Контрольная работа 1 Вариант 43
Что такое твердый раствор внедрения? Приведите пример.
Твердыми растворами называют фазы, в которых один из компонентов сплава сохраняет свою кристаллическую решетку, а атомы других (или другого) компонентов располагаются в решетке первого компонента (растворителя), изменяя ее размеры (периоды). Таким образом, твердый раствор, состоящий из двух или нескольких компонентов, имеет один тип решетки и представляет собой одну фазу.
Существуют твердые растворы внедрения и твердые растворы замещения. При образовании твердых растворов внедрения атомы растворенного компонента B размещаются между атомами растворителя A в его кристаллической решетке.
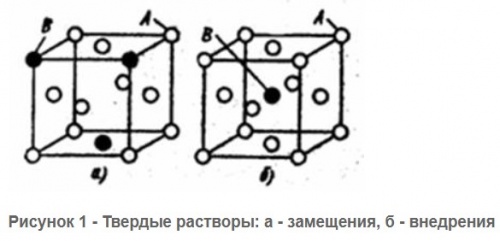
Твердые растворы внедрения могут быть только с ограниченной концентрации, поскольку число пор в решетке ограничено, а атомы основного компонента сохраняются в узлах решетки.
Твердые растворы внедрения: при растворении в металлах неметаллических элементов, как углерод, бор, азот и кислород. Например: Fe и С.
Какие основные характеристики механических свойств определяются при испытании на растяжении? Опишите их.
При испытании на растяжении определяются характеристики прочности и пластичности.
Прочность – свойство материалов в определенных условиях и пределах, не разрушаясь, воспринимать те или иные воздействия.
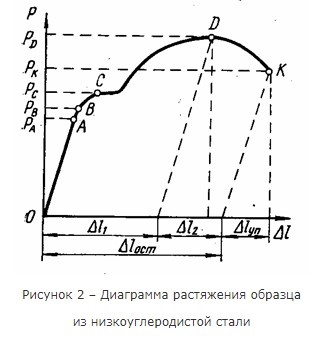
Механические свойства стали (в т. ч. и прочность) обычно определяют по условной диаграмме растяжения. ГОСТ 1497-84 регламентирует следующие прочностные свойства:
– временное сопротивление разрыву (или предел прочности при растяжении) σВ – условное напряжение, соответствующее наибольшей нагрузке PD, предшествующей разрушению образца: σB = PD/F0 кгс/мм2;
– предел текучести σТ (физический) – наименьшее условное напряжение, при котором образец деформируется без заметного увеличения растягивающей нагрузки: σT=PC/F0 кгс/мм2; его определяют для низкоуглеродистой отожженной стали;
– предел текучести σ0,2 (условный) – напряжение, при котором остаточная деформация составляет 0,2% первоначальной расчетной длины; его определяют для большинства марок конструкционной среднеуглеродистой и легированной стали, у которых на диаграмме растяжения отсутствует «площадка текучести». Для определения условного предела текучести от начала координат диаграммы растяжения по оси абсцисс откладывают в соответствующем масштабе отрезок, составляющий 0,2% первоначальной длины; через полученную точку проводят прямую, параллельную начальному линейному участку (ОА) диаграммы (до пересечения с диаграммой). Ордината точки пересечения и соответствует условному пределу текучести σ0,2. Предел текучести σ0,2 можно определить по формуле σ0,2 = P0,2/F0 кгс/мм2;
Пластичность – свойство твердых тел необратимо деформироваться под действием механических нагрузок. Отсутствие или небольшое значение пластичности называется хрупкостью.
Относительное удлинение δ представляет собой отношение приращения длины образца после его разрыва к первоначальной расчетной длине l0 и выражается в процентах:
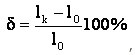
где lк – длина образца после разрыва
Под относительным сужением понимают отношение уменьшения поперечного сечения разорванного образца к первоначальной площади поперечного сечения, выраженное в процентах:
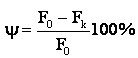
где Fк – площадь поперечного сечения в месте разрыва.
Вычертите диаграмму состояния железо-карбид железа, укажите структурные составляющие во всех областях диаграммы, опишите превращения и постройте кривую охлаждения (с применением правила фаз) для сплава, содержащего 3,4% С. Какова структура этого сплава при комнатной температуре и как такой сплав называется?
Первичная кристаллизация сплавов системы железо-углерод начинается по достижении температур, соответствующих линии ABCD (линии ликвидус), и заканчивается при температурах, образующих линию AHJECF (линию солидус).
При кристаллизации сплавов по линии АВ из жидкого раствора выделяются кристаллы твердого раствора углерода в α-железе (δ-раствор). Процесс кристаллизации сплавов с содержанием углерода до 0,1 % заканчивается по линии АН с образованием α (δ)-твердого раствора. На линии HJB протекает перитектическое превращение, в результате которого образуется твердый раствор углерода в γ-железе, т. е. аустенит. Процесс первичной кристаллизации сталей заканчивается по линии AHJE.
При температурах, соответствующих линии ВС, из жидкого раствора кристаллизуется аустенит. В сплавах, содержащих от 4,3 % до 6,67 % углерода, при температурах, соответствующих линии CD, начинают выделяться кристаллы цементита первичного. Цементит, кристаллизующийся из жидкой фазы, называется первичным. B точке С при температуре 1147°С и концентрации углерода в жидком растворе 4,3 % образуется эвтектика, которая называется ледебуритом. Эвтектическое превращение с образованием ледебурита можно записать формулой ЖР4,3Л[А2,14+Ц6,67]. Процесс первичной кристаллизации чугунов заканчивается по линии ECF образованием ледебурита.
Таким образом, структура чугунов ниже 1147°С будет: доэвтектических — аустенит + ледебурит, эвтектических — ледебурит и заэвтектических — цементит (первичный) + ледебурит.
Превращения, происходящие в твердом состоянии, называются вторичной кристаллизацией. Они связаны с переходом при охлаждении γ-железа в α-железо и распадом аустенита.
Линия GS соответствует температурам начала превращения аустенита в феррит. Ниже линии GS сплавы состоят из феррита и аустенита.
Линия ЕS показывает температуры начала выдел пня цементита из аустенита вследствие уменьшения растворимости углерода в аустените с понижением температуры. Цементит, выделяющийся из аустенита, называется вторичным цементитом.
В точке S при температуре 727°С и концентрации углерода в аустените 0,8 % образуется эвтектоидная смесь состоящая из феррита и цементита, которая называется перлитом. Перлит получается в результате одновременного выпадения из аустенита частиц феррита и цементита. Процесс превращения аустенита в перлит можно записать формулой А0,8П[Ф0,03+Ц6,67].
Линия PQ показывает на уменьшение растворимости углерода в феррите при охлаждении и выделении цементита, который называется третичным цементитом.
Следовательно, сплавы, содержащие менее 0,008% углерода (точкаQ), являются однофазными и имеют структуру чистого феррита, а сплавы, содержащие углерод от 0,008 до 0,03% – структуру феррит + цементит третичный и называются техническим железом.
Доэвтектоидные стали при температуре ниже 727ºС имеют структуру феррит + перлит и заэвтектоидные – перлит + цементит вторичный в виде сетки по границам зерен.
В доэвтектических чугунах в интервале температур 1147–727ºС при охлаждении из аустенита выделяется цементит вторичный, вследствие уменьшения растворимости углерода (линия ES). По достижении температуры 727ºС (линия PSK) аустенит, обедненный углеродом до 0,8% (точка S), превращаясь в перлит. Таким образом, после окончательного охлаждения структура доэвтектических чугунов состоит из перлита, цементита вторичного и ледебурита превращенного (перлит + цементит).
Структура эвтектических чугунов при температурах ниже 727ºС состоит из ледебурита превращенного. Заэвтектический чугун при температурах ниже 727ºС состоит из ледебурита превращенного и цементита первичного.
Сплав железа с углеродом, содержащий 3,4%С, называется доэвтектическим чугуном. Его структура при комнатной температуре цементит (вторичный) + перлит + ледебурит (перлит + цементит).
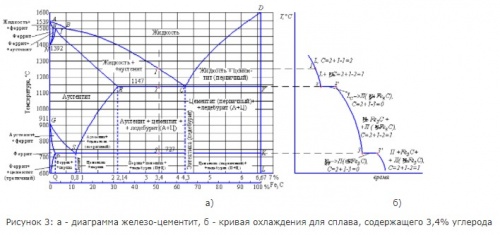
Вычертите диаграмму изотермического превращения аустенита для стали У8. Нанесите на нее кривую режима изотермической обработки, обеспечивающей получение твердости 250 HB. Укажите, как этот режим называется, какая структура получается в этом случае.
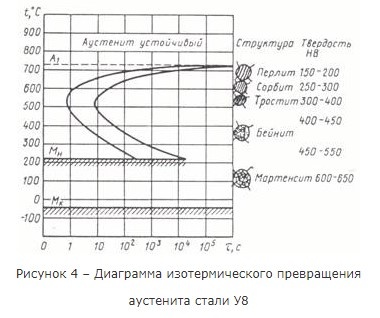
Изотермической обработкой, необходимой для получения твердости HB 250, является изотермический отжиг. При изотермическом отжиге сталь У8 нагревают до температуры на 30-50°С выше точки Ас1 и после выдержки охлаждают до температуры несколько ниже точки Аr1. При этой температуре сталь подвергают изотермической выдержке до полного превращения аустенита, затем охлаждают до комнатной температуры. Для получения структуры пластинчатого перлита заданной твердости (HB 250) устанавливается температура изотермической выдержки 640-660°С.
Чем ниже температура распада аустенита, тем дисперснее продукты распада аустенита и тем выше получаемая твердость.
Изотермический отжиг по сравнению с обычным отжигом имеет два преимущества. Прежде всего, он может дать выигрыш во времени, если суммарное время ускоренного охлаждения, изотермической выдержки и последующего ускоренного охлаждения меньше времени медленного непрерывного охлаждения изделия вместе с печью. Другое преимущество изотермического отжига – получение более однородной структуры, т.к. при изотермической выдержке температура по сечению изделия выравнивается и превращение во всем объеме стали происходит при одинаковой степени переохлаждения. Структура стали У8 после изотермического отжига – перлит.
Сталь 40 подвергалась закалке от температур 750 и 830°С. Используя диаграмму состояния железо-цементит, укажите выбранные температуры нагрева и опишите превращения, которые произошли при двух режимах закалки. Какому режиму следует отдать предпочтение и почему?
Закалка доэвтектоидной стали заключается в нагреве стали до температуры выше критической (Ас3), в выдержке и последующем охлаждении со скоростью, превышающей критическую.
Температура точки Ас3 для стали 40 составляет 790°С.
Если доэвтектоидную сталь нагреть выше Ас1, но ниже Ас3, то в ее структуре после закалки наряду с мартенситом будут участки феррита. Присутствие феррита как мягкой составляющей снижает твердость стали после закалки. При нагреве до температуры 750°С (ниже точки Ас3) структура стали 40 – аустенит + феррит, после охлаждения со скоростью выше критической структура стали – мартенсит + феррит.
Доэвтектоидные стали для закалки следует нагревать до температуры на 30-50°С выше Ас3. Температура нагрева стали под закалку, таким образом, составляет 820-840°С. Структура стали 40 при температуре нагрева под закалку – аустенит, после охлаждения со скоростью выше критической – мартенсит.
Таким образом, более высокие эксплуатационные свойства будет иметь деталь, закаленная от температуры 830°С.
Твердыми растворами называют фазы, в которых один из компонентов сплава сохраняет свою кристаллическую решетку, а атомы других (или другого) компонентов располагаются в решетке первого компонента (растворителя), изменяя ее размеры (периоды). Таким образом, твердый раствор, состоящий из двух или нескольких компонентов, имеет один тип решетки и представляет собой одну фазу.
Существуют твердые растворы внедрения и твердые растворы замещения. При образовании твердых растворов внедрения атомы растворенного компонента B размещаются между атомами растворителя A в его кристаллической решетке.
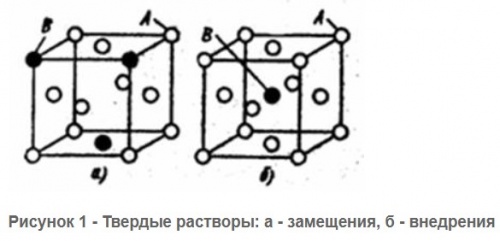
Твердые растворы внедрения могут быть только с ограниченной концентрации, поскольку число пор в решетке ограничено, а атомы основного компонента сохраняются в узлах решетки.
Твердые растворы внедрения: при растворении в металлах неметаллических элементов, как углерод, бор, азот и кислород. Например: Fe и С.
Какие основные характеристики механических свойств определяются при испытании на растяжении? Опишите их.
При испытании на растяжении определяются характеристики прочности и пластичности.
Прочность – свойство материалов в определенных условиях и пределах, не разрушаясь, воспринимать те или иные воздействия.
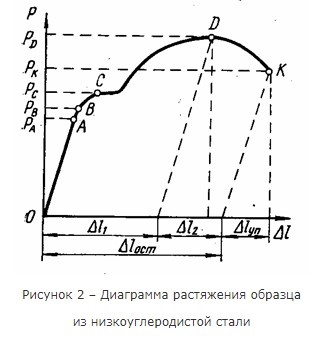
Механические свойства стали (в т. ч. и прочность) обычно определяют по условной диаграмме растяжения. ГОСТ 1497-84 регламентирует следующие прочностные свойства:
– временное сопротивление разрыву (или предел прочности при растяжении) σВ – условное напряжение, соответствующее наибольшей нагрузке PD, предшествующей разрушению образца: σB = PD/F0 кгс/мм2;
– предел текучести σТ (физический) – наименьшее условное напряжение, при котором образец деформируется без заметного увеличения растягивающей нагрузки: σT=PC/F0 кгс/мм2; его определяют для низкоуглеродистой отожженной стали;
– предел текучести σ0,2 (условный) – напряжение, при котором остаточная деформация составляет 0,2% первоначальной расчетной длины; его определяют для большинства марок конструкционной среднеуглеродистой и легированной стали, у которых на диаграмме растяжения отсутствует «площадка текучести». Для определения условного предела текучести от начала координат диаграммы растяжения по оси абсцисс откладывают в соответствующем масштабе отрезок, составляющий 0,2% первоначальной длины; через полученную точку проводят прямую, параллельную начальному линейному участку (ОА) диаграммы (до пересечения с диаграммой). Ордината точки пересечения и соответствует условному пределу текучести σ0,2. Предел текучести σ0,2 можно определить по формуле σ0,2 = P0,2/F0 кгс/мм2;
Пластичность – свойство твердых тел необратимо деформироваться под действием механических нагрузок. Отсутствие или небольшое значение пластичности называется хрупкостью.
Относительное удлинение δ представляет собой отношение приращения длины образца после его разрыва к первоначальной расчетной длине l0 и выражается в процентах:
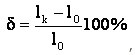
где lк – длина образца после разрыва
Под относительным сужением понимают отношение уменьшения поперечного сечения разорванного образца к первоначальной площади поперечного сечения, выраженное в процентах:
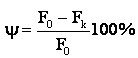
где Fк – площадь поперечного сечения в месте разрыва.
Вычертите диаграмму состояния железо-карбид железа, укажите структурные составляющие во всех областях диаграммы, опишите превращения и постройте кривую охлаждения (с применением правила фаз) для сплава, содержащего 3,4% С. Какова структура этого сплава при комнатной температуре и как такой сплав называется?
Первичная кристаллизация сплавов системы железо-углерод начинается по достижении температур, соответствующих линии ABCD (линии ликвидус), и заканчивается при температурах, образующих линию AHJECF (линию солидус).
При кристаллизации сплавов по линии АВ из жидкого раствора выделяются кристаллы твердого раствора углерода в α-железе (δ-раствор). Процесс кристаллизации сплавов с содержанием углерода до 0,1 % заканчивается по линии АН с образованием α (δ)-твердого раствора. На линии HJB протекает перитектическое превращение, в результате которого образуется твердый раствор углерода в γ-железе, т. е. аустенит. Процесс первичной кристаллизации сталей заканчивается по линии AHJE.
При температурах, соответствующих линии ВС, из жидкого раствора кристаллизуется аустенит. В сплавах, содержащих от 4,3 % до 6,67 % углерода, при температурах, соответствующих линии CD, начинают выделяться кристаллы цементита первичного. Цементит, кристаллизующийся из жидкой фазы, называется первичным. B точке С при температуре 1147°С и концентрации углерода в жидком растворе 4,3 % образуется эвтектика, которая называется ледебуритом. Эвтектическое превращение с образованием ледебурита можно записать формулой ЖР4,3Л[А2,14+Ц6,67]. Процесс первичной кристаллизации чугунов заканчивается по линии ECF образованием ледебурита.
Таким образом, структура чугунов ниже 1147°С будет: доэвтектических — аустенит + ледебурит, эвтектических — ледебурит и заэвтектических — цементит (первичный) + ледебурит.
Превращения, происходящие в твердом состоянии, называются вторичной кристаллизацией. Они связаны с переходом при охлаждении γ-железа в α-железо и распадом аустенита.
Линия GS соответствует температурам начала превращения аустенита в феррит. Ниже линии GS сплавы состоят из феррита и аустенита.
Линия ЕS показывает температуры начала выдел пня цементита из аустенита вследствие уменьшения растворимости углерода в аустените с понижением температуры. Цементит, выделяющийся из аустенита, называется вторичным цементитом.
В точке S при температуре 727°С и концентрации углерода в аустените 0,8 % образуется эвтектоидная смесь состоящая из феррита и цементита, которая называется перлитом. Перлит получается в результате одновременного выпадения из аустенита частиц феррита и цементита. Процесс превращения аустенита в перлит можно записать формулой А0,8П[Ф0,03+Ц6,67].
Линия PQ показывает на уменьшение растворимости углерода в феррите при охлаждении и выделении цементита, который называется третичным цементитом.
Следовательно, сплавы, содержащие менее 0,008% углерода (точкаQ), являются однофазными и имеют структуру чистого феррита, а сплавы, содержащие углерод от 0,008 до 0,03% – структуру феррит + цементит третичный и называются техническим железом.
Доэвтектоидные стали при температуре ниже 727ºС имеют структуру феррит + перлит и заэвтектоидные – перлит + цементит вторичный в виде сетки по границам зерен.
В доэвтектических чугунах в интервале температур 1147–727ºС при охлаждении из аустенита выделяется цементит вторичный, вследствие уменьшения растворимости углерода (линия ES). По достижении температуры 727ºС (линия PSK) аустенит, обедненный углеродом до 0,8% (точка S), превращаясь в перлит. Таким образом, после окончательного охлаждения структура доэвтектических чугунов состоит из перлита, цементита вторичного и ледебурита превращенного (перлит + цементит).
Структура эвтектических чугунов при температурах ниже 727ºС состоит из ледебурита превращенного. Заэвтектический чугун при температурах ниже 727ºС состоит из ледебурита превращенного и цементита первичного.
Сплав железа с углеродом, содержащий 3,4%С, называется доэвтектическим чугуном. Его структура при комнатной температуре цементит (вторичный) + перлит + ледебурит (перлит + цементит).
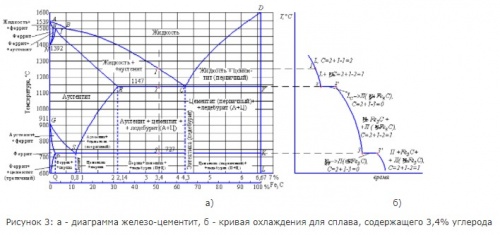
Вычертите диаграмму изотермического превращения аустенита для стали У8. Нанесите на нее кривую режима изотермической обработки, обеспечивающей получение твердости 250 HB. Укажите, как этот режим называется, какая структура получается в этом случае.
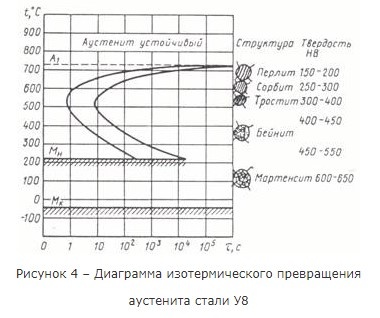
Изотермической обработкой, необходимой для получения твердости HB 250, является изотермический отжиг. При изотермическом отжиге сталь У8 нагревают до температуры на 30-50°С выше точки Ас1 и после выдержки охлаждают до температуры несколько ниже точки Аr1. При этой температуре сталь подвергают изотермической выдержке до полного превращения аустенита, затем охлаждают до комнатной температуры. Для получения структуры пластинчатого перлита заданной твердости (HB 250) устанавливается температура изотермической выдержки 640-660°С.
Чем ниже температура распада аустенита, тем дисперснее продукты распада аустенита и тем выше получаемая твердость.
Изотермический отжиг по сравнению с обычным отжигом имеет два преимущества. Прежде всего, он может дать выигрыш во времени, если суммарное время ускоренного охлаждения, изотермической выдержки и последующего ускоренного охлаждения меньше времени медленного непрерывного охлаждения изделия вместе с печью. Другое преимущество изотермического отжига – получение более однородной структуры, т.к. при изотермической выдержке температура по сечению изделия выравнивается и превращение во всем объеме стали происходит при одинаковой степени переохлаждения. Структура стали У8 после изотермического отжига – перлит.
Сталь 40 подвергалась закалке от температур 750 и 830°С. Используя диаграмму состояния железо-цементит, укажите выбранные температуры нагрева и опишите превращения, которые произошли при двух режимах закалки. Какому режиму следует отдать предпочтение и почему?
Закалка доэвтектоидной стали заключается в нагреве стали до температуры выше критической (Ас3), в выдержке и последующем охлаждении со скоростью, превышающей критическую.
Температура точки Ас3 для стали 40 составляет 790°С.
Если доэвтектоидную сталь нагреть выше Ас1, но ниже Ас3, то в ее структуре после закалки наряду с мартенситом будут участки феррита. Присутствие феррита как мягкой составляющей снижает твердость стали после закалки. При нагреве до температуры 750°С (ниже точки Ас3) структура стали 40 – аустенит + феррит, после охлаждения со скоростью выше критической структура стали – мартенсит + феррит.
Доэвтектоидные стали для закалки следует нагревать до температуры на 30-50°С выше Ас3. Температура нагрева стали под закалку, таким образом, составляет 820-840°С. Структура стали 40 при температуре нагрева под закалку – аустенит, после охлаждения со скоростью выше критической – мартенсит.
Таким образом, более высокие эксплуатационные свойства будет иметь деталь, закаленная от температуры 830°С.
0 комментариев