Контрольная работа 1 Вариант 5
Что такое ограниченные и неограниченные твердые растворы? Каковы необходимые условия образования неограниченных твердых растворов?
По степеням растворимости компонентов различают твердые растворы:
– с неограниченной растворимостью компонентов;
– с ограниченной растворимостью компонентов.
При неограниченной растворимости компонентов кристаллическая решетка компонента растворителя по мере увеличения концентрации растворенного компонента плавно переходит в кристаллическую решетку растворенного компонента.
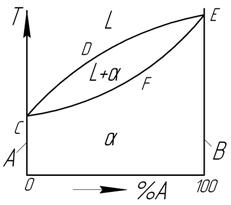
Рисунок 1 – Диаграмма состояний сплавов с неограниченной растворимостью компонентов
В этих сплавах компоненты в твердом состоянии неограниченно растворяются друг в друге; при этом образуется взаимный твердый раствор α. В данном случае чистые компоненты А и В не являются самостоятельными фазами системы, – они представляют собой предельные частные случаи твердого раствора α…
Однофазные области на диаграмме:
1) жидкость L – выше линии ликвидус CDE;
2) тв. раствор α – ниже линии солидус CFE.
Кристаллизация сплавов этого типа начинается на линии СDE и заканчивается на линии CFE постепенным переходом жидкого раствора L в твердые кристаллы α. Структуры всех сплавов этого типа при комнатной температура подобны: однородные кристаллы твердого раствора α, являющиеся единственной структурной составляющей в сплавах этого типа.
Для образования растворов с неограниченной растворимостью необходимо выполнение следующих условий:
– изоморфность (однотипность) кристаллических решеток компонентов;
– близость атомных радиусов компонентов R, которые не должны отличаться более чем на 8…13 %;
– близость физико-химических свойств подобных по строению валентных оболочек атомов.
Например, неограниченно растворяются в твердом состоянии следующие металлы с ГЦК-решеткой: Ag и Au (R=0,2%), Ni и Cu (R=2,7%), Ni и Rd (R=10,5%) и др., а также металлы с ОЦК решеткой: Mo и W (R=9,9%), V и Ti (R=2,0%). Такие металлы, как Na, Ca, R, Pb, Sr и другие, имеющие большой атомный диаметр, в Feγ, Cu, Ni нерастворимы.
Твердые растворы внедрения могут быть только ограниченной концентрации, поскольку число пор в решетке ограничено, а атомы основного компонента сохраняются в узлах решетки.
Сплавы с ограниченной растворимостью компонентов
В этих сплавах в твердом состоянии компоненты растворяются друг в друге с образованием твердых растворов α (В в А) и β (А в В), между которыми образуется эвтектика эвт(α+β).
Однофазные области на диаграмме:
1) жидкость L – выше линии ликвидус DCE;
2) тв. раствор α – область 0DFK0;
3) тв. раствор β – область NGE-100-N.
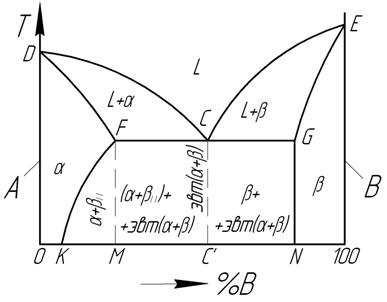
Рисунок 2 – Диаграмма состояний сплавов с ограниченной растворимостью
Линии верхней части диаграммы – образование кристаллов твердых растворов α и β.
Однако, в отличии от предыдущей диаграммы, предельное содержание компонента B в α ограничено: оно не может быть более М% В (в точке F). Аналогично, предельное содержание А в β не может быть более (100-N)% A (в точке G). То есть, в данном случае при растворении компонентов друг в друге образуются так называемые ограниченные твердые растворы α и β.
В общем случае, при снижении температуры после достижения предела растворимости (т.е. ниже уровня FCG) предельное содержание растворенного компонента в твердом растворе может изменяться. Эта зависимость предела растворимости от температуры твердого раствора α показана линией FK, а для β – линией GN. Видно, что с уменьшением температуры возможное содержание В в α уменьшается (от М% В до К% В при 0ºС). Поэтому, при охлаждении сплавов, содержащих от К % В до М % В, ниже линии FK из них будет выделяться оказавшаяся избыточная часть компонента В в виде кристаллов вторичного βII (доказывается правилом отрезков), и в области KFMK сплавы будут иметь фазовый состав α+βII.
В частном случае, показанном линией GN, предел растворимости А в β не зависит от температуры и кристаллы твердого раствора β, образовавшиеся на линии GE, будут охлаждаться до комнатной температуры без каких-либо внутренних изменений.
В средней части диаграммы сплавы кристаллизуются с образованием эвтектики на линии FCG. Эвтектика содержит С/% В и кристаллизуется по реакции: Lэвт–>эвт(α+β). В доэвтектических сплавах этой области в конечной структуре сплава будут присутствовать кроме эвтектики кристаллы (α+βII), а в заэвтектических – кристаллы β.
Структурные составляющие сплавов:
1) кристаллы α – область 0DFK0;
2) кристаллы β – область NGE-100-N;
3) кристаллы эвтектики эвт(α+β) – линия СС/.
Опишите сущность явления наклепа и примеры его практического использования.
Наклеп – изменение структуры и свойств металлического материала, вызванное пластической деформацией. Наклеп снижает пластичность и ударную вязкость, но увеличивает предел пропорциональность, предел текучести и твердость. Наклеп снижает сопротивление материала деформации противоположного знака. При поверхностном наклепе изменяется остаточное напряженное состояние в материале и повышается его усталостная прочность. Наклеп возникает при обработке металлов давлением (прокатка, волочение, ковка, штамповка), резанием, при обкатке роликами, при специальной обработке дробью.
Упрочнение металла в процессе пластической деформации (наклеп) объясняется увеличением числа дефектов кристаллического строения (дислокаций, вакансий, межузельных атомов). Повышение плотности дефектов кристаллического строения затрудняет движение отдельных новых дислокаций, а, следовательно, повышает сопротивление деформации и уменьшает пластичность. Наибольшее значение имеет увеличение плотности дислокаций, так как возникающее при этом между ними взаимодействие тормозит дальнейшее их перемещение.
Повышение долговечности деталей машин методом поверхностного пластического деформирования (ППД) или поверхностного наклепа широко используется в промышленности для повышения сопротивляемости малоцикловой и многоцикловой усталости деталей машин. На рисунке 3 приведены схемы различных ППД.
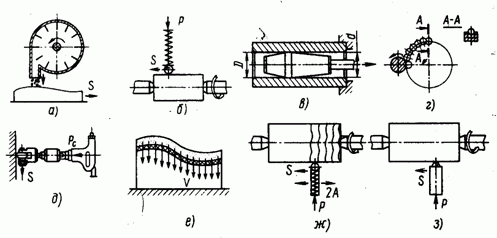
а – дробеструйная упрочняющая обработка; б – чистовая обработка – обкатываем шаром; в – обработка дорнованием; г – центробежно-шариковая чистовая обработка; д – обработка чеканкой; е – упрочнение взрывом; ж — упрочнение виброобкатыванием; з – алмазное выглаживание
Рисунок 3 – Схемы поверхностной пластической деформации
Поверхностное упрочнение достигается:
1) дробеструйным наклепом за счет кинетической энергии потока чугунной или стальной дроби; поток дроби на обрабатываемую поверхность направляется или скоростным потоком воздуха, или роторным дробеметом (рис. 3, а);
2) центробежно-шариковым наклепом за счет кинетической энергии стальных шариков (роликов), расположенных на периферии вращающегося диска; при вращении диска под действием центробежной силы шарики отбрасываются к периферии обода, взаимодействуют с обрабатываемой поверхностью и отбрасываются в глубь гнезда;
3) накатываем стальным шариком или роликом (60 HRC) (рис. 3, б); передача нагрузки на ролик может быть с жестким и упругим контактом между инструментом и обрабатываемой поверхностью;
4) алмазным выглаживанием оправкой с впаенным в рабочей части алмазом (рис. 3, з); оно позволяет получать блестящую поверхность с малой шероховатостью.
Вычертите диаграмму состояния железо – карбид железа, укажите структурные составляющие во всех областях диаграммы, опишите превращения и постройте кривую охлаждения (с применением правила фаз) для сплава, содержащего 1,1% С. Какова структура этого сплава при комнатной температуре и как такой сплав называется?
Первичная кристаллизация сплавов системы железо-углерод начинается по достижении температур, соответствующих линии ABCD (линии ликвидус), и заканчивается при температурах, образующих линию AHJECF (линию солидус).
При кристаллизации сплавов по линии АВ из жидкого раствора выделяются кристаллы твердого раствора углерода в α-железе (δ-раствор). Процесс кристаллизации сплавов с содержанием углерода до 0,1 % заканчивается по линии АН с образованием α (δ)-твердого раствора. На линии HJB протекает перитектическое превращение, в результате которого образуется твердый раствор углерода в γ-железе, т. е. аустенит. Процесс первичной кристаллизации сталей заканчивается по линии AHJE.
При температурах, соответствующих линии ВС, из жидкого раствора кристаллизуется аустенит. В сплавах, содержащих от 4,3 % до 6,67 % углерода, при температурах, соответствующих линии CD, начинают выделяться кристаллы цементита первичного. Цементит, кристаллизующийся из жидкой фазы, называется первичным. B точке С при температуре 1147°С и концентрации углерода в жидком растворе 4,3 % образуется эвтектика, которая называется ледебуритом. Эвтектическое превращение с образованием ледебурита можно записать формулой ЖР4,3Л[А2,14+Ц6,67]. Процесс первичной кристаллизации чугунов заканчивается по линии ECF образованием ледебурита.
Таким образом, структура чугунов ниже 1147°С будет: доэвтектических – аустенит+ледебурит, эвтектических – ледебурит и заэвтектических – цементит (первичный)+ледебурит.
Превращения, происходящие в твердом состоянии, называются вторичной кристаллизацией. Они связаны с переходом при охлаждении γ-железа в α-железо и распадом аустенита.
Линия GS соответствует температурам начала превращения аустенита в феррит. Ниже линии GS сплавы состоят из феррита и аустенита.
Линия ЕS показывает температуры начала выделения цементита из аустенита вследствие уменьшения растворимости углерода в аустените с понижением температуры. Цементит, выделяющийся из аустенита, называется вторичным цементитом.
В точке S при температуре 727°С и концентрации углерода в аустените 0,8 % образуется эвтектоидная смесь состоящая из феррита и цементита, которая называется перлитом. Перлит получается в результате одновременного выпадения из аустенита частиц феррита и цементита. Процесс превращения аустенита в перлит можно записать формулой А0,8П[Ф0,03+Ц6,67].
Линия PQ показывает на уменьшение растворимости углерода в феррите при охлаждении и выделении цементита, который называется третичным цементитом.
Следовательно, сплавы, содержащие менее 0,008% углерода (точкаQ), являются однофазными и имеют структуру чистого феррита, а сплавы, содержащие углерод от 0,008 до 0,03% – структуру феррит+цементит третичный и называются техническим железом.
Доэвтектоидные стали при температуре ниже 727ºС имеют структуру феррит+перлит и заэвтектоидные – перлит+цементит вторичный в виде сетки по границам зерен.
В доэвтектических чугунах в интервале температур 1147–727ºС при охлаждении из аустенита выделяется цементит вторичный, вследствие уменьшения растворимости углерода(линия ES). По достижении температуры 727ºС (линия PSK) аустенит, обедненный углеродом до 0,8% (точка S), превращаясь в перлит. Таким образом, после окончательного охлаждения структура доэвтектических чугунов состоит из перлита, цементита вторичного и ледебурита превращенного (перлит+цементит).
Структура эвтектических чугунов при температурах ниже 727ºС состоит из ледебурита превращенного. Заэвтектический чугун при температурах ниже 727ºС состоит из ледебурита превращенного и цементита первичного.
Правило фаз устанавливает зависимость между числом степеней свободы, числом компонентов и числом фаз и выражается уравнением:
C = K + 1 – Ф,
где С – число степеней свободы системы;
К – число компонентов, образующих систему;
1 – число внешних факторов (внешним фактором считаем только температуру, так как давление за исключением очень высокого мало влияет на фазовое равновесие сплавов в твердом и жидком состояниях);
Ф – число фаз, находящихся в равновесии.
Сплав железа с углеродом, содержащий 1,1 % С, называется заэвтектоидной сталью. Его структура при комнатной температуре – цементит (вторичный) + перлит.
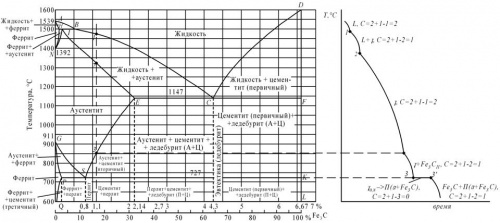
а) б)
Рисунок 4: а – диаграмма железо-цементит, б – кривая охлаждения для сплава, содержащего 1,1% углерода
При непрерывном охлаждении стали У8 получена структура троостит + мартенсит. Нанесите на диаграмму изотермического превращения аустенита кривую охлаждения, обеспечивающую получение данной структуры. Укажите интервалы температур превращений и опишите характер превращения в каждом из них.
Для получения структуры троостит + мартенсит в стали У8 необходимо нагреть ее до температуры выше точки А1, затем охладить так, чтобы пересечь кривую начала превращения аустенита в перлит в области троостита и, минуя кривую конца превращения, перейти в область мартенсита.
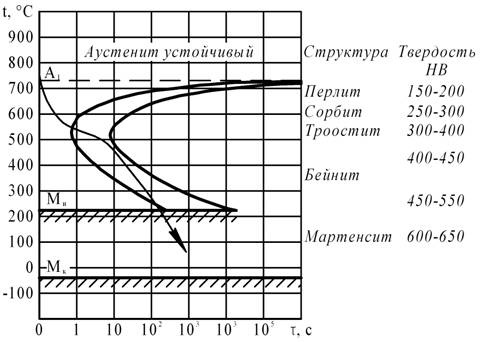
При нагреве стали У8 выше А1 перлит переходит в аустенит. При охлаждении со скоростью ниже критической (см. рис.) образуется ферритно-цементитная структура – троостит и мартенсит.
В зависимости от соотношения содержаний троостита и мартенсита в троостомартенсите (от скорости охлаждения) твердость стали может меняться от 300 НВ (при 100 % троостита) до 650 НВ (при 100 % мартенсита).
С помощью диаграммы железо-цементит, установите температуру полной и неполной закалки для стали 45 опишите структуру и свойства стали после каждого вида термической обработки.
Закалка доэвтектоидной стали заключается в нагреве стали до температуры выше критической (Ас3), в выдержке и последующем охлаждении со скоростью, превышающей критическую.
Температура точки Ас3 для стали 45 составляет 755°С.
Если доэвтектоидную сталь нагреть выше Ас1, но ниже Ас3 (неполная закалка), то в ее структуре после закалки наряду с мартенситом будут участки феррита. Присутствие феррита как мягкой составляющей снижает твердость стали после закалки. При нагреве до температуры 740°С (ниже точки Ас3) структура стали 45 – аустенит + феррит, после охлаждения со скоростью выше критической структура стали – мартенсит + феррит.
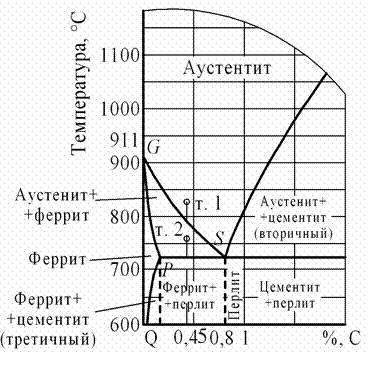
Доэвтектоидные стали для полной закалки следует нагревать до температуры на 30-50°С выше Ас3. Температура нагрева стали под полную закалку, таким образом, составляет 800-840°С. Структура стали 45 при температуре нагрева под закалку – аустенит, после охлаждения со скоростью выше критической – мартенсит.
По степеням растворимости компонентов различают твердые растворы:
– с неограниченной растворимостью компонентов;
– с ограниченной растворимостью компонентов.
При неограниченной растворимости компонентов кристаллическая решетка компонента растворителя по мере увеличения концентрации растворенного компонента плавно переходит в кристаллическую решетку растворенного компонента.
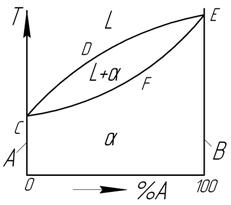
Рисунок 1 – Диаграмма состояний сплавов с неограниченной растворимостью компонентов
В этих сплавах компоненты в твердом состоянии неограниченно растворяются друг в друге; при этом образуется взаимный твердый раствор α. В данном случае чистые компоненты А и В не являются самостоятельными фазами системы, – они представляют собой предельные частные случаи твердого раствора α…
Однофазные области на диаграмме:
1) жидкость L – выше линии ликвидус CDE;
2) тв. раствор α – ниже линии солидус CFE.
Кристаллизация сплавов этого типа начинается на линии СDE и заканчивается на линии CFE постепенным переходом жидкого раствора L в твердые кристаллы α. Структуры всех сплавов этого типа при комнатной температура подобны: однородные кристаллы твердого раствора α, являющиеся единственной структурной составляющей в сплавах этого типа.
Для образования растворов с неограниченной растворимостью необходимо выполнение следующих условий:
– изоморфность (однотипность) кристаллических решеток компонентов;
– близость атомных радиусов компонентов R, которые не должны отличаться более чем на 8…13 %;
– близость физико-химических свойств подобных по строению валентных оболочек атомов.
Например, неограниченно растворяются в твердом состоянии следующие металлы с ГЦК-решеткой: Ag и Au (R=0,2%), Ni и Cu (R=2,7%), Ni и Rd (R=10,5%) и др., а также металлы с ОЦК решеткой: Mo и W (R=9,9%), V и Ti (R=2,0%). Такие металлы, как Na, Ca, R, Pb, Sr и другие, имеющие большой атомный диаметр, в Feγ, Cu, Ni нерастворимы.
Твердые растворы внедрения могут быть только ограниченной концентрации, поскольку число пор в решетке ограничено, а атомы основного компонента сохраняются в узлах решетки.
Сплавы с ограниченной растворимостью компонентов
В этих сплавах в твердом состоянии компоненты растворяются друг в друге с образованием твердых растворов α (В в А) и β (А в В), между которыми образуется эвтектика эвт(α+β).
Однофазные области на диаграмме:
1) жидкость L – выше линии ликвидус DCE;
2) тв. раствор α – область 0DFK0;
3) тв. раствор β – область NGE-100-N.
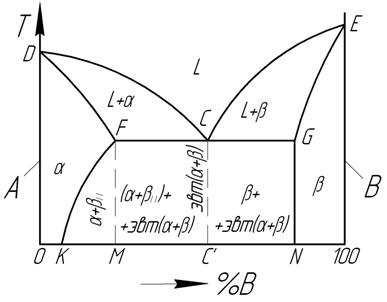
Рисунок 2 – Диаграмма состояний сплавов с ограниченной растворимостью
Линии верхней части диаграммы – образование кристаллов твердых растворов α и β.
Однако, в отличии от предыдущей диаграммы, предельное содержание компонента B в α ограничено: оно не может быть более М% В (в точке F). Аналогично, предельное содержание А в β не может быть более (100-N)% A (в точке G). То есть, в данном случае при растворении компонентов друг в друге образуются так называемые ограниченные твердые растворы α и β.
В общем случае, при снижении температуры после достижения предела растворимости (т.е. ниже уровня FCG) предельное содержание растворенного компонента в твердом растворе может изменяться. Эта зависимость предела растворимости от температуры твердого раствора α показана линией FK, а для β – линией GN. Видно, что с уменьшением температуры возможное содержание В в α уменьшается (от М% В до К% В при 0ºС). Поэтому, при охлаждении сплавов, содержащих от К % В до М % В, ниже линии FK из них будет выделяться оказавшаяся избыточная часть компонента В в виде кристаллов вторичного βII (доказывается правилом отрезков), и в области KFMK сплавы будут иметь фазовый состав α+βII.
В частном случае, показанном линией GN, предел растворимости А в β не зависит от температуры и кристаллы твердого раствора β, образовавшиеся на линии GE, будут охлаждаться до комнатной температуры без каких-либо внутренних изменений.
В средней части диаграммы сплавы кристаллизуются с образованием эвтектики на линии FCG. Эвтектика содержит С/% В и кристаллизуется по реакции: Lэвт–>эвт(α+β). В доэвтектических сплавах этой области в конечной структуре сплава будут присутствовать кроме эвтектики кристаллы (α+βII), а в заэвтектических – кристаллы β.
Структурные составляющие сплавов:
1) кристаллы α – область 0DFK0;
2) кристаллы β – область NGE-100-N;
3) кристаллы эвтектики эвт(α+β) – линия СС/.
Опишите сущность явления наклепа и примеры его практического использования.
Наклеп – изменение структуры и свойств металлического материала, вызванное пластической деформацией. Наклеп снижает пластичность и ударную вязкость, но увеличивает предел пропорциональность, предел текучести и твердость. Наклеп снижает сопротивление материала деформации противоположного знака. При поверхностном наклепе изменяется остаточное напряженное состояние в материале и повышается его усталостная прочность. Наклеп возникает при обработке металлов давлением (прокатка, волочение, ковка, штамповка), резанием, при обкатке роликами, при специальной обработке дробью.
Упрочнение металла в процессе пластической деформации (наклеп) объясняется увеличением числа дефектов кристаллического строения (дислокаций, вакансий, межузельных атомов). Повышение плотности дефектов кристаллического строения затрудняет движение отдельных новых дислокаций, а, следовательно, повышает сопротивление деформации и уменьшает пластичность. Наибольшее значение имеет увеличение плотности дислокаций, так как возникающее при этом между ними взаимодействие тормозит дальнейшее их перемещение.
Повышение долговечности деталей машин методом поверхностного пластического деформирования (ППД) или поверхностного наклепа широко используется в промышленности для повышения сопротивляемости малоцикловой и многоцикловой усталости деталей машин. На рисунке 3 приведены схемы различных ППД.
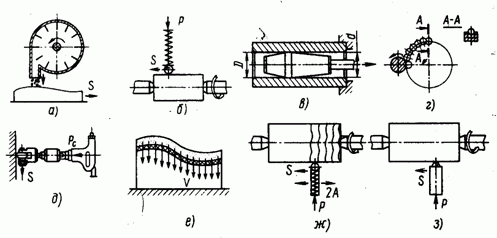
а – дробеструйная упрочняющая обработка; б – чистовая обработка – обкатываем шаром; в – обработка дорнованием; г – центробежно-шариковая чистовая обработка; д – обработка чеканкой; е – упрочнение взрывом; ж — упрочнение виброобкатыванием; з – алмазное выглаживание
Рисунок 3 – Схемы поверхностной пластической деформации
Поверхностное упрочнение достигается:
1) дробеструйным наклепом за счет кинетической энергии потока чугунной или стальной дроби; поток дроби на обрабатываемую поверхность направляется или скоростным потоком воздуха, или роторным дробеметом (рис. 3, а);
2) центробежно-шариковым наклепом за счет кинетической энергии стальных шариков (роликов), расположенных на периферии вращающегося диска; при вращении диска под действием центробежной силы шарики отбрасываются к периферии обода, взаимодействуют с обрабатываемой поверхностью и отбрасываются в глубь гнезда;
3) накатываем стальным шариком или роликом (60 HRC) (рис. 3, б); передача нагрузки на ролик может быть с жестким и упругим контактом между инструментом и обрабатываемой поверхностью;
4) алмазным выглаживанием оправкой с впаенным в рабочей части алмазом (рис. 3, з); оно позволяет получать блестящую поверхность с малой шероховатостью.
Вычертите диаграмму состояния железо – карбид железа, укажите структурные составляющие во всех областях диаграммы, опишите превращения и постройте кривую охлаждения (с применением правила фаз) для сплава, содержащего 1,1% С. Какова структура этого сплава при комнатной температуре и как такой сплав называется?
Первичная кристаллизация сплавов системы железо-углерод начинается по достижении температур, соответствующих линии ABCD (линии ликвидус), и заканчивается при температурах, образующих линию AHJECF (линию солидус).
При кристаллизации сплавов по линии АВ из жидкого раствора выделяются кристаллы твердого раствора углерода в α-железе (δ-раствор). Процесс кристаллизации сплавов с содержанием углерода до 0,1 % заканчивается по линии АН с образованием α (δ)-твердого раствора. На линии HJB протекает перитектическое превращение, в результате которого образуется твердый раствор углерода в γ-железе, т. е. аустенит. Процесс первичной кристаллизации сталей заканчивается по линии AHJE.
При температурах, соответствующих линии ВС, из жидкого раствора кристаллизуется аустенит. В сплавах, содержащих от 4,3 % до 6,67 % углерода, при температурах, соответствующих линии CD, начинают выделяться кристаллы цементита первичного. Цементит, кристаллизующийся из жидкой фазы, называется первичным. B точке С при температуре 1147°С и концентрации углерода в жидком растворе 4,3 % образуется эвтектика, которая называется ледебуритом. Эвтектическое превращение с образованием ледебурита можно записать формулой ЖР4,3Л[А2,14+Ц6,67]. Процесс первичной кристаллизации чугунов заканчивается по линии ECF образованием ледебурита.
Таким образом, структура чугунов ниже 1147°С будет: доэвтектических – аустенит+ледебурит, эвтектических – ледебурит и заэвтектических – цементит (первичный)+ледебурит.
Превращения, происходящие в твердом состоянии, называются вторичной кристаллизацией. Они связаны с переходом при охлаждении γ-железа в α-железо и распадом аустенита.
Линия GS соответствует температурам начала превращения аустенита в феррит. Ниже линии GS сплавы состоят из феррита и аустенита.
Линия ЕS показывает температуры начала выделения цементита из аустенита вследствие уменьшения растворимости углерода в аустените с понижением температуры. Цементит, выделяющийся из аустенита, называется вторичным цементитом.
В точке S при температуре 727°С и концентрации углерода в аустените 0,8 % образуется эвтектоидная смесь состоящая из феррита и цементита, которая называется перлитом. Перлит получается в результате одновременного выпадения из аустенита частиц феррита и цементита. Процесс превращения аустенита в перлит можно записать формулой А0,8П[Ф0,03+Ц6,67].
Линия PQ показывает на уменьшение растворимости углерода в феррите при охлаждении и выделении цементита, который называется третичным цементитом.
Следовательно, сплавы, содержащие менее 0,008% углерода (точкаQ), являются однофазными и имеют структуру чистого феррита, а сплавы, содержащие углерод от 0,008 до 0,03% – структуру феррит+цементит третичный и называются техническим железом.
Доэвтектоидные стали при температуре ниже 727ºС имеют структуру феррит+перлит и заэвтектоидные – перлит+цементит вторичный в виде сетки по границам зерен.
В доэвтектических чугунах в интервале температур 1147–727ºС при охлаждении из аустенита выделяется цементит вторичный, вследствие уменьшения растворимости углерода(линия ES). По достижении температуры 727ºС (линия PSK) аустенит, обедненный углеродом до 0,8% (точка S), превращаясь в перлит. Таким образом, после окончательного охлаждения структура доэвтектических чугунов состоит из перлита, цементита вторичного и ледебурита превращенного (перлит+цементит).
Структура эвтектических чугунов при температурах ниже 727ºС состоит из ледебурита превращенного. Заэвтектический чугун при температурах ниже 727ºС состоит из ледебурита превращенного и цементита первичного.
Правило фаз устанавливает зависимость между числом степеней свободы, числом компонентов и числом фаз и выражается уравнением:
C = K + 1 – Ф,
где С – число степеней свободы системы;
К – число компонентов, образующих систему;
1 – число внешних факторов (внешним фактором считаем только температуру, так как давление за исключением очень высокого мало влияет на фазовое равновесие сплавов в твердом и жидком состояниях);
Ф – число фаз, находящихся в равновесии.
Сплав железа с углеродом, содержащий 1,1 % С, называется заэвтектоидной сталью. Его структура при комнатной температуре – цементит (вторичный) + перлит.
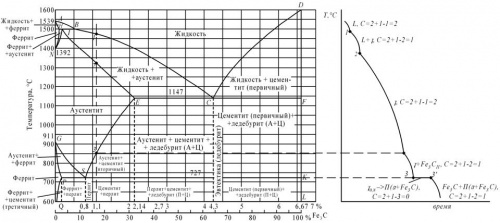
а) б)
Рисунок 4: а – диаграмма железо-цементит, б – кривая охлаждения для сплава, содержащего 1,1% углерода
При непрерывном охлаждении стали У8 получена структура троостит + мартенсит. Нанесите на диаграмму изотермического превращения аустенита кривую охлаждения, обеспечивающую получение данной структуры. Укажите интервалы температур превращений и опишите характер превращения в каждом из них.
Для получения структуры троостит + мартенсит в стали У8 необходимо нагреть ее до температуры выше точки А1, затем охладить так, чтобы пересечь кривую начала превращения аустенита в перлит в области троостита и, минуя кривую конца превращения, перейти в область мартенсита.
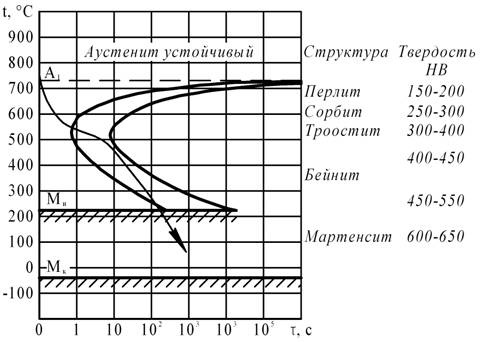
При нагреве стали У8 выше А1 перлит переходит в аустенит. При охлаждении со скоростью ниже критической (см. рис.) образуется ферритно-цементитная структура – троостит и мартенсит.
В зависимости от соотношения содержаний троостита и мартенсита в троостомартенсите (от скорости охлаждения) твердость стали может меняться от 300 НВ (при 100 % троостита) до 650 НВ (при 100 % мартенсита).
С помощью диаграммы железо-цементит, установите температуру полной и неполной закалки для стали 45 опишите структуру и свойства стали после каждого вида термической обработки.
Закалка доэвтектоидной стали заключается в нагреве стали до температуры выше критической (Ас3), в выдержке и последующем охлаждении со скоростью, превышающей критическую.
Температура точки Ас3 для стали 45 составляет 755°С.
Если доэвтектоидную сталь нагреть выше Ас1, но ниже Ас3 (неполная закалка), то в ее структуре после закалки наряду с мартенситом будут участки феррита. Присутствие феррита как мягкой составляющей снижает твердость стали после закалки. При нагреве до температуры 740°С (ниже точки Ас3) структура стали 45 – аустенит + феррит, после охлаждения со скоростью выше критической структура стали – мартенсит + феррит.
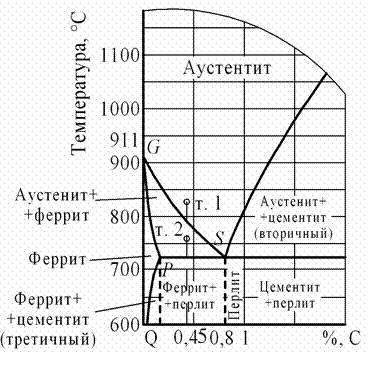
Доэвтектоидные стали для полной закалки следует нагревать до температуры на 30-50°С выше Ас3. Температура нагрева стали под полную закалку, таким образом, составляет 800-840°С. Структура стали 45 при температуре нагрева под закалку – аустенит, после охлаждения со скоростью выше критической – мартенсит.
0 комментариев