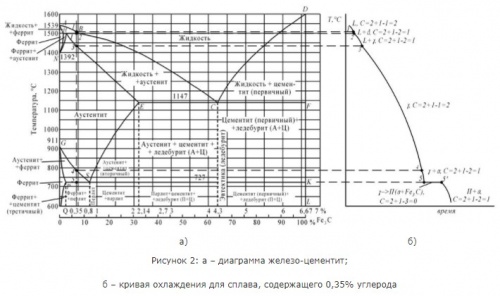
Покажите графически режим отжига для получения перлитного ковкого чугуна. Опишите структурные превращения, происходящие в процессе отжига. Каковы механические свойства чугуна после термической обработки, его структура?
Ковкие чугуны получают из белых чугунов путем графитизирующего отжига (томление).
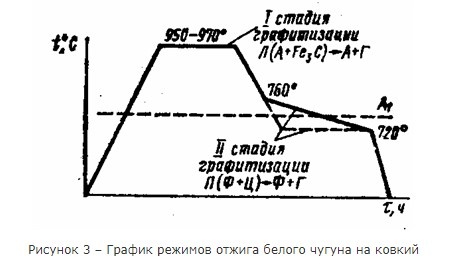
Отжиг проводится в две стадии. Сначала отливки белого чугуна нагревают в течение 20-25 ч до температуры 950-970 °С. Во время выдержки (15 ч) при этой температуре протекает первая стадия графитизации, г. е. распад цементита, входящего в состав ледебурита (A + Fe3C), и установление стабильного равновесия аустенит + графит. В результате распада цементита образуется хлопьевидный графит. Затем отливки медленно охлаждают (в течение 6-12 ч) до температуры 720 °С. При охлаждении происходит выделение из аустенита вторичного графита и рост графитовых включений. По достижении температуры 720 °С дают вторую длительную выдержку, при которой происходит распад цементита, входящего в перлит, на феррит и графит. Вторая стадия графитизации длится около 30 ч, и после ее завершения структура чугуна состоит из графита и феррита. Излом ферритного чугуна бархатисто-черный ввиду большого количества графита.
Если вторую стадию графитизации не проводят, то получают ковкий чугун со структурой графит + перлит. Излом такого чугуна светлый.
Для ускорения отжига белого чугуна на ковкий принимают различные меры: чугун модифицируют алюминием (реже бором или висмутом), повышают температуру нагрева перед разливкой, проводят перед отжигом закалку, повышают температуру первой стадии графитизации (до 1080 °С) и т. д.
Маркируют ковкие чугуны буквами КЧ — ковкий чугун и цифрами. Первые цифры обозначают предел прочности при растяжении, вторые — относительное удлинение (%). Например: КЧ45-6; στ=450 МПа, =6 %.
Из ковкого чугуна изготовляют картер заднего моста, чашки дифференциала, тормозные колодки, ступицы колес для автомобилей и др.
Чугуны со специальными свойствами используются в тех случаях, когда отливка кроме прочности должна обладать специфическими свойствами (износостойкостью, коррозионной стойкостью, жаростойкостью и т. д.).
После термической обработки углеродистой стали получена структура: цементит + мартенсит отпуска. Нанесите на диаграмму состояния железо-цементит ординату заданной стали (примерно) и укажите температуру нагрева этой стали под закалку. Назначьте температуру отпуска, обеспечивающую получение указанной структуры и опишите все превращения, которые совершились в стали в процессе закалки и отпуска.
Структура цементит + мартенсит отпуска получается после закалки и низкого отпуска заэвтектоидной углеродистой стали. Рассмотрим на примере стали У12.
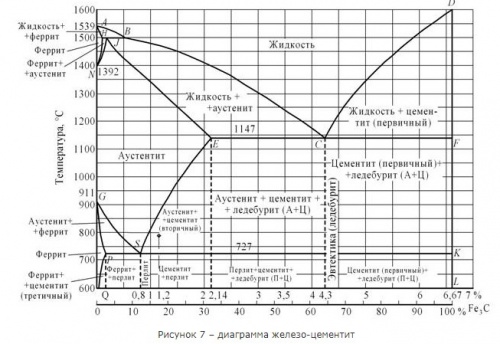
Диаграмма состояния железо-цементит представлена выше. При комнатной температуре сталь У12 имеет структуру цементита и перлита. До температуры Аc1 сохраняется исходная структура. При температуре Аc1 происходит превращение перлита в аустенит с содержанием углерода 0,8%. При нагреве выше точки Ас1 происходит растворение цементита в аустените (в соответствии с линией SE). Увеличение температуры выше точки Асm вызывает рост зерна аустенита.
Критические точки для стали У12: Аc1 = 730°С; Аcm = 820°С.
Для закалки заэвтектоидные стали нагревают на 50-70°С выше точки Ас1. Таким образом, температура нагрева под закалку составляет 780-800°С. При этих температурах в стали наряду с аустенитом имеется цементит. Поэтому после закалки в структуре заэвтектоидных сталей будет мартенсит с цементитом и небольшое количество остаточного аустенита.
Для снятия напряжений и стабилизации структуры после закалки изделия подвергают низкому отпуску при температуре 160–180 °С. Структура стали после низкого отпуска – отпущенный мартенсит + карбиды.
0 комментариев