Контрольная работа 1 Вариант 8
В чем сущность процесса модифицирования? Приведите пример использования модификаторов для повышения свойств литейных алюминиевых сплавов.
Модифицирование – использование специально вводимых в жидкий металл примесей (модификаторов) для получения мелкого зерна. Эти примеси, практически не изменяя химического состава сплава, вызывают при кристаллизации измельчение зерна и в итоге улучшение механических свойств. Так, например, при модифицировании магниевых сплавов зерно уменьшается с 0,2-0,3 до 0,01-0,02 мм. При литье слитков в фасонных отливках модифицирование чаще проводят введением в расплав добавок, которые образуют тугоплавкие соединения (карбиды, нитриды, оксиды), кристаллизирующиеся в первую очередь. Выделяясь в виде мельчайших частиц, эти соединения служат зародышами образующихся при затвердевании кристаллов (модификаторы I рода). В качестве модификаторов при модифицировании алюминиевых сплавов применяют Ti, V, Zr; стали – Al, V, Ti. Иногда используют растворимые в жидком металле модификаторы (модификаторы II рода), избирательно адсорбирующиеся на кристаллическом зародыше, которые снижают межфазовое поверхностное натяжение и затрудняют рост кристаллитов. Для алюминиевых сплавов в качестве модификаторов второго рода используют Li, Na, K, для стали – редкоземельные элементы.
Для измельчения структуры эвтектики и устранения избыточных кристаллов кремния силумины модифицируют натрием (0,05-0,08%) путем присадки к расплаву смеси солей 67% NaF и 33% NaCl. В присутствии натрия происходит смещение линий диаграммы состояния и заэвтектический (эвтектический) сплав АЛ2 (11-13% Si) становится доэвтектическим. В этом случае в структуре сплава вместо избыточного кремния появляются кристаллы α-твердого раствора. В процессе затвердевания кристаллы кремния обволакиваются пленкой силицида натрия Na2Si, которая затрудняет их рост. Такие изменения структуры улучшают механические свойства.
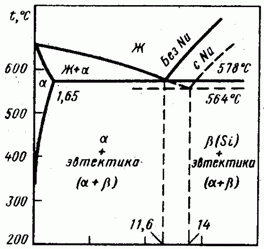
Рисунок 1 – Диаграмма состояния Al-Si
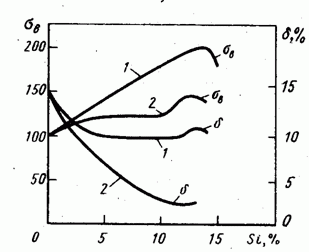
Рисунок 2 – Механические свойства сплава Al-Si (1 – после модифицирования; 2 – до модифицирования)
В чем различие между холодной и горячей пластической деформацией? Опишите особенности обоих видов деформации.
В зависимости от соотношения температуры деформации и температуры рекристаллизации различают холодную и горячую деформации. Холодной деформацией называют такую, которую проводят при температуре ниже температуры рекристаллизации. Поэтому холодная деформация сопровождается упрочнением (наклепом) металла.
Деформацию называют горячей, если ее проводят при температуре выше температуры рекристаллизации для получения полностью рекристаллизованной структуры.
При этих температурах деформация также вызывает упрочнение «горячий наклеп», которое полностью или частично снимается рекристаллизацией, протекающей при температурах обработки и при последующем охлаждении. В отличие от статической полигонизации и рекристаллизации, процессы полигонизации и рекристаллизации, происходящие в период деформации, называют динамическими.
При горячей обработке давлением (прокатке, прессовании, ковке, штамповке и т. д.) упрочнение в результате наклепа (повышение плотности дислокаций) непосредственно в процессе деформации непрерывно чередуется с процессом разупрочнения (уменьшением плотности дислокаций) при динамической полигонизации и рекристаллизации во время деформации и охлаждения. В этом основное отличие динамической полигонизации и рекристаллизации от статической.
Горячую деформацию в зависимости от состава сплава и скорости деформации обычно проводят при температурах (0,7-0,75) Тпл.
Когда металл после деформации имеет частично рекристаллизованную рекристаллизованную структуру, то такую обработку правильнее называть неполной горячей, или теплой, деформацией.
Вычертите диаграмму состояния железо – карбид железа, укажите структурные составляющие во всех областях диаграммы, опишите превращения и постройте кривую охлаждения (с применением правила фаз) для сплава, содержащего 5,0% С. Какова структура этого сплава при комнатной температуре и как такой сплав называется?
Первичная кристаллизация сплавов системы железо-углерод начинается по достижении температур, соответствующих линии ABCD (линии ликвидус), и заканчивается при температурах, образующих линию AHJECF (линию солидус).
При кристаллизации сплавов по линии АВ из жидкого раствора выделяются кристаллы твердого раствора углерода в α-железе (δ-раствор). Процесс кристаллизации сплавов с содержанием углерода до 0,1 % заканчивается по линии АН с образованием α (δ)-твердого раствора. На линии HJB протекает перитектическое превращение, в результате которого образуется твердый раствор углерода в γ-железе, т. е. аустенит. Процесс первичной кристаллизации сталей заканчивается по линии AHJE.
При температурах, соответствующих линии ВС, из жидкого раствора кристаллизуется аустенит. В сплавах, содержащих от 4,3 % до 6,67 % углерода, при температурах, соответствующих линии CD, начинают выделяться кристаллы цементита первичного. Цементит, кристаллизующийся из жидкой фазы, называется первичным. B точке С при температуре 1147°С и концентрации углерода в жидком растворе 4,3 % образуется эвтектика, которая называется ледебуритом. Эвтектическое превращение с образованием ледебурита можно записать формулой ЖР4,3Л[А2,14+Ц6,67]. Процесс первичной кристаллизации чугунов заканчивается по линии ECF образованием ледебурита.
Таким образом, структура чугунов ниже 1147°С будет: доэвтектических — аустенит + ледебурит, эвтектических — ледебурит и заэвтектических — цементит (первичный)+ледебурит.
Превращения, происходящие в твердом состоянии, называются вторичной кристаллизацией. Они связаны с переходом при охлаждении γ-железа в α-железо и распадом аустенита.
Линия GS соответствует температурам начала превращения аустенита в феррит. Ниже линии GS сплавы состоят из феррита и аустенита.
Линия ЕS показывает температуры начала выделения цементита из аустенита вследствие уменьшения растворимости углерода в аустените с понижением температуры. Цементит, выделяющийся из аустенита, называется вторичным цементитом.
В точке S при температуре 727°С и концентрации углерода в аустените 0,8 % образуется эвтектоидная смесь состоящая из феррита и цементита, которая называется перлитом. Перлит получается в результате одновременного выпадения из аустенита частиц феррита и цементита. Процесс превращения аустенита в перлит можно записать формулой А0,8П[Ф0,03+Ц6,67].
Линия PQ показывает на уменьшение растворимости углерода в феррите при охлаждении и выделении цементита, который называется третичным цементитом.
Следовательно, сплавы, содержащие менее 0,008% углерода (точка Q), являются однофазными и имеют структуру чистого феррита, а сплавы, содержащие углерод от 0,008 до 0,03% – структуру феррит + цементит третичный и называются техническим железом.
Доэвтектоидные стали при температуре ниже 727ºС имеют структуру феррит + перлит и заэвтектоидные – перлит + цементит вторичный в виде сетки по границам зерен.
В доэвтектических чугунах в интервале температур 1147–727ºС при охлаждении из аустенита выделяется цементит вторичный, вследствие уменьшения растворимости углерода (линия ES). По достижении температуры 727ºС (линия PSK) аустенит, обедненный углеродом до 0,8% (точка S), превращаясь в перлит. Таким образом, после окончательного охлаждения структура доэвтектических чугунов состоит из перлита, цементита вторичного и ледебурита превращенного (перлит + цементит).
Структура эвтектических чугунов при температурах ниже 727ºС состоит из ледебурита превращенного. Заэвтектический чугун при температурах ниже 727ºС состоит из ледебурита превращенного и цементита первичного.
Правило фаз устанавливает зависимость между числом степеней свободы, числом компонентов и числом фаз и выражается уравнением:
C = K + 1 – Ф,
где С – число степеней свободы системы;
К – число компонентов, образующих систему;
1 – число внешних факторов (внешним фактором считаем только температуру, так как давление за исключением очень высокого мало влияет на фазовое равновесие сплавов в твердом и жидком состояниях);
Ф – число фаз, находящихся в равновесии.
Сплав железа с углеродом, содержащий 5,0%С, называется заэвтектическим чугуном. Его структура при комнатной температуре – цементит (первичный) + ледебурит (перлит + цементит).
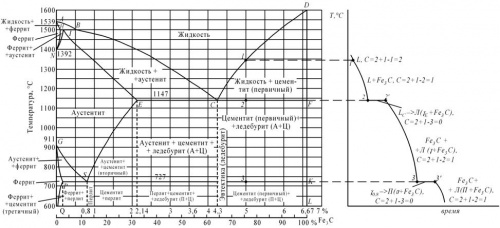
а) б)
Рисунок 1: а-диаграмма железо-цементит, б-кривая охлаждения для сплава, содержащего 5,0% углерода
Углеродистые стали 35 и У8 после закалки и отпуска имеют структуру мартенсит отпуска и твердость: первая 45 HRC, вторая – 60 HRC. Используя диаграмму состояния железо – карбид железа и учитывая превращения, происходящие при отпуске, укажите температуру закалки и температуру отпуска для каждой стали. Опишите превращения, происходящие в этих сталях в процессе закалки и отпуска, объясните, почему сталь У8 имеет большую твердость, чем сталь 45.
Закалка – термическая обработка – заключается в нагреве стали до температуры выше критической (А3 для доэвтектоидной и А1 – для заэвтектоидной сталей) или температуры растворения избыточных фаз, в выдержке и последующем охлаждении со скоростью, превышающей критическую. В результате закалки из аустенита образуется неустойчивая, метастабильная структура мартенсит.
Для стали 35 температура АС3 = 810°С, поэтому температуру закалки выбираем 850-870°С. Для стали У8 критическая точка АС1 = 720°С, поэтому температура закалки равна 770-790°С.
Низкий отпуск снижает закалочные макронапряжения, мартенсит закалки переводится в отпущенный мартенсит, повышается прочность и немного улучшается вязкость без заметного снижения твердости. При отпуске уменьшается степень тетрагональности кристаллической решетки мартенсита вследствие выделения из нее углерода в виде ε-карбида.
Низкий отпуск для обеих сталей проводим при температуре 160 – 200ºС. Более высокие температуры применять не следует, так как это приводит к снижению твердости, статической и усталостной прочности, износостойкости изделий. Структура стали 35 – отпущенный мартенсит, стали У8 – отпущенный мартенсит + карбиды.
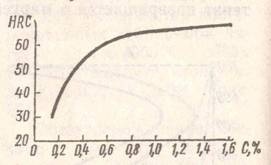
Рисунок 5 – Твердость мартенсита в зависимости от содержания углерода
Из рисунка 5 видно, что сталь У8 (0,8-0,9%С) после закалки имеет большую твердость, чем сталь 35 (0,32-0,40%С).
Сталь 40 подвергалась закалке от температур 760 и 840°С. С помощью диаграммы состояния железо-цементит укажите, какие структуры образуются в каждом случае. Объясните причины образования разных структур и рекомендуйте оптимальный режим нагрева под закалку данной стали.
Закалка доэвтектоидной стали заключается в нагреве стали до температуры выше критической (Ас3), в выдержке и последующем охлаждении со скоростью, превышающей критическую.
Температура точки Ас3 для стали 40 составляет 790°С.
Если доэвтектоидную сталь нагреть выше Ас1, но ниже Ас3, то в ее структуре после закалки наряду с мартенситом будут участки феррита. Присутствие феррита как мягкой составляющей снижает твердость стали после закалки. При нагреве до температуры 760°С (ниже точки Ас3) структура стали 40 – аустенит + феррит, после охлаждения со скоростью выше критической структура стали – мартенсит + феррит.
Аустенит неоднороден по химическому составу. В тех местах, где были пластинки цементита, аустенит богаче углеродом, а где пластинки феррита – беднее. Поэтому при термической обработке для выравнивания химического состава зерен аустенита сталь нагревают немного выше критической точки Ас3 (на 30-50°С) и выдерживают некоторое время при этой температуре. Процесс аустенизации идет тем быстрее, чем выше превышение фактической температуры нагрева под закалку относительно температуры Ас3. Доэвтектоидные стали для полной закалки следует нагревать до температуры на 30-50°С выше Ас3. Температура нагрева стали 40 под полную закалку, таким образом, составляет 820-840°С. Структура стали 40 при температуре нагрева под закалку – аустенит, после охлаждения со скоростью выше критической – мартенсит.
Если нагреть выше этой температуры мелкие зерна аустенита начинают соединяться между собой и чем выше температура нагрева, тем интенсивнее увеличиваются размеры. Крупнозернистая структура ухудшает механические свойства стали.
Модифицирование – использование специально вводимых в жидкий металл примесей (модификаторов) для получения мелкого зерна. Эти примеси, практически не изменяя химического состава сплава, вызывают при кристаллизации измельчение зерна и в итоге улучшение механических свойств. Так, например, при модифицировании магниевых сплавов зерно уменьшается с 0,2-0,3 до 0,01-0,02 мм. При литье слитков в фасонных отливках модифицирование чаще проводят введением в расплав добавок, которые образуют тугоплавкие соединения (карбиды, нитриды, оксиды), кристаллизирующиеся в первую очередь. Выделяясь в виде мельчайших частиц, эти соединения служат зародышами образующихся при затвердевании кристаллов (модификаторы I рода). В качестве модификаторов при модифицировании алюминиевых сплавов применяют Ti, V, Zr; стали – Al, V, Ti. Иногда используют растворимые в жидком металле модификаторы (модификаторы II рода), избирательно адсорбирующиеся на кристаллическом зародыше, которые снижают межфазовое поверхностное натяжение и затрудняют рост кристаллитов. Для алюминиевых сплавов в качестве модификаторов второго рода используют Li, Na, K, для стали – редкоземельные элементы.
Для измельчения структуры эвтектики и устранения избыточных кристаллов кремния силумины модифицируют натрием (0,05-0,08%) путем присадки к расплаву смеси солей 67% NaF и 33% NaCl. В присутствии натрия происходит смещение линий диаграммы состояния и заэвтектический (эвтектический) сплав АЛ2 (11-13% Si) становится доэвтектическим. В этом случае в структуре сплава вместо избыточного кремния появляются кристаллы α-твердого раствора. В процессе затвердевания кристаллы кремния обволакиваются пленкой силицида натрия Na2Si, которая затрудняет их рост. Такие изменения структуры улучшают механические свойства.
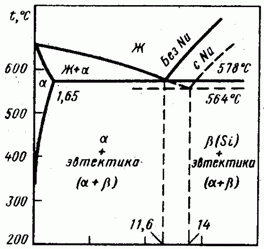
Рисунок 1 – Диаграмма состояния Al-Si
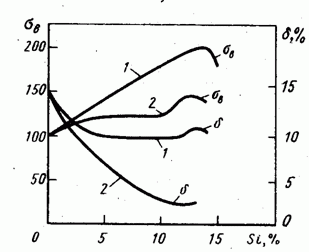
Рисунок 2 – Механические свойства сплава Al-Si (1 – после модифицирования; 2 – до модифицирования)
В чем различие между холодной и горячей пластической деформацией? Опишите особенности обоих видов деформации.
В зависимости от соотношения температуры деформации и температуры рекристаллизации различают холодную и горячую деформации. Холодной деформацией называют такую, которую проводят при температуре ниже температуры рекристаллизации. Поэтому холодная деформация сопровождается упрочнением (наклепом) металла.
Деформацию называют горячей, если ее проводят при температуре выше температуры рекристаллизации для получения полностью рекристаллизованной структуры.
При этих температурах деформация также вызывает упрочнение «горячий наклеп», которое полностью или частично снимается рекристаллизацией, протекающей при температурах обработки и при последующем охлаждении. В отличие от статической полигонизации и рекристаллизации, процессы полигонизации и рекристаллизации, происходящие в период деформации, называют динамическими.
При горячей обработке давлением (прокатке, прессовании, ковке, штамповке и т. д.) упрочнение в результате наклепа (повышение плотности дислокаций) непосредственно в процессе деформации непрерывно чередуется с процессом разупрочнения (уменьшением плотности дислокаций) при динамической полигонизации и рекристаллизации во время деформации и охлаждения. В этом основное отличие динамической полигонизации и рекристаллизации от статической.
Горячую деформацию в зависимости от состава сплава и скорости деформации обычно проводят при температурах (0,7-0,75) Тпл.
Когда металл после деформации имеет частично рекристаллизованную рекристаллизованную структуру, то такую обработку правильнее называть неполной горячей, или теплой, деформацией.
Вычертите диаграмму состояния железо – карбид железа, укажите структурные составляющие во всех областях диаграммы, опишите превращения и постройте кривую охлаждения (с применением правила фаз) для сплава, содержащего 5,0% С. Какова структура этого сплава при комнатной температуре и как такой сплав называется?
Первичная кристаллизация сплавов системы железо-углерод начинается по достижении температур, соответствующих линии ABCD (линии ликвидус), и заканчивается при температурах, образующих линию AHJECF (линию солидус).
При кристаллизации сплавов по линии АВ из жидкого раствора выделяются кристаллы твердого раствора углерода в α-железе (δ-раствор). Процесс кристаллизации сплавов с содержанием углерода до 0,1 % заканчивается по линии АН с образованием α (δ)-твердого раствора. На линии HJB протекает перитектическое превращение, в результате которого образуется твердый раствор углерода в γ-железе, т. е. аустенит. Процесс первичной кристаллизации сталей заканчивается по линии AHJE.
При температурах, соответствующих линии ВС, из жидкого раствора кристаллизуется аустенит. В сплавах, содержащих от 4,3 % до 6,67 % углерода, при температурах, соответствующих линии CD, начинают выделяться кристаллы цементита первичного. Цементит, кристаллизующийся из жидкой фазы, называется первичным. B точке С при температуре 1147°С и концентрации углерода в жидком растворе 4,3 % образуется эвтектика, которая называется ледебуритом. Эвтектическое превращение с образованием ледебурита можно записать формулой ЖР4,3Л[А2,14+Ц6,67]. Процесс первичной кристаллизации чугунов заканчивается по линии ECF образованием ледебурита.
Таким образом, структура чугунов ниже 1147°С будет: доэвтектических — аустенит + ледебурит, эвтектических — ледебурит и заэвтектических — цементит (первичный)+ледебурит.
Превращения, происходящие в твердом состоянии, называются вторичной кристаллизацией. Они связаны с переходом при охлаждении γ-железа в α-железо и распадом аустенита.
Линия GS соответствует температурам начала превращения аустенита в феррит. Ниже линии GS сплавы состоят из феррита и аустенита.
Линия ЕS показывает температуры начала выделения цементита из аустенита вследствие уменьшения растворимости углерода в аустените с понижением температуры. Цементит, выделяющийся из аустенита, называется вторичным цементитом.
В точке S при температуре 727°С и концентрации углерода в аустените 0,8 % образуется эвтектоидная смесь состоящая из феррита и цементита, которая называется перлитом. Перлит получается в результате одновременного выпадения из аустенита частиц феррита и цементита. Процесс превращения аустенита в перлит можно записать формулой А0,8П[Ф0,03+Ц6,67].
Линия PQ показывает на уменьшение растворимости углерода в феррите при охлаждении и выделении цементита, который называется третичным цементитом.
Следовательно, сплавы, содержащие менее 0,008% углерода (точка Q), являются однофазными и имеют структуру чистого феррита, а сплавы, содержащие углерод от 0,008 до 0,03% – структуру феррит + цементит третичный и называются техническим железом.
Доэвтектоидные стали при температуре ниже 727ºС имеют структуру феррит + перлит и заэвтектоидные – перлит + цементит вторичный в виде сетки по границам зерен.
В доэвтектических чугунах в интервале температур 1147–727ºС при охлаждении из аустенита выделяется цементит вторичный, вследствие уменьшения растворимости углерода (линия ES). По достижении температуры 727ºС (линия PSK) аустенит, обедненный углеродом до 0,8% (точка S), превращаясь в перлит. Таким образом, после окончательного охлаждения структура доэвтектических чугунов состоит из перлита, цементита вторичного и ледебурита превращенного (перлит + цементит).
Структура эвтектических чугунов при температурах ниже 727ºС состоит из ледебурита превращенного. Заэвтектический чугун при температурах ниже 727ºС состоит из ледебурита превращенного и цементита первичного.
Правило фаз устанавливает зависимость между числом степеней свободы, числом компонентов и числом фаз и выражается уравнением:
C = K + 1 – Ф,
где С – число степеней свободы системы;
К – число компонентов, образующих систему;
1 – число внешних факторов (внешним фактором считаем только температуру, так как давление за исключением очень высокого мало влияет на фазовое равновесие сплавов в твердом и жидком состояниях);
Ф – число фаз, находящихся в равновесии.
Сплав железа с углеродом, содержащий 5,0%С, называется заэвтектическим чугуном. Его структура при комнатной температуре – цементит (первичный) + ледебурит (перлит + цементит).
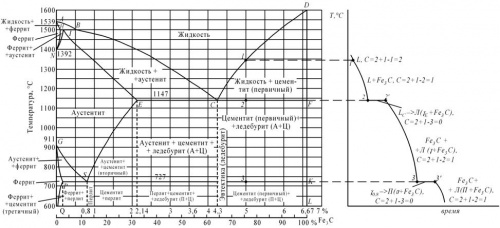
а) б)
Рисунок 1: а-диаграмма железо-цементит, б-кривая охлаждения для сплава, содержащего 5,0% углерода
Углеродистые стали 35 и У8 после закалки и отпуска имеют структуру мартенсит отпуска и твердость: первая 45 HRC, вторая – 60 HRC. Используя диаграмму состояния железо – карбид железа и учитывая превращения, происходящие при отпуске, укажите температуру закалки и температуру отпуска для каждой стали. Опишите превращения, происходящие в этих сталях в процессе закалки и отпуска, объясните, почему сталь У8 имеет большую твердость, чем сталь 45.
Закалка – термическая обработка – заключается в нагреве стали до температуры выше критической (А3 для доэвтектоидной и А1 – для заэвтектоидной сталей) или температуры растворения избыточных фаз, в выдержке и последующем охлаждении со скоростью, превышающей критическую. В результате закалки из аустенита образуется неустойчивая, метастабильная структура мартенсит.
Для стали 35 температура АС3 = 810°С, поэтому температуру закалки выбираем 850-870°С. Для стали У8 критическая точка АС1 = 720°С, поэтому температура закалки равна 770-790°С.
Низкий отпуск снижает закалочные макронапряжения, мартенсит закалки переводится в отпущенный мартенсит, повышается прочность и немного улучшается вязкость без заметного снижения твердости. При отпуске уменьшается степень тетрагональности кристаллической решетки мартенсита вследствие выделения из нее углерода в виде ε-карбида.
Низкий отпуск для обеих сталей проводим при температуре 160 – 200ºС. Более высокие температуры применять не следует, так как это приводит к снижению твердости, статической и усталостной прочности, износостойкости изделий. Структура стали 35 – отпущенный мартенсит, стали У8 – отпущенный мартенсит + карбиды.
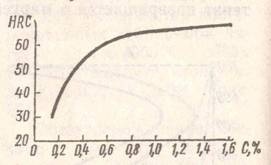
Рисунок 5 – Твердость мартенсита в зависимости от содержания углерода
Из рисунка 5 видно, что сталь У8 (0,8-0,9%С) после закалки имеет большую твердость, чем сталь 35 (0,32-0,40%С).
Сталь 40 подвергалась закалке от температур 760 и 840°С. С помощью диаграммы состояния железо-цементит укажите, какие структуры образуются в каждом случае. Объясните причины образования разных структур и рекомендуйте оптимальный режим нагрева под закалку данной стали.
Закалка доэвтектоидной стали заключается в нагреве стали до температуры выше критической (Ас3), в выдержке и последующем охлаждении со скоростью, превышающей критическую.
Температура точки Ас3 для стали 40 составляет 790°С.
Если доэвтектоидную сталь нагреть выше Ас1, но ниже Ас3, то в ее структуре после закалки наряду с мартенситом будут участки феррита. Присутствие феррита как мягкой составляющей снижает твердость стали после закалки. При нагреве до температуры 760°С (ниже точки Ас3) структура стали 40 – аустенит + феррит, после охлаждения со скоростью выше критической структура стали – мартенсит + феррит.
Аустенит неоднороден по химическому составу. В тех местах, где были пластинки цементита, аустенит богаче углеродом, а где пластинки феррита – беднее. Поэтому при термической обработке для выравнивания химического состава зерен аустенита сталь нагревают немного выше критической точки Ас3 (на 30-50°С) и выдерживают некоторое время при этой температуре. Процесс аустенизации идет тем быстрее, чем выше превышение фактической температуры нагрева под закалку относительно температуры Ас3. Доэвтектоидные стали для полной закалки следует нагревать до температуры на 30-50°С выше Ас3. Температура нагрева стали 40 под полную закалку, таким образом, составляет 820-840°С. Структура стали 40 при температуре нагрева под закалку – аустенит, после охлаждения со скоростью выше критической – мартенсит.
Если нагреть выше этой температуры мелкие зерна аустенита начинают соединяться между собой и чем выше температура нагрева, тем интенсивнее увеличиваются размеры. Крупнозернистая структура ухудшает механические свойства стали.
0 комментариев