Контрольная работа 1 Вариант 44
Что такое ликвация? Причины ее возникновения и способы устранения.
Ликвация (от лат. liquatio – разжижение, плавление) – неоднородность химического состава сплавов, возникающая при их кристаллизации. Особое значение имеет ликвация в стали, впервые обнаруженная русскими металлургами Н. В. Калакуцким и А. С. Лавровым в 1866.
Ликвация возникает в результате того, что сплавы, в отличие от чистых металлов, кристаллизуются не при одной температуре, а в интервале температур. При этом состав кристаллов, образующихся в начале затвердевания, может существенно отличаться от состава последних порций кристаллизующегося маточного раствора. Чем шире температурный интервал кристаллизации сплава, тем большее развитие получает ликвация, причём наибольшую склонность к ней проявляют те компоненты сплава, которые наиболее сильно влияют на ширину интервала кристаллизации (для стали, например, сера, кислород, фосфор, углерод). Ликвация оказывает, как правило, вредное влияние на качество металла, т. к. приводит к неравномерности его свойств.
Различают дендритную ликвацию, которая проявляется в микрообъёмах сплава, близких к размеру зёрен, и зональную ликвацию, наблюдаемую во всём объёме слитка. Дендритная ликвация выражается в том, что оси дендритных кристаллов отличаются по химическому составу от межосных пространств. Этот вид ликвации может быть в значительной степени устранён при длительном отжиге металла (так называемая гомогенизация) в результате диффузии примесей. Зональная ликвация выражается в наличии в слитке нескольких зон с различным химическим составом, которые в зависимости от характера отклонений от среднего состава сплава называются зонами положительной или отрицательной ликвации. Различают осевую и внеосевую ликвацию. Для уменьшения зональной ликвации ограничивают размеры слитков, а также применяют специальные металлургические процессы: непрерывную разливку, переплав в водоохлаждаемом кристаллизаторе (электрошлаковый или вакуумный) и т. п.
Сохраняется ли наклеп металла, если пластическая деформация осуществляется при температуре выше температуры рекристаллизации? Дайте подробное объяснение.
Наклеп – изменение структуры и свойств металлического материала, вызванное пластической деформацией. Наклеп снижает пластичность и ударную вязкость, но увеличивает предел пропорциональности, предел текучести и твердость.
Пластическую деформацию, осуществляемую при температуре выше температуры рекристаллизации, если ее проводят для получения полностью рекристаллизованной структуры, называют горячей.
При этих температурах деформация также вызывает упрочнение «горячий наклеп», которое полностью или частично снимается рекристаллизацией, протекающей при температурах обработки и при последующем охлаждении. В отличие от статической полигонизации и рекристаллизации, процессы полигонизации и рекристаллизации, происходящие в период деформации, называют динамическими.
При горячей обработке давлением (прокатке, прессовании, ковке, штамповке и т. д.) упрочнение в результате наклепа (повышение плотности дислокаций) непосредственно в процессе деформации непрерывно чередуется с процессом разупрочнения (уменьшением плотности дислокаций) при динамической полигонизации и рекристаллизации во время деформации и охлаждения.
Горячую деформацию в зависимости от состава сплава и скорости деформации обычно проводят при температурах (0,7-0,75) Тпл.
Вычертите диаграмму состояния железо – карбид железа, укажите структурные составляющие во всех областях диаграммы, опишите превращения и постройте кривую охлаждения (с применением правила фаз) для сплава, содержащего 5,2% С. Какова структура этого сплава при комнатной температуре и как такой сплав называется?
Первичная кристаллизация сплавов системы железо-углерод начинается по достижении температур, соответствующих линии ABCD (линии ликвидус), и заканчивается при температурах, образующих линию AHJECF (линию солидус).
При кристаллизации сплавов по линии АВ из жидкого раствора выделяются кристаллы твердого раствора углерода в α-железе (δ-раствор). Процесс кристаллизации сплавов с содержанием углерода до 0,1 % заканчивается по линии АН с образованием α (δ)-твердого раствора. На линии HJB протекает перитектическое превращение, в результате которого образуется твердый раствор углерода в γ-железе, т. е. аустенит. Процесс первичной кристаллизации сталей заканчивается по линии AHJE.
При температурах, соответствующих линии ВС, из жидкого раствора кристаллизуется аустенит. В сплавах, содержащих от 4,3 % до 6,67 % углерода, при температурах, соответствующих линии CD, начинают выделяться кристаллы цементита первичного. Цементит, кристаллизующийся из жидкой фазы, называется первичным. B точке С при температуре 1147°С и концентрации углерода в жидком растворе 4,3 % образуется эвтектика, которая называется ледебуритом. Эвтектическое превращение с образованием ледебурита можно записать формулой ЖР4,3Л[А2,14+Ц6,67]. Процесс первичной кристаллизации чугунов заканчивается по линии ECF образованием ледебурита.
Таким образом, структура чугунов ниже 1147°С будет: доэвтектических – аустенит+ледебурит, эвтектических – ледебурит и заэвтектических – цементит (первичный)+ледебурит.
Превращения, происходящие в твердом состоянии, называются вторичной кристаллизацией. Они связаны с переходом при охлаждении γ-железа в α-железо и распадом аустенита.
Линия GS соответствует температурам начала превращения аустенита в феррит. Ниже линии GS сплавы состоят из феррита и аустенита.
Линия ЕS показывает температуры начала выделения цементита из аустенита вследствие уменьшения растворимости углерода в аустените с понижением температуры. Цементит, выделяющийся из аустенита, называется вторичным цементитом.
В точке S при температуре 727°С и концентрации углерода в аустените 0,8 % образуется эвтектоидная смесь состоящая из феррита и цементита, которая называется перлитом. Перлит получается в результате одновременного выпадения из аустенита частиц феррита и цементита. Процесс превращения аустенита в перлит можно записать формулой А0,8П[Ф0,03+Ц6,67].
Линия PQ показывает на уменьшение растворимости углерода в феррите при охлаждении и выделении цементита, который называется третичным цементитом.
Следовательно, сплавы, содержащие менее 0,008% углерода (точкаQ), являются однофазными и имеют структуру чистого феррита, а сплавы, содержащие углерод от 0,008 до 0,03% – структуру феррит+цементит третичный и называются техническим железом.
Доэвтектоидные стали при температуре ниже 727ºС имеют структуру феррит+перлит и заэвтектоидные – перлит+цементит вторичный в виде сетки по границам зерен.
В доэвтектических чугунах в интервале температур 1147–727ºС при охлаждении из аустенита выделяется цементит вторичный, вследствие уменьшения растворимости углерода(линия ES). По достижении температуры 727ºС (линия PSK) аустенит, обедненный углеродом до 0,8% (точка S), превращаясь в перлит. Таким образом, после окончательного охлаждения структура доэвтектических чугунов состоит из перлита, цементита вторичного и ледебурита превращенного (перлит+цементит).
Структура эвтектических чугунов при температурах ниже 727ºС состоит из ледебурита превращенного. Заэвтектический чугун при температурах ниже 727ºС состоит из ледебурита превращенного и цементита первичного.
Правило фаз устанавливает зависимость между числом степеней свободы, числом компонентов и числом фаз и выражается уравнением:
C = K + 1 – Ф,
где С – число степеней свободы системы;
К – число компонентов, образующих систему;
1 – число внешних факторов (внешним фактором считаем только температуру, так как давление за исключением очень высокого мало влияет на фазовое равновесие сплавов в твердом и жидком состояниях);
Ф – число фаз, находящихся в равновесии.
Сплав железа с углеродом, содержащий 5,2%С, называется заэвтектическим чугуном. Его структура при комнатной температуре – цементит (первичный) + ледебурит.
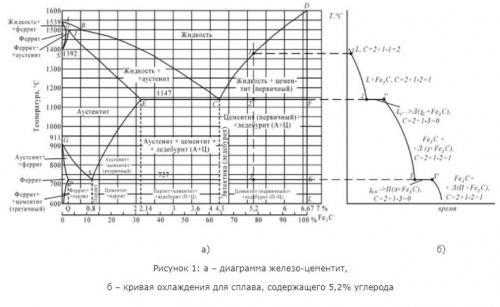
Используя диаграмму состояния железо – карбид железа и кривую изменения твердости в зависимости от температуры отпуска, назначьте для углеродистой стали 40 температуру закалки и температуру отпуска, необходимые для обеспечения твердости 450 НВ. Опишите превращения, которые совершались в стали в процессе закалки и отпуска, и полученную после термической обработки структуру.
Закалка доэвтектоидной стали заключается в нагреве стали до температуры выше критической (Ас3), в выдержке и последующем охлаждении со скоростью, превышающей критическую.
Температура точки Ас3 для стали 40 составляет 790°С, а Ас1 равна 730°С. Структура доэвтектоидной стали при нагреве её до критической точки Ас1 состоит из зерен перлита и феррита. В точке Ас1 происходит превращение перлита в мелкозернистый аустенит. При дальнейшем нагреве от точки Ас1 до Ас3 избыточный феррит растворяется в аустените и при достижении Ас3 (линия GS) превращения заканчиваются.
Доэвтектоидные стали для закалки следует нагревать до температуры на 30-50°С выше Ас3. Температура нагрева стали под закалку, таким образом, составляет 820-840°С. Структура стали 40 при температуре нагрева под закалку – аустенит, после охлаждения со скоростью выше критической – мартенсит.
В зависимости от температуры отпуска меняется твердость закаленной стали. Например, при 600°С твердость НВ не более 200 ед., при 400°С – не более 280 ед., а при 200°С – не более 450 ед.
Поэтому для получения твердости 450 НВ закаленную сталь подвергают низкому отпуску при температуре 180-200°С. Низкий отпуск, незначительно снижая твердость поверхностно-закаленного изделия, существенно повышает сопротивление стали хрупкому разрушению. Структура стали после низкого отпуска на глубину прокаливания – мартенсит отпуска.
В результате термической обработки твердость изделия на глубину прокаливания составит 450 НВ.
Метчики из стали У10 закалены: первый – от 760°С, а второй – от температуры 850°С. Нанесите на диаграмму состояния железо – цементит выбранные температуры нагрева и объясните, какой из этих метчиков закален правильно, имеет более высокие режущие свойства и почему.
Диаграмма состояния железо-цементит представлена на рисунке 1. При комнатной температуре сталь У10 имеет структуру цементита и перлита. До температуры Аc1 сохраняется исходная структура. При температуре Аc1 происходит превращение перлита в аустенит с содержанием углерода 0,8%. При нагреве выше точки Ас1 происходит растворение цементита в аустените (в соответствии с линией SE). Увеличение температуры выше точки Асm вызывает рост зерна аустенита.
Критические точки для стали У10: Аc1 = 730°С; Аcm = 800°С.
При нагреве до 700ºС в стали У10 не происходят аллотропические превращения и мы имеем ту же структуру – перлит + карбиды, быстро охлаждая (т.к. закалка), имеем также после охлаждения перлит + карбиды с теми же механическими свойствами (примерно), что и в исходном состоянии до нагрева под закалку.
Для закалки заэвтектоидные стали нагревают на 50-70°С выше точки Ас1. Таким образом, температура нагрева под закалку составляет 780-800°С. При этих температурах в стали наряду с аустенитом имеется цементит. Поэтому после закалки в структуре заэвтектоидных сталей будет мартенсит с цементитом и небольшое количество остаточного аустенита. Охлаждающая среда при закалке – индустриальное масло. Твердость поверхности после закалки 62-64 HRC. Для снятия напряжений и стабилизации структуры после закалки изделия подвергают низкому отпуску.
Нагрев и выдержка стали У10 при температуре 850ºС перед закалкой приводит к росту зерна и ухудшению механических свойств стали после термической обработки. Крупнозернистая структура вызывает повышенную хрупкость стали, иногда приводит к трещинам.
Таким образом, более высокие режущие свойства (твердость и износостойкость) достигаются при закалке стали от 780-800°С.
Ликвация (от лат. liquatio – разжижение, плавление) – неоднородность химического состава сплавов, возникающая при их кристаллизации. Особое значение имеет ликвация в стали, впервые обнаруженная русскими металлургами Н. В. Калакуцким и А. С. Лавровым в 1866.
Ликвация возникает в результате того, что сплавы, в отличие от чистых металлов, кристаллизуются не при одной температуре, а в интервале температур. При этом состав кристаллов, образующихся в начале затвердевания, может существенно отличаться от состава последних порций кристаллизующегося маточного раствора. Чем шире температурный интервал кристаллизации сплава, тем большее развитие получает ликвация, причём наибольшую склонность к ней проявляют те компоненты сплава, которые наиболее сильно влияют на ширину интервала кристаллизации (для стали, например, сера, кислород, фосфор, углерод). Ликвация оказывает, как правило, вредное влияние на качество металла, т. к. приводит к неравномерности его свойств.
Различают дендритную ликвацию, которая проявляется в микрообъёмах сплава, близких к размеру зёрен, и зональную ликвацию, наблюдаемую во всём объёме слитка. Дендритная ликвация выражается в том, что оси дендритных кристаллов отличаются по химическому составу от межосных пространств. Этот вид ликвации может быть в значительной степени устранён при длительном отжиге металла (так называемая гомогенизация) в результате диффузии примесей. Зональная ликвация выражается в наличии в слитке нескольких зон с различным химическим составом, которые в зависимости от характера отклонений от среднего состава сплава называются зонами положительной или отрицательной ликвации. Различают осевую и внеосевую ликвацию. Для уменьшения зональной ликвации ограничивают размеры слитков, а также применяют специальные металлургические процессы: непрерывную разливку, переплав в водоохлаждаемом кристаллизаторе (электрошлаковый или вакуумный) и т. п.
Сохраняется ли наклеп металла, если пластическая деформация осуществляется при температуре выше температуры рекристаллизации? Дайте подробное объяснение.
Наклеп – изменение структуры и свойств металлического материала, вызванное пластической деформацией. Наклеп снижает пластичность и ударную вязкость, но увеличивает предел пропорциональности, предел текучести и твердость.
Пластическую деформацию, осуществляемую при температуре выше температуры рекристаллизации, если ее проводят для получения полностью рекристаллизованной структуры, называют горячей.
При этих температурах деформация также вызывает упрочнение «горячий наклеп», которое полностью или частично снимается рекристаллизацией, протекающей при температурах обработки и при последующем охлаждении. В отличие от статической полигонизации и рекристаллизации, процессы полигонизации и рекристаллизации, происходящие в период деформации, называют динамическими.
При горячей обработке давлением (прокатке, прессовании, ковке, штамповке и т. д.) упрочнение в результате наклепа (повышение плотности дислокаций) непосредственно в процессе деформации непрерывно чередуется с процессом разупрочнения (уменьшением плотности дислокаций) при динамической полигонизации и рекристаллизации во время деформации и охлаждения.
Горячую деформацию в зависимости от состава сплава и скорости деформации обычно проводят при температурах (0,7-0,75) Тпл.
Вычертите диаграмму состояния железо – карбид железа, укажите структурные составляющие во всех областях диаграммы, опишите превращения и постройте кривую охлаждения (с применением правила фаз) для сплава, содержащего 5,2% С. Какова структура этого сплава при комнатной температуре и как такой сплав называется?
Первичная кристаллизация сплавов системы железо-углерод начинается по достижении температур, соответствующих линии ABCD (линии ликвидус), и заканчивается при температурах, образующих линию AHJECF (линию солидус).
При кристаллизации сплавов по линии АВ из жидкого раствора выделяются кристаллы твердого раствора углерода в α-железе (δ-раствор). Процесс кристаллизации сплавов с содержанием углерода до 0,1 % заканчивается по линии АН с образованием α (δ)-твердого раствора. На линии HJB протекает перитектическое превращение, в результате которого образуется твердый раствор углерода в γ-железе, т. е. аустенит. Процесс первичной кристаллизации сталей заканчивается по линии AHJE.
При температурах, соответствующих линии ВС, из жидкого раствора кристаллизуется аустенит. В сплавах, содержащих от 4,3 % до 6,67 % углерода, при температурах, соответствующих линии CD, начинают выделяться кристаллы цементита первичного. Цементит, кристаллизующийся из жидкой фазы, называется первичным. B точке С при температуре 1147°С и концентрации углерода в жидком растворе 4,3 % образуется эвтектика, которая называется ледебуритом. Эвтектическое превращение с образованием ледебурита можно записать формулой ЖР4,3Л[А2,14+Ц6,67]. Процесс первичной кристаллизации чугунов заканчивается по линии ECF образованием ледебурита.
Таким образом, структура чугунов ниже 1147°С будет: доэвтектических – аустенит+ледебурит, эвтектических – ледебурит и заэвтектических – цементит (первичный)+ледебурит.
Превращения, происходящие в твердом состоянии, называются вторичной кристаллизацией. Они связаны с переходом при охлаждении γ-железа в α-железо и распадом аустенита.
Линия GS соответствует температурам начала превращения аустенита в феррит. Ниже линии GS сплавы состоят из феррита и аустенита.
Линия ЕS показывает температуры начала выделения цементита из аустенита вследствие уменьшения растворимости углерода в аустените с понижением температуры. Цементит, выделяющийся из аустенита, называется вторичным цементитом.
В точке S при температуре 727°С и концентрации углерода в аустените 0,8 % образуется эвтектоидная смесь состоящая из феррита и цементита, которая называется перлитом. Перлит получается в результате одновременного выпадения из аустенита частиц феррита и цементита. Процесс превращения аустенита в перлит можно записать формулой А0,8П[Ф0,03+Ц6,67].
Линия PQ показывает на уменьшение растворимости углерода в феррите при охлаждении и выделении цементита, который называется третичным цементитом.
Следовательно, сплавы, содержащие менее 0,008% углерода (точкаQ), являются однофазными и имеют структуру чистого феррита, а сплавы, содержащие углерод от 0,008 до 0,03% – структуру феррит+цементит третичный и называются техническим железом.
Доэвтектоидные стали при температуре ниже 727ºС имеют структуру феррит+перлит и заэвтектоидные – перлит+цементит вторичный в виде сетки по границам зерен.
В доэвтектических чугунах в интервале температур 1147–727ºС при охлаждении из аустенита выделяется цементит вторичный, вследствие уменьшения растворимости углерода(линия ES). По достижении температуры 727ºС (линия PSK) аустенит, обедненный углеродом до 0,8% (точка S), превращаясь в перлит. Таким образом, после окончательного охлаждения структура доэвтектических чугунов состоит из перлита, цементита вторичного и ледебурита превращенного (перлит+цементит).
Структура эвтектических чугунов при температурах ниже 727ºС состоит из ледебурита превращенного. Заэвтектический чугун при температурах ниже 727ºС состоит из ледебурита превращенного и цементита первичного.
Правило фаз устанавливает зависимость между числом степеней свободы, числом компонентов и числом фаз и выражается уравнением:
C = K + 1 – Ф,
где С – число степеней свободы системы;
К – число компонентов, образующих систему;
1 – число внешних факторов (внешним фактором считаем только температуру, так как давление за исключением очень высокого мало влияет на фазовое равновесие сплавов в твердом и жидком состояниях);
Ф – число фаз, находящихся в равновесии.
Сплав железа с углеродом, содержащий 5,2%С, называется заэвтектическим чугуном. Его структура при комнатной температуре – цементит (первичный) + ледебурит.
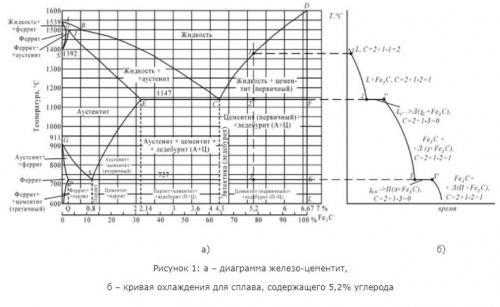
Используя диаграмму состояния железо – карбид железа и кривую изменения твердости в зависимости от температуры отпуска, назначьте для углеродистой стали 40 температуру закалки и температуру отпуска, необходимые для обеспечения твердости 450 НВ. Опишите превращения, которые совершались в стали в процессе закалки и отпуска, и полученную после термической обработки структуру.
Закалка доэвтектоидной стали заключается в нагреве стали до температуры выше критической (Ас3), в выдержке и последующем охлаждении со скоростью, превышающей критическую.
Температура точки Ас3 для стали 40 составляет 790°С, а Ас1 равна 730°С. Структура доэвтектоидной стали при нагреве её до критической точки Ас1 состоит из зерен перлита и феррита. В точке Ас1 происходит превращение перлита в мелкозернистый аустенит. При дальнейшем нагреве от точки Ас1 до Ас3 избыточный феррит растворяется в аустените и при достижении Ас3 (линия GS) превращения заканчиваются.
Доэвтектоидные стали для закалки следует нагревать до температуры на 30-50°С выше Ас3. Температура нагрева стали под закалку, таким образом, составляет 820-840°С. Структура стали 40 при температуре нагрева под закалку – аустенит, после охлаждения со скоростью выше критической – мартенсит.
В зависимости от температуры отпуска меняется твердость закаленной стали. Например, при 600°С твердость НВ не более 200 ед., при 400°С – не более 280 ед., а при 200°С – не более 450 ед.
Поэтому для получения твердости 450 НВ закаленную сталь подвергают низкому отпуску при температуре 180-200°С. Низкий отпуск, незначительно снижая твердость поверхностно-закаленного изделия, существенно повышает сопротивление стали хрупкому разрушению. Структура стали после низкого отпуска на глубину прокаливания – мартенсит отпуска.
В результате термической обработки твердость изделия на глубину прокаливания составит 450 НВ.
Метчики из стали У10 закалены: первый – от 760°С, а второй – от температуры 850°С. Нанесите на диаграмму состояния железо – цементит выбранные температуры нагрева и объясните, какой из этих метчиков закален правильно, имеет более высокие режущие свойства и почему.
Диаграмма состояния железо-цементит представлена на рисунке 1. При комнатной температуре сталь У10 имеет структуру цементита и перлита. До температуры Аc1 сохраняется исходная структура. При температуре Аc1 происходит превращение перлита в аустенит с содержанием углерода 0,8%. При нагреве выше точки Ас1 происходит растворение цементита в аустените (в соответствии с линией SE). Увеличение температуры выше точки Асm вызывает рост зерна аустенита.
Критические точки для стали У10: Аc1 = 730°С; Аcm = 800°С.
При нагреве до 700ºС в стали У10 не происходят аллотропические превращения и мы имеем ту же структуру – перлит + карбиды, быстро охлаждая (т.к. закалка), имеем также после охлаждения перлит + карбиды с теми же механическими свойствами (примерно), что и в исходном состоянии до нагрева под закалку.
Для закалки заэвтектоидные стали нагревают на 50-70°С выше точки Ас1. Таким образом, температура нагрева под закалку составляет 780-800°С. При этих температурах в стали наряду с аустенитом имеется цементит. Поэтому после закалки в структуре заэвтектоидных сталей будет мартенсит с цементитом и небольшое количество остаточного аустенита. Охлаждающая среда при закалке – индустриальное масло. Твердость поверхности после закалки 62-64 HRC. Для снятия напряжений и стабилизации структуры после закалки изделия подвергают низкому отпуску.
Нагрев и выдержка стали У10 при температуре 850ºС перед закалкой приводит к росту зерна и ухудшению механических свойств стали после термической обработки. Крупнозернистая структура вызывает повышенную хрупкость стали, иногда приводит к трещинам.
Таким образом, более высокие режущие свойства (твердость и износостойкость) достигаются при закалке стали от 780-800°С.
0 комментариев