Контрольная работа 1 Вариант 4
Опишите физическую сущность и механизм процесса кристаллизации
Любое вещество может находиться в трех агрегатных состояниях: твердом, жидком, газообразном. Возможен переход из одного состояния в другое, если новое состояние в новых условиях является более устойчивым, обладает меньшим запасом энергии.
С изменением внешних условий свободная энергия изменяется по сложному закону различно для жидкого и кристаллического состояний. Характер изменения свободной энергии жидкого и твердого состояний с изменением температуры показан на рисунке 1.
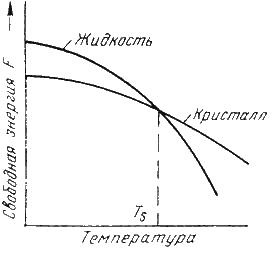
Рисунок 1 –Изменение свободной энергии в зависимости от температуры
В соответствии с этой схемой выше температуры ТS вещество должно находиться в жидком состоянии, а ниже ТS – в твердом.
При температуре равной ТS жидкая и твердая фаза обладают одинаковой энергией, металл в обоих состояниях находится в равновесии, поэтому две фазы могут существовать одновременно бесконечно долго. Температура ТS – равновесная или теоретическая температура кристаллизации.
Для начала процесса кристаллизации необходимо, чтобы процесс был термодинамически выгоден системе и сопровождался уменьшением свободной энергии системы. Это возможно при охлаждении жидкости ниже температуры ТS. Температура, при которой практически начинается кристаллизация называется фактической температурой кристаллизации.
Охлаждение жидкости ниже равновесной температуры кристаллизации называется переохлаждением, которое характеризуется степенью переохлаждения (ΔТ):
ΔТ = Ттеор-Ткр.
Степень переохлаждения зависит от природы металла, от степени его загрязненности (чем чище металл, тем больше степень переохлаждения), от скорости охлаждения (чем выше скорость охлаждения, тем больше степень переохлаждени).
При нагреве всех кристаллических тел наблюдается четкая граница перехода из твердого состояния в жидкое. Такая же граница существует при переходе из жидкого состояния в твердое.
Кристаллизация – это процесс образования участков кристаллической решетки в жидкой фазе и рост кристаллов из образовавшихся центров.
Процесс перехода металла из жидкого состояния в кристаллическое можно изобразить кривыми в координатах время – температура. Кривая охлаждения чистого металла представлена на рисунке 2.
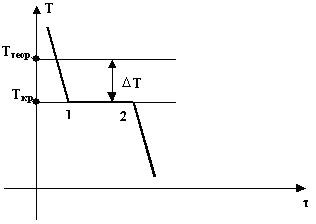
Рисунок 2 – Кривая охлаждения чистого металла
Ттеор – теоретическая температура кристаллизации;
Ткр – фактическая температура кристаллизации.
Процесс кристаллизации чистого металла:
До точки 1 охлаждается металл в жидком состоянии, процесс сопровождается плавным понижением температуры. На участке 1 – 2 идет процесс кристаллизации, сопровождающийся выделением тепла, которое называется скрытой теплотой кристаллизации. Оно компенсирует рассеивание теплоты в пространство, и поэтому температура остается постоянной. После окончания кристаллизации в точке 2 температура снова начинает снижаться, металл охлаждается в твердом состоянии.
Механизм кристаллизации металлов.
При соответствующем понижении температуры в жидком металле начинают образовываться кристаллики – центры кристаллизации или зародыши. Для начала их роста необходимо уменьшение свободной энергии металла, в противном случае зародыш растворяется.
Механизм кристаллизации представлен на рисунке 3.
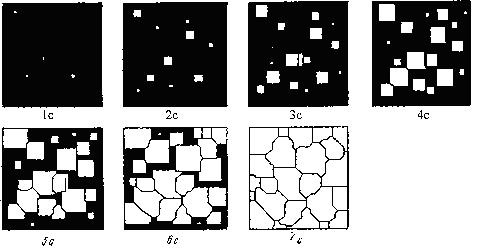
Рисунок 3 –Модель процесса кристаллизации
Центры кристаллизации образуются в исходной фазе независимо друг от друга в случайных местах. Сначала кристаллы имеют правильную форму, но по мере столкновения и срастания с другими кристаллами форма нарушается. Рост продолжается в направлениях, где есть свободный доступ питающей среды. После окончания кристаллизации имеем поликристаллическое тело.
Таким образом, процесс кристаллизации состоит из образования центров кристаллизации и роста кристаллов из этих центров.
В свою очередь, число центров кристаллизации (ч.ц.) и скорость роста кристаллов (с.р.) зависят от степени переохлаждения (рисунок 4).
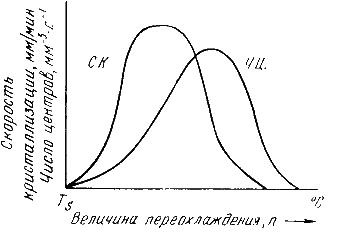
Рисунок 4 – Зависимость числа центров кристаллизации (а) и скорости роста кристаллов (б) от степени переохлаждения
Размеры образовавшихся кристаллов зависят от соотношения числа образовавшихся центров кристаллизации и скорости роста кристаллов при температуре кристаллизации.
При равновесной температуре кристаллизации ТS число образовавшихся центров кристаллизации и скорость их роста равняются нулю, поэтому процесса кристаллизации не происходит.
Если жидкость переохладить до температуры, соответствующей т. а, то образуются крупные зерна (число образовавшихся центров небольшое, а скорость роста – большая).
При переохлаждении до температуры соответствующей т. в – мелкое зерно (образуется большое число центров кристаллизации, а скорость их роста небольшая).
Если металл очень сильно переохладить, то число центров и скорость роста кристаллов равны нулю, жидкость не кристаллизуется, образуется аморфное тело. Для металлов, обладающих малой склонностью к переохлаждению, экспериментально обнаруживаются только восходящие ветви кривых.
Для чего проводится рекристаллизационный отжиг? Как назначается режим этого вида обработки? Приведите несколько конкретных примеров.
Рекристаллизация – процесс зарождения и роста новых недеформированных зерен при нагреве наклепанного металла до определенной температуры.
Рекристаллизационный отжиг используют в промышленности как первоначальную операцию перед холодной обработкой давлением (для придания материалу наибольшей пластичности), как промежуточный процесс между операциями холодного деформирования (для снятия наклепа) и как окончательную (выходную) термическую обработку (для придания полуфабрикату или изделию необходимых свойств).
Нагрев деформированного металла ведет к повышению подвижности атомов, и среди вытянутых зерен идет интенсивное зарождение и рост новых равновесных свободных от напряжений зерен. Новые зерна растут за счет старых, вытянутых, до их столкновения друг с другом и до полного исчезновения вытянутых зерен. При нагреве по достижении температуры начала рекристаллизации предел прочности и особенно текучести резко снижаются, а пластичность увеличивается. Для устранения наклепа необходим отжиг. Основные цели отжига: перекристаллизация стали (измельчение зерна), снятие внутренних напряжений, снижение твердости и улучшение обрабатываемости.
Наименьшую температуру начала рекристаллизации, при которой протекает рекристаллизация и происходит разупрочнение металла, называют температурным порогом рекристаллизации. Эта температура не является постоянной физической величиной. Для данного металла (сплава) она зависит от длительности нагрева, степени предварительной деформации, величины зерна до деформации и т. д.
Температура начала рекристаллизации металлов, подвергнутых значительной деформации, для технически чистых металлов составляет примерно 0,4 Тпл (правило А.А. Бочвара), для чистых металлов снижается до (0,1...0,2)Тпл, а для сплавов твердых растворов возрастает до (0,5...0,6)Тпл.
Для углеродистых сталей с 0,08 – 0,2% С, часто подвергаемых холодной деформации (прокатке, штамповке, волочению), температура отжига находится в интервале 680 – 700 °С. Отжиг калиброванных прутков (холодная протяжка) из высокоуглеродистой легированной стали проводят при 680 – 740 °С в течение 0,5 – 1,5 ч.
Так, например, температура начала рекристаллизации свинца:
Tн.к.=(327+273)0,4-273=-33°C.
Таким образом, комнатная температура превышает температуру начала рекристаллизации свинца.
Вычертите диаграмму состояния железо-карбид железа, укажите структурные составляющие во всех областях диаграммы, опишите превращения и постройте кривую охлаждения (с применением правила фаз) для сплава, содержащего 0,4% С. Какова структура этого сплава при комнатной температуре и как такой сплав называется?
Первичная кристаллизация сплавов системы железо-углерод начинается по достижении температур, соответствующих линии ABCD (линии ликвидус), и заканчивается при температурах, образующих линию AHJECF (линию солидус).
При кристаллизации сплавов по линии АВ из жидкого раствора выделяются кристаллы твердого раствора углерода в α-железе (δ-раствор). Процесс кристаллизации сплавов с содержанием углерода до 0,1 % заканчивается по линии АН с образованием α (δ)-твердого раствора. На линии HJB протекает перитектическое превращение, в результате которого образуется твердый раствор углерода в γ-железе, т. е. аустенит. Процесс первичной кристаллизации сталей заканчивается по линии AHJE.
При температурах, соответствующих линии ВС, из жидкого раствора кристаллизуется аустенит. В сплавах, содержащих от 4,3 % до 6,67 % углерода, при температурах, соответствующих линии CD, начинают выделяться кристаллы цементита первичного. Цементит, кристаллизующийся из жидкой фазы, называется первичным. B точке С при температуре 1147°С и концентрации углерода в жидком растворе 4,3 % образуется эвтектика, которая называется ледебуритом. Эвтектическое превращение с образованием ледебурита можно записать формулой ЖР4,3Л[А2,14+Ц6,67]. Процесс первичной кристаллизации чугунов заканчивается по линии ECF образованием ледебурита.
Таким образом, структура чугунов ниже 1147°С будет: доэвтектических — аустенит+ледебурит, эвтектических — ледебурит и заэвтектических — цементит (первичный)+ледебурит.
Превращения, происходящие в твердом состоянии, называются вторичной кристаллизацией. Они связаны с переходом при охлаждении γ-железа в α-железо и распадом аустенита.
Линия GS соответствует температурам начала превращения аустенита в феррит. Ниже линии GS сплавы состоят из феррита и аустенита.
Линия ЕS показывает температуры начала выдел пня цементита из аустенита вследствие уменьшения растворимости углерода в аустените с понижением температуры. Цементит, выделяющийся из аустенита, называется вторичным цементитом.
В точке S при температуре 727°С и концентрации углерода в аустените 0,8 % образуется эвтектоидная смесь состоящая из феррита и цементита, которая называется перлитом. Перлит получается в результате одновременного выпадения из аустенита частиц феррита и цементита. Процесс превращения аустенита в перлит можно записать формулой А0,8П[Ф0,03+Ц6,67].
Линия PQ показывает на уменьшение растворимости углерода в феррите при охлаждении и выделении цементита, который называется третичным цементитом.
Следовательно, сплавы, содержащие менее 0,008% углерода (точкаQ), являются однофазными и имеют структуру чистого феррита, а сплавы, содержащие углерод от 0,008 до 0,03% – структуру феррит+цементит третичный и называются техническим железом.
Доэвтектоидные стали при температуре ниже 727ºС имеют структуру феррит+перлит и заэвтектоидные – перлит+цементит вторичный в виде сетки по границам зерен.
В доэвтектических чугунах в интервале температур 1147–727ºС при охлаждении из аустенита выделяется цементит вторичный, вследствие уменьшения растворимости углерода(линия ES). По достижении температуры 727ºС (линия PSK) аустенит, обедненный углеродом до 0,8% (точка S), превращаясь в перлит. Таким образом, после окончательного охлаждения структура доэвтектических чугунов состоит из перлита, цементита вторичного и ледебурита превращенного (перлит+цементит).
Структура эвтектических чугунов при температурах ниже 727ºС состоит из ледебурита превращенного. Заэвтектический чугун при температурах ниже 727ºС состоит из ледебурита превращенного и цементита первичного.
Правило фаз устанавливает зависимость между числом степеней свободы, числом компонентов и числом фаз и выражается уравнением:
C = K + 1 – Ф,
где С – число степеней свободы системы;
К – число компонентов, образующих систему;
1 – число внешних факторов (внешним фактором считаем только температуру, так как давление за исключением очень высокого мало влияет на фазовое равновесие сплавов в твердом и жидком состояниях);
Ф – число фаз, находящихся в равновесии.
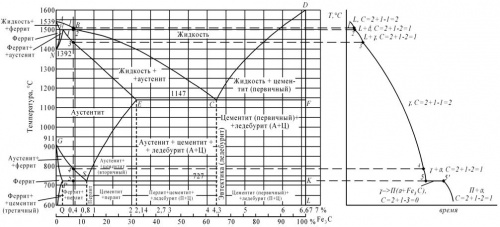
Рисунок 5: а – диаграмма железо-цементит,
б – кривая охлаждения для сплава, содержащего 0,4% углерода
Сплав железа с углеродом, содержащий 0,4% С, называется среднеуглеродистой сталью. Его структура при комнатной температуре феррит + перлит.
Используя диаграмму изотермического превращения аустенита, объясните, почему нельзя получить в стали чисто мартенситную структуру при охлаждении ее со скоростью меньше критической?
Чем больше скорость охлаждения и ниже температура распада аустенита (рисунок 6), тем дисперснее образующаяся феррито-цементитная структура. Следовательно, при небольшой скорости охлаждения υ1 образуется перлит, при большей υ2 – сорбит и еще большей υ3 –троостит.
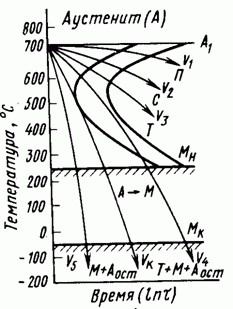
Рисунок 6 – Наложение кривых охлаждения на диаграмму изотермического распада аустенита
При высоких скоростях охлаждения (кривая υ4) часть аустенита переохлаждается до точки Мн и превращается в мартенсит. Структура в этом случае состоит из троостита и мартенсита.
При очень большой скорости охлаждения диффузионный распад аустенита становится вообще невозможным, и тогда аустенит переохлаждается до точки Мн и при дальнейшем охлаждении превращается в мартенсит (кривая υ5). Превращение аустенита в мартенсит не идет до конца, поэтому в закаленной стали наряду с мартенситом всегда присутствует в некотором количестве остаточный аустенит. Минимальную скорость охлаждения (кривая υк), при которой весь аустенит переохлаждается до точки Мн и превращается в мартенсит, называется критической скоростью закалки.
После термической обработки углеродистой стали получена структура цементит + мартенсит отпуска. Нанесите на диаграмму состояния железо-цементит ординату заданной стали (примерно) и обоснуйте температуру нагрева этой стали под закалку. Так же укажите температуру отпуска. Опишите превращения, которые произошли при термической обработке.
Структура цементит + мартенсит отпуска получается после закалки и низкого отпуска заэвтектоидной углеродистой стали. Рассмотрим на примере стали У12.
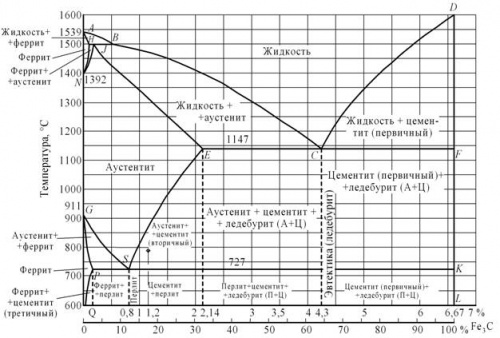
Диаграмма состояния железо-цементит представлена выше. При комнатной температуре сталь У12 имеет структуру цементита и перлита. До температуры Аc1 сохраняется исходная структура. При температуре Аc1 происходит превращение перлита в аустенит с содержанием углерода 0,8%. При нагреве выше точки Ас1 происходит растворение цементита в аустените (в соответствии с линией SE). Увеличение температуры выше точки Асm вызывает рост зерна аустенита.
Критические точки для стали У12: Аc1 = 730°С; Аcm = 820°С.
Для закалки заэвтектоидные стали нагревают на 50-70°С выше точки Ас1. Таким образом, температура нагрева под закалку составляет 780-800°С. При этих температурах в стали наряду с аустенитом имеется цементит. Поэтому после закалки в структуре заэвтектоидных сталей будет мартенсит с цементитом и небольшое количество остаточного аустенита.
Для снятия напряжений и стабилизации структуры после закалки изделия подвергают низкому отпуску при температуре 160–180 °С. Структура стали после низкого отпуска – отпущенный мартенсит + карбиды.
Любое вещество может находиться в трех агрегатных состояниях: твердом, жидком, газообразном. Возможен переход из одного состояния в другое, если новое состояние в новых условиях является более устойчивым, обладает меньшим запасом энергии.
С изменением внешних условий свободная энергия изменяется по сложному закону различно для жидкого и кристаллического состояний. Характер изменения свободной энергии жидкого и твердого состояний с изменением температуры показан на рисунке 1.
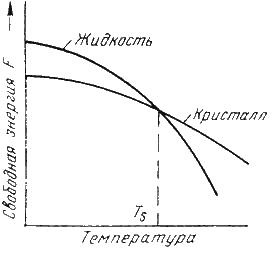
Рисунок 1 –Изменение свободной энергии в зависимости от температуры
В соответствии с этой схемой выше температуры ТS вещество должно находиться в жидком состоянии, а ниже ТS – в твердом.
При температуре равной ТS жидкая и твердая фаза обладают одинаковой энергией, металл в обоих состояниях находится в равновесии, поэтому две фазы могут существовать одновременно бесконечно долго. Температура ТS – равновесная или теоретическая температура кристаллизации.
Для начала процесса кристаллизации необходимо, чтобы процесс был термодинамически выгоден системе и сопровождался уменьшением свободной энергии системы. Это возможно при охлаждении жидкости ниже температуры ТS. Температура, при которой практически начинается кристаллизация называется фактической температурой кристаллизации.
Охлаждение жидкости ниже равновесной температуры кристаллизации называется переохлаждением, которое характеризуется степенью переохлаждения (ΔТ):
ΔТ = Ттеор-Ткр.
Степень переохлаждения зависит от природы металла, от степени его загрязненности (чем чище металл, тем больше степень переохлаждения), от скорости охлаждения (чем выше скорость охлаждения, тем больше степень переохлаждени).
При нагреве всех кристаллических тел наблюдается четкая граница перехода из твердого состояния в жидкое. Такая же граница существует при переходе из жидкого состояния в твердое.
Кристаллизация – это процесс образования участков кристаллической решетки в жидкой фазе и рост кристаллов из образовавшихся центров.
Процесс перехода металла из жидкого состояния в кристаллическое можно изобразить кривыми в координатах время – температура. Кривая охлаждения чистого металла представлена на рисунке 2.
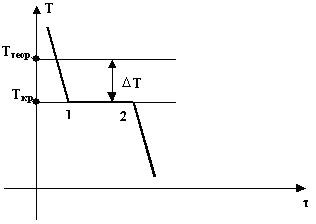
Рисунок 2 – Кривая охлаждения чистого металла
Ттеор – теоретическая температура кристаллизации;
Ткр – фактическая температура кристаллизации.
Процесс кристаллизации чистого металла:
До точки 1 охлаждается металл в жидком состоянии, процесс сопровождается плавным понижением температуры. На участке 1 – 2 идет процесс кристаллизации, сопровождающийся выделением тепла, которое называется скрытой теплотой кристаллизации. Оно компенсирует рассеивание теплоты в пространство, и поэтому температура остается постоянной. После окончания кристаллизации в точке 2 температура снова начинает снижаться, металл охлаждается в твердом состоянии.
Механизм кристаллизации металлов.
При соответствующем понижении температуры в жидком металле начинают образовываться кристаллики – центры кристаллизации или зародыши. Для начала их роста необходимо уменьшение свободной энергии металла, в противном случае зародыш растворяется.
Механизм кристаллизации представлен на рисунке 3.
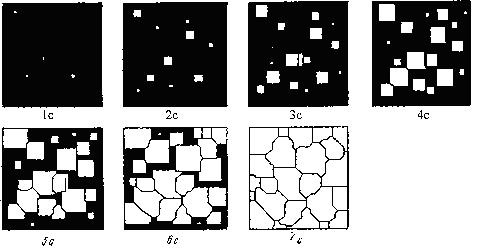
Рисунок 3 –Модель процесса кристаллизации
Центры кристаллизации образуются в исходной фазе независимо друг от друга в случайных местах. Сначала кристаллы имеют правильную форму, но по мере столкновения и срастания с другими кристаллами форма нарушается. Рост продолжается в направлениях, где есть свободный доступ питающей среды. После окончания кристаллизации имеем поликристаллическое тело.
Таким образом, процесс кристаллизации состоит из образования центров кристаллизации и роста кристаллов из этих центров.
В свою очередь, число центров кристаллизации (ч.ц.) и скорость роста кристаллов (с.р.) зависят от степени переохлаждения (рисунок 4).
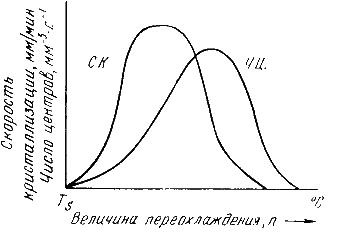
Рисунок 4 – Зависимость числа центров кристаллизации (а) и скорости роста кристаллов (б) от степени переохлаждения
Размеры образовавшихся кристаллов зависят от соотношения числа образовавшихся центров кристаллизации и скорости роста кристаллов при температуре кристаллизации.
При равновесной температуре кристаллизации ТS число образовавшихся центров кристаллизации и скорость их роста равняются нулю, поэтому процесса кристаллизации не происходит.
Если жидкость переохладить до температуры, соответствующей т. а, то образуются крупные зерна (число образовавшихся центров небольшое, а скорость роста – большая).
При переохлаждении до температуры соответствующей т. в – мелкое зерно (образуется большое число центров кристаллизации, а скорость их роста небольшая).
Если металл очень сильно переохладить, то число центров и скорость роста кристаллов равны нулю, жидкость не кристаллизуется, образуется аморфное тело. Для металлов, обладающих малой склонностью к переохлаждению, экспериментально обнаруживаются только восходящие ветви кривых.
Для чего проводится рекристаллизационный отжиг? Как назначается режим этого вида обработки? Приведите несколько конкретных примеров.
Рекристаллизация – процесс зарождения и роста новых недеформированных зерен при нагреве наклепанного металла до определенной температуры.
Рекристаллизационный отжиг используют в промышленности как первоначальную операцию перед холодной обработкой давлением (для придания материалу наибольшей пластичности), как промежуточный процесс между операциями холодного деформирования (для снятия наклепа) и как окончательную (выходную) термическую обработку (для придания полуфабрикату или изделию необходимых свойств).
Нагрев деформированного металла ведет к повышению подвижности атомов, и среди вытянутых зерен идет интенсивное зарождение и рост новых равновесных свободных от напряжений зерен. Новые зерна растут за счет старых, вытянутых, до их столкновения друг с другом и до полного исчезновения вытянутых зерен. При нагреве по достижении температуры начала рекристаллизации предел прочности и особенно текучести резко снижаются, а пластичность увеличивается. Для устранения наклепа необходим отжиг. Основные цели отжига: перекристаллизация стали (измельчение зерна), снятие внутренних напряжений, снижение твердости и улучшение обрабатываемости.
Наименьшую температуру начала рекристаллизации, при которой протекает рекристаллизация и происходит разупрочнение металла, называют температурным порогом рекристаллизации. Эта температура не является постоянной физической величиной. Для данного металла (сплава) она зависит от длительности нагрева, степени предварительной деформации, величины зерна до деформации и т. д.
Температура начала рекристаллизации металлов, подвергнутых значительной деформации, для технически чистых металлов составляет примерно 0,4 Тпл (правило А.А. Бочвара), для чистых металлов снижается до (0,1...0,2)Тпл, а для сплавов твердых растворов возрастает до (0,5...0,6)Тпл.
Для углеродистых сталей с 0,08 – 0,2% С, часто подвергаемых холодной деформации (прокатке, штамповке, волочению), температура отжига находится в интервале 680 – 700 °С. Отжиг калиброванных прутков (холодная протяжка) из высокоуглеродистой легированной стали проводят при 680 – 740 °С в течение 0,5 – 1,5 ч.
Так, например, температура начала рекристаллизации свинца:
Tн.к.=(327+273)0,4-273=-33°C.
Таким образом, комнатная температура превышает температуру начала рекристаллизации свинца.
Вычертите диаграмму состояния железо-карбид железа, укажите структурные составляющие во всех областях диаграммы, опишите превращения и постройте кривую охлаждения (с применением правила фаз) для сплава, содержащего 0,4% С. Какова структура этого сплава при комнатной температуре и как такой сплав называется?
Первичная кристаллизация сплавов системы железо-углерод начинается по достижении температур, соответствующих линии ABCD (линии ликвидус), и заканчивается при температурах, образующих линию AHJECF (линию солидус).
При кристаллизации сплавов по линии АВ из жидкого раствора выделяются кристаллы твердого раствора углерода в α-железе (δ-раствор). Процесс кристаллизации сплавов с содержанием углерода до 0,1 % заканчивается по линии АН с образованием α (δ)-твердого раствора. На линии HJB протекает перитектическое превращение, в результате которого образуется твердый раствор углерода в γ-железе, т. е. аустенит. Процесс первичной кристаллизации сталей заканчивается по линии AHJE.
При температурах, соответствующих линии ВС, из жидкого раствора кристаллизуется аустенит. В сплавах, содержащих от 4,3 % до 6,67 % углерода, при температурах, соответствующих линии CD, начинают выделяться кристаллы цементита первичного. Цементит, кристаллизующийся из жидкой фазы, называется первичным. B точке С при температуре 1147°С и концентрации углерода в жидком растворе 4,3 % образуется эвтектика, которая называется ледебуритом. Эвтектическое превращение с образованием ледебурита можно записать формулой ЖР4,3Л[А2,14+Ц6,67]. Процесс первичной кристаллизации чугунов заканчивается по линии ECF образованием ледебурита.
Таким образом, структура чугунов ниже 1147°С будет: доэвтектических — аустенит+ледебурит, эвтектических — ледебурит и заэвтектических — цементит (первичный)+ледебурит.
Превращения, происходящие в твердом состоянии, называются вторичной кристаллизацией. Они связаны с переходом при охлаждении γ-железа в α-железо и распадом аустенита.
Линия GS соответствует температурам начала превращения аустенита в феррит. Ниже линии GS сплавы состоят из феррита и аустенита.
Линия ЕS показывает температуры начала выдел пня цементита из аустенита вследствие уменьшения растворимости углерода в аустените с понижением температуры. Цементит, выделяющийся из аустенита, называется вторичным цементитом.
В точке S при температуре 727°С и концентрации углерода в аустените 0,8 % образуется эвтектоидная смесь состоящая из феррита и цементита, которая называется перлитом. Перлит получается в результате одновременного выпадения из аустенита частиц феррита и цементита. Процесс превращения аустенита в перлит можно записать формулой А0,8П[Ф0,03+Ц6,67].
Линия PQ показывает на уменьшение растворимости углерода в феррите при охлаждении и выделении цементита, который называется третичным цементитом.
Следовательно, сплавы, содержащие менее 0,008% углерода (точкаQ), являются однофазными и имеют структуру чистого феррита, а сплавы, содержащие углерод от 0,008 до 0,03% – структуру феррит+цементит третичный и называются техническим железом.
Доэвтектоидные стали при температуре ниже 727ºС имеют структуру феррит+перлит и заэвтектоидные – перлит+цементит вторичный в виде сетки по границам зерен.
В доэвтектических чугунах в интервале температур 1147–727ºС при охлаждении из аустенита выделяется цементит вторичный, вследствие уменьшения растворимости углерода(линия ES). По достижении температуры 727ºС (линия PSK) аустенит, обедненный углеродом до 0,8% (точка S), превращаясь в перлит. Таким образом, после окончательного охлаждения структура доэвтектических чугунов состоит из перлита, цементита вторичного и ледебурита превращенного (перлит+цементит).
Структура эвтектических чугунов при температурах ниже 727ºС состоит из ледебурита превращенного. Заэвтектический чугун при температурах ниже 727ºС состоит из ледебурита превращенного и цементита первичного.
Правило фаз устанавливает зависимость между числом степеней свободы, числом компонентов и числом фаз и выражается уравнением:
C = K + 1 – Ф,
где С – число степеней свободы системы;
К – число компонентов, образующих систему;
1 – число внешних факторов (внешним фактором считаем только температуру, так как давление за исключением очень высокого мало влияет на фазовое равновесие сплавов в твердом и жидком состояниях);
Ф – число фаз, находящихся в равновесии.
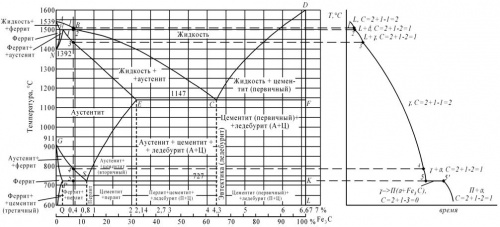
Рисунок 5: а – диаграмма железо-цементит,
б – кривая охлаждения для сплава, содержащего 0,4% углерода
Сплав железа с углеродом, содержащий 0,4% С, называется среднеуглеродистой сталью. Его структура при комнатной температуре феррит + перлит.
Используя диаграмму изотермического превращения аустенита, объясните, почему нельзя получить в стали чисто мартенситную структуру при охлаждении ее со скоростью меньше критической?
Чем больше скорость охлаждения и ниже температура распада аустенита (рисунок 6), тем дисперснее образующаяся феррито-цементитная структура. Следовательно, при небольшой скорости охлаждения υ1 образуется перлит, при большей υ2 – сорбит и еще большей υ3 –троостит.
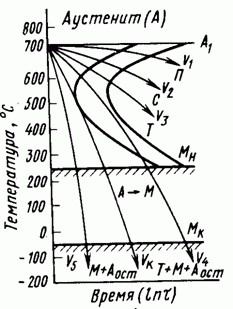
Рисунок 6 – Наложение кривых охлаждения на диаграмму изотермического распада аустенита
При высоких скоростях охлаждения (кривая υ4) часть аустенита переохлаждается до точки Мн и превращается в мартенсит. Структура в этом случае состоит из троостита и мартенсита.
При очень большой скорости охлаждения диффузионный распад аустенита становится вообще невозможным, и тогда аустенит переохлаждается до точки Мн и при дальнейшем охлаждении превращается в мартенсит (кривая υ5). Превращение аустенита в мартенсит не идет до конца, поэтому в закаленной стали наряду с мартенситом всегда присутствует в некотором количестве остаточный аустенит. Минимальную скорость охлаждения (кривая υк), при которой весь аустенит переохлаждается до точки Мн и превращается в мартенсит, называется критической скоростью закалки.
После термической обработки углеродистой стали получена структура цементит + мартенсит отпуска. Нанесите на диаграмму состояния железо-цементит ординату заданной стали (примерно) и обоснуйте температуру нагрева этой стали под закалку. Так же укажите температуру отпуска. Опишите превращения, которые произошли при термической обработке.
Структура цементит + мартенсит отпуска получается после закалки и низкого отпуска заэвтектоидной углеродистой стали. Рассмотрим на примере стали У12.
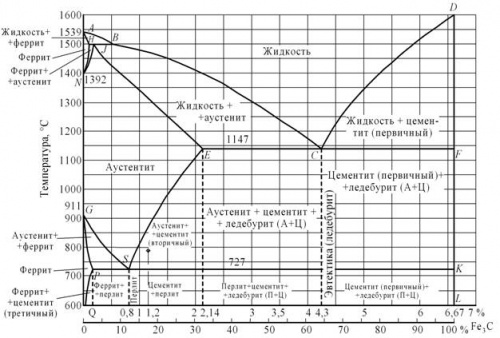
Диаграмма состояния железо-цементит представлена выше. При комнатной температуре сталь У12 имеет структуру цементита и перлита. До температуры Аc1 сохраняется исходная структура. При температуре Аc1 происходит превращение перлита в аустенит с содержанием углерода 0,8%. При нагреве выше точки Ас1 происходит растворение цементита в аустените (в соответствии с линией SE). Увеличение температуры выше точки Асm вызывает рост зерна аустенита.
Критические точки для стали У12: Аc1 = 730°С; Аcm = 820°С.
Для закалки заэвтектоидные стали нагревают на 50-70°С выше точки Ас1. Таким образом, температура нагрева под закалку составляет 780-800°С. При этих температурах в стали наряду с аустенитом имеется цементит. Поэтому после закалки в структуре заэвтектоидных сталей будет мартенсит с цементитом и небольшое количество остаточного аустенита.
Для снятия напряжений и стабилизации структуры после закалки изделия подвергают низкому отпуску при температуре 160–180 °С. Структура стали после низкого отпуска – отпущенный мартенсит + карбиды.
0 комментариев