Контрольная работа 1 Вариант 47
Что такое твердый раствор? Виды твердых растворов. Приведите примеры.
Твердыми растворами называют фазы, в которых один из компонентов сплава сохраняет свою кристаллическую решетку, а атомы других (или другого) компонентов располагаются в решетке первого компонента (растворителя), изменяя ее размеры (периоды). Таким образом, твердый раствор, состоящий из двух или нескольких компонентов, имеет один тип решетки и представляет собой одну фазу.
Существуют твердые растворы внедрения и твердые растворы замещения. При образовании твердых растворов внедрения атомы растворенного компонента B размещаются между атомами растворителя A в его кристаллической решетке. При образовании твердых растворов замещения атомы растворенного компонента B замещают часть атомов растворителя (компонент A) в его кристаллической решетке.
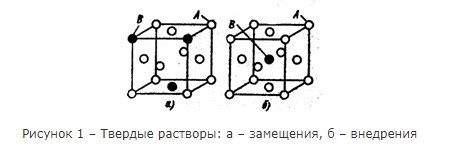
Поскольку размеры растворенных атомов отличаются от размеров атомов растворителя, то образование твердого раствора сопровождается искажением кристаллической решетки растворителя.
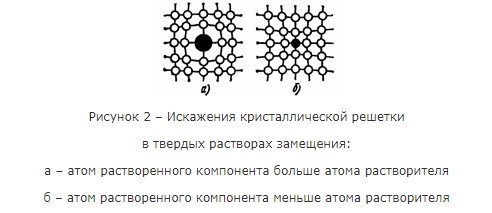
Твердые растворы замещения могут быть с ограниченной и неограниченной растворимостью. В твердых растворах с ограниченной растворимостью концентрация растворенного компонента возможна до определенных пределов.
В твердых растворах с неограниченной растворимостью возможна любая концентрация растворенного компонента (от 0 до 100 %). Твердые растворы с неограниченной растворимостью образуются при соблюдении следующих условий: 1) у компонентов должны быть однотипные кристаллические решетки; 2) различие в атомных радиусах компонентов не должно превышать для сплавов на основе железа 9%, а для сплавов на основе меди 15%; 3) компоненты должны обладать близостью физико-химических свойств. Однако соблюдение этих свойств не всегда приводит к образованию твердых растворов замещения с неограниченной растворимостью. На практике, как правило, образуются твердые растворы с ограниченной растворимостью.
Твердые растворы внедрения могут быть только с ограниченной концентрации, поскольку число пор в решетке ограничено, а атомы основного компонента сохраняются в узлах решетки.
Твердые растворы замещения с неограниченной растворимостью на основе компонентов: Ag и Au, Ni и Cu, Mo и W, V и Ti, и т.д.
Твердые растворы замещения с ограниченной растворимостью на основе компонентов: Al и Cu, Cu и Zn, и т.д.
Твердые растворы внедрения: при растворении в металлах неметаллических элементов, как углерод, бор, азот и кислород. Например: Fe и С.
Какие процессы происходят при горячей пластической деформации и как при этом изменяются строение и свойства металла?
Деформацию называют горячей, если ее проводят при температуре выше температуры рекристаллизации для получения для получения полностью рекристаллизованной структуры.
При этих температурах деформация также вызывает упрочнение («горячий наклеп»), которое полностью или частично снимается рекристаллизацией, протекающей при температурах обработки и при последующем охлаждении.
При горячей обработке давлением (прокатке, прессовании, ковке, штамповке и т. д.) упрочнение в результате наклепа (повышение плотности дислокаций) непосредственно в процессе деформации непрерывно чередуется с процессом разупрочнения (уменьшением плотности дислокаций) при динамической полигонизации и рекристаллизации во время деформации и охлаждения. В этом основное отличие динамической полигонизации и рекристаллизации от статической.
Горячую деформацию в зависимости от состава сплава и скорости деформации обычно проводят при температурах (0,7 – 0,75 Тпл).
Полигонизация – процесс деления зерен на части: фрагменты, полигоны в результате скольжения и переползания дислокаций.
Рекристаллизация – процесс зарождения и роста новых недеформированных зерен при нагреве наклепанного металла до определенной температуры.
Вычертите диаграмму состояния железо – карбид железа, укажите структурные составляющие во всех областях диаграммы, опишите превращения и постройте кривую охлаждения (с применением правила фаз) для сплава, содержащего 5,8% С. Какова структура этого сплава при комнатной температуре и как такой сплав называется?
Первичная кристаллизация сплавов системы железо-углерод начинается по достижении температур, соответствующих линии ABCD (линии ликвидус), и заканчивается при температурах, образующих линию AHJECF (линию солидус).
При кристаллизации сплавов по линии АВ из жидкого раствора выделяются кристаллы твердого раствора углерода в α-железе (δ-раствор). Процесс кристаллизации сплавов с содержанием углерода до 0,1 % заканчивается по линии АН с образованием α (δ)-твердого раствора. На линии HJB протекает перитектическое превращение, в результате которого образуется твердый раствор углерода в γ-железе, т. е. аустенит. Процесс первичной кристаллизации сталей заканчивается по линии AHJE.
При температурах, соответствующих линии ВС, из жидкого раствора кристаллизуется аустенит. В сплавах, содержащих от 4,3 % до 6,67 % углерода, при температурах, соответствующих линии CD, начинают выделяться кристаллы цементита первичного. Цементит, кристаллизующийся из жидкой фазы, называется первичным. B точке С при температуре 1147°С и концентрации углерода в жидком растворе 4,3 % образуется эвтектика, которая называется ледебуритом. Эвтектическое превращение с образованием ледебурита можно записать формулой ЖР4,3Л[А2,14+Ц6,67]. Процесс первичной кристаллизации чугунов заканчивается по линии ECF образованием ледебурита.
Таким образом, структура чугунов ниже 1147°С будет: доэвтектических — аустенит+ледебурит, эвтектических — ледебурит и заэвтектических — цементит (первичный)+ледебурит.
Превращения, происходящие в твердом состоянии, называются вторичной кристаллизацией. Они связаны с переходом при охлаждении γ-железа в α-железо и распадом аустенита.
Линия GS соответствует температурам начала превращения аустенита в феррит. Ниже линии GS сплавы состоят из феррита и аустенита.
Линия ЕS показывает температуры начала выделения цементита из аустенита вследствие уменьшения растворимости углерода в аустените с понижением температуры. Цементит, выделяющийся из аустенита, называется вторичным цементитом.
В точке S при температуре 727°С и концентрации углерода в аустените 0,8 % образуется эвтектоидная смесь состоящая из феррита и цементита, которая называется перлитом. Перлит получается в результате одновременного выпадения из аустенита частиц феррита и цементита. Процесс превращения аустенита в перлит можно записать формулой А0,8П[Ф0,03+Ц6,67].
Линия PQ показывает на уменьшение растворимости углерода в феррите при охлаждении и выделении цементита, который называется третичным цементитом.
Следовательно, сплавы, содержащие менее 0,008% углерода (точкаQ), являются однофазными и имеют структуру чистого феррита, а сплавы, содержащие углерод от 0,008 до 0,03% – структуру феррит+цементит третичный и называются техническим железом.
Доэвтектоидные стали при температуре ниже 727ºС имеют структуру феррит+перлит и заэвтектоидные – перлит+цементит вторичный в виде сетки по границам зерен.
В доэвтектических чугунах в интервале температур 1147–727ºС при охлаждении из аустенита выделяется цементит вторичный, вследствие уменьшения растворимости углерода(линия ES). По достижении температуры 727ºС (линия PSK) аустенит, обедненный углеродом до 0,8% (точка S), превращаясь в перлит. Таким образом, после окончательного охлаждения структура доэвтектических чугунов состоит из перлита, цементита вторичного и ледебурита превращенного (перлит+цементит).
Структура эвтектических чугунов при температурах ниже 727ºС состоит из ледебурита превращенного. Заэвтектический чугун при температурах ниже 727ºС состоит из ледебурита превращенного и цементита первичного.
Правило фаз устанавливает зависимость между числом степеней свободы, числом компонентов и числом фаз и выражается уравнением:
C = K + 1 – Ф,
где С – число степеней свободы системы;
К – число компонентов, образующих систему;
1 – число внешних факторов (внешним фактором считаем только температуру, так как давление за исключением очень высокого мало влияет на фазовое равновесие сплавов в твердом и жидком состояниях);
Ф – число фаз, находящихся в равновесии.
Сплав железа с углеродом, содержащий 5,8%С, называется заэвтектическим чугуном. Его структура при комнатной температуре Цементит (первичный)+Ледебурит(П+Fe3C).

Углеродистая сталь У8 после закалки и отпуска имеет твердость 55...60 HRC. Используя диаграмму состояния железо-карбид железа и учитывая превращения, происходящие в стали при отпуске, выберите температуру закалки и температуру отпуска. Опишите превращения, которые происходят при выбранных режимах термической обработки и окончательную структуру.
Содержание углерода в стали У8 составляет 0,75-0,84%. Поэтому сталь может быть доэвтектоидной, эвтектоидной и заэвтектоидной концентрации. Поэтому исходная структура может состоять из перлита и феррита или перлита или перлита и цементита.
До температуры Аc1 сохраняется исходная структура. При температуре Аc1 происходит превращение перлита в аустенит с содержанием углерода 0,8%. При нагреве выше точки Ас1 происходит растворение цементита в аустените (в соответствии с линией SE). Увеличение температуры выше точки Асm вызывает рост зерна аустенита. Критические точки для стали У8: Аc1 = 720°С; Аcm = 740°С.
Закалка – термическая обработка – заключается в нагреве стали до температуры выше критической (А3 для доэвтектоидной и А1 – для заэвтектоидной сталей) или температуры растворения избыточных фаз, в выдержке и последующем охлаждении со скоростью, превышающей критическую.
Для закалки сталь У8 нагревают на 50-70°С выше точки Ас1. Таким образом, температура нагрева под закалку составляет 780-800°С. При этих температурах в стали наряду с аустенитом может присутствовать цементит (при заэвтектоидной концентрации). Охлаждающая среда при закалке – индустриальное масло. В результате закалки из аустенита образуется неустойчивая, метастабильная структура мартенсит. Структура после закалки – мартенсит (при доэвтектоидной и эвтектоидной концентрации) или мартенсит + цементит (при заэвтектоидной концентрации). Твердость стали У8 после закалки 61-63 HRC.
Для снятия напряжений и стабилизации структуры после закалки изделия подвергают низкому отпуску. Низкий отпуск снижает закалочные макронапряжения, мартенсит закалки переводится в отпущенный мартенсит, повышается прочность и немного улучшается вязкость без заметного снижения твердости. При отпуске уменьшается степень тетрагональности кристаллической решетки мартенсита вследствие выделения из нее углерода в виде ε-карбида. Низкий отпуск проводят при температуре 160-200ºС. Более высокие температуры применять не следует, так как это приводит к снижению твердости, статической и усталостной прочности, износостойкости изделий. Структура стали У8 – отпущенный мартенсит (при доэвтектоидной и эвтектоидной концентрации) или отпущенный мартенсит + карбиды (при заэвектоидной концентрации).
После закалки углеродистой стали была получена структура, состоящая из феррита и мартенсита. Проведите на диаграмме состояния железо-цементит ординату, соответствующую составу заданной стали (примерно). Укажите принятую в данном случае температуру нагрева под закалку. Как называется такой вид закалки? Какие превращения произошли при нагреве и охлаждении?
Рассмотрим на примере стали 45. Температура точки Ас3 для стали 45 составляет 755°С, а Ас1 равна 730°С. Структура доэвтектоидной стали при нагреве её до критической точки Ас1 состоит из зерен перлита и феррита. В точке Ас1 происходит превращение перлита в мелкозернистый аустенит. При дальнейшем нагреве от точки Ас1 до Ас3 избыточный феррит растворяется в аустените и при достижении Ас3 (линия GS) превращения заканчиваются.
Если доэвтектоидную сталь нагреть выше Ас1, но ниже Ас3 (неполная закалка), то в ее структуре после закалки наряду с мартенситом будут участки феррита. Присутствие феррита как мягкой составляющей снижает твердость стали после закалки. При нагреве до температуры, например, 740°С (ниже точки Ас3) структура стали 45 – аустенит + феррит, после охлаждения со скоростью выше критической структура стали – мартенсит + феррит. Температура нагрева стали 45 под неполную закалку составляет 730-755°С (т. 2 на рисунке 1).
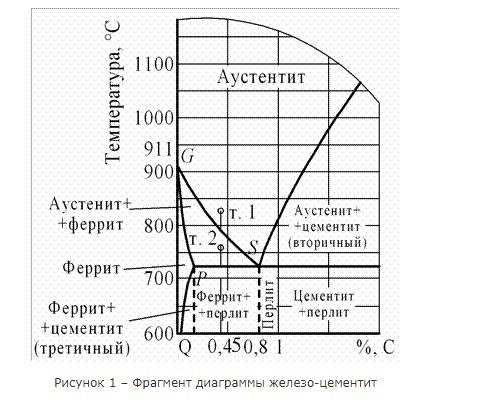
Неполная закалка обеспечивает хорошие механические свойства и штампуемость.
Твердыми растворами называют фазы, в которых один из компонентов сплава сохраняет свою кристаллическую решетку, а атомы других (или другого) компонентов располагаются в решетке первого компонента (растворителя), изменяя ее размеры (периоды). Таким образом, твердый раствор, состоящий из двух или нескольких компонентов, имеет один тип решетки и представляет собой одну фазу.
Существуют твердые растворы внедрения и твердые растворы замещения. При образовании твердых растворов внедрения атомы растворенного компонента B размещаются между атомами растворителя A в его кристаллической решетке. При образовании твердых растворов замещения атомы растворенного компонента B замещают часть атомов растворителя (компонент A) в его кристаллической решетке.
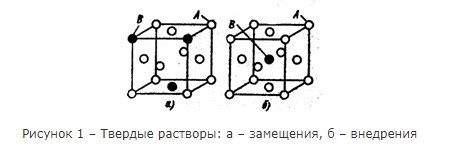
Поскольку размеры растворенных атомов отличаются от размеров атомов растворителя, то образование твердого раствора сопровождается искажением кристаллической решетки растворителя.
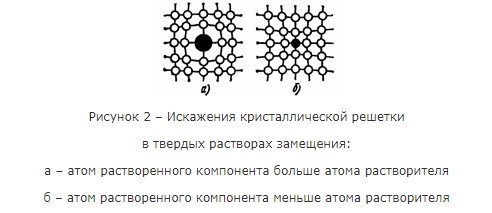
Твердые растворы замещения могут быть с ограниченной и неограниченной растворимостью. В твердых растворах с ограниченной растворимостью концентрация растворенного компонента возможна до определенных пределов.
В твердых растворах с неограниченной растворимостью возможна любая концентрация растворенного компонента (от 0 до 100 %). Твердые растворы с неограниченной растворимостью образуются при соблюдении следующих условий: 1) у компонентов должны быть однотипные кристаллические решетки; 2) различие в атомных радиусах компонентов не должно превышать для сплавов на основе железа 9%, а для сплавов на основе меди 15%; 3) компоненты должны обладать близостью физико-химических свойств. Однако соблюдение этих свойств не всегда приводит к образованию твердых растворов замещения с неограниченной растворимостью. На практике, как правило, образуются твердые растворы с ограниченной растворимостью.
Твердые растворы внедрения могут быть только с ограниченной концентрации, поскольку число пор в решетке ограничено, а атомы основного компонента сохраняются в узлах решетки.
Твердые растворы замещения с неограниченной растворимостью на основе компонентов: Ag и Au, Ni и Cu, Mo и W, V и Ti, и т.д.
Твердые растворы замещения с ограниченной растворимостью на основе компонентов: Al и Cu, Cu и Zn, и т.д.
Твердые растворы внедрения: при растворении в металлах неметаллических элементов, как углерод, бор, азот и кислород. Например: Fe и С.
Какие процессы происходят при горячей пластической деформации и как при этом изменяются строение и свойства металла?
Деформацию называют горячей, если ее проводят при температуре выше температуры рекристаллизации для получения для получения полностью рекристаллизованной структуры.
При этих температурах деформация также вызывает упрочнение («горячий наклеп»), которое полностью или частично снимается рекристаллизацией, протекающей при температурах обработки и при последующем охлаждении.
При горячей обработке давлением (прокатке, прессовании, ковке, штамповке и т. д.) упрочнение в результате наклепа (повышение плотности дислокаций) непосредственно в процессе деформации непрерывно чередуется с процессом разупрочнения (уменьшением плотности дислокаций) при динамической полигонизации и рекристаллизации во время деформации и охлаждения. В этом основное отличие динамической полигонизации и рекристаллизации от статической.
Горячую деформацию в зависимости от состава сплава и скорости деформации обычно проводят при температурах (0,7 – 0,75 Тпл).
Полигонизация – процесс деления зерен на части: фрагменты, полигоны в результате скольжения и переползания дислокаций.
Рекристаллизация – процесс зарождения и роста новых недеформированных зерен при нагреве наклепанного металла до определенной температуры.
Вычертите диаграмму состояния железо – карбид железа, укажите структурные составляющие во всех областях диаграммы, опишите превращения и постройте кривую охлаждения (с применением правила фаз) для сплава, содержащего 5,8% С. Какова структура этого сплава при комнатной температуре и как такой сплав называется?
Первичная кристаллизация сплавов системы железо-углерод начинается по достижении температур, соответствующих линии ABCD (линии ликвидус), и заканчивается при температурах, образующих линию AHJECF (линию солидус).
При кристаллизации сплавов по линии АВ из жидкого раствора выделяются кристаллы твердого раствора углерода в α-железе (δ-раствор). Процесс кристаллизации сплавов с содержанием углерода до 0,1 % заканчивается по линии АН с образованием α (δ)-твердого раствора. На линии HJB протекает перитектическое превращение, в результате которого образуется твердый раствор углерода в γ-железе, т. е. аустенит. Процесс первичной кристаллизации сталей заканчивается по линии AHJE.
При температурах, соответствующих линии ВС, из жидкого раствора кристаллизуется аустенит. В сплавах, содержащих от 4,3 % до 6,67 % углерода, при температурах, соответствующих линии CD, начинают выделяться кристаллы цементита первичного. Цементит, кристаллизующийся из жидкой фазы, называется первичным. B точке С при температуре 1147°С и концентрации углерода в жидком растворе 4,3 % образуется эвтектика, которая называется ледебуритом. Эвтектическое превращение с образованием ледебурита можно записать формулой ЖР4,3Л[А2,14+Ц6,67]. Процесс первичной кристаллизации чугунов заканчивается по линии ECF образованием ледебурита.
Таким образом, структура чугунов ниже 1147°С будет: доэвтектических — аустенит+ледебурит, эвтектических — ледебурит и заэвтектических — цементит (первичный)+ледебурит.
Превращения, происходящие в твердом состоянии, называются вторичной кристаллизацией. Они связаны с переходом при охлаждении γ-железа в α-железо и распадом аустенита.
Линия GS соответствует температурам начала превращения аустенита в феррит. Ниже линии GS сплавы состоят из феррита и аустенита.
Линия ЕS показывает температуры начала выделения цементита из аустенита вследствие уменьшения растворимости углерода в аустените с понижением температуры. Цементит, выделяющийся из аустенита, называется вторичным цементитом.
В точке S при температуре 727°С и концентрации углерода в аустените 0,8 % образуется эвтектоидная смесь состоящая из феррита и цементита, которая называется перлитом. Перлит получается в результате одновременного выпадения из аустенита частиц феррита и цементита. Процесс превращения аустенита в перлит можно записать формулой А0,8П[Ф0,03+Ц6,67].
Линия PQ показывает на уменьшение растворимости углерода в феррите при охлаждении и выделении цементита, который называется третичным цементитом.
Следовательно, сплавы, содержащие менее 0,008% углерода (точкаQ), являются однофазными и имеют структуру чистого феррита, а сплавы, содержащие углерод от 0,008 до 0,03% – структуру феррит+цементит третичный и называются техническим железом.
Доэвтектоидные стали при температуре ниже 727ºС имеют структуру феррит+перлит и заэвтектоидные – перлит+цементит вторичный в виде сетки по границам зерен.
В доэвтектических чугунах в интервале температур 1147–727ºС при охлаждении из аустенита выделяется цементит вторичный, вследствие уменьшения растворимости углерода(линия ES). По достижении температуры 727ºС (линия PSK) аустенит, обедненный углеродом до 0,8% (точка S), превращаясь в перлит. Таким образом, после окончательного охлаждения структура доэвтектических чугунов состоит из перлита, цементита вторичного и ледебурита превращенного (перлит+цементит).
Структура эвтектических чугунов при температурах ниже 727ºС состоит из ледебурита превращенного. Заэвтектический чугун при температурах ниже 727ºС состоит из ледебурита превращенного и цементита первичного.
Правило фаз устанавливает зависимость между числом степеней свободы, числом компонентов и числом фаз и выражается уравнением:
C = K + 1 – Ф,
где С – число степеней свободы системы;
К – число компонентов, образующих систему;
1 – число внешних факторов (внешним фактором считаем только температуру, так как давление за исключением очень высокого мало влияет на фазовое равновесие сплавов в твердом и жидком состояниях);
Ф – число фаз, находящихся в равновесии.
Сплав железа с углеродом, содержащий 5,8%С, называется заэвтектическим чугуном. Его структура при комнатной температуре Цементит (первичный)+Ледебурит(П+Fe3C).

Углеродистая сталь У8 после закалки и отпуска имеет твердость 55...60 HRC. Используя диаграмму состояния железо-карбид железа и учитывая превращения, происходящие в стали при отпуске, выберите температуру закалки и температуру отпуска. Опишите превращения, которые происходят при выбранных режимах термической обработки и окончательную структуру.
Содержание углерода в стали У8 составляет 0,75-0,84%. Поэтому сталь может быть доэвтектоидной, эвтектоидной и заэвтектоидной концентрации. Поэтому исходная структура может состоять из перлита и феррита или перлита или перлита и цементита.
До температуры Аc1 сохраняется исходная структура. При температуре Аc1 происходит превращение перлита в аустенит с содержанием углерода 0,8%. При нагреве выше точки Ас1 происходит растворение цементита в аустените (в соответствии с линией SE). Увеличение температуры выше точки Асm вызывает рост зерна аустенита. Критические точки для стали У8: Аc1 = 720°С; Аcm = 740°С.
Закалка – термическая обработка – заключается в нагреве стали до температуры выше критической (А3 для доэвтектоидной и А1 – для заэвтектоидной сталей) или температуры растворения избыточных фаз, в выдержке и последующем охлаждении со скоростью, превышающей критическую.
Для закалки сталь У8 нагревают на 50-70°С выше точки Ас1. Таким образом, температура нагрева под закалку составляет 780-800°С. При этих температурах в стали наряду с аустенитом может присутствовать цементит (при заэвтектоидной концентрации). Охлаждающая среда при закалке – индустриальное масло. В результате закалки из аустенита образуется неустойчивая, метастабильная структура мартенсит. Структура после закалки – мартенсит (при доэвтектоидной и эвтектоидной концентрации) или мартенсит + цементит (при заэвтектоидной концентрации). Твердость стали У8 после закалки 61-63 HRC.
Для снятия напряжений и стабилизации структуры после закалки изделия подвергают низкому отпуску. Низкий отпуск снижает закалочные макронапряжения, мартенсит закалки переводится в отпущенный мартенсит, повышается прочность и немного улучшается вязкость без заметного снижения твердости. При отпуске уменьшается степень тетрагональности кристаллической решетки мартенсита вследствие выделения из нее углерода в виде ε-карбида. Низкий отпуск проводят при температуре 160-200ºС. Более высокие температуры применять не следует, так как это приводит к снижению твердости, статической и усталостной прочности, износостойкости изделий. Структура стали У8 – отпущенный мартенсит (при доэвтектоидной и эвтектоидной концентрации) или отпущенный мартенсит + карбиды (при заэвектоидной концентрации).
После закалки углеродистой стали была получена структура, состоящая из феррита и мартенсита. Проведите на диаграмме состояния железо-цементит ординату, соответствующую составу заданной стали (примерно). Укажите принятую в данном случае температуру нагрева под закалку. Как называется такой вид закалки? Какие превращения произошли при нагреве и охлаждении?
Рассмотрим на примере стали 45. Температура точки Ас3 для стали 45 составляет 755°С, а Ас1 равна 730°С. Структура доэвтектоидной стали при нагреве её до критической точки Ас1 состоит из зерен перлита и феррита. В точке Ас1 происходит превращение перлита в мелкозернистый аустенит. При дальнейшем нагреве от точки Ас1 до Ас3 избыточный феррит растворяется в аустените и при достижении Ас3 (линия GS) превращения заканчиваются.
Если доэвтектоидную сталь нагреть выше Ас1, но ниже Ас3 (неполная закалка), то в ее структуре после закалки наряду с мартенситом будут участки феррита. Присутствие феррита как мягкой составляющей снижает твердость стали после закалки. При нагреве до температуры, например, 740°С (ниже точки Ас3) структура стали 45 – аустенит + феррит, после охлаждения со скоростью выше критической структура стали – мартенсит + феррит. Температура нагрева стали 45 под неполную закалку составляет 730-755°С (т. 2 на рисунке 1).
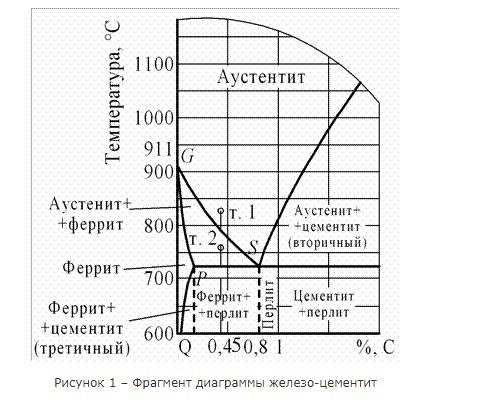
Неполная закалка обеспечивает хорошие механические свойства и штампуемость.
0 комментариев