Контрольная работа 1 Вариант 11
Опишите линейные несовершенства кристаллического строения. Как они влияют на свойства металлов и сплавов
В любом реальном кристалле всегда имеются дефекты строения. Линейные несовершенства имеют малые размеры в двух измерениях и большую протяженность в третьем. Эти несовершенства называются дислокациями.
Краевая дислокация представляет собой линию, вдоль которой обрывается внутри кристалла край “лишней“ полуплоскости (рисунок 1)
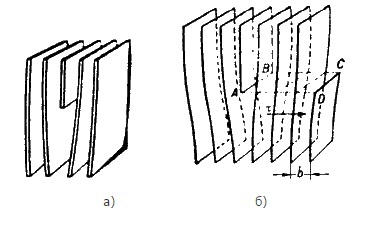
Рисунок 1 – Краевая дислокация (а) и механизм ее образования (б)
Неполная плоскость называется экстраплоскостью.
Большинство дислокаций образуются путем сдвигового механизма. Ее образование можно описать при помощи следующей операции. Надрезать кристалл по плоскости АВСD, сдвинуть нижнюю часть относительно верхней на один период решетки в направлении, перпендикулярном АВ, а затем вновь сблизить атомы на краях разреза внизу.
Наибольшие искажения в расположении атомов в кристалле имеют место вблизи нижнего края экстраплоскости. Вправо и влево от края экстраплоскости эти искажения малы (несколько периодов решетки), а вдоль края экстраплоскости искажения простираются через весь кристалл и могут быть очень велики (тысячи периодов решетки) (рисунок 2).
Если экстраплоскость находится в верхней части кристалла, то краевая дислокация – положительная (┴), если в нижней, то – отрицательная (┬). Дислокации одного знака отталкиваются, а противоположные притягиваются.
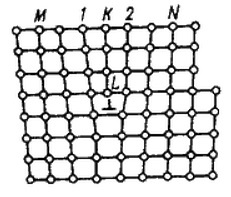
Рисунок 2 – Искажения в кристаллической решетке при наличии краевой дислокации
Другой тип дислокаций был описан Бюргерсом, и получил название винтовая дислокация
Винтовая дислокация получена при помощи частичного сдвига по плоскости Q вокруг линии EF (рисунок 3) На поверхности кристалла образуется ступенька, проходящая от точки Е до края кристалла. Такой частичный сдвиг нарушает параллельность атомных слоев, кристалл превращается в одну атомную плоскость, закрученную по винту в виде полого геликоида вокруг линии EF, которая представляет границу, отделяющую часть плоскости скольжения, где сдвиг уже произошел, от части, где сдвиг не начинался. Вдоль линии EF наблюдается макроскопический характер области несовершенства, в других направлениях ее размеры составляют несколько периодов.
Если переход от верхних горизонтов к нижним осуществляется поворотом по часовой стрелке, то дислокация правая, а если поворотом против часовой стрелки – левая.
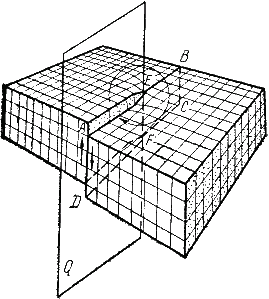
Рисунок 3 – Механизм образования винтовой дислокации
Винтовая дислокация не связана с какой-либо плоскостью скольжения, она может перемещаться по любой плоскости, проходящей через линию дислокации. Вакансии и дислоцированные атомы к винтовой дислокации не стекают.
В процессе кристаллизации атомы вещества, выпадающие из пара или раствора, легко присоединяются к ступеньке, что приводит к спиральному механизму роста кристалла.
Линии дислокаций не могут обрываться внутри кристалла, они должны либо быть замкнутыми, образуя петлю, либо разветвляться на несколько дислокаций, либо выходить на поверхность кристалла.
Дислокационная структура материала характеризуется плотностью дислокаций.
Плотность дислокаций в кристалле определяется как среднее число линий дислокаций, пересекающих внутри тела площадку площадью 1 м2, или как суммарная длина линий дислокаций в объеме 1 м3:
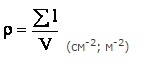
Плотность дислокаций изменяется в широких пределах и зависит от состояния материала. После тщательного отжига плотность дислокаций составляет 10 5…10 7 м-2, в кристаллах с сильно деформированной кристаллической решеткой плотность дислокаций достигает 1015…10 16 м –2.
Плотность дислокации в значительной мере определяет пластичность и прочность материала (рисунок 4).
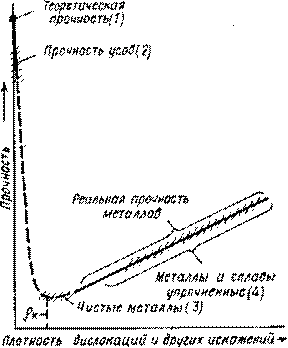
Рисунок 4 – Влияние плотности дислокаций на прочность
Минимальная прочность определяется критической плотностью дислокаций
м-2
Если плотность меньше значения а, то сопротивление деформированию резко возрастает, а прочность приближается к теоретической. Повышение прочности достигается созданием металла с бездефектной структурой, а также повышением плотности дислокаций, затрудняющим их движение. В настоящее время созданы кристаллы без дефектов – нитевидные кристаллы длиной до 2 мм, толщиной 0,5…20 мкм – «усы» с прочностью, близкой к теоретической: для железа σВ = 13000 МПа, для меди σВ =30000 МПа. При упрочнении металлов увеличением плотности дислокаций, она не должна превышать значений 1015…10 16 м –2. В противном случае образуются трещины.
Дислокации влияют не только на прочность и пластичность, но и на другие свойства кристаллов. С увеличением плотности дислокаций возрастает внутреннее, изменяются оптические свойства, повышается электросопротивление металла. Дислокации увеличивают среднюю скорость диффузии в кристалле, ускоряют старение и другие процессы, уменьшают химическую стойкость, поэтому в результате обработки поверхности кристалла специальными веществами в местах выхода дислокаций образуются ямки.
Дислокации образуются при образовании кристаллов из расплава или газообразной фазы, при срастании блоков с малыми углами разориентировки. При перемещении вакансий внутри кристалла, они концентрируются, образуя полости в виде дисков. Если такие диски велики, то энергетически выгодно «захлопывание» их с образованием по краю диска краевой дислокации. Образуются дислокации при деформации, в процессе кристаллизации, при термической обработке.
В чем различие между упругой и пластической деформацией, между хрупким и вязким разрушением
Деформацией называется изменение формы и размеров тела под действием напряжений.
Деформация металла под действием напряжений может быть упругой и пластической.
Упругой называется деформация, полностью исчезающая после снятия вызывающих ее напряжений.
При упругом деформировании изменяются расстояния между атомами металла в кристаллической решетке. Снятие нагрузки устраняет причину, вызвавшую изменение межатомного расстояния, атомы становятся на прежние места, и деформация исчезает.
Упругая деформация на диаграмме деформации характеризуется линией ОА (рисунок 5).
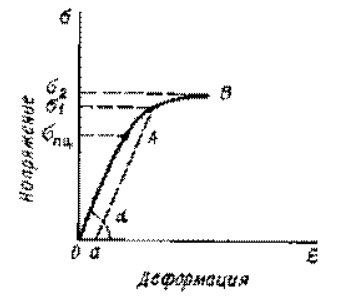
Рисунок 5 – Диаграмма зависимости деформации металла ε от действующих напряжений σ
Если нормальные напряжения достигают значения сил межатомных связей, то наблюдается хрупкое разрушение путем отрыва (рисунок 6)
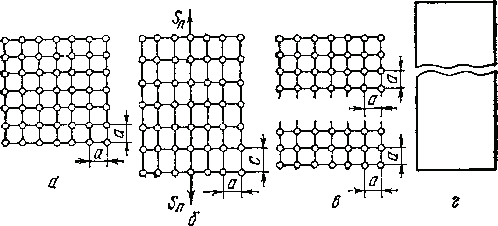
Рисунок 6 – Схема упругой деформации и хрупкого разрушения под действием упругих напряжений а – ненапряженная решетка металла; б – упругая деформация; в, г – хрупкое разрушение в результате отрыва
Зависимость между упругой деформацией ε и напряжением σ выражается законом Гука
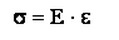
где Е – модуль упругости.
Модуль упругости является важнейшей характеристикой упругих свойств металла. По физической природе величина модуля упругости рассматривается как мера прочности связей между атомами в твердом теле.
Эта механическая характеристика структурно нечувствительна, т. е. термическая обработка или другие способы изменения структуры не изменяют модуля упругости, а повышение температуры, изменяющее межатомные расстояния, снижает модуль упругости.
Пластической или остаточной называется деформация после прекращения действия вызвавших ее напряжений.
При пластическом деформировании одна часть кристалла перемещается по отношению к другой под действием касательных напряжений. При снятии нагрузок сдвиг остается, т.е. происходит пластическая деформация (рисунок 7)
В результате развития пластической деформации может произойти вязкое разрушение путем сдвига.
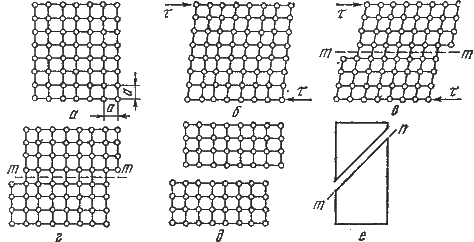
Рисунок 7 – Схема пластической деформации и вязкого разрушения под действием касательных напряжений а – ненапряженная решетка; б – упругая деформация; в – упругая и пластическая деформация; г – пластическая деформация; д, е – пластичное (вязкое) разрушение в результате среза
Процесс деформации при достижении высоких напряжений завершается разрушением. Тела разрушаются по сечению не одновременно, а вследствие развития трещин. Разрушение включает три стадии: зарождение трещины, ее распространение через сечение, окончательное разрушение.
Различают хрупкое разрушение – отрыв одних слоев атомов от других под действием нормальных растягивающих напряжений. Отрыв не сопровождается предварительной деформацией. Механизм зарождения трещины одинаков благодаря скоплению движущихся дислокаций перед препятствием (границы субзерен, фазовые границы), что приводит к концентрации напряжений, достаточной для образования трещины. Когда напряжения достигают определенного значения, размер трещины становится критическим и дальнейший рост осуществляется произвольно.
Для хрупкого разрушения характерна острая, часто ветвящаяся трещина. Величина зоны пластической деформации в устье трещины мала. Скорость распространения хрупкой трещины велика – близка к скорости звука (внезапное, катастрофическое разрушение). Энергоемкость хрупкого разрушения мала, а работа распространения трещины близка к нулю.
Различают транскристаллитное разрушение – трещина распространяется по телу зерна, интеркристаллитное – по границам зерен (всегда хрупкое).
Результатом хрупкого разрушения является блестящий светлый кристаллический излом с ручьистым строением. Хрупкая трещина распространяется по нескольким параллельным плоскостям. Плоскость излома перпендикулярна нормальным напряжениям.
Вязкое разрушение – путем среза под действием касательных напряжений. Ему всегда предшествует значительная пластическая деформация.
Трещина тупая раскрывающаяся. Величина пластической зоны впереди трещины велика. Малая скорость распространения трещины. Энергоемкость значительная, энергия расходуется на образование поверхностей раздела и на пластическую деформацию. Большая работа затрачивается на распространение трещины. Поверхность излома негладкая, рассеивает световые лучи, матовая (волокнистый) излом. Плоскость излома располагается под углом.
По излому можно определить характер разрушения.
Вычертите диаграмму состояния железо – карбид железа, укажите структурные составляющие во всех областях диаграммы, опишите превращения и постройте кривую охлаждения (с применением правила фаз) для сплава, содержащего 0,5% С. Какова структура этого сплава при комнатной температуре и как такой сплав называется?
Первичная кристаллизация сплавов системы железо-углерод начинается по достижении температур, соответствующих линии ABCD (линии ликвидус), и заканчивается при температурах, образующих линию AHJECF (линию солидус).
При кристаллизации сплавов по линии АВ из жидкого раствора выделяются кристаллы твердого раствора углерода в α-железе (δ-раствор). Процесс кристаллизации сплавов с содержанием углерода до 0,1 % заканчивается по линии АН с образованием α (δ)-твердого раствора. На линии HJB протекает перитектическое превращение, в результате которого образуется твердый раствор углерода в γ-железе, т. е. аустенит. Процесс первичной кристаллизации сталей заканчивается по линии AHJE.
При температурах, соответствующих линии ВС, из жидкого раствора кристаллизуется аустенит. В сплавах, содержащих от 4,3 % до 6,67 % углерода, при температурах, соответствующих линии CD, начинают выделяться кристаллы цементита первичного. Цементит, кристаллизующийся из жидкой фазы, называется первичным. B точке С при температуре 1147°С и концентрации углерода в жидком растворе 4,3 % образуется эвтектика, которая называется ледебуритом. Эвтектическое превращение с образованием ледебурита можно записать формулой ЖР4,3Л[А2,14+Ц6,67]. Процесс первичной кристаллизации чугунов заканчивается по линии ECF образованием ледебурита.
Таким образом, структура чугунов ниже 1147°С будет: доэвтектических — аустенит+ледебурит, эвтектических — ледебурит и заэвтектических — цементит (первичный)+ледебурит.
Превращения, происходящие в твердом состоянии, называются вторичной кристаллизацией. Они связаны с переходом при охлаждении γ-железа в α-железо и распадом аустенита.
Линия GS соответствует температурам начала превращения аустенита в феррит. Ниже линии GS сплавы состоят из феррита и аустенита.
Линия ЕS показывает температуры начала выделения цементита из аустенита вследствие уменьшения растворимости углерода в аустените с понижением температуры. Цементит, выделяющийся из аустенита, называется вторичным цементитом.
В точке S при температуре 727°С и концентрации углерода в аустените 0,8 % образуется эвтектоидная смесь состоящая из феррита и цементита, которая называется перлитом. Перлит получается в результате одновременного выпадения из аустенита частиц феррита и цементита. Процесс превращения аустенита в перлит можно записать формулой А0,8П[Ф0,03+Ц6,67].
Линия PQ показывает на уменьшение растворимости углерода в феррите при охлаждении и выделении цементита, который называется третичным цементитом.
Следовательно, сплавы, содержащие менее 0,008% углерода (точкаQ), являются однофазными и имеют структуру чистого феррита, а сплавы, содержащие углерод от 0,008 до 0,03% – структуру феррит+цементит третичный и называются техническим железом.
Доэвтектоидные стали при температуре ниже 727ºС имеют структуру феррит+перлит и заэвтектоидные – перлит+цементит вторичный в виде сетки по границам зерен.
В доэвтектических чугунах в интервале температур 1147–727ºС при охлаждении из аустенита выделяется цементит вторичный, вследствие уменьшения растворимости углерода (линия ES). По достижении температуры 727ºС (линия PSK) аустенит, обедненный углеродом до 0,8% (точка S), превращаясь в перлит. Таким образом, после окончательного охлаждения структура доэвтектических чугунов состоит из перлита, цементита вторичного и ледебурита превращенного (перлит+цементит).
Структура эвтектических чугунов при температурах ниже 727ºС состоит из ледебурита превращенного. Заэвтектический чугун при температурах ниже 727ºС состоит из ледебурита превращенного и цементита первичного.
Правило фаз устанавливает зависимость между числом степеней свободы, числом компонентов и числом фаз и выражается уравнением:
C = K + 1 – Ф,
где С – число степеней свободы системы;
К – число компонентов, образующих систему;
1 – число внешних факторов (внешним фактором считаем только температуру, так как давление за исключением очень высокого мало влияет на фазовое равновесие сплавов в твердом и жидком состояниях);
Ф – число фаз, находящихся в равновесии.
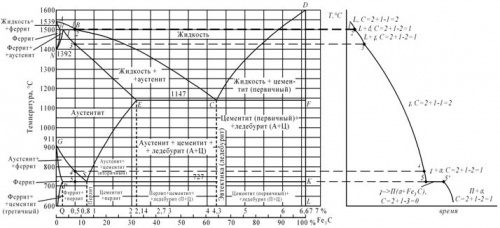
а) б)
Рисунок 8: а-диаграмма железо-цементит, б-кривая охлаждения для сплава, содержащего 0,5% углерода
Сплав железа с углеродом, содержащий 0,5 %С, называется доэвтектической сталью. Его структура при комнатной температуре – Феррит + Перлит.
Вычертите диаграмму изотермического превращения аустенита для стали У8, нанесите кривую режима изотермической обработки, обеспечивающей получение твердости 50HRC. Укажите, как этот режим называется, опишите сущность превращения и какая структура получается в данном случае.
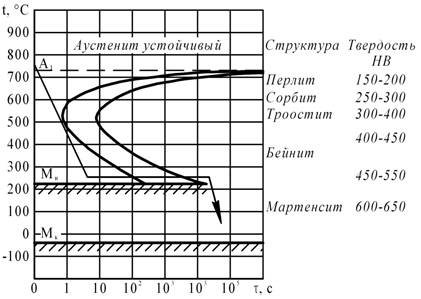
Рисунок 9 – Диаграмма изотермического превращения аустенита стали У8
Изотермической обработкой, необходимой для получения твердости 50 HRC, является изотермическая закалка. При изотермической закалке сталь У8 нагревают до температуры на 30-50°С выше точки Ас1 (Ас1 = 730°С) и после выдержки охлаждают до температуры 250-350°С, что несколько превышает температуру начала мартенситного превращения. Выдержка деталей в закалочной среде должна быть достаточной для полного превращения аустенита в нижний бейнит, имеющий твердость 50HRC. Нижний бейнит представляет собой структуру, состоящая из α-твердого раствора, претерпевшего мартенситное превращение и несколько пересыщенного углеродом, и частиц карбидов.
В качестве охлаждающей среды при изотермической закалке применяют расплавленные соли или расплавленные щелочи.
С помощью диаграммы состояния железо-цементит опишите структурные превращения, происходящие при нагреве стали У12. Укажите критические точки и выберите оптимальный режим нагрева этой стали под закалку. Охарактеризуйте процесс закалки, опишите получаемую структуру и свойства стали.
Диаграмма состояния железо-цементит представлена на рисунке 8. При комнатной температуре сталь У12 имеет структуру цементита и перлита. До температуры Аc1 сохраняется исходная структура. При температуре Аc1 происходит превращение перлита в аустенит с содержанием углерода 0,8%. При нагреве выше точки Ас1 происходит растворение цементита в аустените (в соответствии с линией SE). Увеличение температуры выше точки Асm вызывает рост зерна аустенита.
Критические точки для стали У12: Аc1 = 730°С; Аcm = 820°С.
Для закалки заэвтектоидные стали нагревают на 50-70°С выше точки Ас1. Таким образом, температура нагрева под закалку составляет 780-800°С. При этих температурах в стали наряду с аустенитом имеется цементит. Поэтому после закалки в структуре заэвтектоидных сталей будет мартенсит с цементитом и небольшое количество остаточного аустенита. Охлаждающая среда при закалке – индустриальное масло. Твердость поверхности после закалки 62-64 HRC. Для снятия напряжений и стабилизации структуры после закалки изделия подвергают низкому отпуску.
В любом реальном кристалле всегда имеются дефекты строения. Линейные несовершенства имеют малые размеры в двух измерениях и большую протяженность в третьем. Эти несовершенства называются дислокациями.
Краевая дислокация представляет собой линию, вдоль которой обрывается внутри кристалла край “лишней“ полуплоскости (рисунок 1)
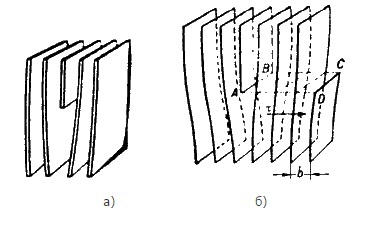
Рисунок 1 – Краевая дислокация (а) и механизм ее образования (б)
Неполная плоскость называется экстраплоскостью.
Большинство дислокаций образуются путем сдвигового механизма. Ее образование можно описать при помощи следующей операции. Надрезать кристалл по плоскости АВСD, сдвинуть нижнюю часть относительно верхней на один период решетки в направлении, перпендикулярном АВ, а затем вновь сблизить атомы на краях разреза внизу.
Наибольшие искажения в расположении атомов в кристалле имеют место вблизи нижнего края экстраплоскости. Вправо и влево от края экстраплоскости эти искажения малы (несколько периодов решетки), а вдоль края экстраплоскости искажения простираются через весь кристалл и могут быть очень велики (тысячи периодов решетки) (рисунок 2).
Если экстраплоскость находится в верхней части кристалла, то краевая дислокация – положительная (┴), если в нижней, то – отрицательная (┬). Дислокации одного знака отталкиваются, а противоположные притягиваются.
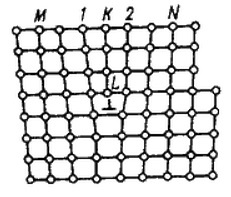
Рисунок 2 – Искажения в кристаллической решетке при наличии краевой дислокации
Другой тип дислокаций был описан Бюргерсом, и получил название винтовая дислокация
Винтовая дислокация получена при помощи частичного сдвига по плоскости Q вокруг линии EF (рисунок 3) На поверхности кристалла образуется ступенька, проходящая от точки Е до края кристалла. Такой частичный сдвиг нарушает параллельность атомных слоев, кристалл превращается в одну атомную плоскость, закрученную по винту в виде полого геликоида вокруг линии EF, которая представляет границу, отделяющую часть плоскости скольжения, где сдвиг уже произошел, от части, где сдвиг не начинался. Вдоль линии EF наблюдается макроскопический характер области несовершенства, в других направлениях ее размеры составляют несколько периодов.
Если переход от верхних горизонтов к нижним осуществляется поворотом по часовой стрелке, то дислокация правая, а если поворотом против часовой стрелки – левая.
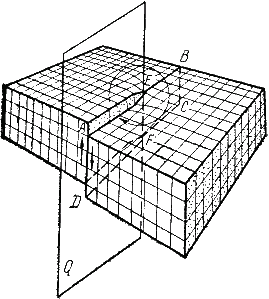
Рисунок 3 – Механизм образования винтовой дислокации
Винтовая дислокация не связана с какой-либо плоскостью скольжения, она может перемещаться по любой плоскости, проходящей через линию дислокации. Вакансии и дислоцированные атомы к винтовой дислокации не стекают.
В процессе кристаллизации атомы вещества, выпадающие из пара или раствора, легко присоединяются к ступеньке, что приводит к спиральному механизму роста кристалла.
Линии дислокаций не могут обрываться внутри кристалла, они должны либо быть замкнутыми, образуя петлю, либо разветвляться на несколько дислокаций, либо выходить на поверхность кристалла.
Дислокационная структура материала характеризуется плотностью дислокаций.
Плотность дислокаций в кристалле определяется как среднее число линий дислокаций, пересекающих внутри тела площадку площадью 1 м2, или как суммарная длина линий дислокаций в объеме 1 м3:
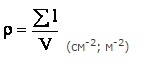
Плотность дислокаций изменяется в широких пределах и зависит от состояния материала. После тщательного отжига плотность дислокаций составляет 10 5…10 7 м-2, в кристаллах с сильно деформированной кристаллической решеткой плотность дислокаций достигает 1015…10 16 м –2.
Плотность дислокации в значительной мере определяет пластичность и прочность материала (рисунок 4).
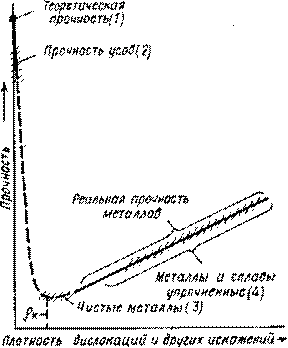
Рисунок 4 – Влияние плотности дислокаций на прочность
Минимальная прочность определяется критической плотностью дислокаций
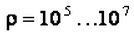
Если плотность меньше значения а, то сопротивление деформированию резко возрастает, а прочность приближается к теоретической. Повышение прочности достигается созданием металла с бездефектной структурой, а также повышением плотности дислокаций, затрудняющим их движение. В настоящее время созданы кристаллы без дефектов – нитевидные кристаллы длиной до 2 мм, толщиной 0,5…20 мкм – «усы» с прочностью, близкой к теоретической: для железа σВ = 13000 МПа, для меди σВ =30000 МПа. При упрочнении металлов увеличением плотности дислокаций, она не должна превышать значений 1015…10 16 м –2. В противном случае образуются трещины.
Дислокации влияют не только на прочность и пластичность, но и на другие свойства кристаллов. С увеличением плотности дислокаций возрастает внутреннее, изменяются оптические свойства, повышается электросопротивление металла. Дислокации увеличивают среднюю скорость диффузии в кристалле, ускоряют старение и другие процессы, уменьшают химическую стойкость, поэтому в результате обработки поверхности кристалла специальными веществами в местах выхода дислокаций образуются ямки.
Дислокации образуются при образовании кристаллов из расплава или газообразной фазы, при срастании блоков с малыми углами разориентировки. При перемещении вакансий внутри кристалла, они концентрируются, образуя полости в виде дисков. Если такие диски велики, то энергетически выгодно «захлопывание» их с образованием по краю диска краевой дислокации. Образуются дислокации при деформации, в процессе кристаллизации, при термической обработке.
В чем различие между упругой и пластической деформацией, между хрупким и вязким разрушением
Деформацией называется изменение формы и размеров тела под действием напряжений.
Деформация металла под действием напряжений может быть упругой и пластической.
Упругой называется деформация, полностью исчезающая после снятия вызывающих ее напряжений.
При упругом деформировании изменяются расстояния между атомами металла в кристаллической решетке. Снятие нагрузки устраняет причину, вызвавшую изменение межатомного расстояния, атомы становятся на прежние места, и деформация исчезает.
Упругая деформация на диаграмме деформации характеризуется линией ОА (рисунок 5).
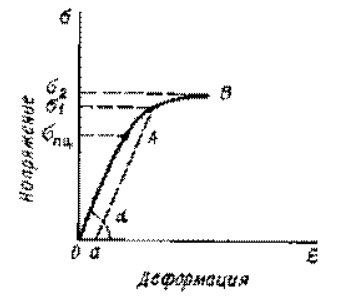
Рисунок 5 – Диаграмма зависимости деформации металла ε от действующих напряжений σ
Если нормальные напряжения достигают значения сил межатомных связей, то наблюдается хрупкое разрушение путем отрыва (рисунок 6)
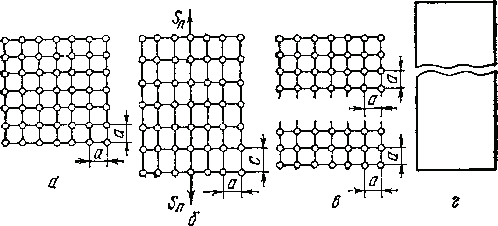
Рисунок 6 – Схема упругой деформации и хрупкого разрушения под действием упругих напряжений а – ненапряженная решетка металла; б – упругая деформация; в, г – хрупкое разрушение в результате отрыва
Зависимость между упругой деформацией ε и напряжением σ выражается законом Гука
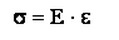
где Е – модуль упругости.
Модуль упругости является важнейшей характеристикой упругих свойств металла. По физической природе величина модуля упругости рассматривается как мера прочности связей между атомами в твердом теле.
Эта механическая характеристика структурно нечувствительна, т. е. термическая обработка или другие способы изменения структуры не изменяют модуля упругости, а повышение температуры, изменяющее межатомные расстояния, снижает модуль упругости.
Пластической или остаточной называется деформация после прекращения действия вызвавших ее напряжений.
При пластическом деформировании одна часть кристалла перемещается по отношению к другой под действием касательных напряжений. При снятии нагрузок сдвиг остается, т.е. происходит пластическая деформация (рисунок 7)
В результате развития пластической деформации может произойти вязкое разрушение путем сдвига.
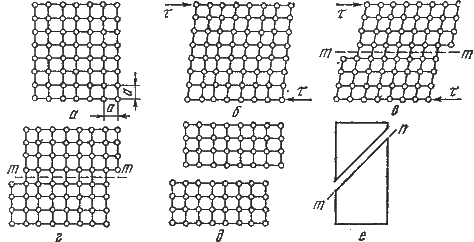
Рисунок 7 – Схема пластической деформации и вязкого разрушения под действием касательных напряжений а – ненапряженная решетка; б – упругая деформация; в – упругая и пластическая деформация; г – пластическая деформация; д, е – пластичное (вязкое) разрушение в результате среза
Процесс деформации при достижении высоких напряжений завершается разрушением. Тела разрушаются по сечению не одновременно, а вследствие развития трещин. Разрушение включает три стадии: зарождение трещины, ее распространение через сечение, окончательное разрушение.
Различают хрупкое разрушение – отрыв одних слоев атомов от других под действием нормальных растягивающих напряжений. Отрыв не сопровождается предварительной деформацией. Механизм зарождения трещины одинаков благодаря скоплению движущихся дислокаций перед препятствием (границы субзерен, фазовые границы), что приводит к концентрации напряжений, достаточной для образования трещины. Когда напряжения достигают определенного значения, размер трещины становится критическим и дальнейший рост осуществляется произвольно.
Для хрупкого разрушения характерна острая, часто ветвящаяся трещина. Величина зоны пластической деформации в устье трещины мала. Скорость распространения хрупкой трещины велика – близка к скорости звука (внезапное, катастрофическое разрушение). Энергоемкость хрупкого разрушения мала, а работа распространения трещины близка к нулю.
Различают транскристаллитное разрушение – трещина распространяется по телу зерна, интеркристаллитное – по границам зерен (всегда хрупкое).
Результатом хрупкого разрушения является блестящий светлый кристаллический излом с ручьистым строением. Хрупкая трещина распространяется по нескольким параллельным плоскостям. Плоскость излома перпендикулярна нормальным напряжениям.
Вязкое разрушение – путем среза под действием касательных напряжений. Ему всегда предшествует значительная пластическая деформация.
Трещина тупая раскрывающаяся. Величина пластической зоны впереди трещины велика. Малая скорость распространения трещины. Энергоемкость значительная, энергия расходуется на образование поверхностей раздела и на пластическую деформацию. Большая работа затрачивается на распространение трещины. Поверхность излома негладкая, рассеивает световые лучи, матовая (волокнистый) излом. Плоскость излома располагается под углом.
По излому можно определить характер разрушения.
Вычертите диаграмму состояния железо – карбид железа, укажите структурные составляющие во всех областях диаграммы, опишите превращения и постройте кривую охлаждения (с применением правила фаз) для сплава, содержащего 0,5% С. Какова структура этого сплава при комнатной температуре и как такой сплав называется?
Первичная кристаллизация сплавов системы железо-углерод начинается по достижении температур, соответствующих линии ABCD (линии ликвидус), и заканчивается при температурах, образующих линию AHJECF (линию солидус).
При кристаллизации сплавов по линии АВ из жидкого раствора выделяются кристаллы твердого раствора углерода в α-железе (δ-раствор). Процесс кристаллизации сплавов с содержанием углерода до 0,1 % заканчивается по линии АН с образованием α (δ)-твердого раствора. На линии HJB протекает перитектическое превращение, в результате которого образуется твердый раствор углерода в γ-железе, т. е. аустенит. Процесс первичной кристаллизации сталей заканчивается по линии AHJE.
При температурах, соответствующих линии ВС, из жидкого раствора кристаллизуется аустенит. В сплавах, содержащих от 4,3 % до 6,67 % углерода, при температурах, соответствующих линии CD, начинают выделяться кристаллы цементита первичного. Цементит, кристаллизующийся из жидкой фазы, называется первичным. B точке С при температуре 1147°С и концентрации углерода в жидком растворе 4,3 % образуется эвтектика, которая называется ледебуритом. Эвтектическое превращение с образованием ледебурита можно записать формулой ЖР4,3Л[А2,14+Ц6,67]. Процесс первичной кристаллизации чугунов заканчивается по линии ECF образованием ледебурита.
Таким образом, структура чугунов ниже 1147°С будет: доэвтектических — аустенит+ледебурит, эвтектических — ледебурит и заэвтектических — цементит (первичный)+ледебурит.
Превращения, происходящие в твердом состоянии, называются вторичной кристаллизацией. Они связаны с переходом при охлаждении γ-железа в α-железо и распадом аустенита.
Линия GS соответствует температурам начала превращения аустенита в феррит. Ниже линии GS сплавы состоят из феррита и аустенита.
Линия ЕS показывает температуры начала выделения цементита из аустенита вследствие уменьшения растворимости углерода в аустените с понижением температуры. Цементит, выделяющийся из аустенита, называется вторичным цементитом.
В точке S при температуре 727°С и концентрации углерода в аустените 0,8 % образуется эвтектоидная смесь состоящая из феррита и цементита, которая называется перлитом. Перлит получается в результате одновременного выпадения из аустенита частиц феррита и цементита. Процесс превращения аустенита в перлит можно записать формулой А0,8П[Ф0,03+Ц6,67].
Линия PQ показывает на уменьшение растворимости углерода в феррите при охлаждении и выделении цементита, который называется третичным цементитом.
Следовательно, сплавы, содержащие менее 0,008% углерода (точкаQ), являются однофазными и имеют структуру чистого феррита, а сплавы, содержащие углерод от 0,008 до 0,03% – структуру феррит+цементит третичный и называются техническим железом.
Доэвтектоидные стали при температуре ниже 727ºС имеют структуру феррит+перлит и заэвтектоидные – перлит+цементит вторичный в виде сетки по границам зерен.
В доэвтектических чугунах в интервале температур 1147–727ºС при охлаждении из аустенита выделяется цементит вторичный, вследствие уменьшения растворимости углерода (линия ES). По достижении температуры 727ºС (линия PSK) аустенит, обедненный углеродом до 0,8% (точка S), превращаясь в перлит. Таким образом, после окончательного охлаждения структура доэвтектических чугунов состоит из перлита, цементита вторичного и ледебурита превращенного (перлит+цементит).
Структура эвтектических чугунов при температурах ниже 727ºС состоит из ледебурита превращенного. Заэвтектический чугун при температурах ниже 727ºС состоит из ледебурита превращенного и цементита первичного.
Правило фаз устанавливает зависимость между числом степеней свободы, числом компонентов и числом фаз и выражается уравнением:
C = K + 1 – Ф,
где С – число степеней свободы системы;
К – число компонентов, образующих систему;
1 – число внешних факторов (внешним фактором считаем только температуру, так как давление за исключением очень высокого мало влияет на фазовое равновесие сплавов в твердом и жидком состояниях);
Ф – число фаз, находящихся в равновесии.
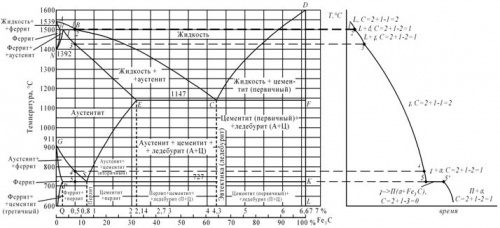
а) б)
Рисунок 8: а-диаграмма железо-цементит, б-кривая охлаждения для сплава, содержащего 0,5% углерода
Сплав железа с углеродом, содержащий 0,5 %С, называется доэвтектической сталью. Его структура при комнатной температуре – Феррит + Перлит.
Вычертите диаграмму изотермического превращения аустенита для стали У8, нанесите кривую режима изотермической обработки, обеспечивающей получение твердости 50HRC. Укажите, как этот режим называется, опишите сущность превращения и какая структура получается в данном случае.
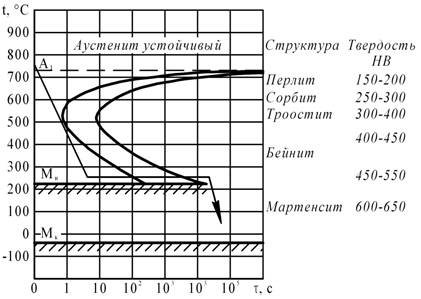
Рисунок 9 – Диаграмма изотермического превращения аустенита стали У8
Изотермической обработкой, необходимой для получения твердости 50 HRC, является изотермическая закалка. При изотермической закалке сталь У8 нагревают до температуры на 30-50°С выше точки Ас1 (Ас1 = 730°С) и после выдержки охлаждают до температуры 250-350°С, что несколько превышает температуру начала мартенситного превращения. Выдержка деталей в закалочной среде должна быть достаточной для полного превращения аустенита в нижний бейнит, имеющий твердость 50HRC. Нижний бейнит представляет собой структуру, состоящая из α-твердого раствора, претерпевшего мартенситное превращение и несколько пересыщенного углеродом, и частиц карбидов.
В качестве охлаждающей среды при изотермической закалке применяют расплавленные соли или расплавленные щелочи.
С помощью диаграммы состояния железо-цементит опишите структурные превращения, происходящие при нагреве стали У12. Укажите критические точки и выберите оптимальный режим нагрева этой стали под закалку. Охарактеризуйте процесс закалки, опишите получаемую структуру и свойства стали.
Диаграмма состояния железо-цементит представлена на рисунке 8. При комнатной температуре сталь У12 имеет структуру цементита и перлита. До температуры Аc1 сохраняется исходная структура. При температуре Аc1 происходит превращение перлита в аустенит с содержанием углерода 0,8%. При нагреве выше точки Ас1 происходит растворение цементита в аустените (в соответствии с линией SE). Увеличение температуры выше точки Асm вызывает рост зерна аустенита.
Критические точки для стали У12: Аc1 = 730°С; Аcm = 820°С.
Для закалки заэвтектоидные стали нагревают на 50-70°С выше точки Ас1. Таким образом, температура нагрева под закалку составляет 780-800°С. При этих температурах в стали наряду с аустенитом имеется цементит. Поэтому после закалки в структуре заэвтектоидных сталей будет мартенсит с цементитом и небольшое количество остаточного аустенита. Охлаждающая среда при закалке – индустриальное масло. Твердость поверхности после закалки 62-64 HRC. Для снятия напряжений и стабилизации структуры после закалки изделия подвергают низкому отпуску.
0 комментариев