Контрольная работа 1 Вариант 45
Как влияет реальная среда на процесс кристаллизации?
Кристаллы, образующиеся в процессе затвердевания металла, могут иметь различную форму в зависимости от скорости охлаждения, характера и количества примесей. Чаще в процессе кристаллизации образуются разветвленные (древовидные) кристаллы, получившие название дендритов (рисунок 1).
При образовании кристаллов их развитие идет в основном в направлении, перпендикулярном к плоскостям с максимальной плотностью упаковки атомов. Это приводит к тому, что первоначально образуются длинные ветви, так называемые оси первого порядка. Одновременно с удлинением осей первого порядка на их ребрах зарождаются и растут перпендикулярные к ним такие же ветви второго порядка. В свою очередь, на осях второго порядка зарождаются и растут оси третьего порядка и т. д. В конечном счете образуются кристаллы в форме дендритов.
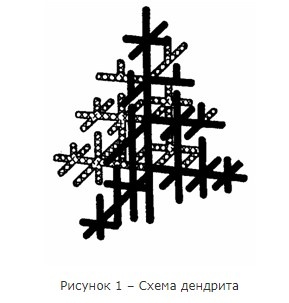
При затвердевании слитка кристаллизация начинается у поверхности более холодной формы и происходит вначале преимущественно в примыкающем к поверхности тонком слое сильно переохлажденной жидкости. Вследствие большой скорости охлаждения это приводит к образованию на поверхности слитка очень узкой зоны 1 сравнительно мелких равноосных кристаллитов (рисунок 2).
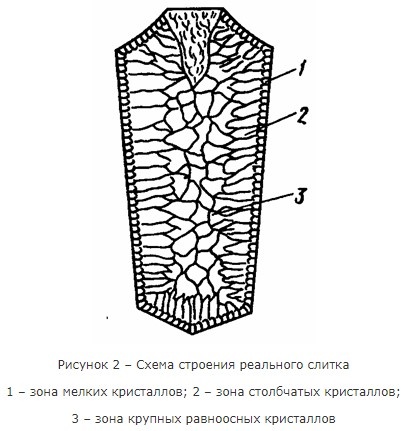
За зоной 1 в глубь слитка расположена зона 2 удлиненных дендритных кристаллитов (зона транскристаллизации). Рост этих кристаллитов происходит в направлении отвода теплоты, т. е. нормально к стенкам изложницы. Последовательный рост дендритов к стенкам изложницы происходит в результате продвижения в глубь расплава ветвей первого порядка и их разветвления аналогично тому, как это было описано выше.
В зоне дальнейшей кристаллизации направленность отвода теплоты теряется, скорость охлаждения уменьшается и поэтому в центральной части слитка образуются крупные равноосные кристаллы.
Зоны столбчатых кристаллов в процессе кристаллизации стыкуются, это явление называется транскристаллизацией. Для малопластичных металлов и для сталей это явление нежелательное, так как при последующей прокатке, ковке могут образовываться трещины в зоне стыка.
В верхней части слитка образуется усадочная раковина, которая подлежит отрезке и переплавке, так как металл более рыхлый (около 15…20 % от длины слитка).
Прутки олова были деформированы при температуре 20°С. Объясните, почему эти прутки не упрочнились при деформировании, и опишите процессы, протекающие при этом.
В зависимости от соотношения температуры деформации и температуры рекристаллизации различают холодную и горячую деформации. Холодной деформацией называют такую, которую проводят при температуре ниже температуры рекристаллизации. Поэтому холодная деформация сопровождается упрочнением (наклепом) металла.
Деформацию называют горячей, если ее проводят при температуре выше температуры рекристаллизации для получения полностью рекристаллизованной структуры.
При этих температурах деформация также вызывает упрочнение «горячий наклеп», которое полностью или частично снимается рекристаллизацией, протекающей при температурах обработки и при последующем охлаждении. В отличие от статической полигонизации и рекристаллизации, процессы полигонизации и рекристаллизации, происходящие в период деформации, называют динамическими.
По правилу А. А. Бочвара можно оценить в первом приближении температурный порог рекристаллизации по известной температуре плавления металла: Тп.р.=0,4Тп.л…
Температура начала рекристаллизации олова:
Тн.р.=(232+273)0,4-273=-71°С.
Следовательно, деформирование олова при температуре 20 °C является горячей деформацией, и упрочнение не происходит.
Вычертите диаграмму состояния железо – карбид железа, укажите структурные составляющие во всех областях диаграммы, опишите превращения и постройте кривую охлаждения (с применением правила фаз) для сплава, содержащего 0,45% С. Какова структура этого сплава при комнатной температуре и как такой сплав называется?
Первичная кристаллизация сплавов системы железо-углерод начинается по достижении температур, соответствующих линии ABCD (линии ликвидус), и заканчивается при температурах, образующих линию AHJECF (линию солидус).
При кристаллизации сплавов по линии АВ из жидкого раствора выделяются кристаллы твердого раствора углерода в α-железе (δ-раствор). Процесс кристаллизации сплавов с содержанием углерода до 0,1 % заканчивается по линии АН с образованием α (δ)-твердого раствора. На линии HJB протекает перитектическое превращение, в результате которого образуется твердый раствор углерода в γ-железе, т. е. аустенит. Процесс первичной кристаллизации сталей заканчивается по линии AHJE.
При температурах, соответствующих линии ВС, из жидкого раствора кристаллизуется аустенит. В сплавах, содержащих от 4,3% до 6,67 % углерода, при температурах, соответствующих линии CD, начинают выделяться кристаллы цементита первичного. Цементит, кристаллизующийся из жидкой фазы, называется первичным. B точке С при температуре 1147°С и концентрации углерода в жидком растворе 4,3% образуется эвтектика, которая называется ледебуритом. Эвтектическое превращение с образованием ледебурита можно записать формулой ЖР4,3Л[А2,14+Ц6,67]. Процесс первичной кристаллизации чугунов заканчивается по линии ECF образованием ледебурита.
Таким образом, структура чугунов ниже 1147°С будет: доэвтектических – аустенит + ледебурит, эвтектических – ледебурит и заэвтектических – цементит (первичный)+ледебурит.
Превращения, происходящие в твердом состоянии, называются вторичной кристаллизацией. Они связаны с переходом при охлаждении γ-железа в α-железо и распадом аустенита.
Линия GS соответствует температурам начала превращения аустенита в феррит. Ниже линии GS сплавы состоят из феррита и аустенита.
Линия ЕS показывает температуры начала выделения цементита из аустенита вследствие уменьшения растворимости углерода в аустените с понижением температуры. Цементит, выделяющийся из аустенита, называется вторичным цементитом.
В точке S при температуре 727°С и концентрации углерода в аустените 0,8 % образуется эвтектоидная смесь состоящая из феррита и цементита, которая называется перлитом. Перлит получается в результате одновременного выпадения из аустенита частиц феррита и цементита. Процесс превращения аустенита в перлит можно записать формулой А0,8П[Ф0,03+Ц6,67].
Линия PQ показывает на уменьшение растворимости углерода в феррите при охлаждении и выделении цементита, который называется третичным цементитом.
Следовательно, сплавы, содержащие менее 0,008% углерода (точкаQ), являются однофазными и имеют структуру чистого феррита, а сплавы, содержащие углерод от 0,008 до 0,03% – структуру феррит+цементит третичный и называются техническим железом.
Доэвтектоидные стали при температуре ниже 727ºС имеют структуру феррит + перлит и заэвтектоидные – перлит + цементит вторичный в виде сетки по границам зерен.
В доэвтектических чугунах в интервале температур 1147–727ºС при охлаждении из аустенита выделяется цементит вторичный, вследствие уменьшения растворимости углерода(линия ES). По достижении температуры 727ºС (линия PSK) аустенит, обедненный углеродом до 0,8% (точка S), превращаясь в перлит. Таким образом, после окончательного охлаждения структура доэвтектических чугунов состоит из перлита, цементита вторичного и ледебурита превращенного (перлит + цементит).
Структура эвтектических чугунов при температурах ниже 727ºС состоит из ледебурита превращенного. Заэвтектический чугун при температурах ниже 727ºС состоит из ледебурита превращенного и цементита первичного.
Правило фаз устанавливает зависимость между числом степеней свободы, числом компонентов и числом фаз и выражается уравнением:
C = K + 1 – Ф,
где С – число степеней свободы системы;
К – число компонентов, образующих систему;
1 – число внешних факторов (внешним фактором считаем только температуру, так как давление за исключением очень высокого мало влияет на фазовое равновесие сплавов в твердом и жидком состояниях);
Ф – число фаз, находящихся в равновесии.
Сплав железа с углеродом, содержащий 0,45%С, называется доэвтектоидной сталью. Его структура при комнатной температуре – феррит + перлит.
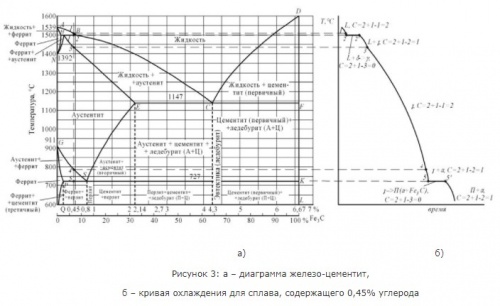
После закалки углеродистой стали У8 была получена структура, состоящая из троостита и мартенсита. Проведите на диаграмме изотермического превращения переохлажденного аустенита кривую охлаждения, обеспечивающую получение такой структуры. Опишите превращения, которые совершились в стали при охлаждении, ее твердость.
Для получения структуры троостит + мартенсит в стали У8 необходимо нагреть ее до температуры выше точки А1, затем охладить так, чтобы пересечь кривую начала превращения аустенита в перлит в области троостита и, минуя кривую конца превращения, перейти в область мартенсита.
При нагреве стали У8 выше А1 перлит переходит в аустенит. При охлаждении со скоростью ниже критической (см. рис.) образуется ферритно-цементитная структура – троостит и мартенсит.
В зависимости от соотношения содержаний троостита и мартенсита в троостомартенсите (от скорости охлаждения) твердость стали может меняться от 300 НВ (при 100 % троостита) до 650 НВ (при 100 % мартенсита).
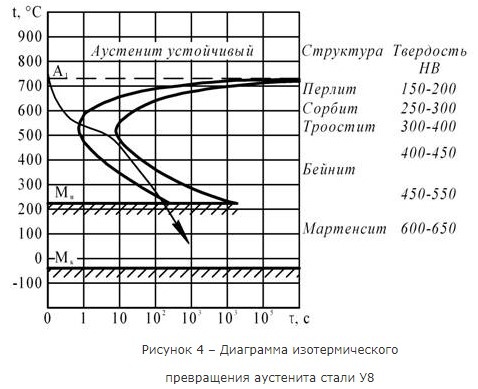
Покажите графически режим отжига для получения ферритного ковкого чугуна. Опишите структурные превращения, происходящие в процессе отжига. Каковы механические свойства чугуна после термической обработки, его структура?
Ковкие чугуны получают из белых чугунов путем графитизирующего отжига (томление). Схема отжига белого чугуна на ковкий показана на рис.
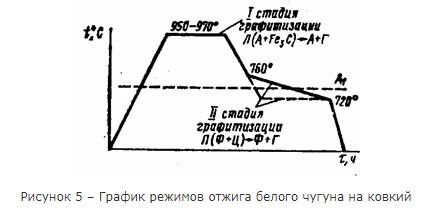
Отжиг проводится в две стадии. Сначала отливки белого чугуна нагревают в течение 20-25 ч до температуры 950-970 °С. Во время выдержки (15 ч) при этой температуре протекает первая стадия графитизации, г. е. распад цементита, входящего в состав ледебурита (A + Fe3C), и установление стабильного равновесия аустенит + графит. В результате распада цементита образуется хлопьевидный графит. Затем отливки медленно охлаждают (в течение 6-12 ч) до температуры 720 °С. При охлаждении происходит выделение из аустенита вторичного графита и рост графитовых включений. По достижении температуры 720°С дают вторую длительную выдержку, при которой происходит распад цементита, входящего в перлит, на феррит и графит. Вторая стадия графитизации длится около 30 ч, и после ее завершения структура чугуна состоит из графита и феррита. Излом ферритного чугуна бархатисто-черный ввиду большого количества графита.
Если вторую стадию графитизации не проводят, то получают ковкий чугун со структурой графит + перлит. Излом такого чугуна светлый.
Для ускорения отжига белого чугуна на ковкий принимают различные меры: чугун модифицируют алюминием (реже бором или висмутом), повышают температуру нагрева перед разливкой, проводят перед отжигом закалку, повышают температуру первой стадии графитизации (до 1080 °С) и т. д.
Ферритные ковкие чугуны КЧ 37-12 и КЧ 35-10 используют для изготовления деталей, работающих при ударных и вибрационных нагрузках (картеры редукторов, ступицы, крюки, скобы и т.д.), ферритные ковкие чугуны КЧ 30-6 и КЧ 33-8 – для менее ответственных деталей (головки, гайки, хомутки, фланцы и т.д.). Твердость ферритного чугуна 163 НВ.
Кристаллы, образующиеся в процессе затвердевания металла, могут иметь различную форму в зависимости от скорости охлаждения, характера и количества примесей. Чаще в процессе кристаллизации образуются разветвленные (древовидные) кристаллы, получившие название дендритов (рисунок 1).
При образовании кристаллов их развитие идет в основном в направлении, перпендикулярном к плоскостям с максимальной плотностью упаковки атомов. Это приводит к тому, что первоначально образуются длинные ветви, так называемые оси первого порядка. Одновременно с удлинением осей первого порядка на их ребрах зарождаются и растут перпендикулярные к ним такие же ветви второго порядка. В свою очередь, на осях второго порядка зарождаются и растут оси третьего порядка и т. д. В конечном счете образуются кристаллы в форме дендритов.
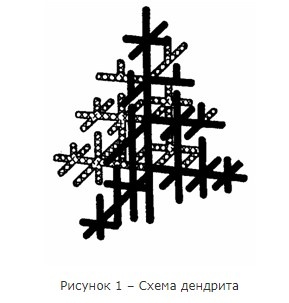
При затвердевании слитка кристаллизация начинается у поверхности более холодной формы и происходит вначале преимущественно в примыкающем к поверхности тонком слое сильно переохлажденной жидкости. Вследствие большой скорости охлаждения это приводит к образованию на поверхности слитка очень узкой зоны 1 сравнительно мелких равноосных кристаллитов (рисунок 2).
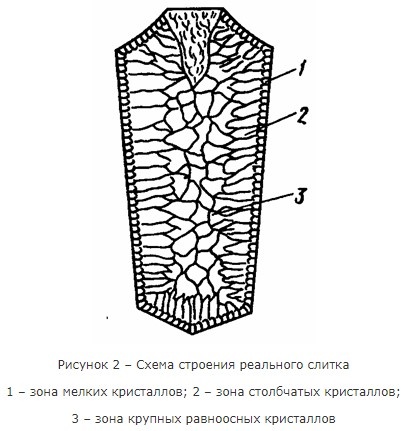
За зоной 1 в глубь слитка расположена зона 2 удлиненных дендритных кристаллитов (зона транскристаллизации). Рост этих кристаллитов происходит в направлении отвода теплоты, т. е. нормально к стенкам изложницы. Последовательный рост дендритов к стенкам изложницы происходит в результате продвижения в глубь расплава ветвей первого порядка и их разветвления аналогично тому, как это было описано выше.
В зоне дальнейшей кристаллизации направленность отвода теплоты теряется, скорость охлаждения уменьшается и поэтому в центральной части слитка образуются крупные равноосные кристаллы.
Зоны столбчатых кристаллов в процессе кристаллизации стыкуются, это явление называется транскристаллизацией. Для малопластичных металлов и для сталей это явление нежелательное, так как при последующей прокатке, ковке могут образовываться трещины в зоне стыка.
В верхней части слитка образуется усадочная раковина, которая подлежит отрезке и переплавке, так как металл более рыхлый (около 15…20 % от длины слитка).
Прутки олова были деформированы при температуре 20°С. Объясните, почему эти прутки не упрочнились при деформировании, и опишите процессы, протекающие при этом.
В зависимости от соотношения температуры деформации и температуры рекристаллизации различают холодную и горячую деформации. Холодной деформацией называют такую, которую проводят при температуре ниже температуры рекристаллизации. Поэтому холодная деформация сопровождается упрочнением (наклепом) металла.
Деформацию называют горячей, если ее проводят при температуре выше температуры рекристаллизации для получения полностью рекристаллизованной структуры.
При этих температурах деформация также вызывает упрочнение «горячий наклеп», которое полностью или частично снимается рекристаллизацией, протекающей при температурах обработки и при последующем охлаждении. В отличие от статической полигонизации и рекристаллизации, процессы полигонизации и рекристаллизации, происходящие в период деформации, называют динамическими.
По правилу А. А. Бочвара можно оценить в первом приближении температурный порог рекристаллизации по известной температуре плавления металла: Тп.р.=0,4Тп.л…
Температура начала рекристаллизации олова:
Тн.р.=(232+273)0,4-273=-71°С.
Следовательно, деформирование олова при температуре 20 °C является горячей деформацией, и упрочнение не происходит.
Вычертите диаграмму состояния железо – карбид железа, укажите структурные составляющие во всех областях диаграммы, опишите превращения и постройте кривую охлаждения (с применением правила фаз) для сплава, содержащего 0,45% С. Какова структура этого сплава при комнатной температуре и как такой сплав называется?
Первичная кристаллизация сплавов системы железо-углерод начинается по достижении температур, соответствующих линии ABCD (линии ликвидус), и заканчивается при температурах, образующих линию AHJECF (линию солидус).
При кристаллизации сплавов по линии АВ из жидкого раствора выделяются кристаллы твердого раствора углерода в α-железе (δ-раствор). Процесс кристаллизации сплавов с содержанием углерода до 0,1 % заканчивается по линии АН с образованием α (δ)-твердого раствора. На линии HJB протекает перитектическое превращение, в результате которого образуется твердый раствор углерода в γ-железе, т. е. аустенит. Процесс первичной кристаллизации сталей заканчивается по линии AHJE.
При температурах, соответствующих линии ВС, из жидкого раствора кристаллизуется аустенит. В сплавах, содержащих от 4,3% до 6,67 % углерода, при температурах, соответствующих линии CD, начинают выделяться кристаллы цементита первичного. Цементит, кристаллизующийся из жидкой фазы, называется первичным. B точке С при температуре 1147°С и концентрации углерода в жидком растворе 4,3% образуется эвтектика, которая называется ледебуритом. Эвтектическое превращение с образованием ледебурита можно записать формулой ЖР4,3Л[А2,14+Ц6,67]. Процесс первичной кристаллизации чугунов заканчивается по линии ECF образованием ледебурита.
Таким образом, структура чугунов ниже 1147°С будет: доэвтектических – аустенит + ледебурит, эвтектических – ледебурит и заэвтектических – цементит (первичный)+ледебурит.
Превращения, происходящие в твердом состоянии, называются вторичной кристаллизацией. Они связаны с переходом при охлаждении γ-железа в α-железо и распадом аустенита.
Линия GS соответствует температурам начала превращения аустенита в феррит. Ниже линии GS сплавы состоят из феррита и аустенита.
Линия ЕS показывает температуры начала выделения цементита из аустенита вследствие уменьшения растворимости углерода в аустените с понижением температуры. Цементит, выделяющийся из аустенита, называется вторичным цементитом.
В точке S при температуре 727°С и концентрации углерода в аустените 0,8 % образуется эвтектоидная смесь состоящая из феррита и цементита, которая называется перлитом. Перлит получается в результате одновременного выпадения из аустенита частиц феррита и цементита. Процесс превращения аустенита в перлит можно записать формулой А0,8П[Ф0,03+Ц6,67].
Линия PQ показывает на уменьшение растворимости углерода в феррите при охлаждении и выделении цементита, который называется третичным цементитом.
Следовательно, сплавы, содержащие менее 0,008% углерода (точкаQ), являются однофазными и имеют структуру чистого феррита, а сплавы, содержащие углерод от 0,008 до 0,03% – структуру феррит+цементит третичный и называются техническим железом.
Доэвтектоидные стали при температуре ниже 727ºС имеют структуру феррит + перлит и заэвтектоидные – перлит + цементит вторичный в виде сетки по границам зерен.
В доэвтектических чугунах в интервале температур 1147–727ºС при охлаждении из аустенита выделяется цементит вторичный, вследствие уменьшения растворимости углерода(линия ES). По достижении температуры 727ºС (линия PSK) аустенит, обедненный углеродом до 0,8% (точка S), превращаясь в перлит. Таким образом, после окончательного охлаждения структура доэвтектических чугунов состоит из перлита, цементита вторичного и ледебурита превращенного (перлит + цементит).
Структура эвтектических чугунов при температурах ниже 727ºС состоит из ледебурита превращенного. Заэвтектический чугун при температурах ниже 727ºС состоит из ледебурита превращенного и цементита первичного.
Правило фаз устанавливает зависимость между числом степеней свободы, числом компонентов и числом фаз и выражается уравнением:
C = K + 1 – Ф,
где С – число степеней свободы системы;
К – число компонентов, образующих систему;
1 – число внешних факторов (внешним фактором считаем только температуру, так как давление за исключением очень высокого мало влияет на фазовое равновесие сплавов в твердом и жидком состояниях);
Ф – число фаз, находящихся в равновесии.
Сплав железа с углеродом, содержащий 0,45%С, называется доэвтектоидной сталью. Его структура при комнатной температуре – феррит + перлит.
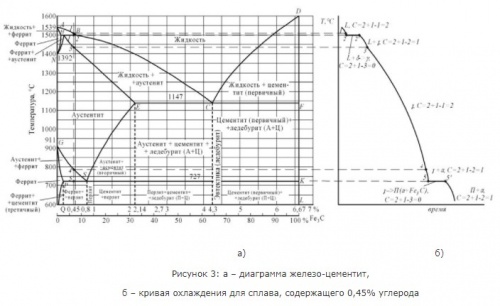
После закалки углеродистой стали У8 была получена структура, состоящая из троостита и мартенсита. Проведите на диаграмме изотермического превращения переохлажденного аустенита кривую охлаждения, обеспечивающую получение такой структуры. Опишите превращения, которые совершились в стали при охлаждении, ее твердость.
Для получения структуры троостит + мартенсит в стали У8 необходимо нагреть ее до температуры выше точки А1, затем охладить так, чтобы пересечь кривую начала превращения аустенита в перлит в области троостита и, минуя кривую конца превращения, перейти в область мартенсита.
При нагреве стали У8 выше А1 перлит переходит в аустенит. При охлаждении со скоростью ниже критической (см. рис.) образуется ферритно-цементитная структура – троостит и мартенсит.
В зависимости от соотношения содержаний троостита и мартенсита в троостомартенсите (от скорости охлаждения) твердость стали может меняться от 300 НВ (при 100 % троостита) до 650 НВ (при 100 % мартенсита).
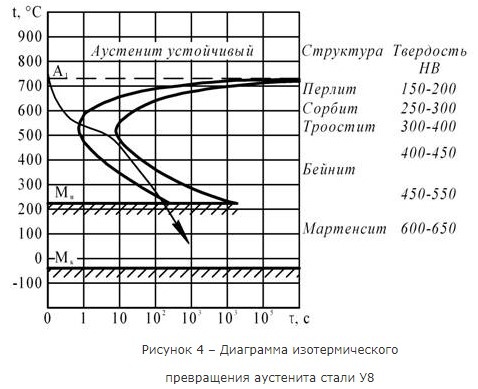
Покажите графически режим отжига для получения ферритного ковкого чугуна. Опишите структурные превращения, происходящие в процессе отжига. Каковы механические свойства чугуна после термической обработки, его структура?
Ковкие чугуны получают из белых чугунов путем графитизирующего отжига (томление). Схема отжига белого чугуна на ковкий показана на рис.
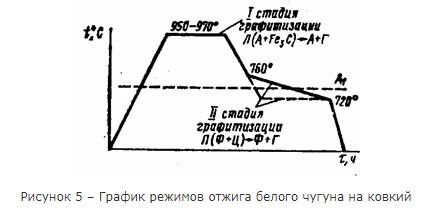
Отжиг проводится в две стадии. Сначала отливки белого чугуна нагревают в течение 20-25 ч до температуры 950-970 °С. Во время выдержки (15 ч) при этой температуре протекает первая стадия графитизации, г. е. распад цементита, входящего в состав ледебурита (A + Fe3C), и установление стабильного равновесия аустенит + графит. В результате распада цементита образуется хлопьевидный графит. Затем отливки медленно охлаждают (в течение 6-12 ч) до температуры 720 °С. При охлаждении происходит выделение из аустенита вторичного графита и рост графитовых включений. По достижении температуры 720°С дают вторую длительную выдержку, при которой происходит распад цементита, входящего в перлит, на феррит и графит. Вторая стадия графитизации длится около 30 ч, и после ее завершения структура чугуна состоит из графита и феррита. Излом ферритного чугуна бархатисто-черный ввиду большого количества графита.
Если вторую стадию графитизации не проводят, то получают ковкий чугун со структурой графит + перлит. Излом такого чугуна светлый.
Для ускорения отжига белого чугуна на ковкий принимают различные меры: чугун модифицируют алюминием (реже бором или висмутом), повышают температуру нагрева перед разливкой, проводят перед отжигом закалку, повышают температуру первой стадии графитизации (до 1080 °С) и т. д.
Ферритные ковкие чугуны КЧ 37-12 и КЧ 35-10 используют для изготовления деталей, работающих при ударных и вибрационных нагрузках (картеры редукторов, ступицы, крюки, скобы и т.д.), ферритные ковкие чугуны КЧ 30-6 и КЧ 33-8 – для менее ответственных деталей (головки, гайки, хомутки, фланцы и т.д.). Твердость ферритного чугуна 163 НВ.
0 комментариев